Scania unveils Euro VI engines
5 April 2011
Scania announced it is ready to start delivering trucks with Euro VI diesel engines. The engines incorporate aftertreatment technologies for PM and NOx, with both emissions being reduced by around 80% compared to the current Euro V emission standards.
The new engines are made available ahead of the regulatory Euro VI deadlines—2013 for new types, 2014 for all models. Truck operators who will invest into Euro VI equipment will be able to benefit from lower motorway charges and other incentives that may be introduced by authorities.
In the development of the Euro VI engines Scania has combined a number of technologies developed by the company in recent years: exhaust gas recirculation, variable turbo geometry, common-rail high-pressure fuel injection, selective catalytic reduction and particulate filtering. The new engines are designed to give the same performance and fuel efficiency as their Euro V counterparts, said Scania.
The 440 hp (324 kW) and 480 hp (353 kW) 13-liter engines will be available across the G- and R-series truck ranges for all types of applications. The cast-iron cylinder block remains unchanged from Euro V engines, being designed from the outset for high combustion pressures, in this case up to 200 bar. Steel pistons with a slightly reshaped bowl provide a compression ratio of 17.3:1. The weight of the engine is similar to Euro V engines with EGR, but the vehicle weight is up by up to 200 kg due to the added complexity of the aftertreatment system. The engines can be operated using biodiesel blends up to 8%.
The Scania XPI common-rail fuel injection system, designed for maximum injection pressures of up to 2,400 bar, typically operates around 1,800 bar. The eight-hole injectors provide up to three injection events per cycle. This includes a post injection, that is used when needed to maintain sufficient exhaust temperatures for the SCR catalyst, as well as to assist the regeneration of the particulate filter.
The Scania Euro VI emission control system is shown in the following schematic. The flow of intake air from the variable-geometry turbocharger (VGT) can be restricted with the intake throttle to prevent cold air from flowing through the engine and into the exhaust when coasting. The upstream NOx sensor, diesel oxidation catalyst (DOC), wall-flow diesel particulate filter (DPF), urea (AdBlue) mixer, twin parallel SCR catalysts, ammonia slip catalysts (ASC) and downstream NOx sensor are all integrated in a compact silencer unit. The temperature (°C) is measured all the way up to the catalysts and the pressure drop (ΔP) across the DPF monitored to assess the status of the filter.
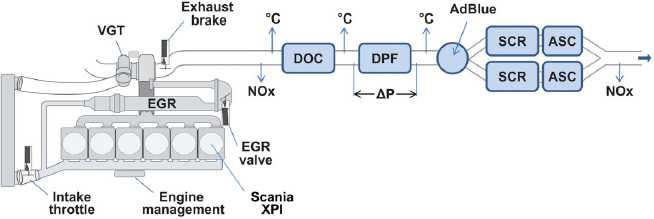
The particulate filter reduces particulate emissions by 99%. Typically, around 50% of NOx emissions are eliminated at source by the EGR system and another 95% over the SCR catalysts. The SCR system includes a 75 liter urea solution (AdBlue) tank. The consumption of urea corresponds to 3-4% of fuel consumption, compared to 5-6% for Scania’s Euro V SCR engines.
The development of the new engine generation and the technology to meet Euro VI emissions, all done in-house, has taken five years and involves costs for Scania of approximately SEK 10 billion (US$158 million).
Source: Scania