Conference report: SAE WCX 2018 Congress
30 April 2018
The SAE “World Congress Experience” (WCX 18) was held April 10-12, 2018 in Detroit, MI. The Congress included a three-day schedule of technical sessions, keynote and panel discussions, as well as an exhibition. The technical program included 1,348 presentations (1298 technical papers and some oral-only talks) covering all areas of automotive technology, including a number of papers on engines, engine efficiency and emission topics. The event had over 11,000 attendees and more than 200 exhibitors—slightly more than last year—on the show floor.
Please log in to view the full version of this article (subscription required).
Technical sessions on engine and vehicle emissions were opened, as in previous years, with a review of recent regulatory and technical developments in vehicle efficiency and emissions, presented jointly by Tim Johnson and Ameya Joshi of Corning [Paper #2018-01-0329]. Attended by hundreds of listeners in a room filled to capacity, it was the final review talk given by Dr. Johnson, who announced his intention to retire from this role. The review started with a summary of upcoming emission regulations. These include the newly proposed EU CO2 emission targets, with 15 and 30% emission reductions in 2025 and 2030, respectively, from 2020 levels. The real driving emissions (RDE) regulations continue to evolve; the tests are now conducted using the moving window method, while power binning has been discontinued. Euro 7 regulations are considered; while there is no proposal yet, it is expected the Euro 7 standards will be fuel neutral, the PN cut off will likely be lowered from 23 nm to 10 nm, additional emission limits are possible for NO2, NH3, N2O, HCHO, and a low temperature type approval test (-7°C) may be added. China is tightening emission standards, with China 6a (2021) and China 6b (2023) stages scheduled for both light- and heavy-duty engines. For nonroad engines, China is adopting Tier 4 regulations, similar in stringency to the US Tier 4i, but additionally including a PN limit that will force the use of particulate filters. The talk also covered the most promising engine efficiency technologies and concepts—including HCCI with spark assist, 2 stroke opposed piston engines, Mazda’s spark controlled compression ignition, and GDCI (Delphi’s gasoline DI CI)—as well as new developments in diesel and gasoline emission aftertreatment.
Diesel Emission Strategies. SwRI [C. Sharp, oral only] provided an update on the CARB low NOx heavy-duty vehicle program, which targets NOx emission levels of 0.02 g/bhp-hr. While the first phase of this project has been completed, a follow-up project targets some of the challenges faced in the previous phase. In the earlier work, some of the aftertreatment parts were damaged during full useful life (FUL) aging. It is unclear how this damage affected the final emissions results. Stage 1 of the follow-up project will repeat the FUL aging and retest with the 2014 MD13TC Euro VI Volvo engine. Preliminary emissions results look encouraging so far with the degreened FTP results matching those of phase 1. Emissions over the RMC cycle are better (0.001 g/bhp-hr NOx) primarily due to improved control system performance. Final FUL results are expected July 2018.
Stage 2 of the follow-up program will test the system over several low load and urban drive cycles as well as develop a new low load duty cycle using NREL’s Fleet DNA and CARB/CE-CERT data. The test engine will then be re-calibrated to achieve a high NOx conversion efficiency over low load profiles and then demonstrated over the low load as well as regulatory cycles. While the final NOx limits of the future CARB HD engine emission regulations is unclear, it is quite certain that emission control at low loads will become a regulatory requirement.
Stage 3 of the program will switch to a 2017 Cummins X15 engine. Importantly, this engine has no turbocompounding as the Volvo engine did and it is hoped that this will simplify the aftertreatment system. Some of the technologies being considered include cylinder deactivation, an air gap insulated exhaust manifold, exhaust turbine bypass, EGR cooler bypass and CAC bypass.
For some medium duty applications, meeting US EPA Phase 2 GHG reductions may put significant pressure on improving engine efficiency because of limited opportunities to make improvements to the vehicle. FEV evaluated two technology packages that could improve engine fuel efficiency by 7-10%: (1) downspeeding, two-step variable compression ratio (VCR) system, cylinder deactivation and turbocompounding; (2) downsizing (5.1 L four cylinder) and two-step VCR system [2018-01-1429]. However, these technologies require measures to accelerate the light-off of the SCR catalyst in order to meet a NOx limit of 0.02 g/bhp-hr. A heating strategy that involves “intelligent use of an HC doser and an electrically heated catalyst” provided the lowest NOx emissions while keeping the fuel penalty associated with heating relatively low. This heating strategy combined with the downsizing/VCR package and an aftertreatment system consisting of eDOC + SCRF + SCR + ASC could achieve about 15 mg/bhp-hr NOx with a 7.4% reduction in fuel consumption over a baseline 7.7 L six cylinder engine.
Some options for light-duty diesel engines to comply with California LEV III SULEV 30 requirements were presented by FEV [2018-01-0877]. Improved air and fuel system control accuracy could provide 35-40% reduction in engine-out NOx from a LEV II vehicle. The parameters requiring the most improvement include: air mass, boost pressure and fuel rail pressure. Some of the technologies discussed in more detail included an electric intake air compressor, fuel injection controls to compensate for individual injector drift and changes in multiple injection patterns and combustion rate shaping. Aftertreatment system details will also be critical—especially measures to accelerate catalyst warm-up and/or lower cold start emissions. Aftertreatment system architectures such as LNT-DPF-SCR and ccDOC/SCR-SCRF-ASC, the later with two urea dosers, appear promising. To facilitate catalyst light-off, a combination of early exhaust valve opening combined with a reduced intake valve lift can raise DOC inlet temperature faster and maintain lower space velocity and longer residence time in the DOC without affecting fuel economy; a 30% reduction in NOx over the WLTC is claimed. An electrically heated DOC can provide significant increases in catalyst light-off as well with a simulated decrease in SCRF light-off time of about 100s. Incorporating components with high electrical power demands such as the electric compressor and electrically heated catalyst would be greatly facilitated with a 48V mild hybrid architecture that could offset at least some of the power demand through recuperation of braking energy.
SCR Technology. The Sustained Low Temperature NOx Reduction program was a US DOE-funded collaborative effort by Cummins, Johnson Matthey, and the Pacific Northwest National Lab to develop an SCR system that would achieve a 90% NOx conversion at the SCR catalyst inlet temperature of 150°C [2018-01-0341]. A hybrid Fe-Cu/zeolite SCR catalyst was selected of relatively low sensitivity to the NO2/NOx ratio. Another advantage of the catalyst was it did not produce ammonium nitrate—an SCR catalyst contaminant formed from NH3 and NO2 at low temperatures. While the 90% NOx reduction target has been demonstrated, major challenges remain before the system can be used in commercial engines. One of these is to achieve the required NO2/NOx ratio at 150°C. One approach used in the project was to position the DOC in the pre-turbo location. Another key challenge is to atomize urea to supply droplets below 10 µm—an ultrasonic urea doser was used to achieve this objective.
Ammonium nitrate (AN) can also be formed on an ammonia slip oxidation catalyst (AMOX). In laboratory reactor experiments conducted by Cummins, AN was formed over the 100-175°C temperature range, with a significant negative effect on the catalyst BET surface area [2018-01-0342]. No significant AN formation at 175°C and above occurred in the presence of NO. It was suggested that NO may mitigate AN formation in real world, due to a reaction between AN and NO that leads to chemical decomposition of AN.
Another SCR study by Cummins [2018-01-0347] studied N2O formation over a Cu-Chabazite (SSZ-13) catalyst. There are two types of active sites in the Cu-SSZ-13 structure, referred to as Z2Cu and ZCuOH. The two types of sites appear to have similar SCR reactivity, but different N2O selectivity. Two catalysts were prepared with different distribution of the Cu species. The sample with more ZCuOH sites showed higher selectivity to N2O.
A team from Isuzu [2018-01-0346] reported on the improvement of their SCR model by accounting for the oxidation of NH3 by adsorbed NO and NO2. The new model was more accurate in predicting NOx conversion, especially at high temperatures.
Vanadia-based SCR catalysts remain an attractive option for heavy-duty diesel engines. In addition to their low cost, V-SCR catalysts show excellent sulfur tolerance, and are chemically robust—meaning they can be used with low quality diesel fuels. Some 30% of Euro VI engines use vanadia catalysts, while their use in the US market is limited to (nonroad) engines without DPF, due to concerns about vanadium release at high temperatures (such as during DPF regeneration events). Umicore [A. Åberg, oral only] presented some experimental results on vanadium release using the test procedure recommended by the US EPA. One of the experiments was carried out with an ammonia slip catalyst downstream of the SCR sample. No vanadium release was measured, which suggests that an AMOX catalyst might provide a degree of protection against vanadium release. V-SCR catalysts were also studied by Cummins Emission Solutions [Y. Xi, oral only], who conducted a laboratory investigation of the formation of carbonaceous deposits by unburned fuel and lube oil, using three different hydrocarbon species and different operating conditions. Lower content of water vapor in the gas, such as encountered during engine idle, caused increased deposits for all three HCs studied.
Hino Motors discussed an HC-SCR (also known as the lean NOx catalyst) emission system using diesel fuel reductant that was commercialized on a medium-duty vehicle meeting the JP2016 emission standards (NOx = 0.60 g/kWh) [2018-01-0345]. The emission system provides about 60% NOx reduction above 200°C. Two HC-SCR catalysts are used, each with its own fuel injector, to cover the required temperature window. A Pt/Pd catalyst located in one housing upstream of a catalyzed DPF provides the low temperature reactivity. An Ag/alumina catalyst, in a separate housing downstream of the DPF, provides NOx reduction at medium to high temperatures. The Ag catalyst is followed by a passive (i.e., with no urea injection) Cu/zeolite NH3-SCR catalyst and another Pt/Pd DOC. Two NOx sensors are used to control the rate of injected fuel.
Umicore evaluated sulfur poisoning and desulfation behavior of diesel oxidation catalysts (DOC), with focus on the NO2 generation functionality that is needed in SCR applications [2018-01-1262]. A number of Pt/Pd formulations of varying Pt:Pd ratios, from Pt-only to Pd-only, were evaluated. Catalyst samples were poisoned by exposure to 40 ppm SO2, and desulfated at temperatures of 300-500°C. DOCs containing combinations of Pt/Pd were more sensitive to sulfur poisoning, especially for NO oxidation (as opposed to HC oxidation). This suggests that Pd becomes poisoned by the SO3 generated over Pt sites (Pd-only catalysts did not produce SO3). It was recommended that tailored DOC desulfation procedures be implemented in SCR systems to keep the NO2 content within the target range, and to enable lower PGM loadings.
When released into the atmosphere, NO2 may present a health issue due to its higher reactivity and toxicity compared to NO. A stand-alone NO2 emission limit, in addition to a NOx limit, may become a part of the future Euro 7 regulations. Cummins Emission Solutions provided an overview of the impact of modern diesel emission control catalyst technologies on NO2 concentrations [2018-01-0651]. Component-level reactor-based experiments were conducted on DOCs (Pt/Pd), a DPF (Pt/Pd), an CuZ-SCR catalyst, and an AMOX catalyst. While the particular catalysts could contribute to both NO2 formation and consumption, the evaluated DOC + DPF + CuZ-SCR + AMOX aftertreatment system reduced tailpipe NO2 emissions from 83 to 94% in comparison to engine-out.
CI Engines. FEV presented a novel approach to integrating turbocompounding, electrification and supercharging [2018-01-0887]. They propose using a planetary gear system equipped with a dry clutch and a band brake. A secondary compressor is connected to the ring gear, a turbocompounding turbine or organic Rankine cycle (ORC) expander to the sun gear and an electric motor/generator (M/G) to the carrier gear. Depending on speed and load, this arrangement allows switching between electric turbocompounding and mechanical turbocompounding or using a combination of the two (power-split turbocompounding). As well, the secondary compressor (C2) can be powered by the power turbine (T2) and/or the M/G. The M/G can still provide torque boost to the engine while C2 is active. While there is a small additional drive cycle benefit relative to independent integration of the same components on the engine, a packaging and cost advantage is claimed for the ITES. Details of the packaging and cost advantages will be presented in a future publication.
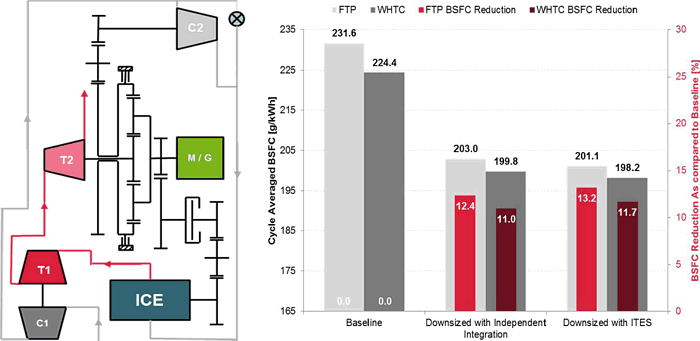
SwRI has evaluated the effect of lower engine oil and coolant flow requirements on a 2012 Cummins ISX 15L 450 hp engine [2018-01-0980]. No high pressure EGR is used. The engine was part of SwRI’s CHEDE-IV project. They found that engine coolant flow could be reduced significantly while still ensuring engine ΔT did not exceed 8°C and that the valve bridge and liner temperatures did not exceed the highest values measured with the stock coolant flow. Even at full load conditions, the coolant pump power could be reduced significantly and the resulting increase in BTE is shown below. Oil flow was reduced to the point that the required oil pressure could be maintained without opening the pressure relief valve and the resulting BTE benefit is also shown below. Other measures were also evaluated including: replacing one-to-one crankshaft drillings with one-to-two drilling to reduce number of grooved (up to 0.15 increase in BTE) and shutting off piston cooling (0.8-1.2 increase in BTE) The benefit from shutting off piston cooling was attributed to lower oil pump losses and lower heat losses from the combustion chamber due to higher piston temperature.
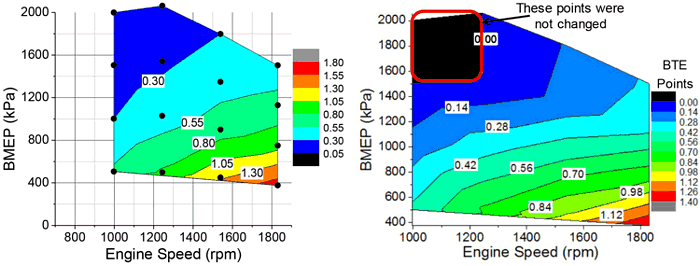
Cylinder deactivation (CDA) is a technology that is gaining interest for diesel engines. Unlike for SI engines where the primary purpose of CDA is to reduce pumping losses, the interest for CI engines is primarily for thermal management of the aftertreatment system to maintain higher catalyst temperatures. The lower exhaust flow equates to less heat transfer from the aftertreatment system and provides a more fuel efficient alternative to other exhaust temperature management techniques. Purdue University., Eaton and Cummins demonstrated that at steady state loaded idle, the fuel savings can be as high as 40% compared to other thermal management strategies that achieve similar exhaust temperatures. At higher engine speeds, CDA provides a 5% - 32% improvement in fuel economy, an increased rate of aftertreatment system warm-up, higher steady state temperatures and the possibility of active diesel particulate filter regeneration without hydrocarbon dosing of the DOC. At a highway cruise condition, half-engine CDA and two-third engine CDA can be used to reach engine outlet temperatures of 520-570°C, a 170-220°C increase. Full engine CDA enables reductions in motoring torque that could help save fuel and keep the aftertreatment system warm during vehicle coasting [2018-01-0384]. Over the heavy-duty FTP cycle, a 3.4% fuel economy benefit was noted. Fuel savings were more significant over Orange County bus cycle (5.6%) and the Port Drayage Drive Cycle (4-35%) [2018-01-0880]. A variable CDA implantation strategy is recommended by Eaton based on NVH considerations [2018-01-1284].
Another opportunity to improve engine efficiency in medium-duty diesel engines being promoted by MAHLE is a change in piston material [2018-01-1275]. Many medium-duty engines continue to use aluminum pistons for cost reasons. This limits peak cylinder pressure (PCP) to about 19.5 MPa and thus the potential to improve engine efficiency. While the required efficiency gains required may not warrant the cost of switching to forged steel (up to 26 MPa PCP), a material that would allow PCP to increase to about 23 MPa may be an attractive option. Nodular cast iron is one such material that offers some of the benefits of forged steel (reduced compression height and lower thermal conductivity) but at a lower cost. The potential fuel consumption benefit is claimed to be 2-4%.
SuperTurbo Technologies (formerly Van Dyne SuperTurbo) presented simulation and engine testing results that showed their SuperTurbo can provide a fuel savings of about 6% over part of the JE05 transient cycle. The ability to downspeed the engine can provide an additional 3% savings for a total potential improvement of 9% [2018-01-0970].
SI engines. Mahle is developing a 35 bar BMEP, 160 kW/L heavily downsized 1.2 liter, 3-cylinder demonstration engine (Di3). The engine is fitted with Aeristech’s 48V electric supercharger. In its current configuration, excess fuel is required above power levels of 90 kW/liter in order to protect the turbine from excessive exhaust gas temperatures (930°C max). An analytical study showed that cooled HP EGR (max EGR rate 15%) with the electric supercharger located downstream of the main turbocharger compressor, has the potential to enable stoichiometric operation up to 160 kW/L maximum power output [2018-01-0975].
Tula Technologies cylinder deactivation technology, Dynamic Skip Fire (DSF), was discussed in numerous presentations. While the potential fuel economy benefit of DSF can be as high as 15%, in practice is limited to more modest levels of around 8% due to NVH considerations. One option to further enhance the benefit of DSF is to use the motor/generator unit of a 48V hybrid to counteract some of the torque pulses. This approach can provide an additional ~2% fuel economy benefit (eDSF) [2018-01-0864]. In another example, DSF was shown to be an option to extend the benefits of lean operation in a homogeneous lean burn engine to very low loads; DSF avoided the need to enrich AFR at these conditions (λDSF). A 5-10% fuel consumption benefit over certification cycles plus higher low load exhaust temperature is possible [2018-01-0891]. DSF can be combined with Miller cycle operation in a way that randomly operates some cylinder with Miller intake valve timing and some without for a 7-% drive cycle fuel economy benefit relative to a standard Miller cycle engine (mDSF) [Ortiz-Soto, oral only]. Standard OBD misfire detection techniques are not suitable for DSF due to larger random variations in crankshaft accelerations. Instead, a technique based on crank acceleration that takes the skip fire sequence into account is proposed [2018-01-1158]. Fuel injection control also needs to account for variations in inducted air mass in order to minimize emissions and improve efficiency in the low load range [2018-01-1284].
3M has developed pervaporation separation modules made with flexible organic membranes that selectively remove and concentrate ethanol and methanol from gasoline blends. The application of this to Octane-on-demand, i.e, high octane components of commercial fuels are injected only when needed, was discussed in two papers. Honda evaluated the performance of a separation module for up to 15% ethanol and up to 15% methanol blends and for aromatic separation capability and stability [2018-01-0882]. A study by MIT evaluated its use for medium-duty applications. The reduction in fuel economy is modest compared to a two tank system with pure ethanol while the need to fill a second tank is removed. Fuel efficiency gains ranged from 17.5-30% with commercial E10 gasoline. With E10, the module can provide a 30 to 90% ethanol fuel blend [2018-01-0879].
BorgWarner has been promoting divided-exhaust turbocharging as a means to improve turbocharging efficiency in SI engines since at least 2010 [2018-01-0895]. In this approach, one exhaust valve and port from each cylinder can be directed to the turbocharger turbine and the other can bypass the turbocharger. Significant engine efficiency and performance improvements over the base turbocharged engine as well as a large improvement in catalyst light-off performance (it can completely remove the turbocharger from the exhaust pathway during the cold-start period) are claimed. Early work used a concentric exhaust cam with two cam phasers and was referred to as Valve Event Modulated Boost (VEMB). To simplify the hardware requirements, a version using a solid exhaust cam with a single cam-phaser has been developed and is referred to as Divided-Exhaust-Boost (DEB or DE-Boost) that retains the previously reported improvement in aftertreatment system light-off.
FEV discussed a smart battery charging strategy that could contribute up to 2% improvement in fuel economy in conventional non-hybrid vehicles [2018-01-0326]. In this approach, the alternator load is increased during vehicle braking to convert some of the vehicle’s kinetic energy into electrical energy stored in the battery. Upon vehicle acceleration, the load on the alternator is reduced. Smaller, low mass vehicles gain the most relative benefit from this approach.
Conference website: wcx18.org