Feature: Liebherr’s SCRFilter Stage V emission system
9 November 2019
The EU Stage V emission standards for nonroad mobile machinery (NRMM) introduced a particle number (PN) emission limit for a number of engine categories that requires the use of diesel particulate filters (DPF) on all affected nonroad engines that complied with the previous Stage IV standards without a DPF. Among the various Stage V emission system configurations, Liebherr pioneered the SCR-on-filter (SCRF) technology—brand named SCRFilter—that can provide an elegant and compact emissions package, highly desired in nonroad engine applications limited by exhaust system space constrains.
The SCRFilter system was developed several years ahead of the Stage V requirements, which have been in effect since the beginning of this year. Liebherr—based in Bulle, Switzerland—has also been supplying engines and equipment for the Swiss construction market, where, under the LRV regulation, particulate filters have been required since 2008. Liebherr supplied first LRV-compliant, Stage IV machines with SCRFilter in 2014. The Stage V version was unveiled at the Bauma trade show in 2016, with sales ramping up this year.
The SCRFilter is the newest addition to Liebherr’s modular emission aftertreatment system, Figure 1, compatible with engines in the D93, D94, D95 and D96 series. The base (Stage 0) engine is equipped with a common rail injection system and an engine control unit, both designed and manufactured by Liebherr. For Stage IIIA applications, the engine is fitted with a cooled EGR system, without any exhaust aftertreatment. For Stage IV and US Tier 4 final, an SCR system is used—referred to as SCROnly—which utilizes a homogeneously extruded vanadium-based catalyst.
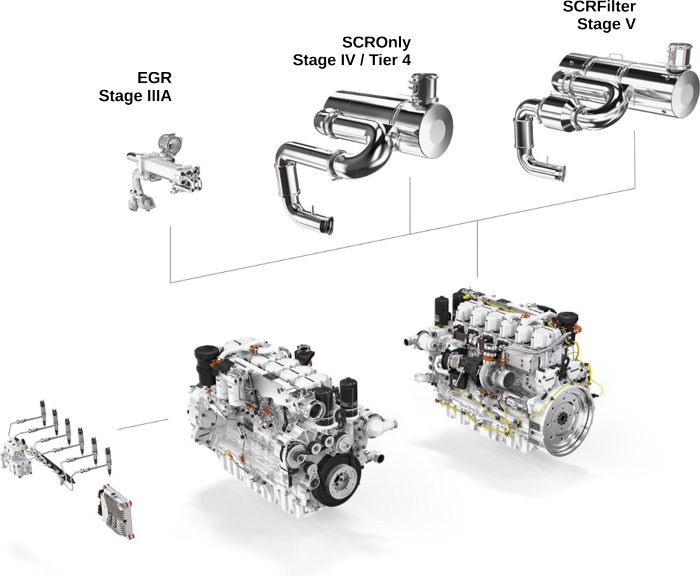
The Stage V SCRFilter package, Figure 2, is based on the SCROnly system. On the outside, the only changes are the piping between the turbine outlet and the SCR converter (where a DOC was added), and a 20% longer housing to accommodate the DPF. The fastening of both aftertreatment systems and the urea (AdBlue) dosing is the same, making it possible to fit the same machine with either the SCRFilter or the SCROnly aftertreatment.
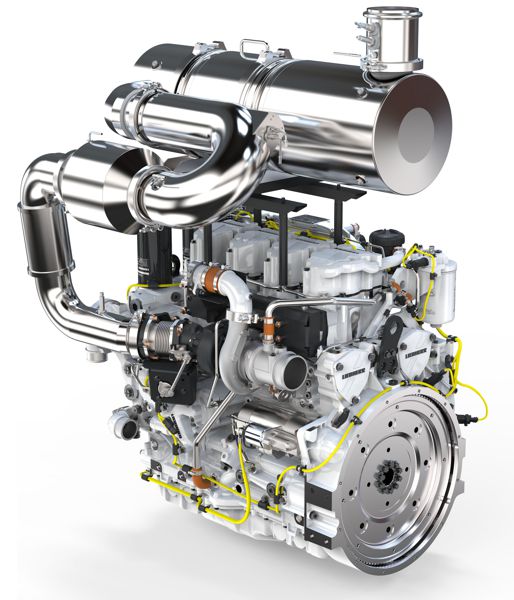
The development targets of the SCRFilter system included compliance with Stage V emission limits (NOx = 0.4 g/kWh, PN = 1×1012 kWh-1); passive DPF regeneration on specific customer cycles and on NRTC; an emissions durability target of 15,000 hours (almost twice the regulatory Stage V requirement of 8,000 hours); and the ability to accept different fuels (US diesel, B10 biodiesel).
The SCR-on-filter technology was chosen due to its potential for the most compact system and the lowest PGM loading. However, several challenges were faced during the development. These include the competition for NO2 from both the SCR process and DPF regeneration, the effect of the SCR catalyst on PM filtration and pressure drop, the impact of ash on the SCR catalyst and NOx reduction, other potential emission durability issues, as well as the possibility of vanadium catalyst sublimation. These effects were studied by Liebherr researchers in cooperation with experts from academia [4520][4519]. Research on fuel quality impacts was supported by the Franco-Swiss OPTI Interreg program.
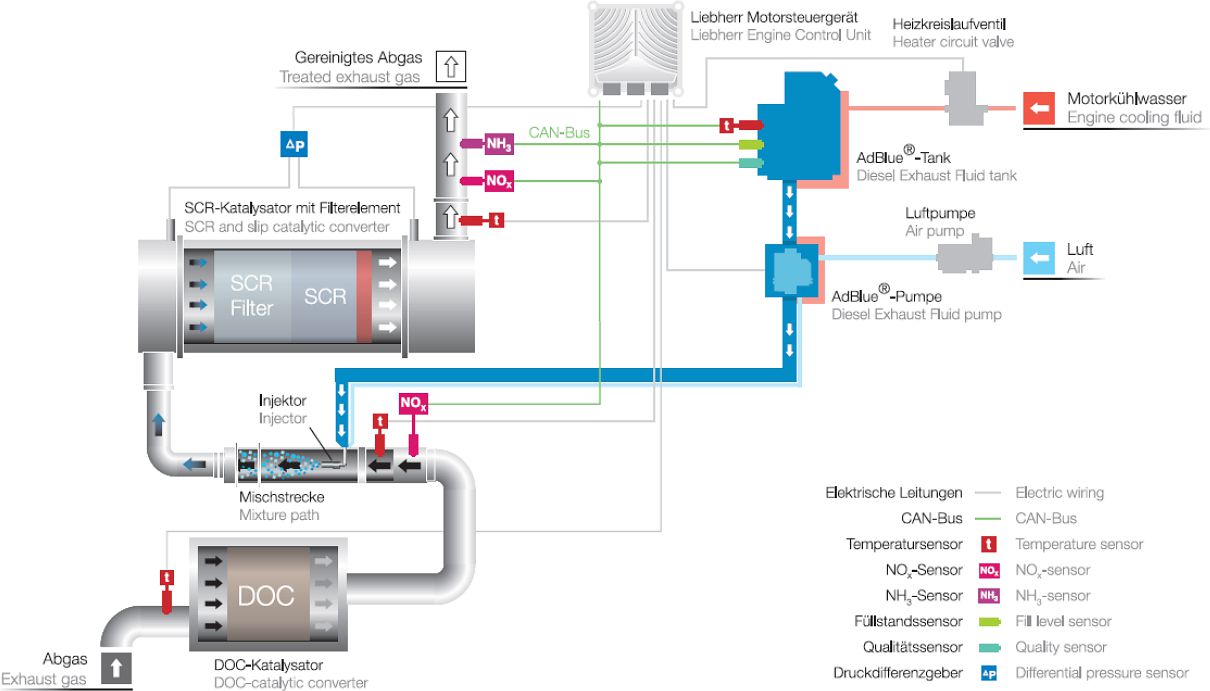
(Source: Liebherr)
The SCRFilter system (Figure 3) includes a Pt/Pd oxidation catalyst, followed by urea injection using an air-assisted dosing system, a wall-flow DPF coated with a vanadium-based SCR catalyst, and a flow-through vanadium SCR catalyst with an ammonia slip catalyst (ASC) coated over the outlet zone. The system provides a high NOx reduction efficiency of 96% (NRTC), which enables engine calibration for high engine-out NOx and low PM. This, in turn, allows for high NO2:PM ratios downstream of the DOC, facilitating passive DPF regeneration—further supported by the vanadium catalyst.
If the exhaust temperature and NO2:PM ratio are sufficiently high, continuous passive regeneration keeps the soot load on the filter low. In situations where normal passive regeneration is not sufficient, thermal management measures are applied, primarily through exhaust gas throttling. In applications characterized by very low load factors—for instance in crane engines—in-cylinder post-injection may also be used. The thermal management system does not utilize exhaust fuel injection.
The filter’s ash cleaning interval is 4,500 working hours. Cleaning can be performed in Liebherr’s own remanufacturing centers.
Liebherr tested several field-aged SCRFilter units, and found satisfactory emission performance for both NOx and PM/PN. To date, about 300 Stage IV systems for the Swiss LRV market and more than 300 Stage V units have been sold. More tests of aged SCRFilter units from the field are planned as Stage V systems accumulate more working hours.
The Liebherr SCRFilter is the first application of SCRF technology on a heavy-duty engine. The technology has also been pursued for Stage V compliance by other manufacturers of nonroad engines. In light-duty engines, SCRF systems were launched around 2012/2013—among the first light-duty SCRF applications was the VW EA288 2.0 liter TDI engine. Until now, there have been no SCRF applications on heavy-duty onroad engines, where space constrains are normally less severe than in the nonroad and light-duty applications.
* * *
Liebherr diesel engines have been specifically developed for off-road applications including construction, agriculture, mining, oil & gas, railway, and maritime. Liebherr’s diesel engine portfolio covers a power range from 130 kW to 4,500 kW, with displacements from 1.75 L/cylinder to 5.17 L/cylinder. The Stage V SCRFilter system is available for engines between 130 kW and 560 kW.
Liebherr gas engines are available in configurations from 4-cylinder inline engines up to 20-cylinder V-engines. Typical applications include power generation using biogas or natural gas.