Conference report: 5th Conference on Emission Reduction and Emission Sensors
25 July 2018
The 5th International Conference: Emission Reduction and Emission Sensors—organized by SV Veranstaltungen—was held in Stuttgart, Germany on July 10-12, 2018. The conference started with an introductory seminar on automotive exhaust gas sensors. The technical program in the following two days included presentations by government, academia, and industry experts on two groups of topics, organized in two parallel tracks. The first track covered emission reduction of exhaust pollutants and CO2; the second track focused on various types of sensor technologies used in engines and emission control systems.
Please log in to view the full version of this article (subscription required).
The introductory seminar was given by Stefan Carstens [EngineSens Motorsensor]. It started with an overview of sensors used for engine and aftertreatment control, followed by the principles, design and operation of several types of exhaust gas sensors: temperature resistive probes (Pt200); NTC (negative temperature coefficient) thermistor based temperature sensors; thermocouple sensors; oxygen sensors (binary and wide-range); NOx sensors; pressure and RF sensors for DPF monitoring; and soot sensors.
Regulatory Trends. Among the many regulatory changes in the EU, such as the new WLTC test cycle for vehicle type approvals and Euro 6d-TEMP emission standards with RDE (Real Driving Emissions) testing requirements, the proposed post-2020 CO2 emission standards may present the biggest challenge for engine and vehicle manufacturers. For the first time ever, CO2 standards have been proposed for heavy-duty vehicles [D. Savvidis, European Commission]. The proposed standards require a 15% emission reduction by 2025 (relative to 2019), and a 30% emission reduction by 2030. Emissions are determined using the VECTO simulation tool. The VECTO based CO2 certification regulation is already in place, with 2019 as the first CO2 reporting year.
In light-duty vehicles, the proposed post-2020 CO2 standards have a similar two-tier structure: a 15% emission reduction by 2025 (relative to 2021) and a 30% reduction by 2030 [H. Jahn, German UBA]. These targets are considered impossible to meet without a significant penetration of the light-duty vehicle market by electric vehicles (EV). The proposal includes non-binding EV targets of 15% by 2025, and 30% by 2030. EVs can generate additional emission credits—for each percentage point of exceeding the EV target the manufacturer CO2 target is reduced by 1%, up to 5% max.
The declining market share of diesel vehicles is clearly counterproductive in achieving CO2 targets. In 2017, EU CO2 emissions increased slightly, for the first time, due to the smaller diesel share. According to some analysts [J. de Groot, Dataforce], by 2021, EU carmakers may face a 9 g CO2/km gap from the regulatory target, which could cost them a potential 7.9 billion euros in CO2 non-compliance penalties. Some 5% penetration of EVs could potentially eliminate the gap. However, a wider adoption of EVs would require large-scale infrastructure projects that are characterized by long duration, high cost, and unpredictable risks [J. Madalinski, U Dortmund]. The study also pointed out that EVs—while assigned a zero CO2 emission value by emission regulations—are not zero-emission vehicles when their life cycle analysis is considered. Emissions from battery production were found to be a sustained disadvantage of battery electric vehicles (BEV). A higher life cycle CO2 reductions could be provided by H2 fuel cell vehicles—albeit at a higher cost—and by combustion engine vehicles fueled by renewable methanol.
Sensors. The flame ionization detector (FID) is a conventional method for laboratory hydrocarbons measurements. It relies on the production of free electrons and ions during combustion of HCs in a hydrogen flame. The Fraunhofer Institute [S. Ziesche] has developed a miniaturized version of the FID detector, intended for use as a part of portable (PEMS) analyzers. The system includes the miniaturized FID, an electrolyzer for the combustion gas supply, supply of water, electronics and packaging. Using the multilayer ceramic technology, the FID was miniaturized into a square of about 15 × 15 mm. The electrolyzer, based on proton-exchange membrane (PEM) technology, has also been considerably miniaturized. The electrolyzer is integrated with a water reservoir (2 liters of water allow for 6 months of operation). The system can be operated as a highly sensitive or a low fuel consumption device, depending on the application.
A new accumulating, resistive soot sensor has been introduced by Stoneridge [T. Essert]. The sensor has been in series production since December 2015, for US market as well as Euro VI applications. The current Gen II version was launched in early 2018. The sensor utilizes two comb-structured, interdigital electrodes. However, contrary to the soot sensor from Bosch, each of the electrodes forms a closed circuit, which makes the sensor self-diagnostics easier. The sensor is also claimed to have a faster response time, with several complete measurement-regeneration cycles possible within the WLTC cycle. The comb electrode structure itself serves as a heater, with sensor regeneration conducted at 775°C.
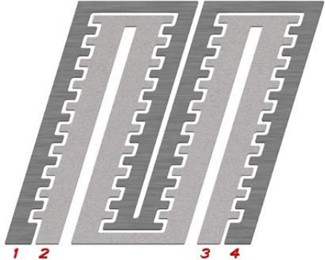
Emission Control and OBD. Mann+Hummel presented a fine dust filter designed to remove particulate pollution from ambient air, rather than from vehicle-based sources. The “Fine Dust Eater” system is available in a stationary as well as mobile version (figure below). The mobile system, which can be installed on light- and heavy-duty urban vehicles, utilizes replaceable dust filters and a bank of fans (top-right in the figure) to drive sufficient air flow through the filter. While the efficacy of this approach remains to be demonstrated—reducing pollutants at their source would appear much more cost-effective—the company expects the system will find demand in high PM2.5 pollution cities in Europe and Asia, where authorities are under political pressures to reduce pollution. The demonstrator vehicle was also fitted with a brake dust particle filter (bottom-right).
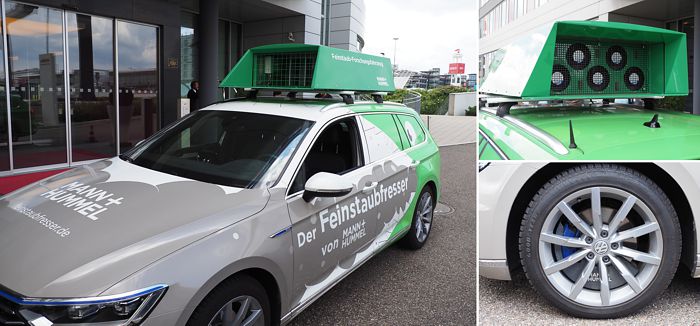
Gasoline particulate filters (GPF) are being rapidly adopted in Europe and are also expected to be widely used in China. Some GPFs may also be introduced in California LEV III applications. The respective OBD monitoring requirements (EU 6-2, CN 6, and LEV III) were reviewed by Bosch [C. Schauz]. Three types of OBD monitoring were proposed, including pressure based monitoring, temperature based monitoring and the use of a HEGO sensor to monitor the oxygen storage capability (OSC) of a catalyzed GPF. The monitoring of GPF for removal can be achieved through both the pressure and temperature methods. In the pressure based method, a differential pressure sensor is used—the method also monitors the hoses connecting the sensor. In the temperature based method, temperature sensors must be positioned close to the GPF, in the inlet and outlet cones.
Cybersecurity is becoming an increasingly important topic in automotive technology and particularly in OBD [M. Weber, Roben Automotive]. The current OBD systems have been designed without cybersecurity considerations—for instance, there is no user authentication in current OBD and important commands and operations, such as ECU reset, can be executed by anyone. Vehicle connectivity technologies further increase the risks. Existing OBD systems are designed for non-connected applications, and only the technician can send commands through the OBD interface. In connected vehicles, the OBD system can be manipulated by a hacker, who can access other vehicles and/or more data once the system is compromised. Standards are being developed, e.g., SAE J3061, to harden OBD systems and data links against cybersecurity threats.