Conference report: 2020 CLEERS Virtual Workshop
22 September 2020
The 2020 CLEERS Workshop was held as a virtual event on September 14-18, 2020. CLEERS (Crosscut Lean Exhaust Emissions Reduction Simulations) is an initiative by the US Department of Energy (DOE) to support the development of computer simulation tools for use in the design, calibration, and control of next generation engine emission control systems. This years’ event included 24 technical presentations via the Zoom platform, as well as several invited talks, a panel discussion, and a number of posters. The topics covered all types of automotive emission control catalysts, with focus on low-temperature catalyst activity, particle filters, SCR, and passive NOx adsorbers (PNA).
Please log in to view the full version of this article (subscription required).
Catalyst Light-off and PGM Utilization. Much of the basic research in emission control catalysts has been focused on lowering the catalyst light-off temperature—to address the challenges of low exhaust temperatures in high efficiency engines or during start-stop cycles in hybrids—and on better utilization of platinum group metals (PGM). A low light-off target known as the “DOE 150°C challenge” calls for a 90% conversion of NOx/CO/HC by 150°C. The PGM utilization objective reflects the growing concern with PGM resource constraints, particularly in the case of palladium and rhodium.
“Single atom catalyst” technology has a potential to address both of these challenges in automotive catalysts [A. Datye, University of New Mexico]. Single atom catalysts are finely dispersed on the support, either in atomic form or as very small, sub-nanometer clusters. These finely dispersed catalysts can be formed using the atom trapping method, where the PGM component is deposited from vapor phase at high temperature (~800°C). Many PGM as well as base metals have vapor pressures that are sufficiently high to allow this approach. Ceria has been identified as a suitable support that can stabilize many single atom catalysts. In case of Pt, vapor phase PtO2 reacts with Ce3+ to form Pt-O-Ce linkages on the surface of the Ce sites. Fixing the PGM catalyst or other transition metals on the surface can also stabilize and increase the surface area of ceria, Figure 1. T90 light-off temperatures for CO of less than 100°C were achieved with Pt1/CeO2 catalysts, but many challenges remain. Importantly, Pt must be in the metallic state to achieve high activity. As Pt oxidizes at high temperature (~600°C) to a less active oxide form, a periodic reactivation through reduction of the Pt oxides may be required.
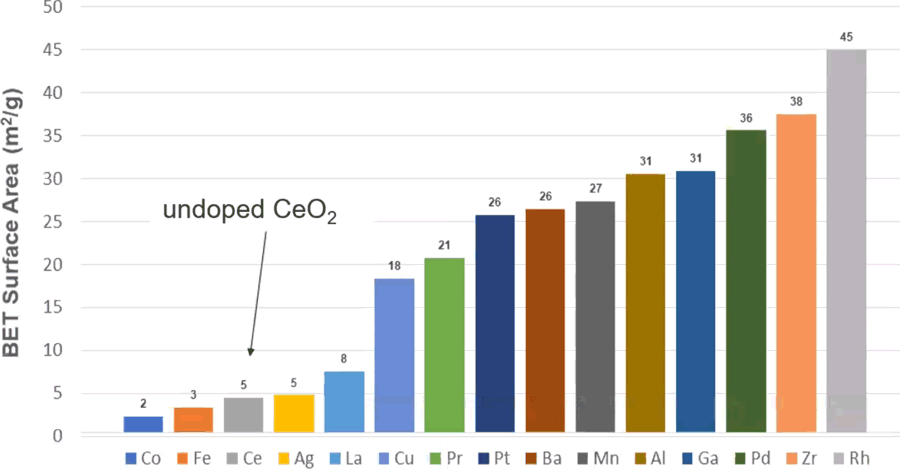
The Pacific Northwest National Laboratory (PNNL) [K. Khivantsev] studied the activity of a 0.5 wt% and 0.1 wt% Rh1/CeO2 catalyst prepared via atom trapping for the NO+CO reaction. According to preliminary results, the catalyst showed NO removal activity already at ~50°C, and was also active in the presence of water. However, NH3 was formed when water was present (with the water shift reaction as the source of H2). At low temperatures, the catalyst was reducing NO to N2O; its selectivity toward N2 increased above 100°C.
In another talk, PNNL [Y. Wang] discussed their atomically dispersed Cu/CeO2 catalyst, synthesized via atom trapping. At 2 wt% Cu/CeO2, the catalyst was highly active for low temperature CO oxidation, was stable (with H2O), and tolerant to sulfur.
University of Michigan [A. Hill] presented another approach to develop highly active and durable catalysts by controlling the catalyst morphology. Palladium ‘cores’ were placed inside of ceria ‘shells’, to isolate the Pd sites and prevent sintering. This Pd@CeO2 was compared with a conventional, surface impregnated Pd/CeO2 catalyst. After exposure to high temperatures, the core@shell catalyst showed a further redispersion of Pd and improved activity, Figure 2, while the conventional catalyst sintered and lost activity. The high activity of this redispersed Pd catalyst—meeting the 150°C light-off target after a number of 800°C aging cycles—could be sustained over a range of operating conditions.
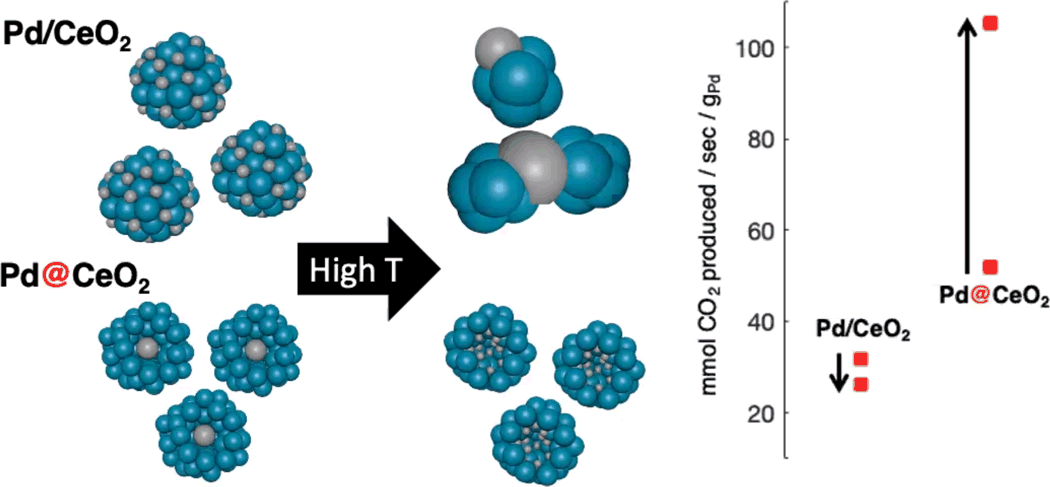
A panel discussion on PGM utilization covered two upcoming DOE-funded research programs, to be led by the University of Virginia [W. Epling] and by Washington State University [Y. Wang], which will be developing highly dispersed catalysts with an objective to reduce PGM use in the US vehicle fleet by 50%. Representatives from the catalyst industry shared their concerns about PGM supply. Both Pd and Rh have been in deficit for several years (with the exception of the Covid-19 period) and will remain so in the coming years, according to an analysis by BASF [S. Alerasool]. The rapidly increasing palladium prices have been driving a major effort to replace Pd with Pt. However, technical challenges remain, as Pt is less durable than Pd under hot oxidizing condition. For rhodium, there is no known replacement. Catalyst makers have been reducing the loadings of Pd and Rh through improved catalyst technology (e.g., stabilization by dopants) in combination with engine calibration (rich events must be short in order to bring Rh back to the active metal state). Since 2018, Umicore [W. Mueller] reduced PGM loadings by 69% for Pd and by 53% for Rh in the 1.0-1.6 L vehicle class.
Particulate Filters. A number of presentations discussed particle filters for gasoline (GPF) and diesel (DPF) applications. NGK [M. Taylor] talked about GPF system development for China 6b (2023) applications with RDE testing requirements. Four GPF formulations were tested at locations throughout China. The GPF unit replaced the original, close-coupled three-way catalyst (TWC) and was followed by an underfloor TWC. The newest, Gen 2 GPF (8 mil/200 cpsi, low pore size, low porosity) could meet the PN standard of 6×1011 1/km with the current conformity factor of 2.1. The impacts of both temperature and altitude were found to be marginal (even though China 6b extends the altitude requirements from 1300 to 2400 m). Aggressive driving has potentially the biggest impact during RDE testing, with some tested GPFs failing the PN limit.
A simple but insightful analysis of GPF filtration efficiency was presented by Ford [X. Liu]. Two filtration models were used, including the unit collector model and the capillary tube model, to analyze the relationship between GPF material parameters and performance. It was shown that narrower pore size distribution, smaller pore sizes, and higher porosity all increase filtration efficiency. Interesting results were shown on the effect of catalyst coating. In-wall coating (washcoat within the wall porosity) reduces efficiency and increases pressure drop, just like reduced porosity. On-wall coating on the other hand increases the wall thickness (filtration path) and thus increases filtration efficiency, as well as the pressure drop. A highly porous top layer of artificial ash can boost efficiency at a lower pressure drop penalty.
In a study on particulate filter ash presented by MIT [C. Kemp], a number of analytical tools were used to investigate ash hydration in field-returned particle filters (DPF and GPF). CaSO4, commonly found in lubricant-derived ash, has a high ability to form hydrated species, such as CaSO4 × 2H2O (gypsum). Hydrated ash can form large crystalline features up to 100-300 μm. In some field filters, as much as 50% of ash was found to be hydrated. While hydrates release water on heating, some hydrated Ca species can remain stable up to 900°C. These hydrated ash particles can increase the risk of ash collapsing in the filter channels and affect ash transport and accumulation mechanisms. Due to their lower density, they take up more volume in the particle filter than anhydrous ash, thus affecting the DPF/GPF performance, especially in applications with higher exhaust or ambient humidity levels.
Exothermia [G. Koltsakis] has upgraded their aftertreatment models to better account for the accumulation and transport of ash and soot within particle filters. A model was developed to account for soot layer detachment, thermally induced ash agglomeration, and ash layer detachment. The model was calibrated using a burner test rig, and applied in transient engine data. Further research topics were identified with respect to the ash fate in the wall pores, plug ash density as a function of the agglomerate size, and stochastic ash bridging in filter channels.
Cummins [Y. Wang] developed a DPF filtration model that accounts for realistic pore size distribution of the filer material. Cummins researchers found that classical filtration models predict filtration efficiencies that are much higher than experimental data, because the DPF pore size distribution is ignored and uniform cells are assumed. In the new model, a discrete framework was developed using over 50 grids to describe pore size distribution. The model was validated with experimental and literature data.
SCR Technology. Copper-substituted zeolites have been used as commercial SCR catalysts for diesel engines since at least 2010, but the mechanisms of the catalytic reactions are still not fully understood. In the widely used catalysts utilizing chabazite type zeolites (Cu-CHA), there are at least two different Cu active sites: ZCu2+OH bonded to one Al atom of the CHA framework, and Z2Cu2+ bonded to two Al atoms. A number of talks covered recent research on this SCR catalyst system. Two studies by Politecnico di Milano looked into the Cu2+/Cu+ redox mechanisms during the standard SCR reaction [A. Tronconi], and into hydrothermal aging effects on Cu speciation [U. Iacobone]. Researchers at PNNL [F. Gao] employed electron paramagnetic resonance (EPR) spectroscopy to probe the reactivity and relocation of Cu2+ sites. Cummins [S. Joshi] applied kinetic models of the NH3-SCR redox cycle to quantify active Cu sites and aging of the Cu-CHA catalyst.
John Deere [D. Dou] discussed the integration of SCR with other aftertreatment components and the diesel engine, illustrated by the comany’s nonroad engine architectures to meet US Tier 4 and EU Stage V emissions. The company developed a library of models which are used for system simulation to meet given design targets. Simulation tools helped in system optimization and downsizing. However, simulation alone cannot predict unforeseen failure modes. For instance, the SAPO-34 zeolite used in some Tier 4 SCR systems proved to be prone to low temperature degradation (leading to engine recalls), while in certain configurations that utilize SCR-coated particulate filters (SCRF), Pt migration to the SCRF components may occur, contributing to a rapid deterioration of SCR activity. John Deere Stage V emission system includes a DOC, an uncatalyzed DPF, an SCR catalyst and an ammonia slip catalyst (ASC). EGR continues to be used to help reduce NOx at low exhaust temperatures. Reduced mass of exhaust piping helped to improve pollutant conversion over cold start NRTC test.
The Karlsruhe Institute of Technology (KIT) [D. Zengel] investigated the impact of formaldehyde (HCHO) on SCR catalysts (Fe-ZSM-5, Fe-BEA, V2O5-WO3/TiO2, Cu-SSZ-13) in natural gas applications. In general, HCHO conversion increased and NOx conversion decreased when HCHO was present. At the same time, an overconsumption of NH3 was observed (about 10% higher compared to NOx conversion), which was found to react with HCHO and lead to the emission of HCN. Of particular concern is the observation that more than 50% of HCHO may be converted to HCN. A mechanism for HCN formation was proposed.