Conference report: SAE WCX 2020 Digital Summit
29 June 2020
The SAE “World Congress Experience” (WCX 2020) originally scheduled for April 21-23, 2020 in Detroit, MI was canceled due to the Covid-19 situation. Instead, WCX™ Digital Summit was held on June 16-18—a digital, online-only version of the event. The virtual conference included 30 “live” sessions and discussion panels, as well as over 175 pre-recorded, “on demand” presentations covering all areas of automotive technology. The following summary details a number of WCX 2020 papers—most of which, but not all, were presented at the Digital Summit—on engines, engine emissions, and related technologies.
Please log in to view the full version of this article (subscription required).
The stage was set for these topics by Ameya Joshi of Corning, who presented a review of recent regulatory and technical developments in vehicle efficiency and emission control technologies [4782]. The EU 2030 CO2 targets have attracted a lot of attention due to their EV-forcing character, but they also drive advancement in internal combustion engines. A range of new engine technologies under development may enable a 45% BTE in gasoline engines. One of the promising technologies is gasoline compression ignition; a combination of GDCI and mild hybridization may bring a 40% reduction in fuel consumption. In heavy-duty engines, research under the SuperTruck II program appears to be on track to reach 55% BTE in a heavy-duty diesel engine to provide significant fuel savings.
Upcoming new pollutant regulations include the lower NOx standards for heavy-duty engines in California/USA and Euro 7/VII in Europe. In both regulations, the focus is to ensure low emission levels for NOx and other pollutants under all real driving conditions, including slow urban driving. The list of technologies envisioned for meeting the CARB lower NOx standards include thermal management via cylinder deactivation and/or other means, and the addition of a close-coupled SCR system (so-called dual dosing SCR).
A number of regulatory changes are considered in Europe. Even before the Euro 7 stage, the particle number measurement will likely be modified to include smaller particles, down to 10 nm (from the current 23 nm). Changes considered at the Euro 7 stage, which may become effective around 2027, include a low temperature (-7°C) type approval test, modifications to RDE/ISC testing to emphasize urban driving, improved in-use compliance through on-board monitoring (OBM), additional emission limits (NO2, N2O, NH3, HCHO, CH4), as well as some tightening of existing emission limits. With the low temperature test, port fuel injected (PFI) gasoline engines may require gasoline particulate filters (GPF), now used only in GDI engines. PFI engines can produce high PN emissions, especially in hybrid powertrains, due to frequent engine stop-starts. If an NH3 emission limit is adopted, gasoline engines may require a passive SCR catalyst or an ammonia slip catalyst.
High Efficiency Engines
The summit included a number of presentations on high efficiency engine concepts and various approaches to improving engine efficiency. The focus of most of these papers was for light-duty SI engines.
In the opinion of the Southwest Research Institute (SwRI), internal combustion engines (ICEs) are expected to be widely used until 2050 with hybrid applications becoming dominant over ICE-only vehicles, Figure 1 [4768]. Hybridization offers opportunities to further improve ICE efficiency. For example, low speed torque requirements in SI engines are commonly met through compromises such as reduced compression ratio that affect efficiency over the entire engine map. With a hybrid drive powertrain, even 5 kW of crankshaft assist at these low speeds can reduce the low speed torque required from the ICE that can enable the use of a higher compression ratio and allow the turbocharger to be re-optimized. Near rated power conditions, the re-optimized turbocharger can lower residual gas fraction and allow combustion phasing to be advanced and enrichment to be reduced to considerably lower fuel consumption and CO emissions while maintaining rated power and exhaust temperature limits.
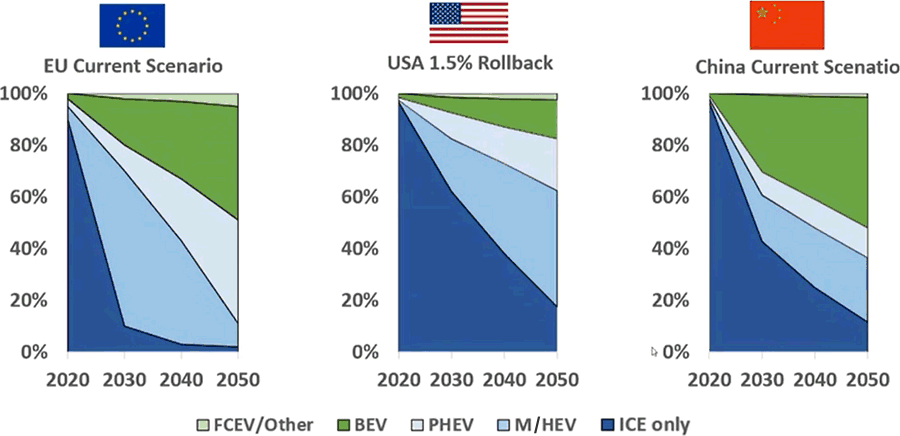
In their paper, SwRI compared this “Hybrid Boost” strategy to a baseline SI ICE-only and a parallel hybrid approach where the electric motor is only used in EV mode at low load with the engine off (Hybrid EV). For an SUV class vehicle, while the Hybrid EV strategy provided fuel economy gains of around 35% over urban-like driving represented by the FTP cycle, on higher loaded cycles such as the US06, these gains largely disappeared. While the Hybrid Boost gains over the FTP were more modest at 10-15%, it was able to provide gains of 5-10% over the US06 cycle. Thus, while the Hybrid EV strategy may be appropriate for vehicles operating under relatively light engine loads such as that experienced by passenger vehicles in urban driving, the Hybrid Boost strategy can provide larger fuel economy gains for highly loaded vehicle operation.
GM is developing a pragmatic engine concept that maximizes efficiency and minimizes pollutant emissions through aggressive downsizing, exhaust energy recovery and a multi-mode combustion system [4769]. The design has 3-cylinders of which two provide power while the third one is used for exhaust compounding, Figure 2. Lean/dilute advanced combustion is used at light and part loads to maximize efficiency while beyond 2000 rpm and/or 10 bar BMEP, conventional stoichiometric boosted operation is used for high power density. Brake thermal efficiency (BTE) of 41.2% @ 2000 rpm and 110 kW/L @ 5500 rpm have been achieved so far. The peak efficiency was obtained over a wide load range relevant for typical drive cycles.
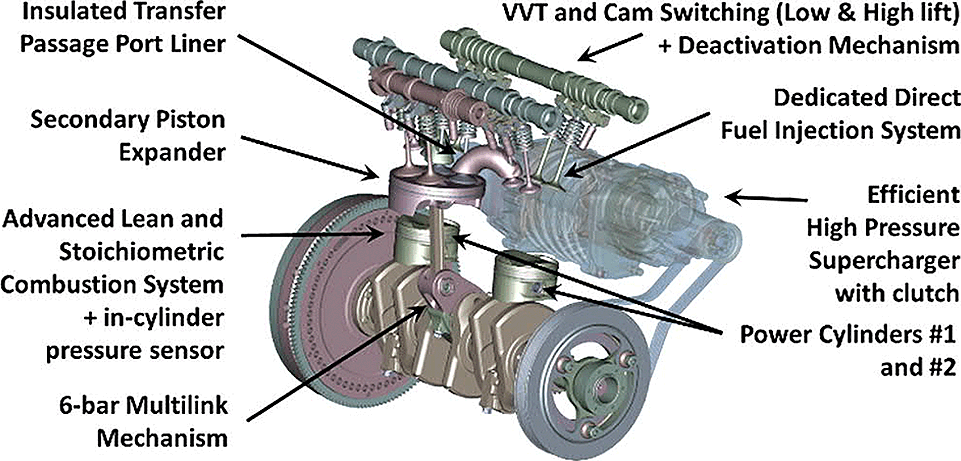
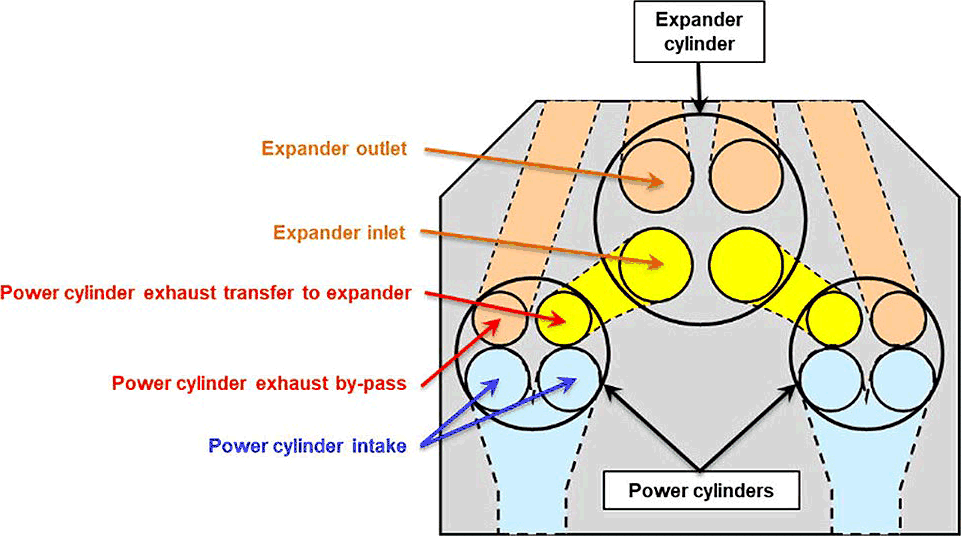
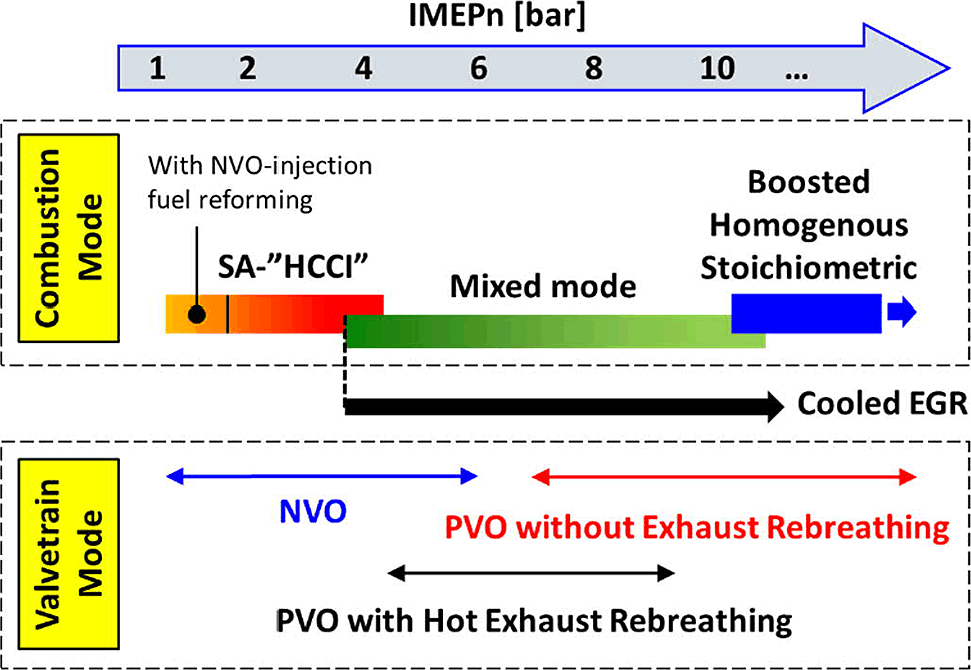
Initial work has focused on the lean/dilute combustion system development and because of the range of loads that must be accommodated, different modes and control strategies are required to ensure low NOx, Figure 2. From about 1-4 bar BMEP, the combustion strategy is based on spark-assisted HCCI (SA-HCCI) using a single injection at the beginning of the intake stroke to create a well mixed nearly homogeneous mixture and constant spark-timing (40°BTDC). At about 4 bar BMEP, this mode becomes knock/stability limited. From about 4-10 bar BMEP, the combustion process is based on a double injection strategy that creates into a quasi-homogeneous background, a richer region that is ignited by the spark-plug (mixed-mode combustion). Combustion of the richer region raises the temperature and pressure in the cylinder and triggers autoignition of the background mixture. Cooled EGR is required to limit NOx in mixed-mode combustion.
For the SA-HCCI mode and the low load region of the mixed-combustion mode, a negative valve overlap (NVO) strategy is used to retain residual gas and provide the high charge temperature required for LTC. Combustion phasing is controlled by varying the NVO duration and in the low load region of mixed mode combustion, spark timing can be varied as well. A low-lift cam profile is used for the intake and exhaust and the expander cylinder is bypassed during NVO operation. At about 5.6 bar BMEP, a lack of air that coincides very closely to the knock/stability limit requires switching to a high-lift, long duration cam profile that leads to a positive valve overlap (PVO). Simultaneously, exhaust from the power cylinders is directed into the expander cylinder. Under these conditions, exhaust re-breathing is used to stabilize combustion. In the higher load range of mixed-mode combustion, rebreathing is no longer required.
While dilute combustion modes use a 13.5 compression ratio, conventional homogeneous SI combustion would be optimized with a 9.0 compression ratio to avoid knock and the engine would benefit from variable compression ratio. Future work will focus on transient operation between the different combustion modes and demonstrating the potential for the engine to be compatible with passive a lean-aftertreatment system (TWC+SCR) that has been discussed previously [4770].
Michigan Technological University and Roth Engine Science summarized simulation results for an example implementation of the true Atkinson Cycle using a multi-link mechanism in a light-duty SI engine [4771]. At light to medium load conditions, the efficiency benefit derives almost exclusively from overexpansion. However, at higher loads, additional benefits arise because spark timing can be better optimized for efficiency while avoiding knock. For example, at 2500 rpm/10 bar IMEP, a net indicated efficiency of 46.7% was estimated with a compression ratio of 10.5 and expansion ratio of 13.0. This compares with 41.9% for a baseline engine with 10.5 compression ratio and 43.0% for an engine with 13.0 compression ratio. At higher loads, a third benefit arises from the ability to meet exhaust temperature limits with little or no enrichment. Using the same parameters as above, the net indicated efficiency with the Atkinson mechanism at 3500 rpm/20 bar IMEP was estimated to be 46.1% compared to 36.2% for the baseline engine. Over the FTP and US06 cycles, fuel economy improvements of 10% and 13% were estimated.
Another overexpansion concept proposed by EcomanIQ uses deactivated cylinders to achieve overexpansion at part load [4772]. At part load conditions where some cylinders can be deactivated, the non-firing cylinders are used to further expand exhaust gas from the firing cylinders. Simulation work with a 4-cylinder SI engine with a maximum torque rating of about 190 Nm suggests that BSFC reductions of over 10% might be possible between 40-100 Nm torque.
Mahle presented two papers on their pre-chamber spark plug, Mahle Jet Ignition (MJI). In one paper using a fuel fed active prechamber, a lean burn light-duty engine fueled with pump grade gasoline was able to achieve a peak BTE of 42% with λ in the 2-14 bar BMEP load range varying between 1.55-1.80 [4773]. In a second paper using a passive prechamber, stoichiometric operation over the entire engine load range was targeted while keeping engine cost increases to a minimum [4774]. The concept used increased compression ratio, Miller cycle valve timing and low pressure EGR, port fuel injection and a variable geometry turbocharger. When optimized as a prime mover, the engine is capable of delivering a peak BMEP of 18 bar from 2000 rpm to 4000 rpm, a peak power rating of 110 kW at 5500 rpm and a minimum BSFC value of 211 g/kWh (39.6 % BTE) with 12.8 compression ratio. When optimized as an engine for a hybrid vehicles using a 14.7 compression ratio, the minimum BSFC value was reduced to 207 g/kWh (40.3% BTE) with the engine operating in a reduced speed range to provide peak power of 80 kW at 4500 rpm and the peak BMEP of 18 bar from 2500 rpm to 4000 rpm. With the hybrid version, a very wide region where BSFC is less than 240 g/kWh was achieved.
A paper by the University of South Australia demonstrated some interesting aspects of exhaust waste heat recovery for a stationary genset [4776]. They carried out some detailed sizing calculations for the WHR system for a 1.1 MW CAT G3516 genset with heat recovery from the exhaust gas and using water as the working fluid. While a 12.2% efficiency improvement was estimated, the WHR required 6 heat exchangers with a total mass of 16t. The mass of the genset is about 12.5 t.
Thermal Management
Thermal management strategies will be critically important for meeting the proposed California lower NOx emission standards for heavy-duty engines. Particularly challenging are the proposed NOx limits over the low load cycle (LLC): 0.2 g/bhp-hr from 2024 and 0.05 g/bhp-hr from 2027. The LLC cycle provides very little enthalpy to the aftertreatment system—in fact, the exhaust produced during low load operation will actively cool down components that were initially warm. Research at the SwRI—conducted as part of the low NOx diesel engine demonstration for California—strongly suggests the NOx emission targets can be met using a dual dosing SCR configuration in combination with cylinder deactivation (CDA) and additional engine measures to ensure rapid engine warming after cold start [4752][4753]. Aftertreatment aging is still on-going and final results should be available later this year.
Tenneco conducted a simulation study of a heavy-duty aftertreatment system, and proposed an alternative thermal management approach to meet the California lower NOx emission standards [4788]. The study introduced the concept of “thermal deficit” of a low-load cycle, which was quantified by adding a constant heating power to the exhaust stream in order to maintain the required SCR temperature. Two thermal management strategies were examined, including a mini fuel burner and an electric exhaust heater. The fuel burner was able to meet the system objectives on the LLC cycle while utilizing an average 7.7 kW (on the Cummins X15 engine rated 373 kW @ 1800 rpm). When the mini-burner was combined with CDA, the fuel consumed by the mini-burner was reduced by 2.5 kW, indicating that there is a synergy associated with the application of both CDA and an exhaust heating device. The electric exhaust heater, even though limited in maximum power relative to the mini-burner, was also able to satisfy the thermal deficit of the LLC cycle. These results suggest that the combination of mini-burner (or an electric heater) and CDA may present a viable alternative to the configuration proposed by the SwRI. Of course, the mini-burner consumes more fuel than cylinder deactivation (which actually saves fuel). However, CDA alone is insufficient during cold start, and the additional engine measures that must be used to heat the aftertreatment system may very well consume more fuel than the mini-burner. In addition to the conventional heavy-duty aftertreatment configuration, the Tenneco study also includes an analysis of a system with dual dosing SCR.
SwRI, the US EPA and Navistar evaluated the effect of CDA over lightly-loaded heavy-duty drive cycles using a 2018 Navistar A26 (13 L) 450 hp diesel engine with the stock aftertreatment system (DOC+DPF+SCR+ASC) and fitted with Jacobs lost motion valve bridge CDA system [4790]. Three cylinders were deactivated using a calibration that was part of some initial performance development activity for the SuperTruck II program. Test cycles included the LLC and various constituents of the LLC. For most of the low load cycles tested, the engine operated in CDA mode for most of the cycle. The results presented were for warmed-up engine operation—i.e., no cold start results. For most cycles, the increase in average SCR inlet temperature ranged from 24-38°C resulting in tailpipe NOx reductions of up to about 80% and CO2 reductions up to 15%. The highest NOx and CO2 reductions tended to be found for the cycles that operated at the lowest loads. Challenges with CDA include: delayed torque response, insufficient EGR flow at low load and increases in NVH below 1000 rpm. For the heavy-duty systems being developed, CDA is unable to significantly accelerate aftertreatment system warm-up after a cold start and more conventional strategies that also consume significant amounts of fuel may still be required for this task.
Tula Technologies demonstrated that catalyst light-off can be accelerated in SI engines with their Dynamic Skip Fire (DSF) approach [4789]. Using a light duty 4-cylinder SI engine (1.8 L VW EA888 Gen 3) equipped with Delphi Deactivating Roller Finger Followers (DRFF), a close coupled TWC and an underfloor TWC, DSF was shown to have the ability to increase exhaust gas temperature at the catalyst inlet by up to 100°C and the exhaust enthalpy by up to 20% within a few seconds after engine start. Cold start tailpipe carbon monoxide (CO) and hydrocarbon (HC) emissions were reduced by 10% to 20% largely due to the increased exhaust gas temperature and enthalpy. DSF increases the load on the firing cylinders and allows more combustion phasing retard before combustion instability becomes too high. The higher cylinder load also allows intake cam phasing to be advanced to increase residual fraction and provide some emission benefits without degrading combustion stability. Dynamic air pumping (2 firing cylinders fueled rich and 1 deactivated cylinder used as an air pump to provide a lean exhaust AFR) can increase exhaust gas temperature by an additional 30°C and nearly double the enthalpy delivered to the catalyst to reduce cold start HC emissions by more than 50%.
Emission Control
Umicore presented a study on GPF design for China 6b and Euro 7 applications [4780]. A system composed of a close-coupled TWC that was closely followed by a catalyzed GPF was chosen, and optimized for catalyst volumes and PGM loadings. All of the tested, aged configurations could comfortably meet the relevant PN as well as HC emission limits. However, meeting the China 6b NOx and CO limits required a sufficient amount of OSC/washcoat, which required a relatively large TWC volume; a 1 L TWC was found to be necessary on a 1.6 L GTDI engine. Bigger TWC volume (i.e., more washcoat) was more effective in reducing emissions than higher PGM loading—an agreeable finding, considering the high prices of precious metals.
An interesting case study by Cummins evaluated the catalytic performance of a sulfur-poisoned Cu-SSZ-13 SCR catalyst that had been exposed to high sulfur diesel fuel [4783]. The sulfur-poisoned SCR catalysts showed a substantial deterioration of NOx conversion below 350°C. Temperature programmed desorption (TPD), BET surface area and thermo-gravimetric analysis (TGA) were applied to analyze the poisoned SCR catalyst. It was found that both physical poisoning by ammonium bisulfate (ABS) and chemical poisoning (Cu-S species) contributed to the reduced NOx conversion. Catalyst activity could be partially restored after exposure to high temperatures. ABS became decomposed in the ~350-500°C temperature range, while the release of sulfur from the Cu-S species required temperatures above 500°C, and as high as 660°C for the most strongly bound Cu-S compounds. After exposing the poisoned catalyst to 550°C for 1 hour, 52% of the NOx reactivity could be restored.
Industrial Power Alliance and the University of Michigan investigated EGR cooler deposits from non-road diesel fueled equipment [4786]. Industrial Power Alliance supplies EGR coolers for Komatsu non-road engines. The EGR coolers from construction vehicles that had accumulated over 10,000h of operation were removed and analyzed. They discovered that the density of the field aged deposit samples was over 5 times higher when compared to typical samples generated on an engine bench and that the mass and density of deposits at the outlet end of the cooler was greater than at the inlet side. In most cases, the outlet deposits contained a higher proportion of volatiles.