Conference report: US DOE 2017 Annual Merit Review
26 June 2017
The US DOE’s Vehicle Technologies Office (VTO) Annual Merit Review and Peer Evaluation was held in Washington, DC, on June 5-9, 2017. At this meeting, advanced vehicle technologies projects funded by VTO are presented and reviewed for their merit. The VTO’s portion of the meeting covers a wide range of topics including advanced combustion systems, combustion engines, electric drive systems and fuels and lubricants. The meeting also covers the Hydrogen and Fuel Cells Program. Unlike talks at other meetings, the intent of the presentations is not necessarily to present final results but rather to discuss progress and challenges in multi-year projects and to allow reviewers to provide feedback and guidance on the project.
Please log in to view the full version of this article (subscription required).
Engine Efficiency. On the topic of heavy-duty engine efficiency, Cummins [Kocher, ACS098] discussed their program to demonstrate a 55% BTE engine. Not to be confused with the SuperTruck II program discussed below, this program is intended to demonstrate a peak BTE of 55% using a 15 L engine. Cummins has demonstrated 50% BTE without waste heat recovery in the test cell. The target engine speed for peak efficiency is 1000 rpm. Some of the features required to achieve this efficiency include: fast opening, cavitation free fuel injectors for rapid and shorter heat release; a low heat transfer combustion system with insulated surfaces that is able to turn piston cooling off or operate at reduced oil flow to lower the parasitic load required to supply the cooling oil flow to the piston underside; numerous changes to reduce friction and parasitic losses from the coolant and lube system, valve train and power cylinder; an optimized exhaust manifold to utilize exhaust pulsation energy and a dual loop EGR system. The low backpressure aftertreatment system has been moved closer to the engine to facilitate warm-up and gaseous ammonia injection is used to allow earlier activation of the SCR catalyst. Use of the gaseous ammonia delivery system is meant only for development purposes. Also, an SCR on the DPF (SCRF) allows for one less catalyst brick in the system. The waste heat recovery system is a dual loop design with high and low pressure loops utilizing heat from the high and low pressure EGR coolers, the post aftertreatment exhaust, charge air cooler and engine coolant and lubricants. A new axial turbine expander with both high and low pressure plenums is connected to a fixed gear ratio transmission; the Van Dyne variable speed transmission was not carried over from the Supertruck I program. The WHR system is expected to provide an incremental increase in BTE of 4%.
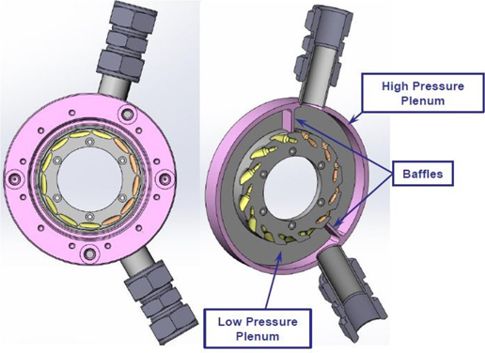
Details of the four Supertruck II projects announced in August 2016 emerged as the teams discussed the approaches they hope to use to demonstrate a minimum of 55% BTE for the engine at a 65 mph cruise and an improvement in Freight Efficiency of 100% or more relative to a 2009 baseline. The later objective is made less daunting by the fact that commercial vehicles have already achieved a significant portion of this target; e.g., Daimler’s 2017 Cascadia is claimed to have an 81% better freight efficiency than the 2009 Cascadia.
The Cummins/Peterbilt [Ruth, ACS102] Supertruck II program uses a 13 L engine having many of the same features used in the 15L engine discussed above. The smaller 13 L engine also provides an aerodynamic advantage for the vehicle. A 48 V mild hybrid system will be employed and connected to the PTO of the transmission where more energy can be recovered than would be the case for a connection to the front of the engine. The proposed energy recovery strategy is as follows:
- Decouple engine on gentle down grades
- Use with engine brake on steep down grades
- Use with service brake in slow / city traffic
- Shave power on gentle inclines or flat roads
- Supplement power on accelerations, in traffic and on inclines
Initial analysis suggests that an electric machine size of more 30 kW and battery capacity above 3-4 kWh gives diminishing returns.
Layout of the 48 V hybrid system in the Cummins/Peterbilt Supertruck II. BMS: battery management system, PE: power electronics, DC/DC: DC converter, M/G: motor generator - Daimler’s [Yee, ACS100] approach will also be based on a 13 L engine and a 48 V hybrid system. The 360 V hybrid and 11L engine of Supertruck I will not be used. The vehicle may also use start/stop. The Supertruck I WHR system worked well at high load but not at lower loads and further improvements will be required including: different working fluid (ethanol was used in Supertruck I), lower temperature condenser, improved expansion machine (a scroll expander used in Supertruck I) and utilization of additional heat sources.
- Volvo [Amar, ACS 101] has not made a final decision on their powerplant but is considering either an 11 L 6 cylinder 4 stroke or a 7-8 L downsized 4 stroke engine. While not completely off the table, a third option is the split cycle engine considered in Supertruck I for achieving 55% BTE. However, the later has a low probability of being selected.
- Navistar [Zukouski, ACS103] is considering using a gasoline compression ignition (GCI) engine strategy utilizing regular pump grade gasoline (87 AKI E10). The approach is being evaluated with Argonne National Laboratory.
For light-duty engines, Eaton [Patil, ACS112] is developing a boosting and downsizing solution that uses a Roots supercharger with electrical assist and variable speed drive (Electrically Assisted Variable Speed TVS Supercharger, EAVS) combined with a Roots based expander for the exhaust (Roots Based Electric Direct Waste Heat Recovery, eWHR). Simulations suggest up to 22% improvement in fuel economy in a diesel application is possible. GM [Sczomak, ACS093] is applying the EAVS to a lean burn Miller cycle gasoline engine.
Oak Ridge National Laboratory [Szybist, ACS015] is developing an engine using thermochemical recuperation by using a catalyst in the EGR loop. In this approach, a cylinder is dedicated to produce EGR and operates lean to feed oxygen to a catalyst. A post injection of fuel (regular gasoline) is used to create a rich feedgas (3-10 ϕ) to the combined steam reforming and partial oxidation reforming catalyst. This reformate is then introduced to the intake of the other cylinders. The remaining cylinders operate at stoichiometric to allow the use of a three way catalyst. The approach allows EGR and MAP to be increased without degrading combustion stability. At part load, a BTE of 32.2% is possible compared to the baseline case without EGR of 29.3%. Conventional EGR in the baseline engine yielded a maximum of about 30.5% BTE.
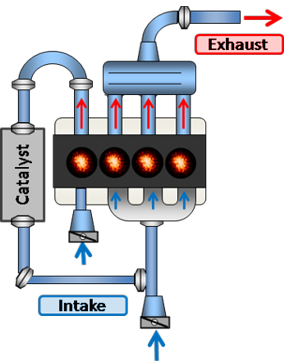
Diesel Combustion. An interesting approach to mixing controlled diesel combustion developed by Charles Mueller of Sandia National Laboratories [Singh, ACS000][Dec, FT056] shows that it is possible to have “soot-free” combustion without having to resort to highly premixed combustion strategies. In this approach, Ducted Fuel Injection (DFI), the fuel jet from the injector is first directed into a small diameter tube that greatly enhances the mixing of air and fuel prior to ignition. The end result is that the richest autoigniting mixtures become leaner and little or no soot is produced. The approach is also tolerant of dilution for NOx control and does not require oxygenated fuels. It is also thought that combustion efficiency is improved by limiting over-mixing at the spray periphery. The later has yet to be confirmed. A patent application for this approach has been published.
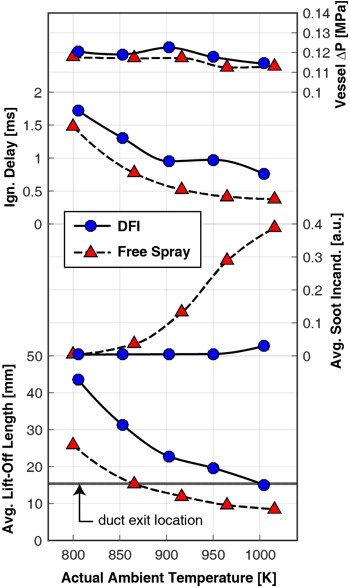
There were several other interesting diesel combustion programs. One intended to gain a better understanding of the mechanism behind the PM reduction potential of a close-coupled post injection in heavy-duty diesel engines [Musculus, ACS001] presented the first clear evidence of post-injection soot oxidation resulting from an increased temperature due to the post injection. Another intended to better understand the differences between re-entrant and stepped-lip combustion systems [Busch, ACS002] showed that faster late-cycle heat release (through changes in late-cycle mixing due to bowl geometry) increases the degree of constant volume combustion and thereby thermal efficiency.
Gasoline Compression Ignition. A number of talks focused on Gasoline Compression Ignition. Delphi [Confer, ACS094] provided an update on the progress of their GDCI concept. Since this was last reported on, the BSFC target for the Gen 3 engine has been set to 200 g/kWh at < 0.2 g/kWh NOx. BSFC values as low as 204 g/kWh were reported. One of several remaining challenges is the refinement and demonstration of an aftertreatment system capable of dealing with the low exhaust temperature (see Figure below).
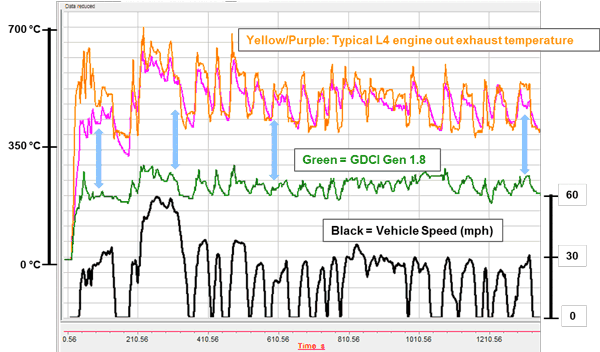
In the near future, Delphi’s GDCI will be benchmarked against a modified 1.8L Turbocharged VW Gen 3 EA888 engine updated with Delphi/Tula Dynamic Skip Fire. This engine represents a future state of the art spark ignition engine that is believed to be representative of what will be in the market at the time that a GDCI would be ready for production.
Another program at Sandia applies GCI to a medium duty engine (~1 L/cyl) [Dec, ACS004] and utilizes Spark Assist to initiate combustion under some operating conditions. Simulations suggested that this approach provided improved fuel economy over several hybrid drivetrain options. Work at Argonne [Ciatti, ACS011] demonstrated how challenging it is to improve efficiency with GCI while trying to keep combustion noise below 90 dB.