Conference report: 4th Conference on SENSORS for Exhaust Gas Aftertreatment and CO2 Reduction
21 July 2017
The 4th International Specialist Conference: SENSORS for Exhaust Gas Aftertreatment and CO2 Reduction—organized by SV Veranstaltungen—was held in Augsburg, Germany on June 27-29, 2017. The conference started with an introductory seminar on automotive exhaust gas sensors. The program in the following two days included presentations by academia and industry experts on various types of sensor technologies used in engines and emission systems. The conference program also included a trip to the MAN engine plant in Augsburg—arguably the birthplace of the diesel engine. Conference delegates could take a tour of the Augsburg manufacturing facility that has been producing diesel engines since the 1890s and currently manufactures medium-speed diesel engines, as well as of the MAN Museum that displays a number of historical engines, including some of the early diesel engine prototypes by Rudolf Diesel.
The introductory seminar, given by Stefan Carstens [EngineSens Motorsensor], started with an overview of sensors used for engine and aftertreatment control, followed by the principles, design and operation of several types of exhaust gas sensors, including temperature resistive probes (Pt200); NTC (negative temperature coefficient) thermistor based temperature sensors; thermocouple sensors; oxygen sensors (binary and wide-range); NOx sensors; pressure sensors for DPF monitoring; and soot sensors.
Technology and Market Trends. Among all types of powertrain sensors, sensors used in emission control systems remain the technology area of most new developments and growth, as evidenced by new patents [B. Kuhn, German Patent Office] and market data [K. Wasiluk, Schlegel]. In diesel engines, the main areas of development include sensors used in SCR systems and soot sensors for OBD of diesel particulate filters (DPF). In gasoline engines, most new developments are related to lambda sensors, O2 pumping, and sensors used in gasoline particulate filter (GPF) systems. The world’s market for powertrain sensors is predicted to reach $5.6 billion (and 1.36 billion units) in 2022 [R. Dixon, IHS Markit]. New devices like NOx and PM sensors experience fast growth in areas with stringent emission standards, while emerging markets drive the growth of conventional sensors.
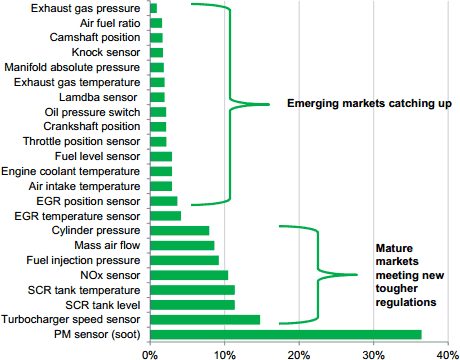
Pressure & Temperature Sensors. Hidria [P. Ursic], a Slovenia-based automotive component supplier, has developed a pressure sensor glowplug (PSG) by incorporating a lead-free piezo electric shear sensor and signal processing electronic circuitry into their diesel glow plug. The data processing algorithm, developed in-house, includes digital offset control to account for signal distortion due to pyroelectricity, leakage currents and mechanical loads. The pressure range is 0-260 bar, the output is analog, ratiometric to the +5V supply, the accuracy is ±2% (±0.25 bar below 12.5 bar). The company received an order for the PSG from a major diesel car maker—undisclosed by the speaker, but rumored to be Volkswagen. The production is scheduled to begin by the end of 2017. Virtual NOx and soot sensors are possible based on the pressure sensor.
Intake air humidity can affect both engine performance and emission measurements (for instance, NOx measurements can be very sensitive to humidity). ICT Engine Sensors [S. Chreif] developed combination sensors that incorporate relative humidity (RH) measurement in a temperature or temperature and pressure sensor. The humidity cell utilizes a water absorbing polymer between two capacity measurement electrodes. The modular design sensors are available in several configurations, including RH + T; RH + T + P; or RH + T + P + P (the latter version can compare the read pressure with barometric pressure, to determine a clogged intake air filter).
A new exhaust gas temperature sensor has been introduced by CMR [P. Flot]. The smart CAN sensor, intended for marine applications, utilizes a type K (chromel-alumel) thermocouple, which offered the best combination of lifetime and response time. The sensor represents “digital thermocouple” technology—signal conditioning and conversion to digital occurs in the sensor itself. Since these sensors have high information gathering potential inside, new functional possibilities are considered for the future. For instance, several sensors could communicate together, share their values to calculate an average value, and each sensor could record its own timeline of historical values.
Radio-Frequency Sensors. Radio frequency (RF) sensors have been used—albeit still on a limited scale—for a direct measurement of the soot mass collected in the DPF. CTS, a developer of RF-based soot sensors, has been expanding the sensor capabilities, to additionally provide OBD functionality in diesel and gasoline particulate filters [A. Sappok]. The upgraded RF sensors can be used for on-board preventive and reactive diagnostics (i.e., detecting actual failures), in addition to the soot load measurement. In field trials on heavy-duty trucks, the RF sensor could detect high soot emissions that lead to an uncontrolled regeneration many hours earlier than the engine control system—a functionality that allows to prevent DPF failures. Simulated defects measurements were conducted on cordierite and AT filters with artificially introduced soot leak defects, such as by removing some end plugs.
RF sensors have been also studied as a prospective tool to monitor other types of emission control catalysts. The University of Bayreuth [R. Moos] used an RF sensor to determine directly the amount of NH3 that is stored in the washcoat of an SCR catalyst. In engine dyno tests, the resonance frequency shift correlated well with the stored NH3. The method was verified with both gaseous ammonia and DEF dosing. However, a number of challenges remain, including temperature calibration of the RF signal, cold start effects, humidity, and poisoning effects. If these challenges are overcome, RF sensors can be used for SCR control [M. Moser, IAV]. A virtual NOx sensor was developed using the RF ammonia load signal. It was shown that the RF based SCR control—including a direct measurement of the stored NH3 and the virtual NOx sensor—could provide better and faster SCR control than the conventional approach using a hardware NOx sensor.
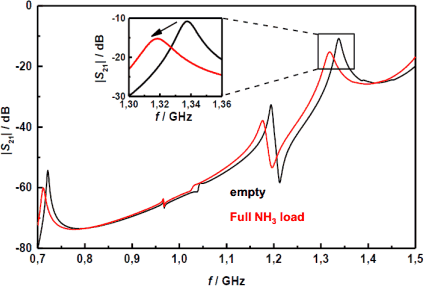
Other Topics. In another talk on virtual sensors, IAV [A. Bojahr] discussed the development of machine learning algorithms to determine connections and correlations between attributes. The work is based on very large data sets accumulated by logging hundreds of attributes controlled by the ECU, such as sensor data, actuator positions, status attributes and other information. The measurements are done while a car is driven under a variety of geographical and climatic conditions. To develop a virtual sensor—for example a virtual soot sensor—from such data sets, methods are being developed to identify attributes that are important for a given feature, and to quantify the attribute importance (correlation factor) and redundancy. Once the important attributes are selected, a model is built for the virtual sensor.
AVL [M. Arndt] discussed their Micro Soot Sensor (MSS)—a laboratory instrument for a fast, transient measurement of soot (black carbon) concentrations in combustion exhaust. The MSS operates based on the photoacoustic principle, where modulated laser light is absorbed by particles, leading to the emission of a sound wave that is detected by a microphone. The instrument has a measurement range from 1 µg/m3 to 50 mg/m3. Measurements upstream of a DPF are possible with a pressure reducing unit. Since the launch of the MSS, over 10 years ago, some 1800 units have been sold worldwide.
Switzerland’s Mems AG [D. Matter] has been developing a micro-thermal sensor for the measurement of natural gas quality in field applications. The gasQS instrument—based on CMOS technology with integrated hot-wire anemometer—can measure the thermal conductivity, heat capacity and density of gas. Additionally, calculated output includes the A/F ratio, methane number, Wobbe index and the calorific value.
CARIT Automotive/CPK provided an update on their development of a new NOx sensor technology [D. Bleicker]. The NOx sensor concept is based on solid, barium nitrate electrolyte with additions (metals). The sensor includes the solid electrolyte (sintered at 485°C), a substrate and a heater. Oxygen reacts with NO, forming nitrates in the solid electrolyte lattice. The concept has not yet been validated with NO2, cross-sensitivities, or poisoning. The project received funding from the German government under the NOx Arbeitsmobil program.