Conference report: 6th International Conference Aftertreatment & Sensors
26 September 2019
The 6th International Conference Aftertreatment & Sensors, organized by Süddeutscher Verlag Veranstaltungen, was held in Munich, Germany on September 19-20, 2019. The technical program included presentations by government, academia, and industry experts on emission regulations, emission control and aftertreatment, and sensors used in engines and emission control systems.
Regulatory Trends. European clean air regulators are apparently satisfied with the prolific stream of amendments to the Euro 6/VI emission standards, and are focusing on the next-stage Euro 7/VII regulations for light-duty (LDV) and heavy-duty vehicles (HDV), respectively. The Euro 7/VII standards have not yet been proposed, but a number of ideas have been under consideration. These include [H. Jahn, German Environment Agency][S. Carstens, EngineSens]:
- Fuel-neutral limit values (i.e., the same set of limits for vehicles fueled by diesel, gasoline and other fuels)
- NOx emission limit of 35 mg/km, matching that of China 6
- Particle number measurement with a 10 nm cut-off (PN10), down from the current 23 nm
- Emission limits for additional pollutants (potentially including ammonia, formaldehyde, and other species)
- Extended altitude conditions (current EU RDE testing requires 1300 m, while China 6 requires an altitude of 2400 m)
- Conformity factor of 1 for real driving emission (RDE) testing
- Emphasis on cold start and warm-up phase performance
- Low temperature type approval test (-7°C) for diesel engines (type VI) to verify the effectiveness of NOx reduction technologies
- Extension of the emission durability periods, possibly up to 200,000 km for LDVs (currently 160,000 km for LDVs and 700,000 km for HDVs)
- New durability requirements for battery electric vehicles (BEV)
- Remote sensing and extended use of RDE testing for in-service conformity (ISC)
- New in-use testing requirements (periodic technical inspection, PTI) for PN and NOx (type II test)
It may be hoped that the Euro 7 regulation will be more robust and efficient than the previous emission stages. The succession of Euro 3, 4, 5, and 6 emission standards showed only limited effect on reducing vehicle emissions, and can be considered an exercise in diminishing return of increasingly more complex regulations. This is especially true in the case of real world NOx emissions from diesel vehicles, Figure 1 [N. Molden, Emissions Analytics].
Test results by Emissions Analytics
As apparent from the figure, the increasingly more stringent emission stages show little distinction in real world NOx emissions, with almost all vehicles emitting more NOx in real driving than over the regulatory test cycles. This changed only after the introduction of RDE testing requirements at the Euro 6d-TEMP stage; most of post-RDE diesels tested by Emissions Analytics had real world NOx below the applicable limits (the dashed lines represent the respective Euro 6d-TEMP and Euro 6d RDE NOx limits).
RDE testing, while complex and costly, appears to be one of the most effective methods to control LDV emissions, and its importance is expected to increase in the future [K. Mathies, TÜV Hessen]. RDE Package 4 (Directive (EU) 2018/1832), in force since 1.1.2019, is the basis for in-service conformity (ISC), which involves testing of used customer vehicles and may provide the most effective control of light-duty vehicle emissions.
Emission Control. Meeting the RDE limits may require significant changes to the engine emission control and aftertreatment systems. In light-duty diesel engines, Volkswagen introduced a “twin-dosing” SCR architecture, with a second SCR catalyst added in the underfloor position [S. Carstens, EngineSens]. The underfloor catalyst, exposed to lower exhaust temperatures, ensures compliance with RDE NOx limits during high speed driving, when temperatures are too high for the close-coupled SCR catalyst (coated on the particulate filter).
In gasoline engines, the future Euro 7 standards are expected to cause a more widespread use of water injection technologies. Water injection (into the combustion chamber or the intake manifold) has been used in some gasoline engines, for example by BMW, to reduce knock and enable increased compression ratio. At the Euro 7 stage, water injection is expected to be used to avoid mixture enrichment at high speed, in order to reduce CO2 emissions and to control NH3 that is formed over the three-way catalyst at rich conditions. In some respects, the development of water injection systems and on-board water storage can be more challenging compared to urea (AdBlue) tanks, because of the higher freezing point of water, higher melting enthalpy, higher fluid consumption, and susceptibility to bio-contamination [N. Schumacher, Kautex]. A VDI working group has been formed to support development of the necessary standards and testing procedures (water quality, refilling interface, bio-contamination), targeting market introduction of the water injection technology in 2020/2021.
A retrofit water injection system has been developed for diesel cars, to reduce NOx emissions and to allow older diesels to enter the “diesel ban” zones [C. Elvers, GoDiesel]. The system has a NOx reduction potential up to 50%, but requires water injection rates in excess of 60-70% relative to the fuel consumption. A further challenge is presented by the potential interactions with the vehicle EGR system. A Euro 4 vehicle (BMW 520d with N47 engine) with a simple, single loop EGR has been chosen as the initial application.
Dinex [M. Geist] presented an overview of SCR catalyst technology, including vanadia and vanadate (FeVO4) catalysts, as well as iron- and copper-zeolite formulations. Performance and aging data was shown for a number of catalysts, and various SCR configurations were discussed including SCR-on-filter.
Sensors. The global market for automotive exhaust sensors (Figure 2) amounts to $1.9 billion and is predicted to remain constant [R. Dixon, IHS Markit]. The world’s car production no longer grows—the new car market is expected to decline through 2020, recover to the 2018 level of just above 90 million vehicles by 2025, and remain flat through 2030. The shipments of automotive sensors reached 170 million in 2017, and are predicted to reach 212 million in 2024. This moderate growth is driven by the introduction of new vehicle technologies. The fastest growth is expected for differential pressure and temperature sensors for gasoline particulate filters, as well as for current and temperature sensors for electric vehicles. Another possible growth area are ammonia/NOx sensors to monitor NH3 emissions from Euro 7 vehicles.
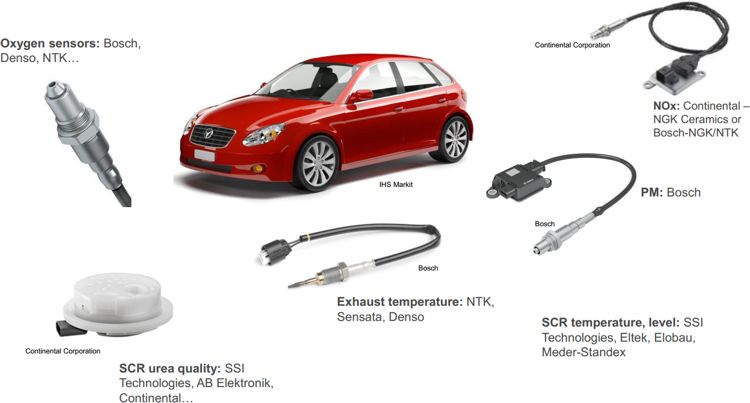
Several talks were given on new sensor technologies. These included a presentation by IAV [M. Moser] on the use of radio frequency (RF) sensors for NH3 load determination in SCR catalysts. The RF sensor, developed in cooperation with Continental, was used in the AECC diesel demonstrator car presented at the Vienna Motor Symposium earlier this year to monitor the underfloor SCR catalyst. Another potential application of the RT sensor is monitoring of soot load in gasoline particulate filters.
CPK Automotive [D. Bleicker] presented an update on the development of a new NOx sensor based on a dosimeter principle. In the dosimeter mode, as NOx is adsorbed on a sensitive layer (KMnO4 was chosen as the NOx storage material), it changes its impedance which is measured by interdigital Pt electrodes. The NOx accumulation phase is followed by regeneration. The dosimeter mode requires an operational temperature of 350°C and allows to measure NOx concentrations in the ppb range. The same sensor can be operated in a gas sensor mode—at 650°C, an equilibrium is reached between the adsorption and desorption of NOx, allowing continuous NOx measurement in the ppm concentration range. It was found that the NOx signal depends on lambda (O2), and an O2 sensitive layer was implemented to provide the necessary compensation. Initial bench test results of the sensor prototype were presented.
The Fraunhofer Institute [S. Ziesche] developed a new exhaust mass flow sensor. The sensor is a miniaturized thermal anemometer utilizing ceramic multi-layer technology (ceramic MEMS). It incorporates two heaters to measure forward and back flow (pulsation), and a Pt 1000 temperature sensors for temperature compensation. The concept was validated through engine test bench testing. The new sensor is expected to enter series production at EngineSens Motorsensor GmbH around 2021. The project received financial support from the AMAZING program by the German Ministry of Education and Research (BMBF).