Conference report: THIESEL 2020
28 September 2020
THIESEL 2020, the 11th edition of the THIESEL Conference on Thermo-and Fluid Dynamic Processes in Direct Injection Engines was held September 8-11th 2020. This year the Universitat Politècnica de València (UPV) together with CMT-Motores Térmicos hosted a virtual version of the conference for the first time. The conference included 6 keynote talks, 30 research paper presentations and 4 poster presentations. Sessions covered alternative fuels, new combustion concepts, injection and combustion, CO2 reduction and emission abatement. Virtual tours of CMT-Motores Térmicos’ hot flow gas stand, rapid compression machine, dynamic vehicle test bench, climatic chamber, MEDAS+MCENAS (intake and exhaust conditioning system test cell), optical single cylinder engine, injection lab, spray lab, HPHT (high pressure high temperature) facility and anechoic chamber were also available. About 380 participants registered for the virtual conference.
Please log in to view the full version of this article (subscription required).
Alternative Fuels
In a keynote address, Saudi Aramco conveyed their thoughts on meeting the EU’s transport carbon neutrality by 2050 using e-fuels [4881]. E-fuels have the advantage of low CO2 (58 kg CO2/BOE compared to advanced biofuels at 116 kg CO2/BOE and conventional fuels at 450 kg CO2/BOE) and are fully compatible with fossil fuels and the current vehicle fleet. They can be cost effective if imported from countries with abundant renewable energy sources—an important contributor to the high cost of e-fuels in the EU is the issue of intermittency of renewable power. Hydrogen production could be via steam reforming of natural gas coupled with carbon capture and storage or via with electrolysis using renewable electricity while CO2 could be obtained from industrial point sources of direct air capture. Fuel synthesis would be via Fischer Tropsch synthesis or methanol synthesis. According to Aramco, they would be most useful for aviation and light-duty vehicles.
For aviation, the CORSIA (Carbon Offsetting and Reduction Scheme for International Aviation) target of carbon neutral growth starting 2020 requires 2.8 Gt CO2 emissions to be offset or reduced between 2020-2035. It is estimated that carbon offsets can achieve 75% of these reductions while biofuels and/or e-fuels would provide the remaining 25%.
For light-duty transport, there are numerous paths that can reach EU’s New Green Deal reduction target of 3.7 Gt CO2 between 2030 and 2050. While a BEV dominant approach (90% BEV/10% ICE mix by 2050) would be one option, this target could also be achieved with a fleet that still relies heavily on the ICE (16.5% BEV/67% ICE/16.5% PHEV + vehicle efficiency improvements). However, an approach relying heavily on electrification may still not be sufficient. Work by FEV that assumes a fleet mix with relatively high electrification (65% BEV/15% FCEV/20% HEV by 2050) showed that low carbon energy carriers such as biofuels, e-fuels and hydrogen may still be required to provide as much as 1/3 of the required CO2 reductions.
One criticism of e-fuels is that process efficiency (i.e., the ratio of energy supplied to the wheels and the amount of renewable electricity produced) is low; 13% overall energy efficiency of e-fuel diesel vehicle compared to 69% for BEV—or a factor of 5.3 according to one source [4110]. However, others claim that if more realistic assumptions for BEV efficiency are used, the ratio of the efficiencies is in fact closer to 2.4 when an ICE vehicle is fueled with e-fuels produced from renewable electricity. The smaller efficiency gap combined with expected cost reductions will make e-fuels more attractive to consumers.
If automakers are to use e-fuels to meet fleet average tailpipe CO2 requirements, they would need to take credit for the CO2 reductions from fuel production. This would only be possible with a full life cycle approach for determining CO2 emissions.
Alcohol Fuels. A combustion system design using 1D and 3D simulation by GM has been developed to enable the use methanol in a CI engine. Methanol is one option to convert renewable energy to a liquid fuel. Ignition could be achieved through a combination of higher compression ratio (19:1) and uncooled EGR. BTE with methanol is equivalent to or better than with conventional diesel. Engine-out NOx are generally lower than with diesel. These results were achieved with a simple injection strategy with minimum optimization. No substantial technology or costly adaptions were required [4879].
While ethanol has been researched as a fuel for heavy-duty compression ignition engines, ignition is of course a challenge. In the past, various means of igniting ethanol have been considered including high compression ratio, ignition improver additives, intake pre-heating, glow plugs and spark plugs. Another approach that KTH Royal Institute of Technology together with Scania are considering is ignition via a diesel pilot. Testing was carried out in a single cylinder version of a Scania D12 heavy-duty engine using a centrally mounted ethanol injector and a side mounted diesel pilot injector. A diesel pilot injector with two holes provided a good trade-off between combustion stability and combustion completeness at low load and the trade-off between ethanol premixing and engine performance at high load [4880].
New Combustion Concepts
A keynote address by John Dec of Sandia National Laboratories demonstrated the potential of low-temperature gasoline combustion to provide low emissions and high efficiency [4882]. While low temperature combustion concepts have been researched for decades with promises of low emissions and high efficiency, little progress on commercializing these approaches have been made. Challenges include complex control requirements, limited efficiency gains and problems limiting NOx and soot emissions under some operating conditions. The Combustion Research Facility at Sandia National Laboratories has been developing a low temperature gasoline combustion (LTGC) concept that they hope will provide a simplified and improved approach to low temperature combustion [4883][4884][4885]. In their Additive Mixing Fuel Injection (AMFI) approach, a small amount of ignition enhancing additive is metered into the fuel at each engine cycle to adjust the auto-ignition characteristics of the fuel. LTGC-AMFI allows LTGC from low idle to high loads and speeds with regular E10 gasoline using 0.01-0.5mm3 2-ethyl hexyl nitrate (EHN) per engine cycle. For a medium duty application, this translates to about 2 gallons for 8000 miles (7.6 L per 12800 km) of operation. The cost of the ENH is estimated to be about $20/gallon. Using a single cylinder conversion of a Cummins B5.9 fitted with a GDI injector fueled with regular E10 gasoline, LTGC-AMFI has been demonstrated from engine speeds from 600 to 2400 rpm and loads from idle to 16.3 bar BMEP.
Using results from the single cylinder engine, BTE and BSFC for a multi-cylinder engine have been estimated using a model provided by GM that corrects indicated efficiency and fuel consumption for pumping work, friction and turbocharger losses. Compared to a 7 L “generic” diesel used in EPA’s GEM model with peak BTE of 40%, BTE improvements over the entire engine map were estimated. Peak BTE was estimated to be 45.5% (a 15% improvement) while improvements at low loads ranged between 19-31%. These efficiency improvements arise from a number of factors including increased ratio of specific heats, lower heat transfer losses and a higher proportion of constant volume combustion. Details can be found elsewhere [4886].
In order to operate over the entire range of speeds and loads, several fuel injection strategies are required. For most of the engine operation from mid-load to high load at lower engine speeds, a single DI early in the intake stroke is used to provide partial fuel stratification. At loads below about 2.5 bar BMEP, a late single DI in the latter part of the compression stroke is used to concentrate fuel near the center of the combustion chamber for good combustion efficiency and low EHN consumption. For high loads at higher engine speeds, a double DI comprising an early DI injecting 70-90% of the fuel and a late DI injecting the remainder of the fuel reduces the heat release rate to allow more advanced combustion phasing for better stability and lower noise. EHN is used at loads below about 9 bar to promote autoignition and its quantity is maximum around 2.5 bar. Varying amounts of EGR at higher loads is used to limit autoignition with rates reaching 50-60% at the highest loads. NOx emissions strongly correlated with EHN consumption—suggesting nitrogen in the EHN is an important source of NOx. The highest NOx emissions, about 0.5 g/kWh, occur around 2.5 bar were EHN consumption is highest. Smoke emissions were just above the detection limit of the AVL smoke meter.
A number of other papers also dealt with combustion topics. These included a couple of presentations on active pre-chamber ignition systems for ultra-lean SI engines. Friedrich-Alexander University Erlangen found that jet propagation speed during the early stages of the jet exiting the pre-chamber (first ~ 10 mm) as well as pre-chamber body temperature correlated with engine combustion stability [4887]. Aramco together with others presented experimental results from a rapid compression machine and CFD modeling results for an active pre-chamber concept that uses a non-return valve mounted between the pre-chamber and the main chamber. The concept is currently sensitive to the presence of liquid fuel within the prechamber and requires measures to avoid this situation [4889][4888].
The LEC Austria presented a gas-diesel combustion concept for high horsepower high speed engines. While the approach has been developed for medium- and low-speed engines using multiple injectors as well as high-speed heavy-duty engines for which a single injector solution has been available for several decades, it is only recently that a single injector solution has become available for high horsepower engines [4341]. In this work, CFD was used to explore a combustion concept for a 6 L/cyl. high speed engine capable of 22 bar BMEP and a 3% diesel pilot. At the reported early stage of development, results suggested NOx emissions of 3.5 g/kWh were possible before methane emissions started to rise due to interactions with the piston bowl [4890].
Karlsruhe Institute of Technology applied RCCI combustion with natural gas and diesel fuel to a single cylinder test engine based on a Daimler OM472 fitted with a Westport HPDI injector. The aim was to achieve engine-out NOx and PM at Euro VI levels while achieving high efficiency and low methane emissions. The trade-off between efficiency, NOx and methane emissions was optimized with natural gas injection early during the intake stroke and diesel pilot around 70°BTDC. While engine-out NOx and PM below Euro VI limits and high efficiency was achieved, minimum methane emissions ranged from 0.5 to 1.4 g/kWh—below those from many conventional dual fuel engines but above those from conventional HPDI combustion. Diesel pilot quantities of 15-20% were required to minimize methane emissions [4891].
CO2 Reduction
Dr. Hiroshi Nakamura of Horiba Europe addressed the global challenge of GHG reduction from light-duty transport with a focus on the different approaches in Japan and the EU [4896]. Shortly after the Kyoto protocol was adopted, the Japanese focused their efforts on hybrids as a means to achieve light-duty vehicle CO2 reductions. Toyota launched its Prius in 1997 and Honda its Insight in 1999. By 2018 more than 30% new vehicle sales were HEV and Toyota had sold more than 10 million hybrids with 50% being sold in Japan, 40% in North America and only 10% in Europe. In Europe, the focus had been on diesels to achieve CO2 reductions with the proportion of diesels reaching 55% in 2011—up from about 20% in 1990. Both the hybrid and diesel paths were able to achieve 130 g/km CO2 by 2014.
In 2013, the Japanese government launched the “Innovative Combustion Technology” program, a national project established under the Cabinet Office as a part of the “Cross‐ministerial Strategic Innovation Promotion Program (SIP)”. The aim was to achieve 50% BTE in gasoline and diesel engines and ensure that Japan would remain competitive in engine development.
However, since the diesel emissions scandal that broke in 2015, the landscape has significantly altered. In Europe, the market share of diesels declined to 36% by 2018 and CO2 emissions have increased from a low of about 118.1 g/km in 2016 to 120.8 g/km in 2018 while the technology focus has shifted towards BEVs as a means of helping to achieve the 2021 target of 95 g/km.
While BEVs have the advantage of a very high tank-to-wheel efficiency, about 80%, the well-to-wheel CO2 emissions depend on the power mix used to charge the batteries. Additionally, the CO2 emissions associated with battery manufacture are not negligible. Using data from various sources, it was demonstrated that while BEVs should reduce CO2 emissions in most EU countries, this will not be the case in those such as Germany that still use significant amounts of coal for power production. For other parts of the world, China and Japan also use significant amounts of coal so BEVs would yield similar of higher lifecycle GHGs to those from HEVs.
Looking towards 2030, even further reductions in CO2 will be required from passenger vehicles in the EU (37.5%) and Japan (30%). Japan is opting for a well-to-wheels approach so BEVs will no longer be considered as zero emission vehicles. While the Japanese powertrain mix is expected to experience declines in ICE-only powertrains, increases in BEV/PHEV powertrains and HEV remaining in the 30-40% range, the most interesting change is expected for clean diesel engines. The proportion of vehicles with diesel engines is expected to double or triple from the current 3.6% of vehicles to 5-10%. Some of the trends envisioned for the coming decade are:
- HEV technology will lead electrification of powertrain systems with China’s NEV update this year expected to drive the market for HEVs.
- For BEVs, there will be considerable differences in the markets. In China, incentives for BEVs have been reduced—maybe due to the import dependency of key materials such as Lithium and Cobalt. In the EU, increased incentives for BEV and PHEVs are expected as part of economic incentives related to Covid-19.
- For FCVs, heavy duty will likely drive the market since BEVs are not viable for many heavy-duty applications. If the heavy-duty market establishes a refueling infrastructure and lowers component costs, FCs could become a viable solution for passenger cars in the more distant future.
- For clean diesels, increased market share is expected in Japan while a mild HEV diesel could be a solution to achieving China’s LFCV targets until 2025.
Thermal Efficiency. It is commonly believed that peak firing pressure will lead to increased mechanical losses that will offset some of the potential efficiency gains. However, New A.C.E. Institute has demonstrated that when using a limited-pressure (or Sabathe) cycle, mechanical losses do not necessary increase significantly even with considerable increases in peak cylinder pressure. Under a peak firing pressure constraint, by modifying the constant-pressure cycle in a way that phases the peak cylinder pressure to about 10°ATDC (i.e., when cylinder volume starts to increase significantly), increased thermal efficiency is possible at a compression ratio of 23.5:1 compared to 19.2:1 without a significant increase in mechanical losses. By phasing peak pressure to about 10°ATDC, lower heat losses to the combustion chamber walls are possible compared to the cases where higher pressures and temperatures occur around TDC. Higher pressure before about 10°ATDC has less benefit on work production because of the relatively low rate of cylinder volume change [4897].
Increased pre-mixed combustion in the typical diesel engine can lead to faster combustion rates and increased proportions of constant volume combustion that should increase thermal efficiency. However, increased combustion noise and heat losses mean that increased efficiency can be difficult to realize. Hokkaido University has demonstrated that a semi-premixed combustion mode that separates the premixed and diffusive combustion modes using larger pilot and pre-injection quantities can address some of the issues related to increased proportions of constant volume combustion. Increases in ITE of 1.6% and 2.5% at low and medium loads respectively were observed without significant increases in combustion noise due to lower exhaust losses and lower coolant losses. The lower heat losses were a result of lower heat flux to the piston due to less jet impingement on bowl [4898].
ETH Zurich experimentally characterized wall heat transfer and temperature for a 130 µm thick porous zirconia thermal swing coating in a high temperature/pressure vessel for potential application as a thermal barrier coating option for engine combustion chamber surfaces. Thermal swing materials are ceramic coatings with a low heat capacity and are thus better able to follow the temperature variations of in-cylinder gases and have less impact on engine volumetric efficiency. They found that the heat transfer benefit of the zirconia thermal swing coating was overshadowed by surface roughness effects—surface roughness increased the heat flux to the surface. Research should focus on achieving smoother thermal swing coatings [4899].
Oak Ridge National Lab is suggesting that direct injection stoichiometric propane engines could be an option to achieve 2027 US EPA heavy-duty CO2 requirements—the 432 g/bhp-hr HHD tractor/trailer engine requirement could be achieved with a cycle average BTE of 40.5% using propane as a fuel. A DI propane engine with a high stroke-to-bore ratio of 1.5, compression ratio of 16.8:1, late intake valve closing and about 30% EGR was shown to be capable of 45% BTE with diesel-like power density. This is a 30% improvement in efficiency compared to current commercial propane engines [4900].
Punch Torino presented a unique piston design developed by GM that is enabled by additive manufacturing and that could provide PM reductions from 30-80% and BSFC reductions of about 2% for light-duty diesel engines, Figure 1. The steel piston has a number of features that increase air utilization and reduce heat losses [4901][4902].
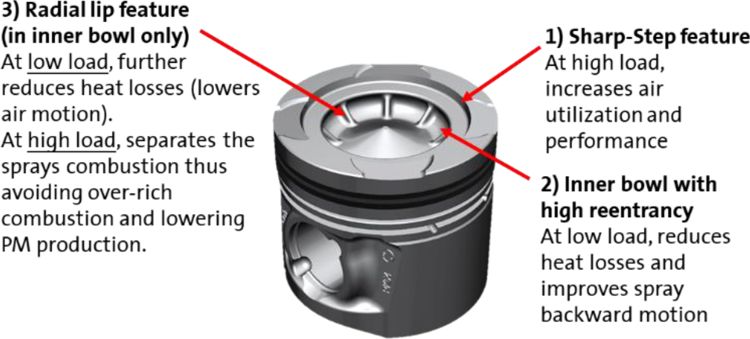
While additive manufacturing holds promise for producing unique combustion chamber and piston cooling passage geometries, production rates remain low. Mahle recently produced a series of additive manufactured pistons for Porsche—each piston blank took 12 h to manufacture.
Emission Abatement
Giorgio Rizzoni of Ohio State University delivered a keynote on the potential of connectivity and automation to deliver fuel economy improvements [4903]. Ohio State is one of the participants in ARPA-E’s NEXTCAR Project. The goal of this project is to coordinate vehicle dynamic controls and powertrain operation to maximize vehicle efficiency under real-world driving conditions for vehicles that are not yet fully automated (NHTSA/SAE levels 0-3) to obtain at least a 20% fuel consumption reduction.
The Ohio State project leverages information from enhanced mapping information (route, elevation, speed limits), the position and speed of a lead vehicle using camera/radar and traffic light timing (V2I data) to develop a look-ahead optimization for belt driven starter/generator BSG torque and vehicle speed.
Using a 48V P0 mHEV with 1.8 L TGDI engine fitted with Tula Technologies Dynamic Skip Fire (DSF) in a passenger car with adaptive cruise control (L1+ automation), fuel consumption reductions as high as 30% were experimentally achieved. The fuel savings were primarily achieved through the optimization of battery charging and e-assist use. The optimized controller achieved more engine-only operation, more e-assist and energy recovery via regenerative braking. More e-assist is possible because the controller determines when it can recover energy and more effectively recharge the batteries. For the baseline case without the optimizing controller, the engine was used more often to recharge the battery.
The fuel savings depended on route details and driver aggressiveness. On a rural route the fuel consumption decreased 10-25% while for a suburban route, the decrease was higher at 25-30%. Three different levels of driver aggressiveness were tested with trip time for each level of aggressiveness remaining the same for the baseline case and that with the optimizer engaged. In at least one case, the optimizer was able to achieve a slightly shorter trip time due to its ability to better anticipate traffic light timing.
Another keynote address was given by Zissis Samaras of Aristotle University of Thessaloniki, who summarized some key findings of the EU’s Horizon 2020 funded “DownTo10” project [4904]. An important emphasis of the measurement system development for this project was the ability to sample hot exhaust aerosols (tailpipe), fresh diluted exhaust aerosols (roadside) and aged exhaust aerosols. In order to achieve this objective, the sampling system had to be flexible and be capable of (1) carrying out the current PMP protocol, (2) being operated with an enhanced volatile particle remover (VPR) including a catalytic stripper and (3) operating without a VPR. As part of the project, measurements were carried out on a large number of engine and aftertreatment system combinations including those certified to Euro 6d-TEMP as well as a variety of different fuels including diesel (including blends with biodiesel and paraffinic diesel), gasoline (including blends with ethanol) and CNG. While some results of this work have been presented previously, a few additional findings are worth noting:
- Vehicles with diffusion based exhaust filters showed the smallest difference in PN emissions between 10 and 23 nm cut-off sizes as well as virtually no particles below 10 nm in size. For a number of vehicles with diesel and gasoline DI engines using exhaust particle filters, the average ratio of PN10nm/PN23nm was 1.3 and 1.4 respectively. There was little difference in PN2.5nm/PN23nm and PN10nm/PN23nm for these vehicles. However, for vehicles without exhaust filters, PN10nm/PN23nm ranged from 1.6 for those with PFI engines to 7.0 for those with CNG engines. These vehicles also had large numbers of particles below 10 nm with PN2.5nm/PN23nm ranging from 2.4 for PFI to 87.2 for CNG.
- For hybrids vehicles, significant differences in PN emissions between charge depleting (PHEV) and charge sustaining (HEV) mode were noted. For a PHEV in charge depleting mode, while PN emissions at a low SOC could be as much as 100× higher than at a high SOC, at low SOC, PN emissions were similar to a HEV which operates in charge sustaining mode. However, the mechanism behind the PN emissions for the two modes of operation were different. With the HEV in charge sustaining mode, engine operation was frequent and PN well controlled. For the PHEV with a low SOC, even though the engine was operated considerably less than for the HEV, PN emissions resulted primarily from engine starts that offset the potential for lower PN emissions due to less engine operation.
- Gasoline fuels with less aromatics have been suggested as a having lower PN emissions than typical gasoline. While the program noted that 23 nm and larger PN emissions from a vehicle fueled with alkylate and no GPF were indeed lower than with gasoline and comparable to those from a gasoline fueled vehicle fitted a GPF, when smaller particles were included, there was little difference between total PN emissions for gasoline and alkylate. They also noted that octane booster additives (MMT) enhanced sub-23nm PN emissions.
- As was already noted, the sampling system was designed to allow operation without the VPR so the TPN could be measured. For most applications, TPN10nm was within the same order of magnitude as SPN10nm (i.e., < 10 times SPN10nm). In these cases, catalyst warm-up and operation were well optimized to minimize the effect of volatiles on TPN values. A few examples where TPN was considerably higher than SPN included a PHEV operating in charge sustaining mode, CNG vehicles as well as PFI and CNG vehicles retrofitted (i.e., not optimized) with a particle filter. This area requires further research.
A so-called Neutral Air Quality Impact Vehicle research initiative, lead by Aramco, investigated a number of sorbents that could be used to reduce cold start NMHC and NH3 emissions from internal combustion engines. The idea would be to place the sorbent, ADS in Figure 2, near the end of the tailpipe where exhaust temperature is low during a cold start and pass the low temperature exhaust through it. As the exhaust warms up, the sorbent would be bypassed. Sorbents could be replaced at vehicle service intervals. Temperature screening of various zeolites, activated carbon and ZIF8 (MOF) has been carried out on a flow bench using gas compositions typical of GDI cold start, GDI short trip and hybrid gasoline vehicle exhaust. For NH3, copper zeolites such as Cu-ZSM5 show high storage capacity—less than 0.2 L of sorbent would be required for about 20,000 km. For NMHCs, sorbent choice is more complex with activated carbon showing better performance for heavier molecules and zeolites being better for lighter molecules—a mix of copper zeolites and activated carbon would be required. GDI vehicles would require about 20 L of sorbent but for hybrid vehicles, about 1L of sorbent would be sufficient to reduce NMHC emissions over 20,000 km of driving over the WLTC [4905].
