Conference report: ASME ICE 2019 Fall Technical Conference
31 October 2019
The ASME Internal Combustion Engine 2019 Fall Conference (ICEF 2019) was held on October 20-23, 2019 in Chicago, IL, USA. The event, attended by more than 200 delegates, included a two-day technical program with 76 technical papers, 17 posters, as well as keynote talks, and student presentations. After the Conference, the participants could take part in a technical tour of the Argonne National Laboratory in Chicago.
In one of the keynote talks, Dr. Amer A. Amer, Chief Technologist, Fuel Technology Division, Saudi Aramco, argued that internal combustion engines can offer a GHG emissions benefit over electrification if all lifecycle emissions are accounted for. Compared to a scenario of 50% BEV penetration, GHG emissions from an ICE pathway were estimated to be 2086 Mt lower in the US and 2266 Mt lower in China by 2040. Some ICE technologies that could reduce GHG emissions being developed at Aramco include gasoline compression ignition (GCI), turbulent jet ignition, alternate energy architectures such as the 2-stroke opposed piston engine, improved aftertreatment systems, mobile carbon capture and fuel optimization.
A number of projects incorporating these technologies are in progress. In one project, a turbocharged Miller cycle engine has demonstrated a 15% improvement in mpg compared to naturally aspirated GDI engine. Further work to increase the benefit to a 20% increase in mpg is ongoing and includes 48V mild hybridization. A demonstration of is expected in 2020.
Another project focused on GCI has demonstrated a 30% improvement in mpg compared to naturally aspirated GDI engine. A 40% improvement target is under development that is expected to be demonstrated in 2023. Ultra low NOx and soot are expected.
A third project focusing on lean combustion uses a compression ratio of 17 and provides a 5% fuel consumption benefit compared to DI diesel.
Work on opposed piston two stroke engines is being carried out with Achates Power from the US and INNEngine from Spain. The Achates Power engine is an inline 3 cylinder engine that incorporates GCI. With the INNEngine, the pistons are arranged around a central shaft to provide a compact power unit.
Work on mobile carbon capture (MCC) has been ongoing since about 2010. A 42% GHG reduction has been demonstrated on a Class 8 Volvo truck with a target of 50% expected to be reached in the near future. The 50% target includes a 10% benefit from engine efficiency improvement using GCI. The marine industry has also expressed interest in this technology.
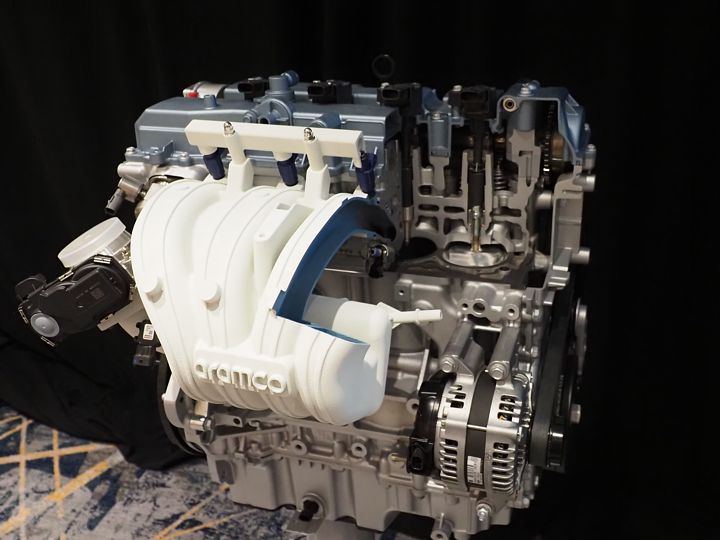
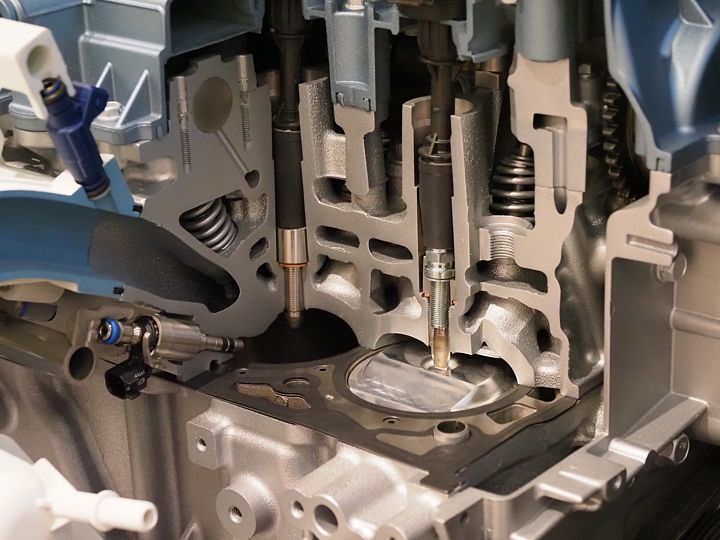
In another keynote, Don Hillebrand, Director of Argonne National Laboratory’s Energy Systems Division raised the topic of the effect of vehicle autonomy on energy consumption and GHG emissions. According to estimates by the DOE, vehicle automation could lead to an energy consumption increase of up to 200% or a decrease of 60% [4534]. The large uncertainty arises because the effect of automation on vehicle miles traveled (VMT) and vehicle efficiency (mpg) is unknown. The 200% increase in energy consumption would arise if efficiency remains at current levels (mpg) and VMT increases significantly due to easier travel, empty vehicle travel or higher speeds. The 60% decrease would result if VMT remains relatively unchanged but efficiency improves significantly.
While many advanced engine strategies are being developed with the aim of reducing emissions and increasing engine efficiency, Hyundai demonstrated that current commercial engine technologies continue to evolve and can be adapted to achieve similar results. They presented a light-duty GDI engine concept capable of a 44% BTE with 92 RON gasoline and stoichiometric operation with EGR dilution. The 2.2 L inline four-cylinder engine had a . stroke to bore ratio of 1.4 (110 mm stroke and 79 mm bore) and 15.2 compression ratio. Knock was suppressed with high levels of EGR dilution at high loads. Additional features included an intake port modified to increase tumble flow for a reduced combustion duration at low and high load and extended EGR-stability limit. Twin spark plugs were also used to ensure stable, complete and fast combustion. Additionally, a 48V electric supercharger was applied with the longer intake camshaft duration of 280° (Atkinson cycle) [4545].
Natural Gas And Dual Fuel Engines
Hoerbiger Service and Advanced Engine Technologies Corp. upgraded a 1980’s Enterprise DGSR-48 dual fuel engine driving a generator to achieve < 2 g/bhp-hr NOx. The engine had been equipped with a low pressure prechamber micropilot and mechanical pressure controlled port fuel-gas admission system. The upgrade included a high pressure direct injection micropilot system using DUAP injectors and pulse-width modulated gas injectors in the intake ports. A continuous combustion pressure monitoring and balancing system was also added. The system was able to easily meet the NOx requirements and was capable of pilot quantities of 2% and less [4546].
Hoerbiger Service and Advanced Engine Technologies Corp. also presented work on upgrading low BMEP gas compression engines to achieve 0.5 g/bhp-hr NOx. These engines are challenging because the exhaust does not typically supply sufficient energy to allow only a turbocharger to be used to achieve the trapped equivalence ratio (TER) required for these NOx levels. In one example for a 10 cylinder piston scavenged GMV-TF two-stroke, achieving the required TER for 0.5 g/bhp-hr NOx required 210 hp to be supplied to an intake compressor but only 145 hp would be available from an exhaust turbine. An electrically driven intake blower powered by a 300 hp electric motor was instead selected. Additional modifications included: new cylinder heads with in-head scavenged pre-chambers for improved ignition of leaner mixtures, an aftercooler for controlling intake manifold temperature, an oxidation catalyst for CO, VOCs and formaldehyde, a dry exhaust manifold for increased exhaust temperature and updated controls. This brought NOx emissions down from 6 g/bhp-hr to the target value of 0.5 g/bhp-hr. While the electric blower increased electricity demand, fuel savings from improved engine efficiency were sufficient to offset almost all of the increased electricity costs [4547].
NOx emissions variations from upgraded two-stroke gas compression engines can be a challenge if significant variations in gas composition occur. This is a common issue in shale gas production. One control option for these upgraded engines studied by Texas A&M and Hoerbiger is to use scavenging efficiency to estimate TER in real time. While controlling to a desired TER can achieve a required NOx emission rate in many applications, when fuel composition varies considerably this is insufficient. In these cases, control approaches that also account for fuel composition variations are needed to ensure NOx compliance [4549][4548].
As natural gas prices remain low, interest in converting heavy-duty diesel engines to spark ignited natural gas remains one option to take advantage of the potential for operating cost savings. The combustion chamber of shape of these engines, a flat head and bowl in the piston, creates some unique combustion characteristics as demonstrated by West Virginia University. Combustion follows a two-stage process with fast burning inside the bowl and a slower burn in the squish region. The slow late burn in the squish region leads to a retarded end of combustion and could explain some of the increased carbon monoxide and unburned hydrocarbon emissions from these engines [4550][4551][4552].
The National Research Council Canada investigated GHG emissions from a dual fuel engine at different load, speed, injection timing, and with the natural gas fraction ranging from 0 to 80% [4535]. The contribution of N2O to the overall GHG emissions was not significant. However, high CH4 emissions were measured, especially at lower loads. The engine was converted from a diesel engine, and one possible source of CH4 emissions was the negative valve overlap. To ensure GHG emission reductions relative to 100% diesel operation, diesel injection timing adjustments may be required. This is especially the case at low load conditions were advancing the timing to 25 - 50°BTDC was able to still provide a modest GHG emissions reduction relative to diesel operation.
The University of Rostock, AVL and FVTR investigated the inverse behavior sometimes seen between the timing of injection and ignition events in dual fuel engines—as pilot injection timing is advanced, ignition timing retards and vice versa. Using simulation tools, they found that early injection at low cylinder temperatures leads to increased premixing and enleanment of the pilot fuel spray cloud that leads to longer ignition delay and later ignition of natural gas [4553].
Gasoline Compression Ignition (GCI)
Future NOx limits such as CARB’s proposed 0.02 g/bhp-hr limit present a significant challenge for heavy-duty engines. For current diesel engines with 4-6 g/kWh engine out emissions, deNOx efficiency of > 99.5% would be required. While potential solutions such as dual dosing SCR systems are being developed to achieve such conversion efficiencies, the possibility of lowering engine out emissions while still maintaining high thermal efficiency continues to be explored. One example of the later approach is the work being carried out at Aramco with support from Cummins on gasoline compression ignition. A 2013 Cummins ISX15 is being used and engine-out NOx of 1-2 g/kWh is being targeted. A combination of mixing-controlled and partially premixed GCI combustion is being used rather than full-time partially premixed combustion. This minimizes the EGR and boost demands and makes the concept more applicable to multi-cylinder engines with a practical air handling system. Initial work used CFD to investigate the effects of piston bowl geometry, injector spray pattern, and in-cylinder swirl motion on GCI combustion. Validation was based on experiments conducted with ethanol-free 93 RON gasoline and with the compression ratio set at 15.7. For the conditions investigated, a split injection strategy was used with the start of the first injection fixed at -30 °ATDC and the start of the second injection varied. Of the configurations investigated with CFD, a high number of injector holes (14) to promote air utilization combined with a low swirl ratio to avoid plume-to-plume interaction and a 16.5 compression ratio had the lowest heat transfer loss and highest ISFC (ITE 48.1% to 51.9%) in the 5-15 bar BMEP range [4554].
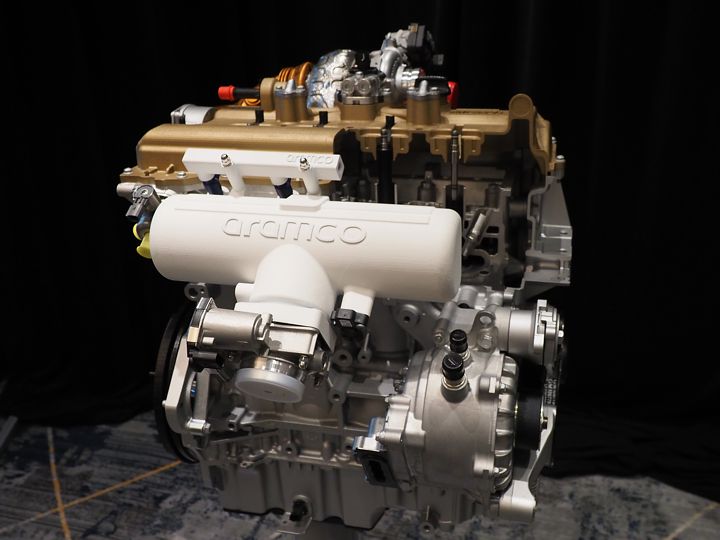
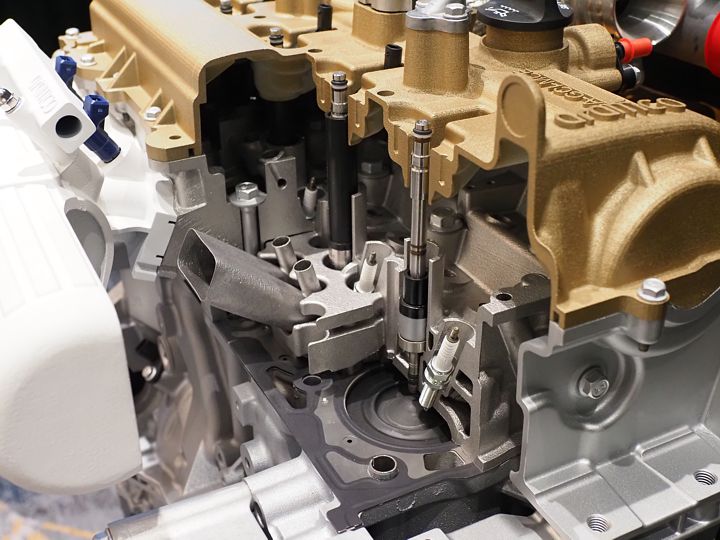
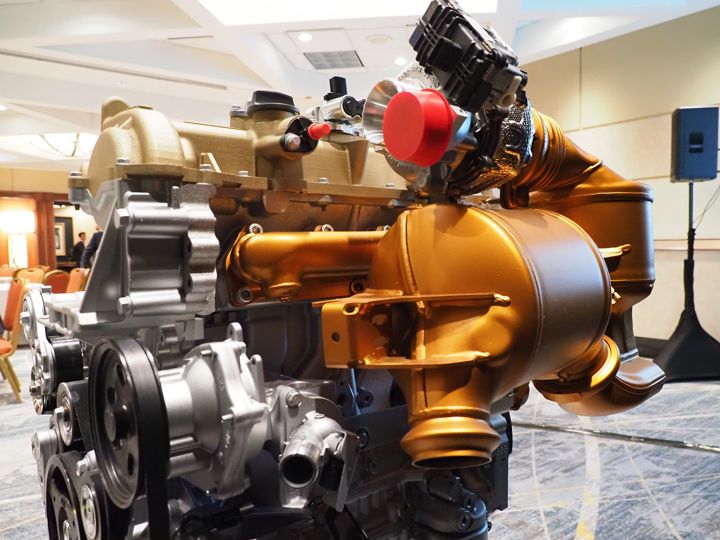
A control strategy for light-duty GCI engines was summarized by the University of Bologna and Magneti Marelli. Controlling ignition timing in a CGI engine is a challenge because of the long ignition delay of gasoline. To address this challenge, multiple injection strategies are commonly applied—HCCI-like combustion of the first pilot injection raises the temperature and greatly reduces the ignition delay of the subsequent injections. However, the timing of the first injection must still be accurately controlled to ensure that when subsequent injections are introduced, combustion proceeds at the intended crank angle. To address the issue of initial pilot injection timing, the researchers developed an ignition delay model that predicts its ignition delay time. Of the various parameters investigated, the best predictions were achieved using the estimated average cylinder temperature and pressure between start-of-injection (SOI) and start-of-combustion (SOC) of the first pilot injection. The estimates were derived from the temperature and pressure at intake valve closing. The model could then be used to feedforward the SOI to achieve a required SOC of the first pilot injection [4555].
New Engine Concepts
A Dutch startup Econamiq is developing a cylinder deactivation technology where increased engine efficiency is achieved via post-combustion over-expansion [4536]. The concept—applied through numerical simulation to a 4 cylinder SI engine—involves directing exhaust gases from active cylinders to passive (deactivated) cylinders to achieve further expansion during partial load operation. At high load, the engine switches to regular, all cylinder operation. This new cycle shows improved efficiency (a simulated 10%) and a higher torque (within the deactivation area on the map), because of the extra expansion overcoming friction and producing work. The concept also produces an exhaust noise benefit. A vehicle demonstration is planned as a next step. The challenges include a potentially complex cylinder head design, and effects on the turbocharger, as more energy is extracted from the exhaust gas.
Another cylinder deactivation concept was investigated by the University of Kaiserslautern [4537]. A 4-cylinder, inline, EU Stage IV John Deere diesel engine was modified to run on 3 cylinders for most of the time, with the 4th cylinder activated as a boost cylinder for high torque (> 75%) operation. The engine crankshaft was redesigned to optimize for the 3-cylinder operation—the firing order was changed, and cylinders 1 and 4 operated in parallel. The new firing order also required changes in the valve train layout and cylinder head design. An important part of the system was a variable valve train, where modified valve lift was used to deactivate the cylinder. Test bench results showed a typical 5-6% BSFC improvement over low load duty cycles, with a maximum improvement of over 15%. The concept also produced increased exhaust temperatures at low loads, which are desirable for emission aftertreatment. Among unresolved issues, the redesign of the engine had a negative impact on NVH behavior.
One of the challenges with modern light-duty diesel engines is the cost premium compared to competing gasoline engines. One option to removing cost from the diesel fuel injection system would be to eliminate the common rail. To this end, researchers at the Politecnico di Torino have developed a “common feeding” system that uses a delivery chamber with a volume around 10 cm3 integrated in the high-pressure pump instead of a much larger common rail and that is being commercialized in the Asian market. From this chamber, high pressure lines extend to each injector. While there are some notable differences in the system behavior compared to a common rail, these can be accommodated in the design and calibration. Some of the differences include a larger pressure drop and variations in the frequency of free pressure waves in the high pressure circuit. For pilot-main injections, orifices are required at the accumulator outlets to dampen the pressure waves triggered by the pilot injection and minimize its effect on main injection quantity [4556].
An interesting study by the University of Maryland and the US Naval Academy numerically investigated the effect of diesel engine bore size on in-cylinder heat transfer. Bore size was varied between 76 and 914 mm while compression ratio was held at 16. The most significant difference is the overall reduced heat transfer in larger engines due to the surface area to volume effect. A three times higher for in-cylinder heat transfer relative to in-cylinder inducted air mass is predicted for the smaller engines. Under cold start conditions, smaller bore diesel engines were found to be more sensitive to cold start conditions and the effect is reduced with increasing wall temperature—the smaller bore engines have lower end-of-compression temperatures under these conditions [4557].
Combustion
Michigan Technological University and Aramco summarized work that was intended to clarify the effect of physical and chemical properties on the auto-ignition process of a fuel spray under conditions typical of a heavy-duty diesel engine with both partially premixed combustion and mixing-controlled combustion. A numerical chemical property perturbation study was carried out with different mixtures of n-heptane and iso-octane where 100% n-heptane (PRF0) was used to represent diesel fuel and 39% n-heptane/61% iso-octane (PRF60) was used to represent a high reactivity gasoline. Their findings included: (1) the primary physical properties that affected liquid length included density, vapor pressure (under low ambient temperature), and viscosity; (2) the primary physical property that affected autoignition was density through its effect on mixing—secondary influences included heat of vaporization and specific heat capacity; (3) the chemical composition of a fuel dominated the autoignition process rather than the physical properties; (4) the ignition processes affect the vaporization process rather than vice versa [4560].
Reducing combustion duration by increasing injector flow rate is an option for increasing diesel engine efficiency. Navistar investigated two options for increased injector flow rate as part of their SuperTruck program: increasing nozzle hole size while keeping the number of holes constant and increasing the number of holes while keeping the size constant. Experiments with the second option, i.e., by varying hole size, were carried out on a 12.4 L engine with a 20.5 compression ratio and using a 900 bar injection pressure. While combustion duration was shortened and indicated thermal efficiency (ITE) improved at higher injector flow rates when SOI was held constant, when the results were analyzed on the basis of combustion phasing (CA50), the differences in ITE were reduced and differences in brake thermal efficiency (BTE) were difficult to detect. Increasing injector flow rate too much lead to increased soot and CO emissions suggesting deteriorating combustion quality [4560].
Ultra-lean combustion with λ > 1.6 can achieve high efficiency, while reducing NOx, in natural gas SI engines. Mahle applied this approach to a small, 1 kWe micro-CHP generator set for residential power and heat applications, powered by a single cylinder, 392 cm3, natural gas engine [4541]. Lean combustion was enabled by Mahle Jet Ignition—a pre-chamber-based combustion system that facilitates ultra-lean operation beyond what is achievable with traditional spark ignition engines. The jet ignition technology enables high levels of dilution, reduced combustion temperatures and reduced heat losses. Lambda was optimized over the engine map for maximum efficiency. A peak BTE of 32.5% was achieved (or 30.5% electrical conversion efficiency including fuel pump losses), which is ~20% higher compared to current commercial engines.
New combustion approaches may also enable high efficiency in stoichiometric natural gas engines. Woodward reported on the development of very promising, while challenging, controlled auto-ignition (CAI) technology for heavy-duty, stoichiometric NG engines [4542]. This system, also referred to as “spark controlled HCCI”, enables significant reduction in burn duration by controlling a two phase combustion event. The first phase is a normal spark ignited propagating flame, which then triggers the second phase which is volumetric auto-ignition. A 15 liter, 6 cylinder, 2013 heavy-duty diesel engine was converted to a prototype gas engine configuration and used for laboratory work. High EGR rates of 20-25% were used to control knock. The CAI process relies on a fast and accurate closed-loop control—the combustion pressure feedback was sampled at a 0.5°CA resolution and processed in real-time combustion metrics (e.g., center of combustion or burn duration). The system offers high efficiency of 42% BTE at 21.5 bar BMEP and greater than 40.5% BTE at 24 bar BMEP, contributing to more than 10% improvement in fuel consumption. A TWC was used to reduce emissions to well below Euro VI levels, with a potential to meet future California NOx emission standard of 0.02 g/bhp-hr.
Turbochargers
Wabtec summarized their approach to selecting turbochargers for North American freight locomotives. These locomotives typically use single stage turbochargers without a wastegate. To avoid exceeding engine and turbocharger design limits, engine derating is typically applied. Turbocharger sizing can be carried out by sizing to meet airflow requirements at full load (Notch 8) and a mid-load point such as Notch 4. The challenge is to select a configuration to meet the mid-load airflow requirement with efficient full load operation. Up to 50% or more of fuel is used at full load operation so efficient turbocharging at full load is essential. The turbocharger must also provide sufficient airflow at low load to maintain a high enough air fuel ratio to prevent excessive particulate emissions. While a smaller turbocharger would improve airflow at low load conditions, it would lead to higher turbocharger speeds and increased peak cylinder pressures at full load. Locomotives operate in a wide range of ambient conditions, including altitudes up to 3,050 meters and across ambient air temperatures ranging from -40°C to over 38°C. Excursions outside of these design limits can also occur, for example in high altitude tunnels where ambient temperatures can reach 110°C and oxygen concentrations can become low for trailing locomotives. Variable geometry turbines and two-stage turbocharging could improve operational and engine efficiency but add cost and complexity to the system. Fuel injection strategies such as multiple injections could be used to lower emissions and thus reduce airflow requirements at low load that could allow additional flexibility in turbocharger matching and improved efficiency or more robust emission control strategies [4559].
Universitat Politècnica de València developed a turbocharger testing methodology for the determination of turbocharger maps [4539]. The proposed standardized methodology involves three sets of tests: (1) quasi-adiabatic tests with cold and hot gas flow, (2) hot gas flow insulated tests, and (3) hot exposed tests. Three different VGT turbochargers were benchmarked using the methodology.
Other Topics
Underwater exhaust systems are of interest for ships to for a variety of reasons including the possibility of reducing drag via exhaust gas lubrication of the hull. However, directing exhaust gases underwater can create high and dynamic back pressure on the engine which can fluctuate in amplitude and time period as a ship operates in varying sea-states. Delft University of Technology investigated this effect in a laboratory using a 4 cylinder MAN L20/27 engine and by simulating wave heights up to 1m using a butterfly valve in the exhaust system. Backpressure had to be kept below 50 mbar to avoid thermally overloading the turbocharger. They found that the adverse effects of dynamic back pressure on the exhaust temperature and fuel consumption were less severe than those for static back pressure. During dynamic and multiple back pressure waves the exhaust receiver temperature increased by a maximum value of 6°C compared to 14°C for static back pressure of the same amplitude. However, as the wave period increases, and once it reaches a critical value, the effect becomes the same as for static back pressure increase. Others have estimated the critical period to be around 12 s [4558].
Lean burn gasoline engines, while rapidly adopted due to their superior fuel economy, present more emission challenges than stoichiometric combustion. One of the potential approaches for controlling NOx from lean burn gasoline engines is passive SCR. In such systems, brief periods of rich operation are used to generate ammonia over a TWC, which is then adsorbed on the downstream SCR catalyst and consumed for NOx reduction during lean operation. A reliable measurement of the SCR ammonia inventory is critically important to control the rich operation and to minimize the associated fuel economy penalty. CTS and the Oak Ridge Laboratory evaluated the use of a radio frequency (RF) sensor to directly monitor ammonia storage over the SCR catalyst and to optimize the combustion process [4538]. A combination of lean stratified and lean homogeneous operation was able to provide improvements in fuel economy by up to 9.3% (relative to stoichiometric) and a NOx conversion of 99.5%. The engine used for experiments was fitted with a gasoline particulate filter; since soot produces a much stronger RF response than NH3, the use of an RF sensor for SCR control is only possible in the absence of PM emissions.
Graz University reported on the development of a new method of lube oil consumption measurement using deuterium as tracer [4540]. Using deuterium (2H) could present an improvement over the commonly used sulfur tracer method, because sulfur is also present in the fuel, and when using SO2 as a tracer one needs to constantly monitor and correct for fuel sulfur levels. A deuterium exchange process of oil was developed, where oil was branded with 2% of 2H. However, a number of challenges were identified during engine bench experiments: (1) a strongly decreasing tracer concentration was observed during the initial ~90 hours of the experiment, raising questions as to tracer stability; (2) the CRD spectrometer used for 2H analysis appeared cross-sensitive to N2, O2 and CO2; (3) the deuterium exchange of mineral (as opposed to synthetic) oils was challenging because the Pd catalyst used in the process was poisoned by phosphorus and sulfur present in mineral oils.
* * *
The ASME Internal Combustion Engine 2020 Fall Conference (ICEF 2020) will be held on November 1-4, 2020 in Denver, Colorado.
Conference website: event.asme.org/ICEF