Toyota, Denso introduce catalyst substrate with dual cell density
22 February 2017
Toyota Motor Corporation announced the commercial availability of a new flow-through catalyst substrate that utilizes different cell density in the inner and outer zones to provide a more uniform exhaust gas flow distribution through the catalyst. The new substrate will be used for the three-way catalyst (TWC) in the Lexus LC 500h later this year. Thanks to the new substrate technology, the catalyst will use 20% less precious metal than conventional catalysts, according to Toyota.
Please log in to view the full version of this article (subscription required).
The design—developed by Toyota and Denso Corporation—is the world’s first “integrally molded” Flow Adjustable Design Cell (FLAD®) substrate, with a different cell cross-sectional area at the inner portion compared to that at the outer portion. In the development process, both companies have improved the uniformity of exhaust gas flow within the catalyst by optimizing factors such as the ratios of cross-sectional areas of cells at the inner and outer portions, and their corresponding cell densities. The developed FLAD substrate design allows to use a more compact catalyst that contains 20% less volume and 20% less precious metal, while maintaining the same exhaust gas purification performance as that of conventional TWC catalysts. The newly developed design and manufacturing technologies have also allowed for the mass production of the world’s first integrally molded catalyst, said Toyota.
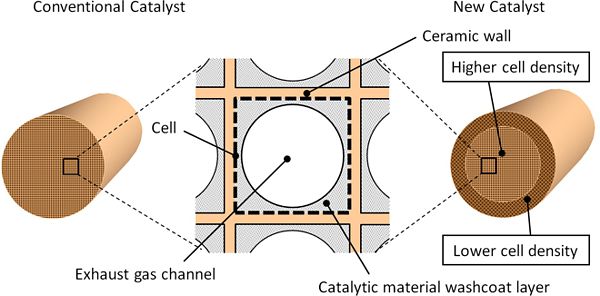
The most commonly used substrate in emission control catalysts for internal combustion engines is made of cordierite ceramic, which utilizes a honeycomb structure consisting of square or hexagonal cells. The walls of cells within the substrate are washcoated with catalytic materials, like platinum (Pt), rhodium (Rh), palladium (Pd) and other metals. While conventional catalysts have a uniform cell cross-sectional area, the newly developed FLAD substrate has a structure with a different cell cross-sectional area at the inner portion compared to that at the outer portion.
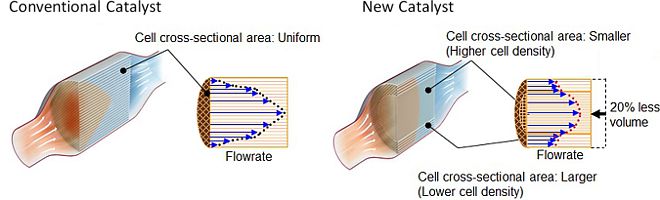
The use of conventional substrates with uniform cell density results in an unbalanced flow of exhaust gas, because the flow of gas through the inner portion of the catalyst is faster, and at a higher space velocity than that through the outer portion. As a result, the emission performance in the inner and outer catalyst channels is different, and the overall precious metal utilization is not optimal. In the new design, the more uniform exhaust gas flow within the catalyst enables a better utilization of the catalytic materials.
Source: Toyota