Conference report: ASME ICE 2016 Fall Technical Conference
31 October 2016
The ASME Internal Combustion Engine Division 2016 Fall Technical Conference (ICEF 2016) was held October 9-12, 2016 in Greenville, South Carolina, USA. The conference—attended by over 200 delegates and hosted by Clemson University—included a two-day technical program with over 90 technical papers. On Tuesday evening, participants could take part in a technical tour of the automotive engineering research facilities located on the Clemson University International Center for Automotive Research (ICAR) campus. On Wednesday morning, another tour to the GE Gas Turbine Engineering and Advanced Manufacturing Works was available.
Keynote Lecture. The conference opened with a keynote presentation by Dr. Zoran Filipi, Executive Director of the Campbell Graduate Engineering Center, Clemson University ICAR. He summarized HCCI research issues being investigated at Clemson University with a focus on the connection between heat transfer and combustion kinetics. In the course of research at Clemson, it was discovered that combustion chamber deposits stabilized HCCI combustion and enabled lower loads to be achieved with HCCI combustion. This ultimately lead to the development of thermal barrier coatings that can be applied within the combustion chamber to achieve the same result. Only piston coatings have been investigated so far. While thermal barrier coatings were investigated several decades ago as a possible means to improve engine efficiency, one of the problems with these early coatings was that they were thick and had a significant heat capacity. This resulted in high wall temperatures and a significant increase in the charge temperature during the intake stroke and a volumetric efficiency penalty. The coatings being investigated now at Clemson are much thinner (about 150 µm for thermal barrier coating plus bond coat) and have significantly lower heat capacity so that the volumetric efficiency penalty is minimal. The coating is applied with the Air Plasma Spray (APS) technique and consists of a base layer of NiCrAl (~50 µm) and then a Yttria Stabilized Zirconia (YSZ) low conductivity topcoat (~100 µm). One important benefit of the thermal barrier coating reduction in the minimum load at which HCCI can be used.
The figure below summarizes the benefit of the thinner coating. The wall temperatures during the combustion phase is similar to thick coatings thus providing similar reductions in heat transfer at this critical time. However, because of the lower heat capacity, the temperature of the exposed surface of the coating drops significantly during the expansion stroke to so that during the intake stroke, the surface same temperature is similar to that of an uninsulated combustion chamber and volumetric efficiency is minimally impacted [ICEF2016-9401]. In addition to enabling HCCI at lower loads, coating lowered hydrocarbon emissions by 2-11%, improved combustion efficiency by 0.1-0.4%, reduced CO emissions 4-9% and improved gross indicated efficiency by 2-3% [ICEF2016-9391].
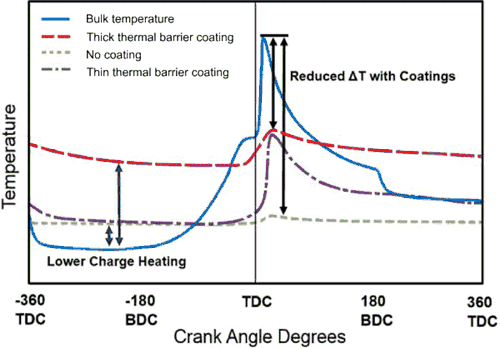
Combustion. Gasoline compression ignition was the subject of a keynote talk by Mark Sellnau, Engineering Manager Advanced Combustion Systems, Delphi Powertrain. Since 2011, Delphi has published material on their efforts to develop a gasoline direct injection compression ignition (GDCI) engine. The current focus of development efforts is CAFE and Tier 3 bin 30 emission limits. Delphi’s GDCI combustion strategy covers the entire engine map (i.e., no mode switching) and uses late multiple injections of gasoline at 300-500 bar rail pressure. No spark plugs are used. The engine incorporates exhaust rebreathing at light load to increase intake and exhaust temperature and collapse the pumping loop. Combustion control is aided by cylinder pressure based control for each cylinder. The engine also incorporates downsizing, is lean burn, unthrottled and has a high compression ratio (15:1 in the Gen 2 engine). The fuel injection strategy uses 1,2, or 3 injections on the intake and/or compression strokes. The last injection is ignition trigger. Early injections are best for emissions and efficiency while late injection provides a similar response to diesel and is used at high loads. Late injection can lead to smoke if not properly managed.
Development up to the Gen 2 engine has focused on reduced friction, advanced injection and advanced thermal management for a BSFC advantage of about 10%. The Gen 3 engine development has focused on combustion, injection and spray and improved transient performance. Some specific goals in the Gen 3 engine development include fast EGR, fast intake air temperature control, fast cold starts, reduced boost parasitics, lower friction, advanced aftertreatment and improved torque and power. The Gen 3 engine provides an additional 5% BSFC benefit.
The latest Gen 3 engine uses 500 bar injection pressure with a centrally mounted injector. Injection is “wetless”. The stroke to bore ratio has been increased to 1.34 (1.04 in the Gen 2 engine) and as a result, there is more clearance for late injections. The combustion system is relatively quiescent with little swirl or squish. Overall, the system has “wide authority” for SOI and combustion phasing (CA50). Other features include intake port electric heaters (2 kW), cylinder pressure sensors, electric cam phaser and integrated exhaust manifold. Exhaust temperatures are relatively low (maximum port temperature is 500°C) so a pre-turbo catalyst has been added to help control emissions. The air management system includes a two-stage boosting system with a turbocharger, supercharger, two intercoolers and low pressure EGR. The downstream oxidation catalyst helps ensures that the EGR cooler stays clean.
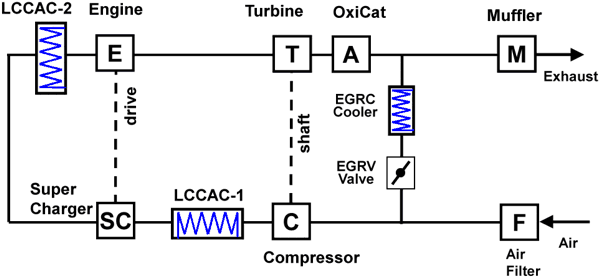
The target for the Gen 3 engine is 0.2 g/kwh NOx at about 211 g/kwh BSFC. Relaxing the NOx to 1 g/kWh would give further give further BSFC benefits. NOx aftertreatment will likely be required to meet Tier3 Bin 30. Hydrocarbon emissions present the most difficult challenge for Tier 3 due to the low exhaust temperatures. With regard to PN emissions, the Gen 1 engine has been shown to be capable of particle number (PN) emissions close to the Euro 6 limit. Additional details on the GDCI technology can be found in SAE papers 2015-01-0834 and 2014-01-1300.
Other work on gasoline compression ignition was also presented at the meeting. Argonne investigated various means of controlling ignition timing and combustion phasing with respect to the time of injection. Boost pressure and air/fuel ratio were found to have a strong impact. The ignition timing of two different fuels with different reactivity (80 and 91 RON) could be matched by controlling the boost pressure at a constant lambda [ICEF2016-9395].
Sandia investigated the use of in-cylinder fuel reformation during negative valve overlap (NVO) to improve the auto-ignition of gasoline compression ignition at low loads where slow burn rates due to elevated dilution fractions and low in-cylinder temperatures can lead to partial burn or even misfire. In this approach, fuel is injected in the cylinder during the recompression period of a long NVO period. The reactivity characteristics of the injected fuel is altered and the retained hot gas helps heat the intake charge. The approach was shown to improve combustion stability (COV IMEP < 1%) and improve thermal efficiency by 2-4% at the test conditions [ICEF2016-9458].
In HCCI applications, low octane fuels are often associated with higher burn rates. The burn rate is often credited to their lower octane number and “intrinsically” higher burn rate. A simulation study carried out at the University of Michigan was used to determine the conditions needed to match the burn rate between a 40 AKI and 87 AKI fuel. The 40 AKI fuel needed not only a lower intake temperature (415K vs 491K), but the thermal gradient (bulk average temperature minus wall temperature) needed to be matched as well (240K vs 400K) [ICEF2016-9355].
Low temperature combustion strategies require high dilution ratios with air and EGR to achieve the longer mixing times and reduced peak combustion temperatures required for low NOx and soot. As the EGR demand is increased, typically the global fuel/air equivalence ratio tends to increase because of the boosting systems’ limited ability to supply fresh air. Oak Ridge National Lab studied the effect of increased EGR on the achievable fuel/air equivalence ratio in a 2007 General Motors 1.9 L ZDTH engine equipped with a variable geometry turbocharger and high pressure EGR. The EGR level was varied from 0 to 50% at speeds ranging from 1,500 to 2,500 rpm and loads from 2 to 10 bar brake mean effective pressure. At about 33% EGR, the vanes of the turbocharger approach the closed position and the engine looses the ability to maintain the desired intake pressure. At 1500 and 2500 rpm, the maximum achievable load while maintaining lean operation was 6 and 10 bar BMEP respectively. At 50% EGR, a maximum load of only 4 bar BMEP was achievable before stoichiometric operation was reached. These results illustrate that the load range for LTC strategies requiring large amounts of EGR could benefit greatly from alternative air handling systems such as two-stage turbocharging, supercharging, and hybrid high/low pressure EGR systems [ICEF2016-9459].
In lean burn SI engines, the engine needs to operated far enough away from the lean misfire limit to avoid ensure misfires do not occur. The benefits of dilute combustion could be extended if this margin could be reduced. A physics-based model capable of predicting the misfire limits as operating conditions change based on driver demand was developed as a means to do this by researchers at the University of Michigan. The model of predicts cycle averaged laminar flame burning velocity within the early flame development period of 0-3% mass fraction burned within 30% uncertainty at steady-state. This was considered to be a reasonable margin of uncertainty since 20% uncertainty equals one standard deviation [ICEF2016-9476].
The influence of intake induced swirl on combustion performance and emissions was investigated by the Czech Technical University [ICEF2016-9325]. The impact of swirl was investigated in a single cylinder research engine for different manifold air pressures and different common rail pressures. The measured emissions included NOx, PM mass, numbers and size distributions, as well as CO/HC.
Past meetings featured numerous papers on RCCI combustion. With one exception from Georgia Southern University [ICEF2016-9394], these were largely absent this year.
Emissions. A passive TWC-SCR aftertreatment system for lean burn gasoline engines was investigated by the University of Michigan [ICEF2016-9441]. The engine was operated in dilute HCCI and SACI (spark assisted compression ignition) combustion modes, which can improve fuel economy and reduce engine out NOx emissions to very low values. However, HCCI/SACI is still unable to achieve California SULEV30 emissions without the use of lean aftertreatment. The proposed TWC-SCR system used periodic rich (SACI) operation to produce NH3 over a TWC to be stored on an SCR catalyst for subsequent NOx conversion during lean (HCCI) operation. In laboratory work performed on a modified 2 liter gasoline engine, the lean/rich HCCI/SACI operation showed a maximum NOx conversion of only 10%, while lean/rich SI operation showed a maximum NOx conversion of 60%. However, if the conversion efficiency of lean/rich HCCI/SACI could be improved through higher catalyst temperatures or larger SCR volumes, simulation results indicated TWC-SCR aftertreatment has the potential to provide near-zero concentration and a fuel efficiency improvement of 7-15% for lean/rich HCCI/SACI relative to stoichiometric SI.
Another study by University of Michigan [ICEF2016-9475] examined rapid pulsing of reductants during the regeneration of NOx adsorbers—the Di-Air process originally proposed by Toyota. In this process, the partially oxidized reductants react with intermediates generated from adsorbed NOx, extending the NOx adsorber temperature window and improving its thermal and sulfur durability. The study compared a number of reductants, including alkanes, alkenes, as well as H2 (the latter was effective at low temperatures, but reduced NOx to NH3 rather than to N2). Experimental work was conducted at 3 Hz pulsing. Different reductants had different effectiveness and different optimum pulse periods. Higher pulsing frequency improved the NOx adsorber selectivity to N2.
An interesting study estimated the real world driving emission effectiveness of the vacuum-insulated catalytic converter (VICC) technology [ICEF2016-9477]. This technology uses vacuum insulation and a phase-change material (in the study, a Mn-Zn-Al eutectic alloy melting at 340°C) to keep the converter above light-off temperature following long periods of vehicle soak. Compared to conventional converters, the VICC technology produces an emission penalty during cold start, and a benefit after hot soak. New model simulations demonstrated the ability of the VICC to achieve significant emissions reductions following vehicle soaks of up to 18 hours. An analysis of real driving data from Atlanta showed a 99% chance that the soak period was less than 10 hours, suggesting that cold start emissions would be reduced for most starts when using the VICC.
Diesel particulate filters accumulate ash deposits inside the channels, which may be difficult to remove by conventional DPF cleaning techniques, such as using compressed air. CTS Corporation (formerly FST) reported on the development of a vibration based DPF cleaning technology [ICEF2016-9432]. Vibration above 5 kHz is used to break up ash deposits and to remove them out of the DPF. The method may be used in conjunction with air cleaning. This study focused on the DPF integrity evaluation after exposure to vibration. The tested DPF samples included a control group, and samples after 10 minutes of vibration at 221 g and 506 g. No statistically significant changes were detected in the compressive strength or in the bending modulus of rupture between the vibrated and non-vibrated samples.
Researchers from Japan’s National Maritime Research Institute conducted an emission study on a ship equipped with conventional marine diesel engines and with lean burn gas engines [ICEF2016-9350]. A combined exhaust gas recirculation (C-EGR) system was proposed, where exhaust gas from a lean burn gas engine was routed to the intake manifold of the marine diesel engine using a blower installed between the engines. The objective was to reduce the methane slip from the gas engine, as well as NOx emissions from the diesel engine. The recirculated gas was cooled in a water cooler. Methane reduction rates ranging from over 90% to below 80% were attained. The methane reduction decreased with increasing engine load, possibly due to the effects of valve overlap.
Large Engines. The impact of minimizing diesel pilot injection quantity below 5% in dual-fuel natural gas (mixed with air prior to induction) in large high speed engines was investigated by LEC of Austria. The results were compared to prechamber SI gas engine capable of ~1.3 g/kWh NOx and a DI diesel engine (6.4 g/kWh NOx and about 1.5-2% lower efficiency than the gas engine). No EGR was used.
At 5% pilot, the efficiency of the gas engine is achievable with the dual fuel engine but with NOx emissions can be as high as 11.5 g/kWh. Two contributors to this are the reduced excess air ratio with dual fuel operation required to offset the comparatively weak ignition characteristics and the NOx emissions from diesel spray. At lower pilot quantity (~1% or less), the NOx emissions of the gas engine are possible but with the lower efficiency of the diesel. At these small pilot quantities, the early combustion phasing and high excess air ratio of the gas engine are not possible with the dual fuel engine and the combination of low NOx and high efficiency of the gas engine are not possible. However, the dual fuel concept does offer an alternative to the diesel engine with similar efficiency and lower NOx. Visualization work suggested that the poor combustion stability of low (~1%) pilot quantities could be a result of greatly reduced jet penetration of the diesel spray that could reduce the early flame front surface area and lower turbulence in the combustion chamber [ICEF2016-9359].
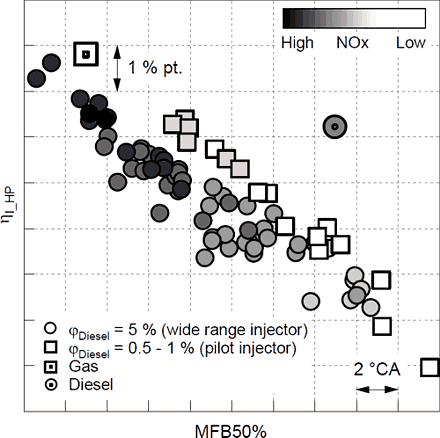
LEC also reported on investigations into the effect of Miller intake valve timing using ABB’s VCM technology on a single cylinder version of GE J624-H (Jenbacher) pre-chamber SI gas engine. The VCM system was configured to have a fixed IVO and lift but to vary IVC. The valve lift with the VCM could be higher than the baseline fixed valve lift profile. The baseline engine has a two-stage turbocharging system and uses a compressor bypass and throttle to control power. On advantage of engine operation with the VCM is that there is no need to retain a compressor bypass reserve (affects the pressure scavenging gradient and thus the pumping work) because a similar control effect is obtained by varying the timing of the intake valves. When the engine control strategy is changed from compressor bypass to IVC control, engine efficiency increases by about 0.5%. An additional gain of up to 0.4% is possible due to a change in shape of the valve lift profile. The Miller valve timing also enabled an increase in compression ratio that raised the potential total efficiency gain to 1.7%. The investigations were carried out using aggressive valve lift curves that may not be appropriate for serial application [ICEF2016-9358].
In two-stroke engines, one of the challenges to reducing PM emissions is effect of lubricating oil carried out with the scavenging air. To address this challenge, WinGD evaluated various tribosystem modifications for low speed two-stroke engines. The most effective solution identified was to introduce a modified ring pack and lube oil accumulating grooves to reduce lubrication losses due “ring pack spray”; a result of accumulated lubricant in the pressurized piston ring pack expanding into the scavenge air receiver during the scavenging phase. The ring pack modification attempts to distribute the oil on the cylinder wall more evenly in both the vertical and circumferential directions. A Federal Mogul eWaveⓇ ring generates a hydrodynamic cross flow to accomplish the distribution in the circumferential direction. An “R-Compression” ring supports the vertical distribution by accumulating a significant amount of lubricant in between the top ring and the R-compression ring. Lube oil accumulating grooves are located on the cylinder wall just above the scavenge port. They are designed so that pressurized combustion gas and lube oil mixture accumulated in the piston ring pack expands into a controlled volume before passing the scavenge air ports. Oil can be collected from the grooves. The effect of these measures on oil loss to the exhaust is shown below. [ICEF2016-9326, WinGD]
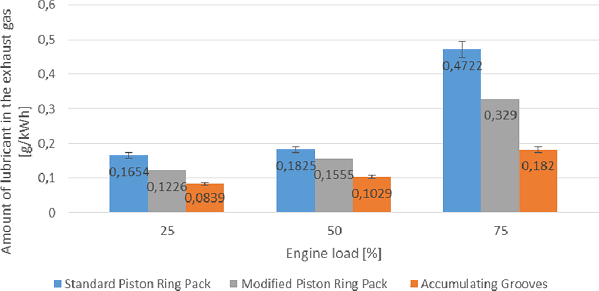
Natural Gas. An optical investigation of dual fuel combustion in a research engine with a Bowditch piston at the University of British Columbia revealed that combustion evolution can be significantly affected by pilot injection pressure. At a higher injection pressure, the diesel jet entrains and mixes faster with the charge gas and penetrates further into the combustion chamber resulting in auto-ignition of a partially-premixed diesel mixture at the bowl periphery. The reaction zone then propagates towards the center. For lower injection pressure, the diesel jet does not penetrate as far or mix as well resulting in the ignition sites that are localized around the vicinity of the pilot fuel jets and a more heterogeneous auto-ignition of the charge. Auto-ignition in these cases occurs after the end of injection and resulted in an increased the local equivalence ratio and intense soot luminescence. The minimum pilot quantity investigated was 10% [ICEF2016-9399].
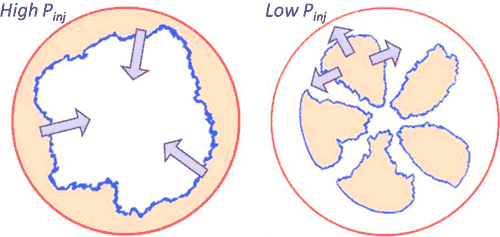
Other papers on natural gas included a study by Argonne on the effect of blending gasoline (port injected E10) and natural gas (direct injected) in an SI engine. Under WOT conditions, direct injection of natural gas was able to overcome the volumetric efficiency losses typically associated with conventional port injection approaches. Natural gas injection closer to IVC gave the highest IMEP. A 50/50 ratio of the two fuels gave the highest IMEP (11 bar) and indicated thermal efficiency (50%) DI NG because MBT timing could used. Lower blend ratios needed retarded timing to avoid knock at WOT with 100% E10 providing a maximum IMEP of 9.5 bar. Operation with 100% natural gas allowed a decrease in CO2 emissions of more than 20% under part-load conditions and 38% under WOT operation compared to 100% E10 [ICEF2016-9370]. Hanyang University also investigated direct injection of methane for light-duty applications. Their interest was to explore the effect of fuel injection timing and pressure at a part load condition. They found that combustion characteristics were strongly influenced by the end of injection timing rather than the start of injection timing. Late injection enhanced the combustion speed because of stronger turbulence at the time of spark. The injection pressure was not an important factor in the combustion. Injection after IVC yielded a 4% increase in volumetric efficiency [ICEF2016-9437].
Syngas. Synthesis gas produced by gasification or pyrolysis processes from sources such as biomass or municipal waste can be an attractive option for remote communities or as a means to extract value from waste materials. Cummins used an analytical tool that uses the fundamental combustion properties: laminar flame speed (LFS), adiabatic flame temperature (AFT) and autoignition interval (AI) to provide information about combustion duration, engine-out NOx, and relative knocking propensity to investigate syngas compositions from different production processes. The analysis indicates that the syngas samples considered should exhibit lower NOx emissions and less likelihood to knock than natural gas. A fuel system capable of providing large mass flow rate is required to avoid a reduction in engine power output. The air handling system needs to be optimized to support the additional charge flow requirements to also avoid a reduction in engine power output [ICEF2016-9430].
Canada’s NRC investigated emissions and efficiency impacts of syngas in dual fuel operation with diesel. The mixtures selected were meant to reflect the syngas composition from downdraft air-blown gasifier and downdraft oxygen-blown gasifier. Syngas substitution at low to medium load usually resulted in brake thermal efficiency that was as much as 4% lower; a higher H2/CO ratio or lower inert component content led to lower soot emissions; NOx emissions generally decreased except when the inert component of the syngas was low [ICEF2016-9367].
WHR. Waste heat recovery systems were also discussed. The potential fuel consumption benefit of an inverted Brayton cycle (IBC) waste heat recovery system on a light-duty vehicle driven over the WLTP was investigated at the University of Bath. The IBC system consists of a turbine, a heat exchanger and compressor(s) in sequence. The turbine fully expands the exhaust gas available from the engine to a pressure below ambient. The remaining heat in the exhaust after expansion is rejected by the downstream heat exchanger and then, the cooled exhaust gases are compressed back to ambient pressure by one or more compressors. For a single stage WHR system, the maximum potential BSFC benefit is 3%. This rises to 4.5% for a two stage system. [ICEF2016-9363, U. Bath] Clemson University found that working fluid pump speed predominantly influences Organic Rankine Cycle power production while the split of working fluid mass flow between EGR and tailpipe evaporators, turbine speed and condenser coolant water pump speed had minimal impact [ICEF2016-9378, Clemson].
Conference website: asme.org/events/icef