Conference report: SAE WCX 2019 Congress
29 April 2019
The SAE “World Congress Experience” (WCX 2019) was held April 9-11, 2019 in Detroit, MI. The Congress included several keynote and panel discussions, a number of technical sessions, as well as an exhibition. The technical program included 933 technical papers and some oral-only presentations covering all areas of automotive technology—including a number of papers on engines, engine efficiency and emission control technology.
Please log in to view the full version of this article (subscription required).
Regulatory Trends
Technical sessions on engine and emission technologies were opened with a review of recent regulatory and technical developments in vehicle efficiency and emissions presented by Ameya Joshi of Corning [4160]. This was the first year this review—presented by Tim Johnson for a number of years—was delivered entirely by Dr. Joshi. In light-duty vehicles, the upcoming regulatory challenges include EU CO2 standards that mandate a 37.5% emission reduction by 2030, along with electrification mandates. European Real Driving Emissions (RDE) testing requirements have been in effect for more than one year; first emission data from RDE-type approved vehicles suggests that both gasoline and diesel vehicles exceed the respectable emission standards. In China, gasoline particulate filters (GPF) are being deployed to meet China 6 particle number (PN) emission limits. The Chinese PN limits apply not only to GDI vehicles as is the case in Europe, but to all types of engines; some PFI vehicles and hybrids will likely adopt GPFs as well.
Among important developments in heavy-duty engines, the EU has established its first-ever CO2 standards for trucks that will require a 30% emission reduction by 2030. In the US, California is leading the development of low-NOx emission standards with a focus on reduced in-use emission from heavy-duty engines. Worldwide, more jurisdictions are adopting DPF-forcing emission standards that include PN emission limits; examples include Brazil’s PROCONVE P8 and China Stage IV regulations for nonroad engines.
Regulatory developments in China arguably attract the most attention; they were covered in a separate talk [4161]. China 6 standards are the most stringent emission standards in the world. They include not only a more stringent NOx limit than Euro 6 (China 6b NOx=0.035 g/km; EU 6 NOx = 0.06 g/km for gasoline, 0.08 g/km for diesel), but also higher altitude requirements (2400 m) and a PN limit of 6x011 #/km applicable to all gasoline and diesel vehicles. Nonroad engines, according to the recently published revisions to the Stage IV proposal, would have to meet a number of new requirements, including a PN emission limit of 5x1012 #/kWh for 37-560 kW engines; wider ambient boundary conditions; OBD for NOx and PM controls, covering EGR, DOC, DPF, SCR; GPS for all nonroad machinery with engines of 37-560 kW; as well as PEMS testing requirements with a focus on in-use emissions. The China Stage IV standards are expected to become effective from December 2020.
NOx Aftertreatment
SwRI provided an update on work evaluating the potential of heavy-duty diesel engines to meet a 0.02 g/bhp-hr NOx limit [4140]. The second phase of this work started about a year ago to address some challenges encountered in the first phase of the program; namely an aftertreatment system damaged during full useful life (FUL) aging and testing on an engine that may be more representative of what will be available in the U.S. post 2020. A repeat of the FUL aging (Stage 1b) is intended to demonstrate the potential of the passive NOx adsorber (PNA) system/mini-burner used in the first phase of the program. The FUL aging for Stage 1b has been completed on the 2014 Volvo MD13TC Euro VI engine but final emission results were still being evaluated. However, the NOx results at 67% FUL were 0.017 g/bhp-hr on the composite FTP and 0.027 g/bhp-hr on the RMC-SET cycles. It was noted that the NOx storage capacity of the PNA decreased with time and accounted for a significant part of the NOx emissions increase during FUL aging. On a related note, laboratory tests at Oak Ridge showed that NOx adsorbers utilizing the Pd/SSZ-13 system require relatively long periods of high temperature regeneration—on the order of 4 hrs at 600°C—to completely release the stored NO [4141].
Another aspect of the SwRI program (Stage 2) is to develop a Low Load Cycle (LLC). This phase has been completed and the final cycle represents heavy-duty vehicles used in food service, drayage, parcel delivery and transfer truck operations. The cycle is intended to be run with a warmed-up engine after a short hot-soak. Testing of a number of production engines over the LLC yielded NOx emissions from 0.8-1.5 g/bhp-hr. Using the Stage 1b Volvo engine, tailpipe NOx emissions were 0.26 g/bhp-hr before the calibration had been finalized.
Stage 3 of the SwRI program is based on a 2017 Cummins X15 engine. The engine has been fitted with cylinder deactivation (CDA) and an EGR cooler bypass for the final evaluations. Other hardware that had been evaluated but not selected included a double walled exhaust manifold, SuperTurbo with turbine bypass, turbine bypass and CAC bypass. For the cold start FTP, a modified cold start strategy is required to achieve 0.02 g/bhp-hr NOx. This strategy, which included elevated idle speed combined with EGR, VGT and multiple injections, was able to significantly increase turbine outlet temperature and shorten the time required to reach 180°C to about 35 s. On the cold start FTP, CDA was able to ensure the temperature stayed above 180°C and also resulted in a smaller CO2 penalty (+1.3%) than would have been the case using the modified cold start strategy only (+4.0%). During the LLC, CDA will reduce the amount of time that the engine operates in thermal management mode and should lead to a CO2 benefit compared to the baseline engine strategy. The next steps will involve evaluating aftertreatment configurations, four of which are shown in Figure 1. Dual dosing SCR systems with a close-coupled SCR catalyst will be the primary aftertreatment systems considered.
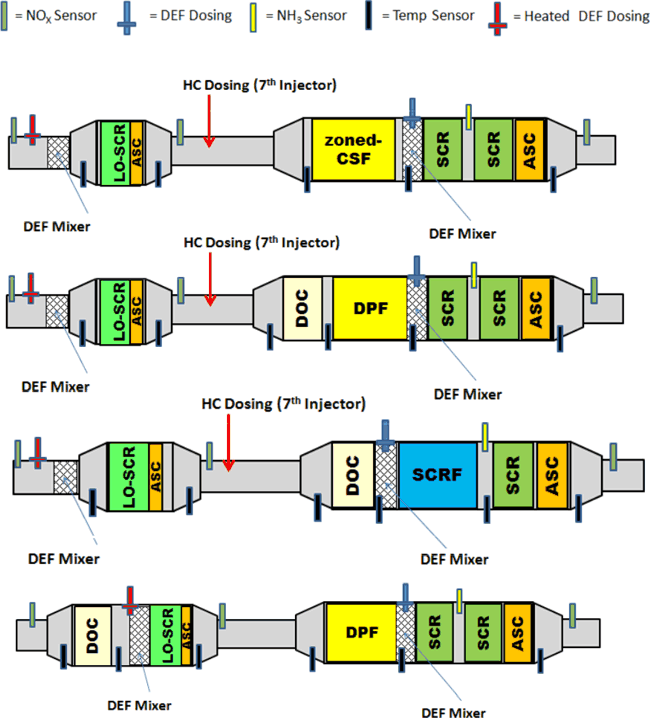
SCR Systems. Tenneco and IAV studied the placement and operation of a close-coupled SCR (ccSCR) catalyst in a dual dosing SCR system using 1D modeling. Based on a Euro VI-compliant engine equipped with series turbochargers, a location downstream of the low-pressure turbine offers the potential for good cold start NOx conversion while minimizing packaging complications. The other locations considered (between the turbines or in a bypass line around the high pressure turbine) offered higher temperatures but the potential for NOx reduction benefit was not sufficient to warrant further consideration. They then went on to examine the performance of a Cu/zeolite ccSCR catalyst placed upstream of a DOC/DPF/SCR system. Dosing for the ccSCR studied needs to be quite aggressive once exhaust temperature reaches 200°C to achieve significant NOx conversion via the standard SCR reaction (2NO + 2NH3 + 0.5O2 → 2N2 + 3H2O). Targeting the control to the amount of NH3 stored on the SCR catalyst is one option to achieve this aggressive dosing while simpler control approaches such as maintaining a fixed ammonia NOx ratio (ANR) provide very little cold start conversion due the reliance on the fast SCR reaction and low concentrations of NO2 (NO2 + NO + 2NH3 → 2N2 + 3H2O). The data showed that optimization of the ccSCR catalyst could potentially provide NOx conversion of 70% or higher over the first 300 s of a cold start FTP while minimizing NH3 slip [4142].
Tenneco and IAV also evaluated several control strategies capable of increasing the exhaust enthalpy and decreasing the engine-out NOx over the initial portion of the cold start FTP cycle; a critical component for meeting a 0.02 g/bhp-hr NOx limit. These were: (1) conventional thermal management measures (intake throttle, exhaust throttle, retarded start of main fuel injection, etc.), (2) VVA-based thermal management (Miller timing and early exhaust valve opening), (3) air gap manifold (AGM) and (4) internal and external turbine bypass strategies combined with the AGM. Some of these results are summarized in Table 1. No single conventional exhaust thermal management (ETM) measure was optimal for all operating conditions and a combination of measures is required. The study picked one example combining injection timing retard and intake and exhaust throttles. Use of ETM results in a significant increase in fuel consumption. An air-gap manifold (AGM) provides ~30°C increase in temperature over the first 300 s of the cold FTP with no additional fuel consumption and could be combined with less severe ETM measures (AGM+ mod. ETM) to achieve a given increase in exhaust temperature to keep exhaust temperature above 200°C over the first 300s of a cold start FTP but with a reduced fuel penalty. Turbine bypass concepts were not very effective primarily because the bypass flow rate must be limited during the early loaded periods of the FTP in order to meet the torque demand of the test [4170].
Baseline | ETM | AGM+ETM | AGM+ mod. ETM | |
---|---|---|---|---|
Fuel consumption, g | 700 | 826 (+18%) | 828 (+18%) | 788 (+13%) |
Exh. temp. increase, °C | - | +84 | +109 | +84 |
Cum. exhaust enthalpy, kJ | 4247 | 6777 (+60%) | 7667 (+81%) | 6836 (+61%) |
Cum. NOx, g | 16.4 | 5.0 | 5.0 | 6.0 |
SCR-on-Filter. While close-coupled SCR seems increasingly accepted as the technology of choice for future low-NOx heavy-duty on-road diesel engines, SCR-on-filter (SCRF or SDPF) remains an attractive aftertreatment option for light-duty vehicles and, potentially, for nonroad engines. One of the challenges with SCRF technology is the thermal durability of the SCR catalyst, which may be exposed to high temperatures during filter regeneration. Hyundai [4164] reported on the development of ultra-stable Cu-Z SCR catalyst using LTA zeolite. The Cu/LTA formulation was compared with a commercial Cu/SSZ-13 (chabazite) SCR catalyst. After 12 hours of hydrothermal aging at 900°C, the SCR performance of Cu/LTA was higher than that of Cu/SSZ-13. The Cu/LTA catalyst also maintained remarkable high-temperature NOx conversion after lean/rich cyclic aging at 620°C, due to its lower oxidation of NH3 to NO. However, the low temperature activity of Cu/LTA required high levels of NO2. A dual brick configuration, Cu/SSZ-13 + Cu/LTA, could provide improved low temperature performance.
Another challenge with SCRF technology is the competition for NO2 between soot oxidation (passive DPF regeneration) and SCR reactions. A PGM catalyst cannot be used to recycle NO2 in the filter via NO oxidation, because it would also oxidize NH3, causing a severe NOx conversion penalty. A team from Paccar reported on the development of a catalyst formulation that would enable NO2 recycling in the SCRF [4162], based on a binary hybrid catalyst concept by PNNL. The catalyst includes two phases: a selective catalytic oxidation (SCO) phase that promotes the oxidation of NO, and an SCR phase. The SCO catalyst utilized ZrO2 doped with elements like Mn and Cu to increase its oxidation activity. The SCR phase was Cu/SSZ-13. Comparative testing with a commercial SCR catalyst showed soot light-off at lower temperatures, but some NH3 oxidation occurred, with a penalty in NOx conversion.
Researchers from John Deere [4163] reported on the degradation of NOx performance in aftertreatment systems containing a DOC and an SCRF or uncatalyzed DPF downstream of the urea injection point. Among the three configurations shown in Figure 2, systems AT-2 and AT-3 experienced severe degradation of NOx performance, while configuration AT-1 did not show degradation.
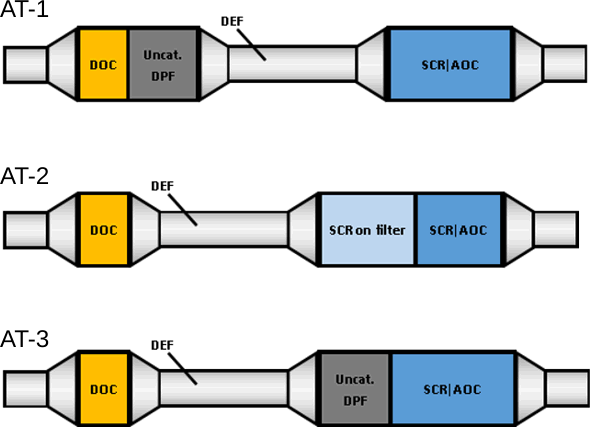
The loss of NOx performance was explained by the migration of Pt from the DOC, via washcoat attrition, and its deposition within the SCRF (AT-2) or DPF (AT-3). The Pt/alumina particles collected in the filter catalyzed the oxidation of ammonia, causing the deterioration in NOx performance. The most severe NOx degradation was observed at high temperatures, such as operating near rated power (this may explain why the phenomenon has not been reported in light-duty SCRF applications). The deactivation of a flow-through SCR catalyst by Pt evaporating from an upstream DOC at high temperatures has been known for a number of years [4174]. However, in that case Pt deposits and deactivation were mostly limited to a short zone at the SCR inlet; in the case of SCRF/DPF contamination by DOC washcoat, the effect is much more severe.
Gasoline Particulate Filters
A number of papers discussed various aspects of GPF technology, ranging from GPF materials through system configuration and GPF regeneration. An important driver of further development of GPF materials is European RDE testing, which may require filters with increased PN filtration efficiency to achieve zero mileage GPF efficiency above 80%. NGK [4168] suggested that for uncoated filters, some increase in porosity combined with a smaller mean pore size (MPS) and a small decrease in open frontal area could provide the required increase in filtration efficiency without significantly increasing pressure drop or reducing material strength. A configuration of 8 mil wall thickness and 200 cpsi was selected, with higher porosity and lower MPS than current GPF technology. For coated filters, the approach is to reduce the volume of larger pores (> 40 µm) while keeping mean pore size relatively unchanged compared to current GPF technology. The chosen configuration was 300 cpsi with high porosity, reduced larger pore volume and moderate decrease in MPS compared to current GPF technology.
An alternative approach to increase the efficiency of fresh filters could be to pre-load them with ash. A study by Ford [4167] found that a GPF loaded with a small amount of thermally stable submicron alumina particles (“artificial ash”) was able to achieve ~90% PN filtration efficiency with only a small increase in pressure drop.
BASF discussed three potential configurations of TWC-coated GPF (trademarked as FWC) for China 6 applications, which are shown in Table 2. In working with customers, they have observed some shift away from the underfloor location to a close coupled position immediately after the TWC. A single FWC has not been common and is unlikely to be used for China 6 [4152].
Configuration | Advantages | Disadvantages |
---|---|---|
![]() | Lower thermal stress Saves space in engine compartment Less catalyst required Lower back pressure | Soot regeneration more challenging |
![]() | Soot regeneration less challenging | Requires space in engine compartment Increased thermal stress More catalyst required Higher back pressure |
![]() | Soot regeneration least challenging | Very high catalyst loading Highest back pressure Light-off activity of TWC poorer due to lower cell density. |
Another GPF paper by Ford discussed GPF regeneration strategies [4138]. The two most important actuators for active GPF regeneration are spark retardation and air-to-fuel ratio modulation. Using these strategies, regeneration could be achieved over challenging drive cycles: stop and go below 30 mph, and steady-state below 40 mph.
Other noteworthy GPF papers included a study by Corning that examined maximum filter temperatures after fuel cut induced regeneration [4155], and research led by the University of Michigan that characterized the reactivity and other properties of soot collected under three sets of conditions, including early and late start of injection (SOI), and with a low injection pressure [4154].
Diesel Particulate Filters
A new theme in the sessions on diesel particulate filter technology was the integration of DOC and DPF components. In most DPF systems, a separate DOC is positioned upstream of a (catalyzed or not) DPF. If these two devices could be integrated into one catalyzed DPF, the size of the aftertreatment system could be reduced. The main driver of this approach is the nonroad machinery sector, where large volume aftertreatment systems often present serious packaging challenges.
Papers on DOC/DPF integration were presented by the major catalyst suppliers: Johnson Matthey [4159], Umicore [4156], and BASF [4157]. The three studies reached generally similar conclusions: the integrated catalyzed DPF (CDPF) performs well under passive regeneration, with uniform (no-zone) high Pt:Pd coating providing best regeneration performance. In active regeneration, on the other hand, the integrated DPF configuration shows a certain disadvantage, due to the lower inlet temperature and lower activity in the DPF inlet zone, resulting in a less complete regeneration. The best performance was achieved with high Pt loads in the front zone of the DPF. Hence, the integrated DOC/DPF configuration is most suitable for applications that rely mostly on passive DPF regeneration. The work by Johnson Matthey also included a system simulation over the WHTC test, while BASF tested a complete emission system (zoned CDPF+SCR+SCR/Amox) over the nonroad NRTC and the onroad FTP test cycles. These results suggest that the integrated DOC/DPF architecture may be also applicable to some categories of onroad engines.
High Efficiency IC Engines
High efficiency engines received coverage not only in a dedicated session that lasted the entire 3 days of the conference but also in other sessions. This coverage spanned a range of fuels including diesel, gasoline and natural gas.
Delphi updated progress on their GDCI engine. The latest Gen 3X version of the engine features a 17:1 compression ratio, GDCI-Diffusion Combustion Strategy for high load, a single stage variable nozzle turbocharger (no supercharger), simplified thermal management with fast air-blend temperature control and a 2-step valvetrain for rebreathing, Figure 3. A fast intake air heater for cold starts was carried over from the Gen 3 engine. As with previous versions, the engine is unthrottled and operates lean with EGR with no spark plug. Targets for peak output and peak cylinder pressure remain at 25 bar MEP and 200 bar respectively while the BSFC target has been lowered to 193 g/kWh. The aftertreatment and EGR systems are identical to those used in the Gen 3 engine. Dynamometer tests demonstrated a minimum BSFC of 194 g/kWh (BTE 43%) at 1750 rpm/12bar IMEP with BSFC less than 210 (40% BTE) over a very wide operating region. The GDCI engine operates on US pump gasoline (RON 91). Simulations suggested that 48% BTE could potentially be achieved through the use of thermal barrier coatings and other improvements to the engine that could be used in a Gen4X engine. Vehicle simulations at Argonne using the Gen3X engine map predicted a 36 to 51% improvement in combined FTP fuel economy for several vehicles (a midsize sedan, SUVs, and a pickup truck) compared to a 2015 1.6L turbocharged GDI engine equipped with intake variable valve lift. Thus, the Gen3X engine with 12V start/stop or mild hybridization could be competitive with full hybrid powertrains in these vehicle segments [4147].
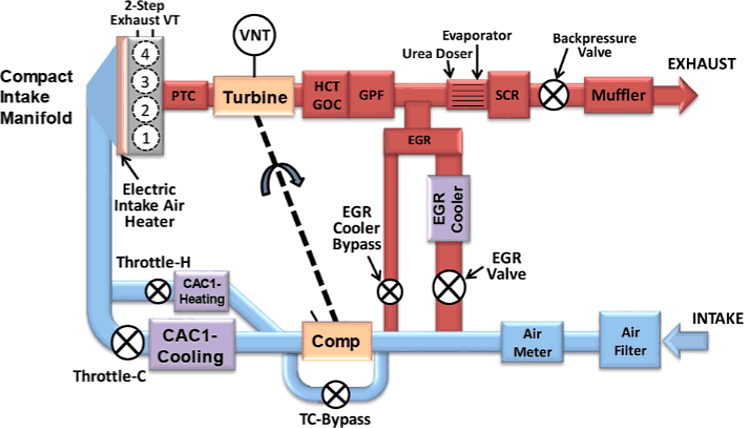
When discussing engine changes such as increased compression ratio, combustion improvements, turbocharger improvements and friction reduction that lead to improved BTE, it is tempting to consider each element as a small independent improvement that when added together, yield a larger benefit. However, as Cummins summarized in a paper discussing the development of a 50% BTE (prior to waste heat recovery) heavy-duty diesel engine for their Supertruck 2 program, this is not the case. Typically if improvements to closed cycle efficiency such as increased compression ratio, shorter combustion duration or increased air-fuel ratio are carried out, engine friction and pumping losses, if not addressed in unison, can increase and negate any potential benefit. To realize improvements in closed cycle efficiency, measures to reduce friction and pumping losses are also required at the same time. Cummins’ closed cycle improvements focused on increasing compression ratio, increasing air-fuel ratio and reducing combustion duration through increased fuel injection rate using higher flow injector nozzles. To address pumping losses, the open-cycle efficiency target was set to 100% and realized through higher turbine inlet temperature, improved turbocharger efficiency, low pressure EGR and reduced aftertreatment pressure losses. The higher turbine inlet temperature was achieved with a “low heat transfer” exhaust manifold and resulted in a lower turbine inlet pressure. Mechanical efficiency improvements focused on the crankshaft, power cylinder and lubrication and cooling systems to further reduce mechanical losses and included measures such as downspeeding, low tension piston rings and piston cooling jet nozzle flow and pressure optimization. The BTE at the time of publication was 49.9% with a breakdown as follows: closed cycle efficiency 52.4%, open cycle efficiency 100.0% and mechanical efficiency 95.4% [4143]. More recent test results show that 50% BTE has been exceeded.
A simulation study by SwRI to see if concepts used in high efficiency 4-stroke medium speed diesel engines, such as the Wärtsilä 31 with > 50% BTE and 30 bar BMEP, could be applied to high speed heavy-duty engines typical of those used in heavy trucks. The primary approach is an aggressive application of the Miller cycle. Using a 9.2 liter six-cylinder diesel engine as the basis and without increasing the peak cylinder pressure, improved efficiency and increased BMEP was demonstrated. The level of improvement was highly dependent on improving open cycle efficiency via increased turbocharger efficiency—the most difficult parameter to scale from the larger engines. At 1600 rpm, and a turbocharging efficiency of 61% (two-stage turbocharging with intercooling and aftercooling), the baseline BMEP of 24 bar was increased to over 26 bar, with a 2% fuel consumption improvement. As turbocharging efficiency increased to over 75% as is more typical for medium speed engines, over 29 bar BMEP was achieved with over 6% fuel consumption improvement. Similar results were seen at 1200 rpm [4171].
Diesel Engines
Work by Istituto Motori CNR, National Research Council of Italy, General Motors and Continental summarized 0.5 L single cylinder research engine work on a new diesel combustion system for passenger car applications intended to reduce fuel consumption without increasing NOx emissions. Using the flexibility of the latest fuel injection technology capable of an increased number of multiple injections and 250 MPa rail pressure, it is possible to achieve power and torque densities of 65-75 kW/L and 200 Nm/L. These power and torque densities fall within the capability of current single stage VGTs. The primary approach was to reduce peak firing pressure. Increasing the hydraulic flow of the injector nozzle allowed rated torque and power conditions to be met with 140 bar peak firing pressure while reducing BSFC and combustion noise. The combustion system improved EGR tolerance at full load and allowed up to 13% EGR to be used. For part load operation at several conditions representative of those encountered during the WLTP cycle, the addition of a close-coupled post injection as well as an additional pilot injection at higher engine speeds provided 4-18% reductions in BSFC, significant PM benefits and modest NOx benefits [4181].
Sandia National Laboratories presented some engine results for their ducted fuel injection (DFI) combustion system. While the engine setup was only capable of light load operation—only two injector holes were present in the injector, it did show that soot reductions were possible with commercial diesel fuels containing ~30% aromatics while having little impact on NOx, HC and CO emissions. As shown in Figure 4, DFI does not show the NOx-soot trade-off typical of conventional diesel combustion [4153]. Caterpillar also presented work on optimization of DFI duct dimensions [4176].
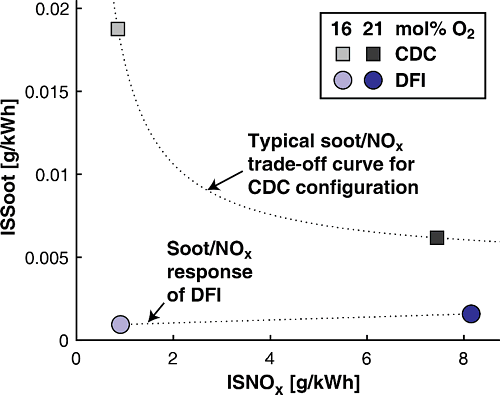
Natural Gas
SwRI reported on an internal program to apply D-EGR to a heavy-duty spark-ignited CNG engine (Cummins-Westport ISX12-G) with the aim of raising the efficiency on par with a diesel engine. The first part of the project involved CFD simulations to guide hardware design for later work. The CFD work identified a piston design an open piston bowl design with reduced squish area and lower heat losses as a first step to improve efficiency (ITE +1.3%). To this piston design, D-EGR was added for an additional 2.1% improvement in ITE. The improved knock characteristics resulting from D-EGR allowed a further 3.1% increase in ITE. The total ITE improvement predicted was 8.1% [4149]. Dynamometer testing on an engine for which two of the six cylinders were utilized as the dedicated cylinders for a nominal EGR rate of 33% compared to the baseline engine utilizing 15-20% high pressure EGR showed a 4% relative BTE improvement at 1270 rpm, 16 bar BMEP. Future testing will incorporate the new piston design and increased compression ratio [4177].
In dual fuel natural gas engine work being carried out at SwRI, a heavy-duty 12.4 L engine was set up to use multiple combustion modes. At light load, diesel only operation avoided high combustion losses of methane. At mid-load, RCCI offered the lowest NOx, smoke and CO2+CH4 emissions and the best BTE. Conventional diesel pilot ignition at high load (above 15 bar BMEP) took over where RCCI became unstable. A BTE above 47.5% with NOx ~5g/kWh was possible [4178].
Emission Measurement
A number of emission measurement presentations focused on European RDE testing and on in-use emission testing in general. A BOSMAL team examined the effects of cold start on RDE results [4182]. Horiba discussed their Smart Emission Measurement Systems (SEMS) being developed in cooperation with TNO [4183]. The SEMS system utilizes automotive sensors, GPS and cloud computing to process large amounts of in-use data over longer periods of time and without the need for the bulky PEMS package. Real-world emission validation using PEMS and GPS was also discussed by the US EPA [4184].
VERT Association presented an update on the European New Periodical Technical Inspection (NPTI) initiative [4166]. An independent periodical technical inspection of vehicles is proposed that would focus on DPF and SCR aftertreatment, to ensure adequate in-use performance and prevent tampering. PN instruments have been under development that allow for a quick and simple DPF test performed at idle. However, the development of an NPTI test for NOx appears to be more challenging. Based on experiments with three Euro 6 vehicles, it was found that NOx measurements require 10-15 minutes of driving in order to stabilize the system and ensure the SCR catalyst reaches its operating temperature. The paper recommends a chassis dynamometer test for NOx measurement.
Denso examined sources of deterioration of an amperometric NOx sensor [4158]. It was found that the deterioration of the sensor output signal after durability testing was caused by transfer of Au particles from the pump electrode (made of Pt/Au) onto the surface of the sensor electrode (Pt/Rh), as well as by particle agglomeration on the electrode surface. To minimize these effects, an improved sensor was developed—in the sensor electrode, the Rh ratio was increased and a pore forming material was added.