Conference report: ASME ICE 2017 Fall Technical Conference
31 October 2017
The ASME Internal Combustion Engine 2017 Fall Technical Conference (ICEF 2017) was held on October 15-18, 2017 in Seattle, Washington, USA. The conference was attended by about 220 delegates and hosted by Paccar. The event included a two-day technical program with 107 technical papers, as well as keynote talks, and student presentations. Conference participants could also take part in a technical tour of the Paccar Technical Center (PTC) in Mount Vernon, WA—an engineering, simulation and validation facility for trucks, truck engines, and components.
Chris Atkinson, Program Director, ARPA-E provided a keynote talk on Tuesday morning. The goal of ARPA-E is to overcome long term and high risk technology barriers in the development of energy technologies. One of the topics he discussed was vehicle automation and its effect on fuel consumption.
SAE defines six levels of vehicle automation, L0 to L5, as summarized in the Figure below.
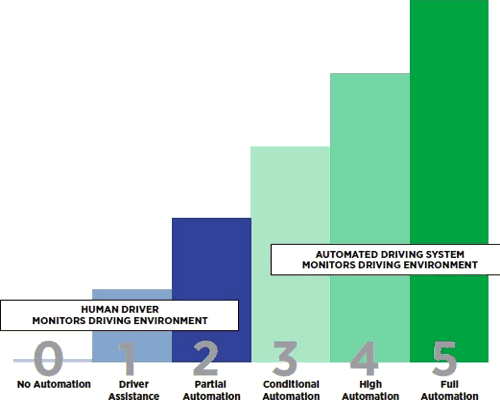
The impact of high levels of vehicle automation on energy use and consumer costs is not entirely clear. It could lead a decrease in energy use of up to 50% or an increase as high as 300%. Vehicle miles traveled may actually increase through increased urban sprawl and driving by proxy—the later being the case when the vehicle self drives without a human operator. A key benefit of high levels of automation is that the vehicle should be “intrinsically safer” allowing for significant weight savings due to the need for less safety equipment. Also, vehicle connectivity allows for platooning, traffic signal phasing and timing optimization and traffic congestion mitigation.
Automation also opens up possibilities for powertrain control to save fuel. Powertrain control will have full future predictive capabilities and vehicles will know what their future power demand will be. This is especially useful for hybrid powertrains due to the possibility of optimizing multiple sources and sinks of energy and power. It will allow for the use of a whole new class of high efficiency, poor transient response engines.
Another topic discussed was the future of the IC engine. Predictions on the proportion of vehicles post 2030 that will have an IC engine range from 0% (various advocacy groups, China, India, Norway) to 80% (IEA, DOE, EPA, IEAE, most OEMs, many suppliers). The most probable outcome is that IC engines will continue to dominate in heavy-duty applications, with some mild hybridization probable, and hybrid electric powertrains will dominate in light-duty vehicles where the spectrum from 48V mild hybrids to strong hybrids will be seen. Overall, about 80% of vehicles in North America, including heavy-duty, will likely have an IC engine. In Europe, it will be about 60%, China may be as low as 20% and the rest of the world about 90%.
Dual Fuel Natural Gas-Diesel Engines
Pilot Ignition. Applying Miller cycle to dual fuel engines is challenging because the lower TDC compression temperatures make it more difficult to ignite the diesel pilot. Researchers at the Technical University of Munich presented two papers on work intended to illuminate the factors affecting diesel pilot injection in dual fuel engines [ICEF2017-3548][ICEF2017-3549].
- If the combustion chamber temperature drops below about 400°C, the ignition delay becomes too long and the air-fuel mixture within the diesel spray falls below the lean ignition limit. The critical ignition delay time at which this occurs is about 5 ms.
- At temperatures below about 480°C, a lower diesel injection pressure (500 bar) leads to more reliable ignition than higher (1000 and 1500 bar) injection pressures—too much air is thought to be entrained into the diesel pilot making the ignition delay too long. The injection pressure trend is reversed at higher temperatures where higher injection pressure yields better ignition.
- Near the lower limit of pilot ignition (400°C) a pilot fraction of 0.5% can be challenging to ignite - an average 3.0/10 pilot sprays ignited. At an 8.0 % pilot fraction, 8.9/10 sprays ignited.
- The natural gas air-fuel ratio also affect ignitability of the pilot spray, when the premixed gas air/fuel ratio was reduced from λ = 2.20 to 1.80 near 400°C, the number of ignited sprays increased from 2.5 to 3.7 and the ignition delay decreases from 9.4 to 3.3 ms.
Researchers from the Karlsruhe Institute of Technology investigated the potential of high cetane number pilot fuels for achieving reliable ignition with pilot quantities down to 1% - these small pilot quantities were needed to achieve engine out NOx emissions ~0.4 g/kWh [ICEF2017-3589]. Reducing the pilot injection amount with diesel fuel (~45 CN) down to 1% leads to premixing of the diesel prior to ignition (ignition occurs after the end of the pilot injection), some loss of combustion phasing control and increased cyclic variability. For higher cetane number fuels, fuels (CN > 70), ignition occurs prior to the end of injection and combustion phasing control can be maintained with low cyclic variability.
In dual fuel engines, the advantage of lower CO2 emissions relative to diesel is offset to a certain degree by the higher methane emissions and low engine efficiency at low load conditions. A team at the National Research Council Canada investigated diesel injection split—with diesel injection delivered in two separate pulses—as a potential strategy to improve the performance of dual fuel engines at low load conditions [ICEF2017-3584][ICEF2017-3585]. It was shown in engine experiments that diesel injection split reduced the peak pressure rise rate and allowed part of the diesel to be injected at an earlier timing than for a single injection. This created an HCCI-like combustion mode with reduced CH4 emissions. At a certain timing range of the two injection pulses, the strategy could provide a simultaneous reduction of NOx. The effect of the split diesel injection on higher hydrocarbon emissions was also investigated. The experiments were conducted with a NG energy fraction of 50% and 75%.
Due to its diesel-like performance, direct injection of natural gas into the dual-fuel engine cylinder (High Pressure Direct Injection, HPDI) remains an attractive natural gas engine concept. The Technical University of Munich conducted an interesting study of the spatial and temporal interaction between diesel pilot and the directly injected natural gas jet [ICEF2017-3532]. A laboratory compression ignition test rig with optical access was developed that included two single nozzle injectors, one for diesel and one for natural gas. The angle between the two sprays was changed by rotating the NG injector. A set of criteria for successful ignition was formulated in terms of the angle between the sprays and their relative injection timing. A numerical simulation was also developed to predict the combustion process when using natural gas direct injection [ICEF2017-3533]. The main focus was to analyze the capability of predicting the pressure curve and heat release rate for different injection strategies.
NOx Emissions with Pilot Injection. A team by Hiltner Combustion Systems and Caterpillar investigated NOx formation in dual fuel engines with a focus on NOx emission trends with air-to-fuel ratio and the natural gas substitution level. The study was driven by gas drilling applications, where operators start with 100% diesel fuel, then increasingly substitute diesel with wellhead natural gas. Experiments were conducted in a single cylinder diesel engine with natural gas fumigation into the intake air [ICEF2017-3522], followed by combustion simulation work [ICEF2017-3642]. In general, NOx emissions were found to trend with the premixed gas lambda, λng (as opposed to λtotal), which is a result of the contribution of NOx from flame propagation in the gaseous portion of combustion. For natural gas substitution rates above 70%, NOx emissions contain a local minimum, which occurs approximately at λng = 1.7 – 1.85. It was hypothesized that at richer conditions (λng < 1.7), NOx formed in the burning of gaseous fuel results in increased total NOx emissions. At leaner conditions (λng > 1.85), the increased NOx emissions were attributed to the NOx formed in the diesel post flame regions, as a result of increased oxygen availability.
A simulation study of NO2 formation and destruction in a natural gas-diesel dual fuel engine was conducted by an international team led by the West Virginia University [ICEF2017-3688]. NO2 was mainly formed in the interface region between the hot NO-containing combustion products and the relatively cool unburnt methane-air mixture. NO2 formed at the early combustion stage is usually destructed to NO after the complete oxidation of methane and n-heptane, while NO2 formed during the post-combustion process would survive and exit the engine. The HO2 produced during the post combustion process of methane was identified as the primary species dominating the formation of NO2. It was concluded that the increased NO2 emissions from NG/diesel dual fuel engines was formed during the post combustion process due to higher concentration of HO2 produced during the oxidation process of the unburned methane at low temperature. This is similar to the NOx mechanism for diesels.
Gas Engines
Methane Number has been shown to be a good indicator of knock propensity in stoichiometric SI engines. In lean burn SI engines, it has been less effective. Two fuels with the same methane number, but with different compositions, may exhibit a different propensity to knocking in lean burn SI engines. This effect is particularly pronounced when comparing fuels that have different amounts of diluents. Cummins proposes a lean burn methane index (LBMI), which is estimated by removing diluents found in the fuel from the calculation, as a better predictor of knock propensity when comparing fuels with widely varying levels of dilution [ICEF2017-3553].
The University of Washington and Hiltner Combustion Systems used modeling to better understand pollutant emissions formation in large bore lean burn natural gas engines [ICEF2017-3577]. CO and HCHO emissions arise from partial oxidation late in the expansion stroke as any remaining unburned charge mixes with the burnt gas. Engine tests show the correlation of UHC and CO emissions to crevice volume. These tests suggest that HCHO emissions also are affected by crevice flows through partial oxidation of crevice hydrocarbons late in the expansion stroke.
Large bore lean burn natural gas engines are typically used in applications with high fuel usage. Hiltner Combustion Systems looked at the possibility of using dilute stoichiometric combustion in these applications to enable the use of a three way catalyst [ICEF2017-3608]. In order to match the efficiency of a lean burn engine, Miller valve timing and an increased CR would be required.The brake thermal efficiency with EGR dilution was shown to be sensitive to the EGR system pressure drop and the method of handling water vapor condensation.
Woodward showed there is a competition between the knock suppression benefits of EGR and the knock attenuation impact of hot residual gas retention due to increased backpressure needed to drive high pressure EGR [ICEF2017-3669]. There are diminishing returns where higher EGR rates do not further suppress knock because of a higher retention of hot residual gases. Residual gas increases the unburned gas temperature up to and above the auto-ignition threshold despite higher levels of cooled EGR. To improve the EGR response, the focus needs to be on delivering EGR with less backpressure.
Argonne, Ford and others discussed work on in-cylinder blending of gasoline and natural gas [ICEF2017-3661]. Natural gas (NG) was directly injected into the cylinder after IVC to overcome the power density loss usually experienced with NG port-fuel injection. Gasoline was injected into the intake-port. Increasing the CR from 10.5 to 14.5 allowed an absolute increase in indicated thermal efficiency of more than 3% for 75/25 NG/gasoline operation at 8 bar net IMEP and 2500 rpm.
Diesel Engines
FEV conducted an analysis of engine strategies to meet the US EPA Phase 2 greenhouse gas emission requirements for heavy-duty diesel engines [ICEF2017-3552]. Simulated and experiential BSFC and NOx results were presented for a medium duty, 6-cylinder, 7.7 L vocational use diesel engine with single stage turbocharging. The considered technologies included engine downsizing (with a dual turbo), downspeeding, turbocompounding (with a clutch), variable compression ratio (VCR), and cylinder deactivation. Engine downsizing was the most effective strategy, with an FTP BSFC reduction of 9.2%, followed by downspeeding at 4.6%. The downsizing strategy also produced the longest delay in the SCR catalyst warm-up—a potential source of NOx compliance challenges.
Doosan discussed the development of their Stage V nonroad diesel engine [ICEF2017-3542]. The development started with the existing Tier 4 final, 100 kW/130 hp engine with EGR and SCR and using Doosan’s Ultra Low Particulate Matter Combustion (ULPC). ULPC features Ricardo’s Twin Vortex Combustion System (TVCS). A DPF must be used in the EU Stage V engine to meet the PN emission limit. Because of the relatively small engine size, the cost of EGR+SCR+DPF would be hard to justify. Doosan is considering SCR+DPF aftertreatment without EGR for this engine range for Stage V. At this stage of development, the Tier 4 wastegated turbine is retained—removing EGR increases the flow through the turbine to increase backpressure and BSFC. Further work on selecting an optimized turbocherger will be carried out. To offset the BSFC increase, the compression ratio is increased from 17 to 18.0. Retarded injection timing is considered to meet an engine out NOx target of 9-11 g/kWh. An SCR system—still under development—will be used to meet the Stage V NOx limit of 0.4 g/kWh. The new engine will use a different combustion system referred to as Ultra Low Fuel Consumption (ULFC) combustion system, details of which have yet to be published.
Locomotive Engines. Unventilated tunnels at high altitude and with an uphill grade are one of the most challenging environments for diesel-electric locomotives. GE Transportation showed that on trains with multiple locomotives, the intake air temperature of locomotives behind the lead locomotive can reach ~90°C [ICEF2017-3693]. To avoid engine damage, engine power is designed to decrease as ambient temperature rises. In one of the most severe tunnels in the US, Norden Tunnel #41 at the Donner Pass, trains with Tier 2 locomotives can slow down to 6 mph (10 km/h) because of the derating. If the train speed drops below 5 mph (8 km/h), the train is considered stalled and the crew needs to stop the train and evacuate. Modeling results for GE’s Tier 4 locomotives that use EGR to help control NOx emissions showed that with the EGR system on, a train with Tier 4 locomotives would slow down about 2.5 mph below that of the train with Tier 2 locomotives and be at greater risk of stalling. In order to maintain the train speed at or above that for the train with Tier 2 locomotives, an Auxiliary Emission Control Device (AECD) was used to shut off the EGR system when intake temperature exceeded 55°C (130°F).
Ganser CRS discussed their common rail systems for large engines such as medium speed locomotives [ICEF2017-3531]. Unique to the Ganser injector is the use of an intermediate poppet valve that opens a large passageway from the high pressure volume to the control volume above the injector needle; allowing for fast injector closing and facilitating multiple injections. For locomotive applications, a maximum 1600 bar pressure can deliver up to 1600 mm3/stroke with a 4.5 ms energize pulse. The injector, along with a split cooling system, was installed on a 1989 V16 GE® 7FDL locomotive to bring emissions down to Tier 0+ levels. Unlike the existing mechanical fuel injection system that was primarily optimized for Notch 8, the common rail system parameters allow for some optimization of injection pressure, timing and multiple injection strategy at all notch positions and for variations in temperature and pressure. Skip firing was introduced at low idle to further reduce the fuel consumption. A fuel savings of 6.6% over the EPA freight duty cycle was claimed. EPA Tier 1+ and Tier 2+ emissions are also possible depending on the fuel saving targets.
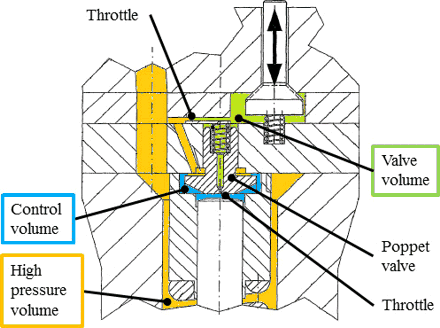
Mechanical turbocompounding was reviewed by DieselNet staff [ICEF2017-3695]. This is an option for highly loaded heavy-duty engines in high fuel usage applications such a long haul class 8 trucks. Engines with mechanical turbocompounding need to operate near full load to realize a fuel savings benefit. Recent product announcements by Volvo and Daimler for North America show there is a place for mechanical turbocompounding for the near future.
Gasoline Direct Injection
Factors affecting PN measurement variability was discussed by the University of Toronto [ICEF2017-3620]. When variations in PN emissions from a 2012 2.0 L Ford GDI engine Tier 2 Bin 4 were examined closely, variations in operating parameters (fuel and oil temperature, PCV filtration) and test conditions (dilution air conditions) could not account for the level of measurement variability observed. It was noted that exhaust emissions of toluene and ethanol were correlated positively with PN emissions, while emissions of isobutylene correlated negatively. Exhaust emissions of toluene and isobutylene were interpreted as markers of gasoline aromatic content and gasoline volatility respectively. Tests conducted with gasoline containing splash blended ethanol (10% and 30% v/v) found that increasing ethanol fuel content increased PN emissions at the steady-state operating condition utilized. Further work is planned to better interpret the observations.
Numerical simulation were carried out at the University of Michigan to investigate the effects of injection strategies on the charge composition and local thermodynamic conditions in a GDI engine [ICEF2017-3623]. When the physical time for air/fuel mixing is not long enough, fuel-rich pockets are present until combustion occurs, where high concentrations of soot precursors are found. Additionally, the location of wetted surface as well as the in-cylinder flow structure induced by the fuel jet hitting the piston bowl, which subsequently affects air/fuel mixing, is influenced by injection timing. When the injected fuel mass is increased, the equivalence ratio distribution inside the combustion chamber generates larger regions of Φ > 1 .5 where the formation of soot precursors is favored. This confirms the hypotheses is that local rich pockets inside the combustion chamber are an important source of PM emissions from GDI engines.
Mahle’s ultra lean (λ ≥ 2) burn SI engine is structured around a pre-chamber assembly package incorporating the spark plug and fuel injector, Mahle Jet Ignition® [ICEF2017-3528]. It was estimated that BTE > 42% is possible with this approach. Due to the low exhaust enthalpy, a VTG would be required to achieve a high enough engine output while achieving high efficiency and reducing system complexity.
Advanced Combustion
Argonne National Laboratory has studied fuel injection strategies to address the challenges of gasoline compression ignition (GCI) at high engine load condition [ICEF2017-3625]. While large amounts of fuel injected early for premixed combustion can provide low emissions, it is harder to control combustion phasing and leads to high combustion noise. More fuel late injected late is easier to control but leads to poor mixing and higher smoke. Multiple injections are key to controlling fuel stratification and achieving a balance between emissions, noise and controllability. A pilot injection at 70° BTDC was selected to avoid a high level of premixed combustion. The pilot, followed by a main injection at 50° BTDC were sufficient to create a highly reactive mixture that could be ignited with a post injection after 30°BTDC. The timing of the post injection had a strong linear relationship with combustion phasing. Engine loads up to 14 bar BMEP were achieved with good control of combustion noise and low emissions of NOx/HC/CO; at higher loads, smoke emissions became excessive.
Oak Ridge and the University of Wisconsin, Madison summarized experimental work on reactivity-controlled compression ignition (RCCI) in a small-bore, multi-cylinder engine operating on premixed iso-octane and direct-injected n-heptane [ICEF2017-3607]. They showed an unexpected combustion phasing advance at early injection timings, which has not been observed in large-bore (heavy-duty) RCCI engines at similar conditions. In larger engines, advancing the injection timing of the high reactivity fuel (n-heptane in this case) typically leads to less fuel stratification and more HCCI-like combustion. This expected behavior was not observed in the small bore (82 mm bore) engine when the high reactivity fuel was injected earlier than about 65°BTDC. CFD modeling showed that at these early injection timings, n-heptane was deposited on the cylinder liner wall that could lead to a high reactivity zone in the squish region that advances combustion phasing. Oil droplets created by the impingement could also serve as ignition sources.
Pinnacle Engines is developing a gasoline fueled, spark ignition 1.2 L 4-stroke opposed piston sleeve valve engine [ICEF2017-3616][ICEF2017-3618]. Simulation results at the Oak Ridge Leadership Computing Facility suggest that Tier 3, Bin 160 emissions are possible using high levels of EGR with only an oxidation catalyst for hydrocarbons.
Emission Aftertreatment
A team from the Technical University Munich studied urea hydrolysis for ammonia production in marine SCR systems [ICEF2017-3537]. Experimental work was conducted in a laboratory hydrolysis reactor rig using a 40% urea solution typical for marine SCR applications. Droplet velocity, gas temperature and the water content were found to have major impact on system performance. Based on the experimental work, a modeling approach was developed for urea hydrolysis reactors.
Direct measurement of the amount of ammonia stored in the SCR catalyst washcoat could be a valuable tool for the control of SCR aftertreatment. CTS Corporation, who had developed an RF-based DPF soot sensor, reported on their newest work to adapt the technology for NH3 measurement [ICEF2017-3572]. It was shown in laboratory test bench experiments that the drop and shift of the RF signal over an ammonia loaded SCR catalyst correlated with the amount of NH3 stored in the washcoat. Temperature calibration of the signal must still be developed to account for ammonia oxidation that increases with temperature.
A durability study of a Pt/Al2O3 oxidation catalyst in a stationary engine application was conducted by researchers at the Gonzaga and the Colorado State Universities [ICEF2017-3550]. The catalyst was installed on a large bore, 2-stroke, lean burn natural gas GMVH-12 engine to satisfy the CO/HCHO emission requirements of the US EPA RICE NIESHAP regulations. The catalyst was aged in the field over a 24-month period. Every two months, the catalyst was brought to the laboratory for engine emission testing and catalyst surface analysis. A number of catalyst poisons derived from the engine lube oil were analyzed, including S, Zn, P, Ca, Pb. Both the catalyst light-off temperature and its peak efficiency decreased with the aging time and the accumulation of catalyst poisons in the washcoat. The results of the study can help site operators to determine the intervals of catalyst replacement or regeneration when complying with the NIESHAP regulations.
Turbocharging
Mainstream Engineering assembled a hybrid-electric turbocharger using an 11kW permanent-magnet machine coupled to a commercial turbocharger via an in-line, bolt-on housing attached to the compressor inlet [ICEF2017-3521]. A variable frequency drive (VFD) and sensorless control algorithm were also developed with ramp rates of over 68,000 rpm/s possible. One challenge with attaching the motor to the end of the compressor shaft in high speed turbochargers is that one of the bending critical speeds of the rotor typically falls within the turbocharger’s operating speed range. Active control of the turbocharger speed was used to avoid operation at these speeds.
Engine Control
University of Bologna in collaboration with Magneti Marelli Powertrain [ICEF2017-3568] discussed the use of a microphone to compensate for injector aging effects on the fuel injection quantity in pre-injections. The researchers previously discussed using a similar technology for turbocharger speed control.
A common approach to EGR control is to control the EGR valve position via feedback from the mass air flow sensor and variable geometry turbocharger (VGT) nozzle position via feedback from the manifold pressure sensor. This approach is challenging for a number of reasons including the fact that it requires significant calibration effort. Researchers at the University of Michigan and Isuzu presented an alternate approach where the VGT position is used to control the pressure difference between the exhaust and intake manifold (∆P) and the EGR valve is incorporated into a cascading control loop using cylinder oxygen fraction estimation and an exhaust NOx sensor [ICEF2017-3672]. Using the estimated cylinder oxygen fraction improves NOx control during transients; the NOx sensor feedback allows for corrections in the oxygen fraction estimation. While the ∆P control via the VGT position requires a compensator to improve transient response, it is less sensitive to set point errors.
Operating with high rates of dilution in premixed charge engines is a considerable control challenge due to need to minimize the effect of misfires. A common control approach is to significantly retard spark timing whenever a misfire is detected and then slowly advance it until misfires are again detected. This approach is over conservative and leaves some of the benefits of dilute operation unavailable. The University of Michigan showed an alternative “likelihood” based controller that instead retards spark advance only enough to keep the rate of misfires detected in a moving window at an acceptable value—below 0.2% [ICEF2017-3679]. The result was that the likelihood based controller kept the combustion parameters at the desired values for longer periods of time - improving the benefits of dilute combustion.
* * *
The next ASME Internal Combustion Engine Fall Technical Conference will be held on November 4-7, 2018 in San Diego, California.