Study finds diesel trains can be converted to battery-electric, rail industry remains skeptical
8 December 2021
Researchers from the US Department of Energy’s Lawrence Berkeley National Laboratory (Berkeley Lab), collaborating with UCLA and UC Berkeley, make a rather optimistic case that diesel-electric trains in the United States could be retrofitted with batteries in a way that is cost-competitive with diesel. Doing so would also decrease adverse health impacts and premature deaths linked to air pollution, and reduce CO2 emissions. The study was recently published in Nature Energy [5306].
The existing battery technology could power a freight train for 150 miles (241 km)—the average daily distance traveled—according to the analysis. A battery-powered freight train would use half the energy required by a diesel-electric train, and taking into account falling battery prices and environmental costs of diesel, battery-electric trains are on track to be more cost-competitive than diesel-electric trains. Since freight rail planning is centralized, the study suggests that railroads could achieve high volume use of fast-charging infrastructure, which would further reduce costs.
One major benefit of retrofitting existing diesel-electric freight trains with battery cars (battery tender cars) is that the battery-electric trains can always fall back on the diesel engine as a backup fuel source. This dual-fuel capability, allowing for either battery or diesel usage, is a unique advantage compared to fully electrifying the freight rail system.
Another benefit perceived by the study is that battery-electric trains could be deployed as clean backup power, thus bolstering the electric grid’s resilience. “Conversion of the U.S. freight rail sector to battery-electric would generate about 220 gigawatt-hours of mobile storage,” said Amol Phadke, a co-author of the study. “Furthermore, these battery tender cars could be deployed during extreme events, such as during the recent catastrophic wildfires in California or the 2021 winter storm in Texas that left millions without access to electricity. This mobile energy storage capability would also create a potential new revenue stream for freight rail operators.”
The study compares the battery- and diesel-electric propulsion technologies via total cost of ownership (TCO) analysis. The results are shown in Figure 1.
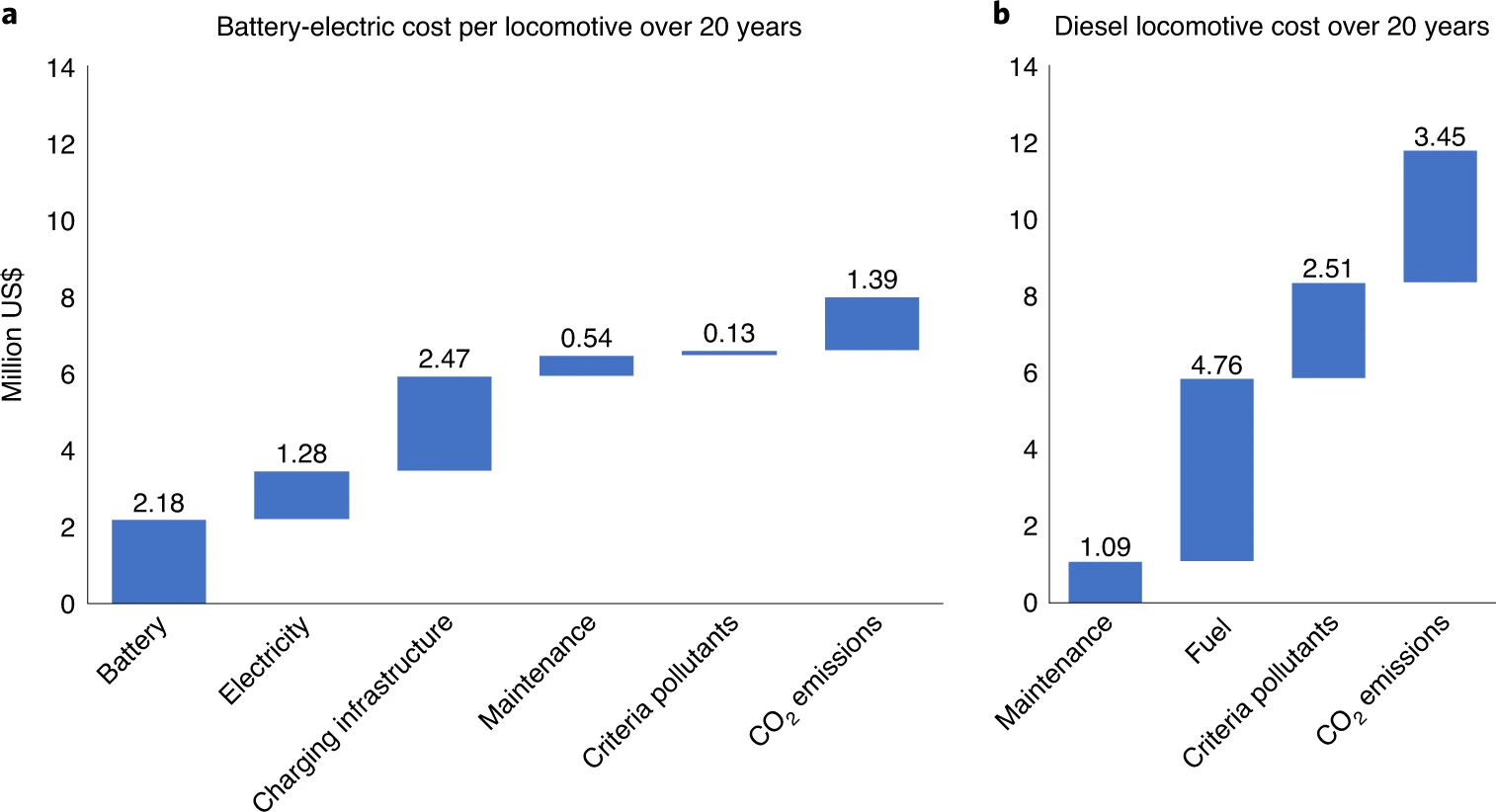
Both technologies are estimated using a 9.1 MWh battery with a 241 km range for a 3.3 MW locomotive pulling 1,090 revenue-tonnes. Assumptions include: US$0.61 l-1 diesel price, US$100 kWh-1 battery price (US$50 kWh-1 replacement price), 30% station use rate and 3% discount rate. The social cost of carbon emissions starts at US$125 t-1 in 2021 and increases to US$226 t-1 by 2040 [5306].
One key conclusion of the study that was widely reported in the media was that a retrofit of diesel-electric trains with batteries is viable both technically and economically, with the battery-electric option actually presenting a lower cost option compared to diesel. However, as apparent from Figure 1, this is entirely due to the social costs of criteria and GHG emissions. These emissions—referred to in economics as externalities—are ‘free’ to the railroad industry, and by avoiding them, railroad companies would not ‘save’ any money. The fact that emissions and other externalities come for free is arguably among the major reasons behind the deepening global ecological crisis. Nevertheless, under current accounting practice in the United States and other countries, emissions do not reflect on a company’s financial results.
The Berkeley Lab TCO analysis would be perhaps more appropriately called a societal TCO. Because of the inclusion of the costs of emissions, the analysis—in contrast to a conventional, private TCO—is not suitable for a railroad company as a tool to guide investment decisions.
Before emission costs, the analysis shows that battery electric propulsion ($6.47 million) is actually more costly than diesel ($5.85 million), Figure 1. Hence, US railroad companies cannot be expected to voluntarily upgrade their locomotive fleets to battery-electric propulsion. It would appear that such rail fleet conversion would require substantial government subsidies to cover the costs of the battery tenders, the modification of thousands of diesel locomotives, design and installation of trackside recharging stations, and upgrading local distribution grids to accommodate “super chargers” for multiple 9 MWh batteries.
Even though the TCO results before emission costs are favorable for the diesel option, they still appear to be based on optimistic assumptions in regards to battery prices and charging.
Battery Cost. The study assumes a ‘near-future’ battery cost of $100/kWh, based on a Bloomberg (BNEF) press release of December 16, 2020. This cost figure quoted by BNEF appears to be an industry average that considers passenger EVs, e-buses, commercial EVs and stationary storage. It would be heavily weighted by the Chinese market, passenger cars, and likely Chinese e-buses.
Locomotive batteries, on the other hand, are similar in scale to stationary batteries used for grid storage, and it would make more sense to base a cost estimate on such batteries. At least some 4h grid storage batteries seem to be of a similar capacity to the batteries the Berkeley study uses [5307]. A recent NREL study [5308] estimates the 2020 capital cost for 4h grid scale batteries is about $345/kWh and a Mid Cost projection of $149/kWh by 2050. NREL’s Low Cost projection would see $100/kWh no sooner than 2045 (see Figure ES-2 of the NREL report).
Charging. The authors of the study envision recharging the battery-electric locomotives when the train stops for crew changes and/or refueling. This would require that high power charging stations (assumed to be 72 MW) be located at suitable locations.
From the paper:
“Battery-powered trains with at least a 241-km range should have ample opportunity to charge during long routes while remaining on schedule. The average length of a US Class I freight haul is 1,662 km (ref. 3). Class I freight rail routes include 30- to 45-min stops for crew changes every 240-400 km, at which point batteries could be recharged. Longer routes also include a refueling stop at the midpoint for 1-2 h (rail representative, personal communication). Technological advances enable charging rates of 30 min to 1 h for fully charging each cell (1-2C charging) for commercially available LFP batteries, although LFP technology can theoretically achieve 4C charging.”
However, this envisioned recharging routine and assumed travel distances seem not to be consistent with the operating practice of Class 1 railroads. The energy costs calculation further assumes that railroads have access to low cost renewable power via suitable electricity tariffs. This presupposes railroads have a degree of flexibility in charging locomotives during periods when low cost power is available, but such flexibility would be limited if trains were to be recharged more than one time per day.
Michael Iden—an Illinois-based railroad consultant and former General Director Locomotive Engineering at United Pacific Railroad—shared with DieselNet a number of comments on the study:
- The authors’ claim that a “battery-powered freight train would use half the energy required by a diesel-electric train” needs clarification. The total energy required to move a freight train would remain the same, assuming no change in train tonnage, route, speeds, etc. If, however, a “well to wheels” basis is considered, the electrical power delivered to the batteries (during recharging) would follow generation and transmission to the recharging locations, all such activities involving their own inefficiencies. Typical battery “round trip” inefficiencies can be as high as 10% when charging and another 10% when discharging, whereas the energy stored in liquid fuel remains essentially constant “in the tank” until used by the diesel engine.
- Any CO2 (GHG) reductions would require charging the batteries with electrical grid power that is significantly lower in carbon intensity than exists today in the United States.
- A nationwide deployment of battery tenders (and modifying most of the locomotive fleet) will also require design, production and installation of trackside battery charging equipment. But the even bigger challenge will likely be getting suitable grid connectivity and the availability of large amounts of power. Charging one single 9 MWh tender (let alone more than one as most trains have more than one diesel locomotive) won’t be a trivial utility load. A 9 MWh battery tender would be the equivalent of recharging 36 of Tesla’s proposed battery-powered Cybertruck tractors each with a 250 kWh battery (or 90 Tesla autos each with a 100 kWh battery). And, unlike a battery automobile used for family use or daily commuting, freight trains and the railroads that operate them won’t have the luxury of waiting for optimal electricity charge times before “plugging in”.
- The 241 km (150 miles) “average daily distance traveled by US Class 1 freight trains” has no citation. There are trains operating between Chicago and the West Coast, for example, that can traverse the ~2,200 mile distance (several routes) in 2.5-3 days for a maximum of ~733 miles per day. Such routes would require about 5 recharges per day.
- The authors’ assertion that a national fleet of battery tenders “would generate about 220 gigawatt-hours of mobile storage” for use in areas experiencing “extreme events” (such as recent power outages in California and Texas) would require moving (by rail) 24,444 battery tenders to the affected area. (220,000 GWh of energy divided by 9 MWh capacity per tender translates to 24,444 battery tenders.) Considering the authors are assuming a national deployment of 24,444 battery tenders across the US railroad network, the railroads would have to stop using the tenders (dispersed across the lower-48 states) for locomotives, fully recharge them and then transport the tenders to the “emergency zone” that alone could take several days if not a week or longer. Once in the “emergency zone” the battery tenders (storing and capable of delivering DC power) would have to be connected somehow to the local or regional grid delivering synchronized 60 Hz alternating current (AC) power. And, in the absence of some source of recharging power (in a “blackout zone”), once a battery tender would be “used” it would have zero capability for emergency power.
- The authors state rail routes include “30-to-45 minutes stops for crew changes every 240-400 km” (150-248 miles) that could be used for charging. What is the logic and source(s) of such lengthy crew change stops? Many crew changes can require less than 15 minutes to accomplish.
- The authors refer to diesel locomotive refueling stops requiring 1-2 hours. Most mainline refueling locations at major terminals can refuel a 5000 USG fuel tank in 15 minutes, with the ability to refuel multiple locomotives on a train simultaneously. The authors imply that their “boxcar tender” could be recharged during such stops. That is highly assumptive.
- The authors’ estimate of capital costs for battery tenders appears to be based solely on the average price of batteries (ignoring the cost of manufacturing the rail vehicle or modifying diesel locomotives). A contemporary diesel-electric locomotive (with no battery tender connectivity) has a market price of around US$3 million.
- Last, while the concept of a battery tender “connected to” a modified diesel locomotive is technically feasible, it won’t be technically simple. A battery tender should not be assumed to be “simply” a freight-carrying box car “converted” into a battery tender. A large concentration of batteries will require a support system (cooling the cells and even selective heating during wintertime conditions), a “battery management system” and physical ability to maintain and repair (i.e., remove and replace) defective cells. Likewise, to “electrically connect” a battery tender to a diesel locomotive, the locomotive itself will have to be modified to have suitable cable connections, onboard cabling, switch gear, a modified control system, etc. Assuming 25,000 “line haul” locomotives in the United States alone, there are more than a dozen major models of locomotives in service, each of which would require significant engineering design and modification work.
Source: Berkeley Lab