Conference report: 45th International Vienna Motor Symposium
27 May 2024
The 45th International Vienna Motor Symposium was held April 24-26, 2024. Due to the limited number of attendees that could be accommodated, a “Virtual Event” option was offered again this year. Virtual attendees could access the symposium material starting May 2nd. Topics covered included new engine concepts and emission reduction, driveline technologies, powertrain electrification, hybrid technologies, fuels, battery technologies, fuel cell technologies, and hydrogen engines.
Please log in to view the full version of this article (subscription required).
Light-Duty Engines
Prior to the provisional agreement on Euro 7 in December 2023, suppliers had been developing emission systems based on the stricter requirements of the November 2022 proposal that would have required implementation by 2025. These technologies addressed emissions related to cold start, cold drive-off, transient driving at low load and dynamic driving at high load and included features to quickly warm up the aftertreatment system. For Bosch, this included some combination of ICE start delay, a fuel burner and electric heater depending on the vehicle application [6167]. For Emitec, it relied heavily on their electrically heated catalyst [6168]. Since the final Euro 7 regulation has been significantly relaxed from the November 2022 proposal, these technologies are no longer needed for Euro 7 and suppliers are instead hoping to apply them to China 7 or CARB LEV IV/EPA Tier 4 vehicles.
Mazda continues to develop their ICE platforms. The next generation gasoline and diesel engines could see the application of insulation to reduce engine cooling losses. Preliminary results have demonstrated a 56% ITE for the gasoline engine platform (SKYACTIV-X) using structural insulation. An insulating coating that can be applied to combustion chamber surfaces is being developed that involves mixing hollow particles with resin material to form a film on to the combustion chamber surface [6169].
Details on several engine developments were provided by VW group companies. In 2024, Audi will launch the so-called Premium Platform Combustion (PPC) that includes at least two new engine developments, the EA888evo5 R4 TFSI and the 3.0 L V6 TFSI EA839evo.
The EA888evo5 R4 TFSI engines will be offered for worldwide applications in combination with a 48V mild hybrid system or as a plug-in hybrid. This 2-liter, 4-cylinder engine includes increased compression ratio, a more robust crank train, λ=1 over the entire engine map, a VTG rated for a maximum exhaust temperature of 1020°C, increased fuel injection pressure, electric camshaft phaser, indirect charge air cooling and Miller intake valve timing. The exhaust aftertreatment system for vehicles with a longitudinal engine installation intended for the EU and China use a 3-way catalytic converter located close to the engine directly at the turbine outlet to achieve optimum light-off times and is designed with a sensor bore and integrated binary λ-Sensor, Figure 1a. The GPF is positioned between the bulkhead and the engine in a transverse manner. Due to this arrangement close to the engine and the use of a catalytic converter with integrated sensor in the first position, the GPF does not use a catalytic coating. For longitudinal SULEV applications, a 2-brick catalyst is used in the first position to achieve an optimum between aging resistance, light-off behavior, and unit costs by increasing both the cell density and the precious metal loading in the front brick, Figure 1b. A second catalytic converter is also used after the gasoline particle filter and is positioned as close as possible to the GPF. For transverse mounted platforms, a highly integrated assembly consisting of a catalytic converter, uncoated GPF and sensors (λ-sensors, temperature measuring points) for all performance classes and markets is used along with an additional underbody catalytic converter, Figure 1c [6170].
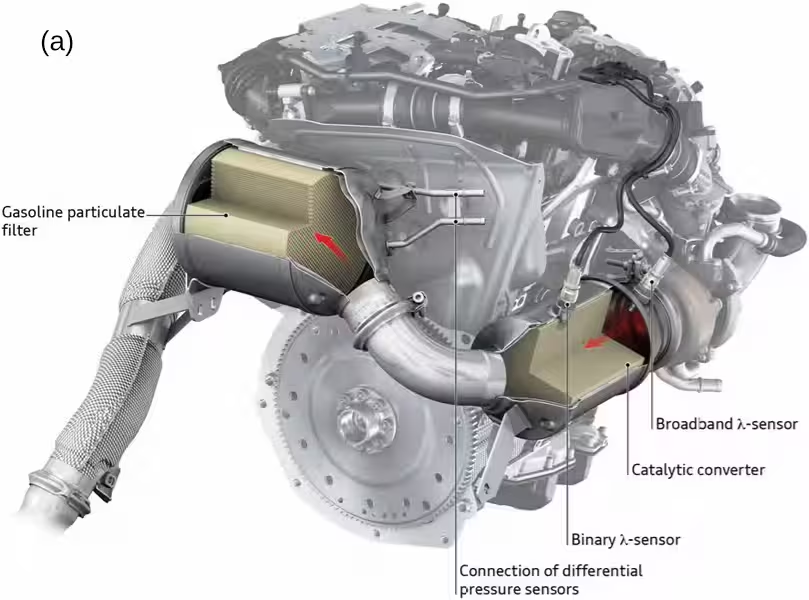
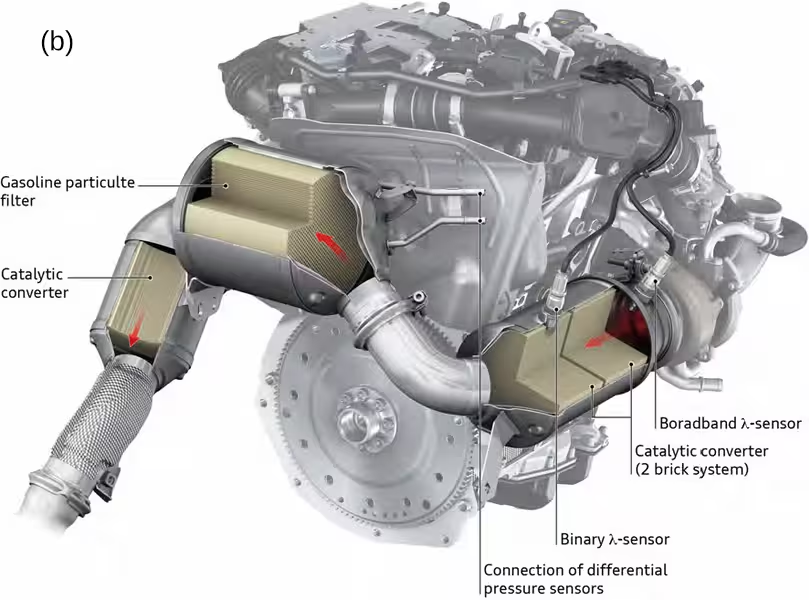
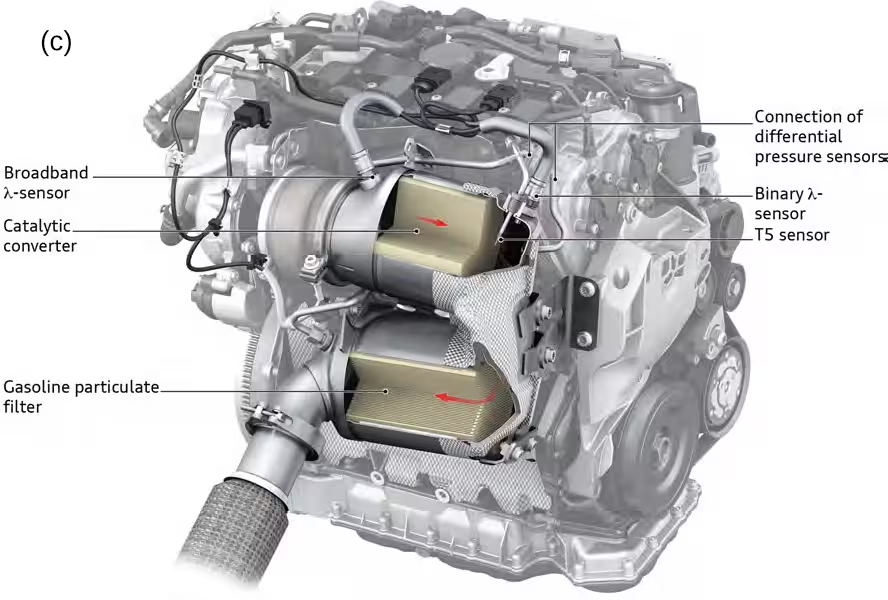
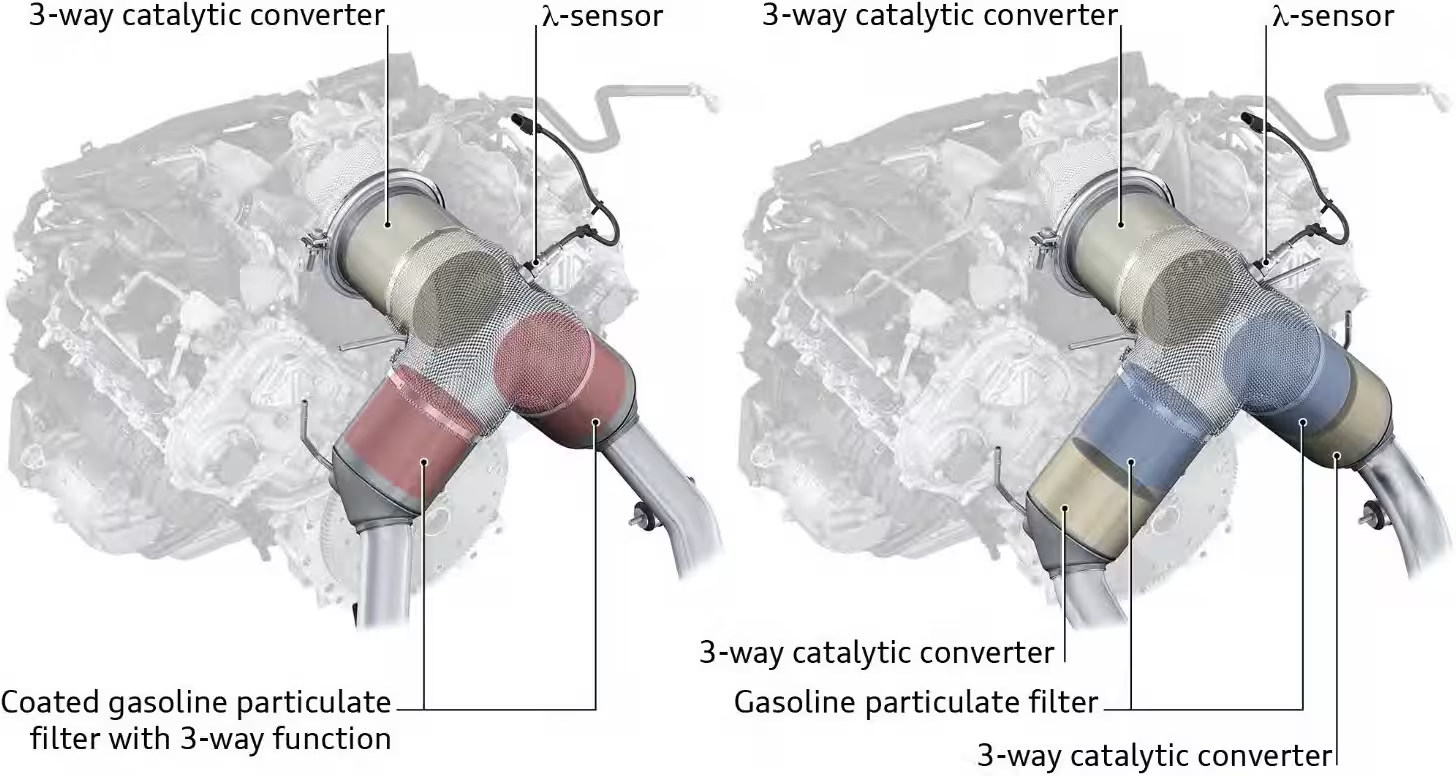
Volkswagen provided an update on the development of the latest generation 1.5 L TSI EA211 evo2 petrol engine. While the previous version of the evo2 was used in mHEV applications, the new generation of this engine is further optimized for performance and fuel consumption and is intended for parallel hybrid use. It is featured in VW’s PHEV2 platform. The engine will be available in 110 kW and 130 kW ratings, features Miller valve timing, a VTG, VVT and a high compression ratio (11.5). An atmospheric plasma spray (APS) coating on the cylinder walls minimizes friction and improves wall heat transfer to the coolant to ensure efficient cooling at full load. The VTG (rated for 980°C) is optimized to allow Miller operation even at full load. Operation is at λ=1 over the entire map range. The exhaust gas after-treatment system is arranged in an L-shape directly behind the turbocharger to save space and achieve very rapid heating, Figure 3. System light-off can be achieved after a cold start after only a few seconds of driving. The entire exhaust system in the PHEV2 drive is insulated so that the emission reduction devices remain in the thermal working range even during extended electric driving [6172].
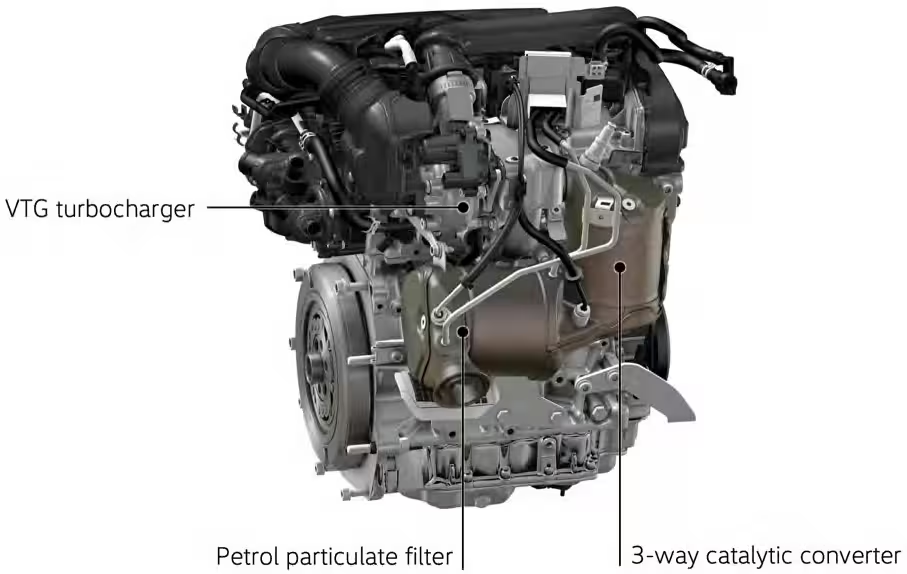
Heavy-Duty Engines
A paper by Cummins examined the potential for a P2 hybrid truck to help meet EU CO2 reduction requirements for heavy-duty trucks in 2030 and 2035. Starting with a 5LH (4×2, articulated tractor) vehicle whose CO2 is very close to 2019 5LH industry average and fitted with a Euro VII capable Cummins X10, they examined various configurations of a P2 (parallel) hybrid with different sized motors (75-250 kW) and batteries (25-200 kWh), Figure 4. While some level of BEV adoption will be required in 2035 with the assumed vehicle (minimum 25% BEVs), 2030 requirements could be met with the strongest hybrid configuration examined (250 kW electric motor, 200 kWh battery). However, compared to BEVs, the annual running costs of hybrids are higher and only slightly lower than the diesel-only truck. The difference in running costs between the hybrid and BEV options depends on the diesel/electricity price ratio. If this ratio is low (1.28 €/liter, 0.20 €/kWh) the annual BEV cost advantage is only about 10% lower and is limited to the lower annual service costs. For a higher cost ratio (1.40 €/liter, 0.12 €/kWh), the annual BEV advantage could be as high as 40% [6173].
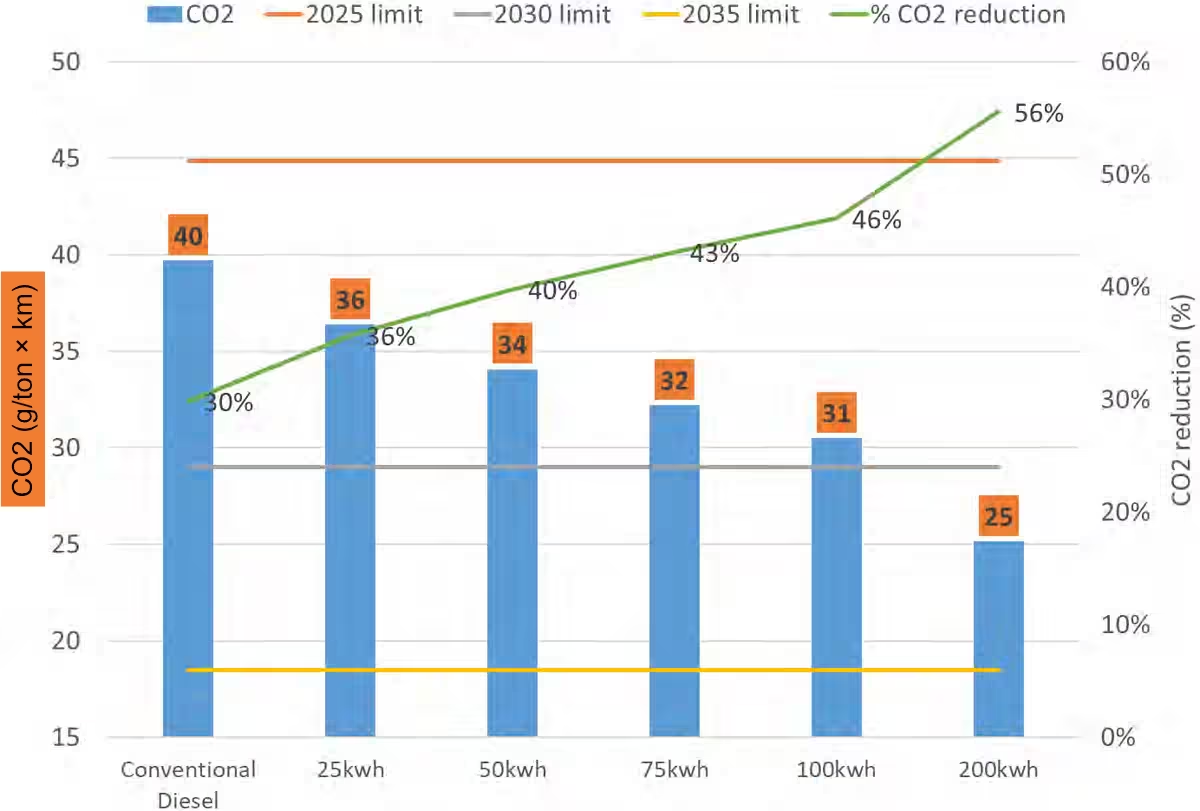
SwRI presented work on a spark ignited, PFI hydrogen heavy-duty engine that was developed from a 2024 Cummins X15N natural gas engine. The hydrogen fueled version uses no EGR, a Superturbo in place of the turbocharger, active CCV using vacuum pumps and retains the production ignition system. A peak efficiency of 42% is achieved and efficiency remains over 40% over the loaded operating range of the engine. The aftertreatment system was in the process of being integrated and consists of OC+urea SCR+ASC+PF but appears to now be complete as evidenced by a recent announcement that the engine demonstrated 0.008 g/bhp-hr NOx with aged catalysts [6174].
Westport and Scania presented recent results on the use of hydrogen in Westport’s HPDI fuel system. Last year, they showed that a Scania CBE1 Euro V engine could achieve 51.5% BTE at the A75 operating point on hydrogen with minimal changes to the engine. With a hydrogen fueled Euro VI CBE1 engine tuned to match the diesel engine’s engine-out NOx emissions, the efficiency exceeded 49% across the typical operating regime for a heavy-duty truck, with maximum torque available from 900 rpm at a BTE close to 48%. A peak efficiency of 52.02% at the A75 point was achieved. Higher efficiency is possible but at the expense of higher engine-out NOx. The exhaust temperatures are lower at low and medium load when running on hydrogen and a turbocharger rematch may be necessary to achieve the needed exhaust temperatures for the aftertreatment system. Hydrogen testing on the Scania engine was done with pilot quantities of ~6-7 mg/stroke to ensure stable operation and avoid any potential misfire. Simulation results and testing have shown that the pilot quantity could be lowered to ~2 mg/injection (a Pilot Energy Ratio of 2-3%) but may require that the injector pilot hole configuration be changed and further injector improvements carried out. The pilot quantity for the natural gas HPDI engine is approximately 5% across the WHTC. The hydrogen test results were carried out with a 560 hp/2800 Nm calibration but 600 hp/3000 Nm should be possible without exceeding the mechanical or thermal boundaries of the engine [6175].
Sandia National Laboratories summarized recent work on understanding pre-ignition in hydrogen fueled engines. They conclude that hot-spot and combustion-residuals are unlikely to be the main contributors to pre-ignition and back-fire. With regards to oil-induced pre-ignition, hydrogen significantly inhibits auto-ignition reactions of fuel-lean well-mixed hydrocarbon mixtures but the effect is less pronounced as the hydrocarbon equivalence ratio increases. The evaporation of oil droplets in the engine combustion chamber likely induces long-persisting regions with high hydrocarbon equivalence ratio near the droplet surface but further testing is required explore the impact of this [6176].
* * *
The 46th International Vienna Motor Symposium is scheduled to take place on May 14-16, 2025 in Vienna, Austria.
Conference website: wiener-motorensymposium.at