Conference report: 2016 CIMAC Congress
28 June 2016
The 28th CIMAC World Congress was held in Helsinki, Finland on June 6-9, 2016. The CIMAC Congress, organized once every three years, is a major technical meeting that covers internal combustion engine technology for ship propulsion, power generation and rail traction. About 188 papers were presented in four parallel technical sessions and 30 posters were displayed over the course of 4 days. The Congress also included an exhibition showcasing engines, engine components and related products, with strong participation from European suppliers. The meeting was attended by over 800 delegates.
Please log in to view the full version of this article (subscription required).
Comprehensive solutions to enable vessels to switch operation between IMO Tier II and Tier III NOx emissions received significant attention. In many new engines, IMO Tier II NOx standards can be met by all fuels including HFO without having to resort to SCR or EGR. This is not the case for IMO Tier III. For engines operating on MGO/HFO, EGR or SCR are the two primary options. Since regions where IMO Tier III NOx levels will be required are also subject to a 0.1% fuel sulfur limit (or require an exhaust scrubber), operation of the EGR and SCR systems will often coincide with the use of low sulfur fuels; significantly simplifying their design and operation. For engines with the capability to operate with natural gas and other gaseous fuels, Otto cycle operation will be sufficient. One interesting option for low speed 2-stroke engines is the use of low pressure EGR and low pressure SCR (after turbo) with the latter enabled by low sulfur fuels.
IMO fuel quality regulations set a global sulfur cap of 0.5% on marine fuels (or require exhaust scrubbers) effective 2020/2025. In the long term, the HFO fuel share—now almost 90%—is expected to drop to 50%, while the share of low sulfur (0.5%) fuels will increase to 30% [MAN Diesel & Turbo, #73]. Alternative fuels such as natural gas, LPG, methanol etc., are expected to play a role partially meeting the demand for low sulfur fuels—especially in cases where they are available at a competitive cost to the vessel operator. While the current low oil prices make some of these alternative fuels unattractive economically (especially for natural gas), this situation is not expected to last.
Diesel Engines
High Speed. A number of papers discussed new developments in high-, medium- and low-speed diesel engine technology. MTU presented their new generation Series 4000 engines [S. Harscher, #196], which are available in 12/16/20 V configurations with power between 1000-4300 kW for off-highway, rail, marine and power generation applications. The engines feature a new 2500 bar common-rail fuel injection system developed by MTU and L’Orange. The emission system depends on the application. Off-highway engines use Miller timing with dual stage turbocharging and a donor-cylinder EGR, without aftertreatment. Rail engines (EU Stage IIIB) use a diesel particulate filter. The use of a DPF has been largely driven by customer demand, as the regulatory PM limits could be met without a filter. The DPF is passively regenerated, with retarded injection and intake air throttling used at low temperatures. Marine engines (EPA Tier 4 and IMO III) utilize SCR aftertreatment, while power generation engines (EPA Tier 4) use an SCR + DPF emission system.
Bosch attempted to forecast the emission solutions that would be adopted for EU Stage V [C. Kendlbacher, #79]. They predict that the technical solutions already exist and that no new technology will be required. For engines adopting EGR, a 2200 bar fuel injection system provides the best NOx/soot and NOx/ISFC trade-offs. For non-EGR engines, 1800 bar injection pressure is best from NOx/ISFC considerations. For engines that will be subject to a PN limit (marine and railcar), a DOC/DPF will be required. Non-EGR railcar and marine as well as marine engines with EGR will require urea SCR. Railcar engines with EGR will not require NOx aftertreatment. For engines not subject to PN limits (genset, locomotive and construction) a DPF will be optional; non-EGR engines as well as gensets with EGR will require SCR. EGR as well as a DOC will be sufficient for locomotive and construction equipment.
GE introduced a new 616 Diesel Genset [#164], based on the Jenbacher J616 gas genset family and the GE P616 diesel locomotive engine (which was itself based on the J616). Changes in the new design include piston bowl shape, ring grove detail, and intake cam profile. The engine delivers 2750 kW and is intended for emission-unregulated markets in Asia.
Russian engine manufacturers are introducing new diesel engines developed in cooperation with European consultants. ZVEZDA is about to launch the V12 version (3.1 L/cyl) of their new PULSAR M150 high speed diesel engine family designed together with AVL [#266]. Another manufacturer, Ural Diesel Motor Works (UDMZ), will introduce the DM-185 diesel engine family developed with FEV [#93]. The engines—featuring 12-16-20 cylinders, 5.77 L/cyl, 1500-300 kW and Stage IIIA / IMO II emissions—are scheduled for introduction in 2017.
Medium Speed. Ricardo designed a completely new medium speed engine platform intended for power generation applications in developing countries [#112], developed in cooperation with an undisclosed engine manufacturer. The engine has a market entry power rating of 530 kW/cyl, uses a single stage turbo, and operates at up to 250 bar firing pressure. The initial production engine will run on HFO/MDO with natural gas and dual fuel variants under development.
EGR can be applied to older engine models to reduce NOx and comply with the IMO III emission standards. Caterpillar discussed the EGR development process [#52], based on a concept study that involved the addition of EGR to the MAK 6M32C medium speed marine engine. The engine was converted to a two stage turbocharging system with a high pressure loop EGR path. A special EGR turbocharger was used to drive the EGR flow. While IMO III emissions could be reached using EGR rates up to 20%, high soot emissions were present in the entire load range. To reduce soot, a post-injection strategy was used with a new 2000 bar common rail system. A tubular EGR cooler avoids the need for exhaust flowing over fins to reduce fouling by sticky soot deposits. Another issue that needed to be addresses was corrosion due to the condensation of sulfuric acid, even with low sulfur fuels.
A paper by Yanmar discussed the development of low fuel consumption technology for medium speed diesel engines [#148]. The technologies included electronic unit pump (EUP, 2 stage turbocharging with a pressure ratio about 7 and Miller valve timing of 10-20° before BDC. The 2 stage turbo with Miller timing and the EUP could each provide a 5 g/kWh SFOC improvement. A test engine with both technologies demonstrated more than 10 g/kWh SFOC improvement over the existing strategy when using “non-ECA map”.
Several talks covered new medium-speed engine models from other manufacturers. These included the MAN V4x/60CR four-stroke, 2-stage turbocharged engine with over 50% efficiency [#181], the Wärtsilä 31 with an impressive fuel consumption of 160 g/kWh (also available in dual fuel and SI gas versions) [#225], and the Bergen B33:45 engine series [#307].
Low Speed. In spite of the slowdown in the low speed engine market, several interesting papers were also presented on 2-stroke, low speed engines. MAN discussed the recent evolution of components and subsystems in MAN B&W engines fueled by both diesel and gaseous fuels [#116]. A new fuel booster injection valve (FBIV) and a top-controlled exhaust valve (TCEV) have been developed for diesel engines. MAN is also investigating a common rail system (in cooperation with OMT) to replace their unit injector system. New fuel systems have also been developed for various types of gaseous fuels, including liquid gas fuels (LPG, DME, methanol, ethanol). The company also launched a new G90 gas engine platform, based on a mass optimized design with a target of 10% weight reduction.
In the area of Tier III NOx emission systems, MAN optimized their SCR and EGR systems for low sulfur fuel operation. In the case of SCR, low sulfur fuels allow an increased NH3 slip and a smaller catalyst volume (ammonia slip must be kept low with high sulfur to control fouling by ammonium sulfate). In the case of EGR, low sulfur fuels allow reductions in the scrubber size, resulting in an EGR unit that is not much larger than that for Tier II applications.
MAN licensee Kawasaki, discussed their IMO Tier III solution for low speed 2-strokes on a Kawasaki MAN B&W 7S60ME-C8.2 with K-ECOS engine [M. Higashida, #106]. The emission control system consists of four systems: EGR, EGR water treatment, water emulsified fuel (WEF) system and a turbocharger cut-out system. The WEF system mixes water and fuel with a mechanical mixer prior to injection. EGR flows from the turbocharger turbine inlet to the compressor discharge via a blower. The turbocharging system is a parallel sequential arrangement of a larger and smaller turbocharger. IMO Tier III emissions are achieved with the combination of EGR (above 15% load), WEF and keeping the smaller turbocharger inactive over the entire load range. IMO Tier II NOx requires WEF with the smaller turbo active above 70% load. Operation with HFO requires the emulsification system to be used while distillate fuels do not. EGR rates are 30-35% while water/fuel ratios are 30-40%.
Mitsubishi Heavy Industries presented their latest two-stroke, low speed 6UEC50LSH-Eco engine. The fuel consumption has been reduced to 164 g/kWh by such measures as improved trade-off between SFOC and NOx obtained by an optimized fuel injection pressure and rate, reduction of mechanical losses, and high efficiency of the exhaust gas and scavenging air system. The engine can comply with IMO Tier III NOx regulations when combined with an electronic control system and EGR or SCR.
Among their NOx control options, Mitsubishi introduced a low pressure EGR system—the first ever LP EGR installed on a low speed 2-stroke engine [#142]. The recirculated exhaust is drawn from downstream of the turbocharger, is cleaned in a scrubber, and pumped by an EGR blower to the turbocharger inlet. A water treatment system, incorporating two centrifuges, cleans the scrubbing water. The sludge from the second centrifuge must be disposed of as industrial waste. Due to the low temperature and pressure, the scrubber system is simpler and less costly compared to high pressure EGR systems. The LP-EGR system has been installed on a 34,000 DWT Bulk Carrier and is undergoing a long-term durability confirmation during the sea trials and commercial voyages.
Locomotives
GE presented more information on their updated diesel engines to meet EPA Tier 4 locomotive requirements and IMO Tier III requirements for marine applications [R. Mischler, #309]. The locomotive EVO engine has 12 cylinders and is rated at 3375 kW. For marine applications, the L/V250 engine series with variants from 6 to 16 cylinders is available. At the 2013 CIMAC Congress, the path to Tier 4 included exhaust aftertreatment. However, as development switched from single cylinder engine testing to multi-cylinder engine testing, GE was able to identify a technology solution that allowed meeting emission requirements without any aftertreatment. The new engines use cooled EGR, 2-stage turbocharging, Miller valve timing, and high pressure common-rail fuel injection, along with control strategies to achieve emission targets without the use of aftertreatment. Miller valve timing is implemented without the use of a variable valve timing mechanism. Donor cylinders are used to supply EGR. The intake oxygen fraction required to meet both NOx and PM emissions is very narrow, about 1% from minimum to maximum. Thus, EGR control is via feedback of intake manifold oxygen concentration from a virtual sensor as well as closed loop control of brake specific NOx emissions. A NOx sensor in the exhaust provides both exhaust gas oxygen and NOx concentration measurements. The fuel efficiency penalty compared to the Tier 3 locomotive engine is about 1%.
GE also presented a dual fuel overhaul kit to bring EVO 12V250 locomotive engines to EPA Tier 3 emission levels [E. Dillen, #214]. The concept is built around the Otto cycle with gas injected into the intake ports and a diesel injection for ignition. A GE3000 locomotive for BNSF was used as a demonstrator and accumulated 30,000 km in revenue service until mid 2015. Additional demonstrator locomotives have been added for a current total of 3 and a total accumulation of 80,000 km. Additional demonstrator units are planned before year end with a total anticipated number of 25 by 2017. Production is planned for 2018. In the demonstrator locomotives, fuel substitution rates of 55-60% were achieved while the production target is 80% over the entire duty cycle. An oxidation catalyst is required for HC and CO control. LNG is vaporized using heat from the engine coolant. While Florida East Coast is interested in purchasing these locomotives, most other railroads have adopted a wait and see approach to LNG.
Turbochargers
While two-stage turbocharging has been considered for application to medium and low speed engines for many decades, the application to commercial products has been relatively limited. Older two-stage systems typically combined turbochargers designed for single stage operation into a package and the focus was primarily on achieving a higher pressure ratio than that capable of a single stage turbocharging solution. As a result, flow range and turbocharger efficiency was less than optimum. In the latest design iteration, the individual turbochargers of two-stage turbocharger packages are optimized to work together and not only are high pressure ratios achievable but efficiencies above those of single stage turbochargers are now possible.
In one presentation, Wärstsilä summarized their experience with two-stage turbocharging for medium speed engines [M. Vaarasto, #191]. The primary motivation for considering two-stage turbocharging in diesel engines is to lower engine-out NOx emissions via advanced Miller valve timing (see Figure below). With single stage turbochargers, the boost pressure is limited to about 5 and only relatively modest Miller valve timings and NOx reductions are possible. With two-stage turbochargers, pressure ratios close to 10 enable more advanced Miller timings to provide NOx reductions on the order of 50% along with improvements in SFOC of 7-9 g/kWh. A further benefit is that engine output can be further increased; a BMEP of 31.4 bar was achieved during development. For premixed charge gas and dual fuel engines where NOx emissions are low to begin with, the primary motivation is to increase engine output. Advanced Miller timing provides a cooler charger at TDC that is more pre-ignition resistant with an improved knock margin. BMEPs with gas in excess of 30 bar have been reported. With advanced Miller timings in both diesel and gas engines, variable intake valve timing is required to address start-up and part load operating challenges.
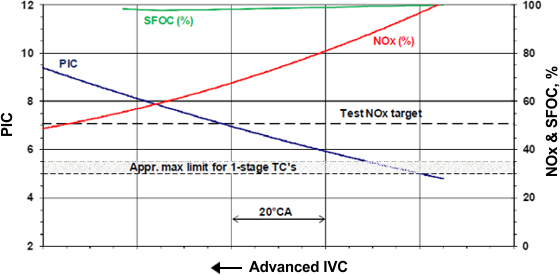
ABB examined several turbocharger options for a high output engine (28.5 bar BMEP) using an engine simulation model. While a sequential single stage turbocharger package could be selected that would provide the required boost and airflow to achieve the required output, a two-stage turbocharging solution offered about a 5 g/kWh SFOC benefit. More critically, the exhaust temperature with the single stage package was excessive and in practise, a 28.5 bar BMEP would not be possible.
In low speed two-stroke engines, realizing efficiency and engine output gains via turbocharging is more challenging than in 4 stroke engines [R. Ryser, #281]. In 2-stokes, increasing airflow to the engine would increase the scavenging flow through the engine and have little impact on trapped air mass; a small increase would result due to better flushing of residuals. One way to realize gains in engine efficiency would be to reduce the intake port height; this would increase the expansion ratio and improve engine efficiency. However, reduced port height increases the amount of residuals in the charge that increases compression work to offset any potential efficiency gains. In this work, ABB proposed incorporating a sleeve over the intake port that when coupled to a mechanism that moves the sleeve, would enable a variable intake port height. If the mechanism is also made fast acting, an asymmetric intake port height profile would be possible so that a longer expansion ratio is achieved while maintaining sufficient scavenge flow to keep the residual fraction low. While variable exhaust valve timing is a common feature in modern low speed 2-stroke engines that can be used to reduce the effective compression ratio for an effect similar to the Miller effect in 4-stroke engines, a variable intake port height would complement this by maximizing the expansion ratio.
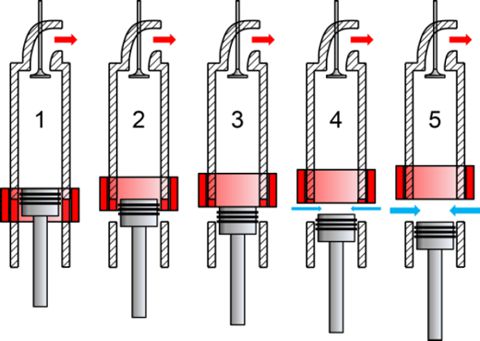
- Exhaust valve is fully opened
- Edge of piston crown reaches upper end of intake port
- Edge of sleeve reaches edge of piston crown
- Intake ports partly covered by sleeve; scavenging starts
- Intake ports not any longer covered by sleeve
Fuels and Lubricants
Ships that operate in and out of IMO Emission control Areas (ECA) are required to switch to low sulfur fuels when in the ECA. Cylinder lubricants with low sulfur fuel require acid neutralizing capabilities—the use of high base number (BN) oils with low sulfur fuels leads to hard calcium deposits on piston rings that scuff the cylinder. To make the switching between lube oils easier, MAN introduced an automated cylinder oil mixing (ACOM) system [D.M.S. Jacobsen, MAN Diesel & Turbo, #73]. The ACOM mixes two oils—of a low and of a high BN—in the right proportion depending on the sulfur content of the fuel.
Total [V. Doyen, #240] is attempting to solve the same problem using a new lube oil chemistry. The conventional high BN oils use calcium carbonate to neutralize acidic sulfur compounds, but can leave calcium sulfate deposits if too high of a BN is used for a given fuel sulfur content. A new, organic technology was developed, called Ash-free Neutralising Molecules (ANM), capable of neutralizing acidic compounds without the risk of deposits if the BN reserve is not used up. A new oil formulation—a combination of conventional and ANM chemistry—can be used with fuels of different sulfur content, inside and outside ECA.
Papers on oil and fuel filtration included a talk by Bosch [#45], who presented a new filter system for the hydraulic power supply system in 2-stroke engines, and by Drew Marine [#297], who introduced a depth filtration technology to protect engines from cat fines in residual fuels.
DNV GL, Netherlands [M. van Essen, #123] presented an interesting study on the effect of boil-off on the knock resistance of LNG gases. There are currently 156 LNG ships (77 in operation and 79 confirmed new builds) fueled by the boil-off gas. An LNG evaporation model was developed, which showed that the boil-off gas, initially methane and nitrogen,has high initial knock resistance. However, the methane number of the boil-off decreases during the voyage (due to increased proportions of propane and butane), potentially putting the engine at risk.
***
The 29th CIMAC World Congress will be held in 2019 in Vancouver, Canada.
Conference website: cimaccongress.com