Mercedes-Benz unveils the new OM 654 2.0 liter diesel engine
18 February 2016
Daimler announced the OM 654 2.0 L, four-cylinder diesel engine, which marks the debut of a new family of engines from Mercedes-Benz. Exemplary efficiency and emissions ensure that the premium diesel is future-proof while underlining the key role to be played by the diesel engine in achieving the challenging global climate targets. The OM 654 will premiere in the new E-Class E 220d to be launched this Spring.
The new, modular family of engines is intended for application across the entire range of Mercedes-Benz cars and vans. There are plans for several output variants as well as longitudinal and transverse installation in vehicles with front-, rear- and all-wheel drive.
Another objectives behind the new generation of engines was to reduce the number of variants as far as possible—said Daimler. The engine’s compact dimensions allow even more flexibility in adapting to different vehicle models. The interfaces between drive unit and vehicle have been standardized across all model series. Importantly, all the elements of the exhaust aftertreatment system are now configured directly on the engine itself and no longer on the vehicle.
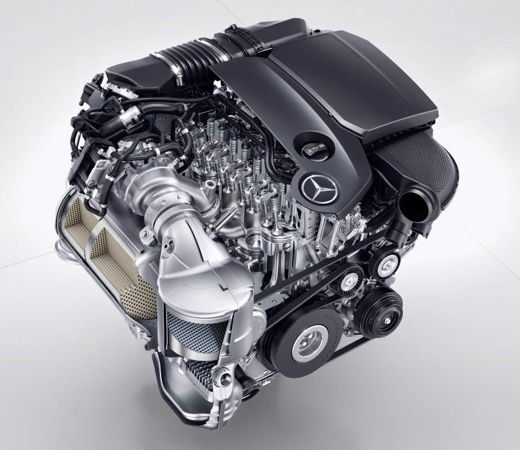
The OM 654 delivers around 13% lower fuel consumption and CO2 emissions—according to Daimler—and an increase in output from 125 to 143 kW. The key areas of innovation include:
- first all-aluminum construction of a four-cylinder diesel engine,
- steel pistons with stepped-lip combustion bowls, NANOSLIDE® cylinder coating, fourth-generation common rail injection,
- all exhaust treatment technologies configured directly on the engine,
- significantly lighter and more compact: 168.4 kg vs. 202.8 kg (-17%), two-liter displacement instead of 2.15 liters, cylinder spacing 90 mm vs. 94 mm, and
- lower noise level and higher vibration comfort.
The OM 654 engine has a torque density of 205 Nm/L (2.6 MPa BMEP) and power density of 73 kW/L, putting the single-stage variable geometry diesel engine well into the region dominated by engines with two-stage boosting systems only a few years ago.
The new engine is equipped with multi-way exhaust gas recirculation (EGR), which combines cooled high-pressure and low-pressure EGR. This approach allows to reduce NOx across the entire engine map, while providing good fuel economy.
The engine is designed to meet future emission legislation, including the RDE (Real Driving Emissions) and WLTP (Worldwide harmonized Light vehicles Test Procedure) testing. All emission system components are installed directly on the engine, in a close-coupled position. Supported by insulation measures and improved catalyst coatings, there is “absolutely no need for engine temperature management during cold starting or at low load”. This also results in fuel savings, especially during short trips.
The exhaust gas from the turbocharger is sent first to a diesel oxidation catalyst. Then, it passes to a mixer—where urea (AdBlue®) is added using a water-cooled dosing module—and to a downstream sDPF (SCR-on-filter, SCRF) unit. An additional SCR catalyst is positioned downstream of the sDPF.
Source: Daimler