Conference report: 44th International Vienna Motor Symposium
24 May 2023
The 44th International Vienna Motor Symposium was held April 26-28, 2023. Due to the limited number of attendees that could be accommodated, a “Virtual Event” option was offered again this year. Virtual attendees could access the symposium material starting May 3rd. Topics covered included new engine concepts and emission reduction, driveline technologies, powertrain electrification, hybrid technologies, fuels, battery technologies, fuel cell technologies and hydrogen engines.
Please log in to view the full version of this article (subscription required).
New Engines
Mercedes-Benz summarized the updates to the M256 gasoline and OM656 diesel six-cylinder engines from its FAME (Family of Modular Engines) engine family. Both engines are now electrified through the incorporation of 48 V mild-hybrid technology using an ISG [5790].
The M256 engine has been electrified since its launch in 2016 and one goal of the update was to reduce the enrichment needed at high power to reduce emissions. This was achieved by reducing the engine’s knock tendency and increasing its maximum exhaust temperature tolerance. To lower the tendency to knock with the expanded use of stoichiometric mixtures, an early intake valve timing strategy was used to lower the final compression temperature and upgrading the turbocharger reduced the backpressure and therefore the residual gas fraction. The early intake valve timing strategy required a re-optimization of the in-cylinder flow. Upgrading turbocharger materials increased the exhaust gas temperature limit at the exhaust manifold while increased convective cooling of the exhaust manifold and turbine housing kept catalyst inlet temperature from increasing excessively. As a result, over 280 kW engine output is possible in stoichiometric operation and 330 kW with a fuel enrichment of 6%.
The OM656 engine was electrified for the first time with this upgrade as well as receiving an upgraded aftertreatment system to reduce NOx and PN emissions, Figure 1. The power output for the highest power variant of the engine has also been increased. The upgraded exhaust gas aftertreatment system replaced the DOC of the previous version with a close-coupled NOx storage catalyst. Following the NSC is an SCR catalyst and SCR-coated DPF (sDPF) intended to reduce cold start and dynamic driving NOx. Previously, the close-coupled SCR was located after the sDPF. An additional underbody SCR catalyst and ASC increase NOx conversion during high temperature operation such as during DPF regeneration. The first stage of urea dosing is supplied just after the NSC and the second stage upstream of the under-body SCR. The DPF has been upgraded to a filter substrate with “artificial pre-ashing” that ensures surface filtration and high filtration efficiency is achieved even during and after DPF regeneration. Engine power was increased by 27 kW with the aid of increased displacement (via long stroke), increased peak injection pressure (2700 bar) and enhanced piston cooling with sodium.
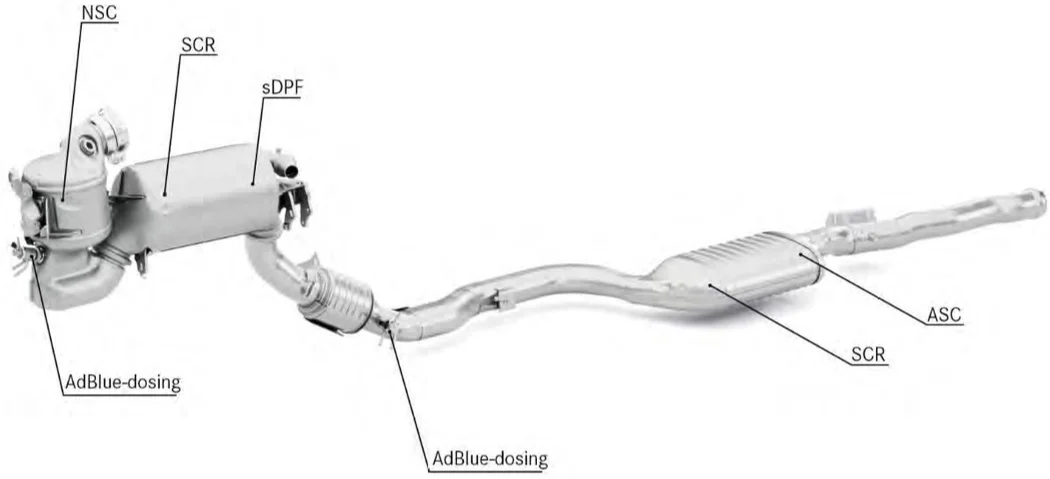
Mazda presented its most recent SKYACTIV powertrain offerings that includes an in-line six-cylinder SKYACTIV-D3.3 diesel, a SKYACTIV-G3.3 Turbo gasoline, a six-cylinder SKYACTIV-X and a four-cylinder SKYACTIV-G2.5 gasoline engine [5791]. The SKYACTIV-D3.3 is the second generation SKYACTIV diesel engine and has an expanded operating range over which Premixed Compression Ignition (PCI) is used to achieve a large area of BTE > 40% in the WLTC operating envelope. This required a new dual-egg shaped piston bowl and multi-stage injection to limit soot production. EGR is used up to high load to limit NOx and EV mode via a mild-hybrid P2 motor/generator can be used at very light-loads to ensure fuel efficient operation. The six-cylinder SKYACTIV-G3.3 Turbo features stronger in-cylinder flow to increase combustion speed and reduce knock intensity and enable a 12:1 compression ratio. Improved combustion stability allows higher EGR rates to lower fuel consumption. The four-cylinder SKYACTIV-G2.5 also uses a high compression ratio and will be the base engine for a PHEV. The SKYACTIV-X concept is being applied to an in-line six-cylinder gasoline engine. Future engine developments will focus on reducing cooling losses with an insulation material and the rapid warm-up of exhaust gas. Mazda has developed an insulation material that mixes hollow particles into a resin material. For diesel engines, a rapid warm-up combustion strategy that uses post-injections is being developed.
Dedicated Hybrid Engines
Several dedicated hybrid engine concepts were evaluated that targeted BTE as high as 45%.
AVL’s design is a 2.5 L I4 turbocharged Atkinson cycle engine with up to 70 kW/L power density. It features a cooled, coated exhaust manifold, a 16.5:1 compression ratio, a low surface roughness piston crown and combustion chamber, cooled LP EGR, low friction, an electric turbocharger, three spark plugs per cylinder and an aftertreatment system featuring an electrically heated catalyst [5792]. A stoichiometric air-fuel ratio is possible up to the full load rating of 175 kW and a peak BTE of 45% is reported with BTE > 38% over a large area. The electric turbo allows pre-heating the aftertreatment system prior to engine starting. When integrated into a demonstration vehicle, CO2 emissions of 142 g/km were achieved in charge sustaining mode – a 15.5% decrease compared to the baseline vehicle’s 168 g/km. When charge depleting operation is accounted for, overall CO2 emissions of 40 g/km can be achieved.
Bosch evaluated several engine and hybrid configurations options for a high voltage D-segment hybrid vehicle and concluded that a dedicated hybrid engine coupled to a dedicated hybrid transmission (DHT) with two electric machines in a series or series-parallel configuration would be adequate to meet future CO2 requirements such as those being discussed for China (4.0 L/100 km or ~95 gCO2/km in 2035) [5793]. Of the engine options evaluated, the gasoline fueled dedicated hybrid engine that would be most relevant to the market was rated at 80 kW, operated at a stoichiometric air-fuel ratio, and achieved a peak BTE of 41%. To achieve this efficiency, a downsized engine with 13.7:1 compression ratio, Miller timing, cooled low-pressure EGR, variable geometry turbocharger and a passive pre-chamber spark plug was proposed. While other stoichiometric engine options could achieve higher peak efficiency, the selected engine minimized both charging losses and energy throughput of the high voltage battery to achieve a low overall fuel consumption.
China FAW Group and IAV considered the technologies needed to raise the BTE of an SI engine over 45% [5794]. With EGR rates up to 42%, a compression ratio of 17.5:1, a long stroke design, specially developed intake and exhaust ports and an active pre-Chamber spark plug, a stoichiometric single cylinder engine achieved a peak indicated thermal efficiency (ITE) of 46.8% and a power density of 55 kW/L. Through further optimization of the piston crown, pre-chamber layout and settings, it was believed that increased EGR could be used to bring BTE beyond 45% for a multi-cylinder engine assuming friction could be kept at the lower end of benchmark engines. With the same hardware set-up, lean-burn (λ=2.4) BTE of 45.8% was demonstrated. The power density in lean-burn was limited to 47 kW/L at λ=1.6.
Engine Research
Sandia National Laboratories has evaluated the performance of the Sandia LTGC-AMFI research engine in a medium-duty class 6 truck and a nonroad vehicle using cycle simulation [5795]. For the medium-duty truck, fuel economy improvements of 20-25% and engine-out NOx emissions of 0.020 g/bhp-hr or less were estimated depending on the drive cycle. Over the ISO 8178 C1 and C2 nonroad cycles, fuel consumption decreased by 21% and 9% respectively while engine-out NOx was well below the 0.40 g/kWh Tier 4 limit.
Numerous papers on hydrogen fueled engines covered light- and heavy-duty applications:
- Toyota presented work on the basic analysis of combustion, emissions, and functional reliability of hydrogen engines, as well as the mechanism of abnormal combustion and guidelines for suppressing it to improve engine output [5796],
- Volvo presented work on the development of a hydrogen engine demonstrator based on its current 750hp 16L platform [5797],
- TNO presented work on key performance indicators and their limiting factors for both lean burn port fuel injection (PFI SI) as well as High Pressure Direct Injection (HPDI) combustion in a single cylinder 1.8 L research engine [5798],
- Westport and Scania presented an overview of two heavy-duty demonstration vehicles equipped with hydrogen HPDI fuel systems [5799],
- FEV and JCB investigated technology options including port fuel injection and direct fuel injection for a 55 kW nonroad Stage V engine [5800],
- PUNCH Torino developed a combustion system featuring optimized injection and ignition systems as well as a dedicated piston bowl for a 6.6 L V8 spark ignited hydrogen engine for genset and marine applications [5801],
- Graz University of Technology carried out experimental investigations to develop a transient operating strategy for a highly boosted, lean-burn hydrogen engine under the constraint of Euro 7 NOx limits [5802],
- BorgWarner demonstrated the process for engine optimization and light commercial vehicle adaptation to a hydrogen ICE while meeting Euro 7 requirements [5803].
Conference website: wiener-motorensymposium.at