Conference report: SAE COMVEC 2024
27 September 2024
The SAE International’s COMVEC™ conference was held on September 10-12, 2024, in Schaumburg, Illinois, USA. COMVEC is one of the key forums for the exchange of information on research and technology among the commercial vehicle industry, including the on-highway, off-highway, and defense sectors. The COMVEC formula includes keynote speeches and panels with Q&A sessions, and no proceedings are published from the conference. This year’s event was attended by about 700 registered participants—including many executive level attendees—mainly from North America and Europe. The conference also included an exhibition for commercial vehicle manufacturers and their suppliers.
Please log in to view the full version of this article (subscription required).
This year’s conference focused on two key topic areas:
- Powertrain and propulsion technologies: The commercial vehicle industry is faced with regulatory requirements that mandate, for the fist time ever, the introduction of entirely new powertrain technologies. The US EPA Phase 3 GHG standards and the California ACT & ACF regulations require manufacturers to introduce an increasing proportion of zero tailpipe emission vehicles within very challenging deadlines. At the same time, the EPA 2027 emission standards require further significant NOx emission reductions from heavy-duty engines.
- Automated and software defined vehicles (SDV): The ongoing powertrain and vehicle digitalization has the potential for improved safety, efficiency, and performance. The road safety aspect has been emphasized by many speakers, as motor fatalities in the United States remain at elevated levels and road safety is an important priority for the relevant government agencies. The benefits of vehicle automation, however, come with a very high level of complexity and several associated risks.
Vehicle Automation. The conference opened with a keynote speech by Continental’s Ismail Dagli, who discussed several aspects of future SDV technologies. Advanced driver assistance systems (ADAS) such as blind spot information and lane detection systems are already being introduced in commercial vehicles. These technologies can reduce vehicle crashes and play a key role in addressing safety. Autonomous trucking—a future technology being developed, among others, by Continental in cooperation with Aurora—could help solve the problem of truck driver shortage in the USA and elsewhere. Other benefits of autonomous trucking expected by the speaker include higher utilization of and faster freight, lower fuel consumption, and safer roads.
The benefits of digital technologies were further explored in a dedicated panel discussion. Modern heavy-duty trucks are always connected to the cloud and computer controlled [P. Stephenson, Paccar]. This enables such technologies as digital cruise control and predictive adaptive cruise control, which utilizes static maps combined with GPS and input from various sensors (radars, cameras) to achieve significant fuel economy improvements.
An example application in the nonroad sector is a computerized agricultural weed sprayer that uses cameras to “see” and identify weeds, and applies the pesticide selectively on the weeds [S. Schinckel, John Deere].
Software defined vehicles are a complex technology that already requires hundreds of millions lines of code. This complexity, which is likely to increase with the application of machine learning technologies (a.k.a. AI), involves high costs and carries other risks:
- Cybersecurity—Software requires maintenance effort such as supplying security updates. This also raises concerns about the reliability, longevity, and durability of software dependent equipment. Software updates and its functionality must be maintained for many years, while software developers may be no longer interested in the specific old platform.
- Customer acceptance—Various software driven ‘features’ may not be necessarily desired by the customer and become a source of customer/driver annoyance. They may also have a negative impact on safety.
- Compliance—Software may have unintended consequences on regulatory compliance, for example in OBD systems (which are now also mandatory in electric vehicles). OBD systems must comply with regulations and must be kept as simple as possible.
- The benefits of AI—Vehicle manufacturers now use machine learning algorithms to collect and analyze vast amounts of data during vehicle development and operation. However, the results of AI analysis can only be as good as the quality of the underlying data. Additionally, AI analysis can define a correlation, but not necessarily the causality of events, which must be understood in the development of autonomous vehicles.
Decarbonization of Transportation. A sobering analysis of the state of decarbonization of the US transportation sector was presented by Chris Atkinson [Ohio State Univ. & US DOT]. While light-duty vehicles are undergoing electrification, BEV sales have now stagnated below 10% of the market share due to consumer acceptance problems. Other issues with electrification include vehicle affordability, critical minerals supply, charging infrastructure, and grid capability.
The picture is much bleaker in the heavy-duty sector—long haul trucking, off-highway, rail, and high horsepower marine applications are all in a similar state of “fuel confusion, indecision and paralysis”.
As the uptake of alternative energy sources remains slow, the US economy continues to be powered by fossil fuels. A shift of transportation energy away from fossil fuels would require a massive increase in renewable energy (5×), huge grid buildup (2×), availability of electric vehicle supply equipment (EVSE) (100×), improved energy storage (2× or more), or 10× biofuel production increase.
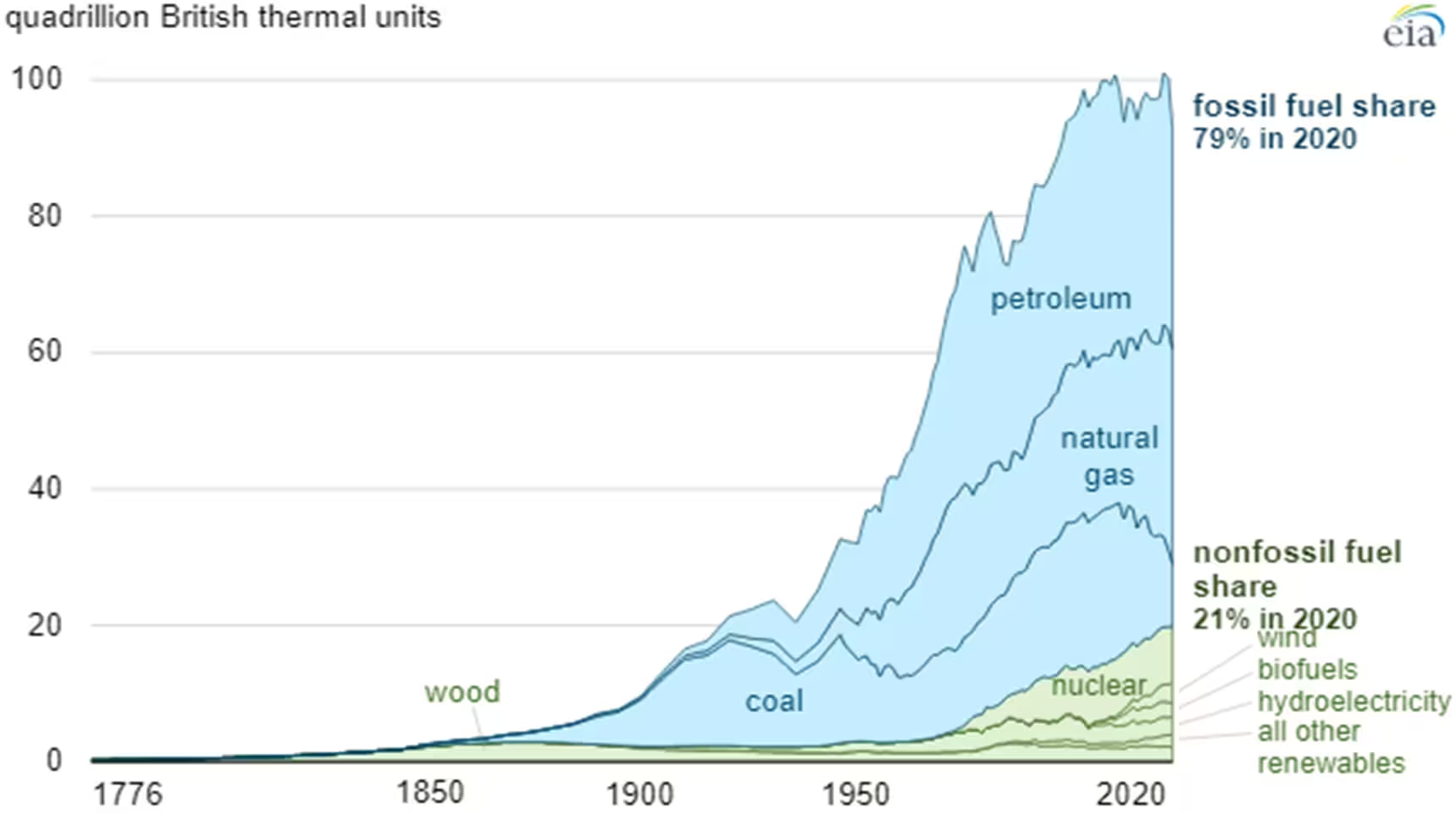
Among low-carbon fuels, biofuels present the only feasible option, but are limited by the availability of biomass. Other low-carbon fuels such as H2 or NH3 face too many hurdles to adoption to succeed. The trucking, off-road, rail, marine and aviation sectors are competing for the same low-carbon energy and fuel sources, and aviation is winning the competition for biofuels—with little low-carbon fuel to be left for the other sectors.
Another concerning aspect of the decarbonization approach is its dependence on imported minerals and materials. In 2018, the United States finally achieved energy independence. Now, the nation is choosing a complete dependence on critical materials for zero-carbon transportation, which must be imported from foreign and not always friendly countries. Dr Atkinson concluded his talk stating that the current approach to decarbonization has not been effective and requires a reset.
In a panel discussion on the Path to Zero Emissions, engine makers and speakers from academia discussed fuel-powertrain combinations that are typically envisioned for the decarbonization of transportation: BEVs for short to medium distance application, fuel cell vehicles for medium to long distance trucks, and H2 ICE for long-haul trucking. The implementation of these technologies presents a number of challenges:
- Availability of clean energy—Today’s hydrogen, made via steam methane reforming (SMR), is a fossil fuel product, it does not provide emission reductions [K. Ramakrishnan, Cummins]. Likewise, gid quality impacts BEV emissions. In some areas, BEVs produce higher lifecycle emissions than diesel. Grid capacity is another limitation of wider adoption of electric vehicles.
- Energy density—The energy density of batteries is much lower than that of diesel fuel, which impacts several characteristics of electric trucks, from payload capacity to refueling time. For example, a 60 gpm diesel fuel pump transfers energy at a rate of 144 MW, compared to some 250 kW for a fast charging station [M. Lewis, UT Austin]. The refueling rate for hydrogen is somewhat closer to diesel; dispensing 10 kg/min of H2 is equivalent to about 20 MW.
- Hydrogen fuel cell challenges—Fuel cells degrade over time and the technology has not yet achieved an adequate life time. The efficiency of fuel cells, while comparable to that of the diesel engine, declines with load; high load efficiency is still problematic. A major problem with fuel cell engines is heat release. While the diesel engine dissipates a large fraction if its waste heat with the exhaust gas, 100% of the waste heat from a fuel cell must be removed via the cooling system.
- Cost of fuel—High pump price of hydrogen is a barrier for wider adoption of H2 powertrains. E-fuels are likely to be even more costly.
Powertrains & Engines. Vehicle manufacturers are caught between a rock and a hard place—customer acceptance is heavily weighted toward diesel, as diesel vehicles have a superior payload, range, and cost. The “regulatory acceptance”, on the other hand, favors battery electric and fuel cell based powertrains [A. Thiruvengadam, Paccar].
Meeting the regulatory challenges of the EPA Phase 3 GHG standards and the California ACT regulation will require ramping up the sales of electric vehicles and other new powertrain options. At the same time, the EPA 2027 emission standards will require much more complex and robust (to meet the extended emission warranty periods) aftertreatment systems, as well as increasingly complex OBD, on diesel engines.
Navistar [N. Singh] estimates that the EPA Phase 3 regulation will require that 1 in 10 trucks they sell be electric by 2027, and 4 in 10 by 2032. For California and other states that adopt the California ACT regulation, all trucks must be ZEVs by 2036.
It is still uncertain what will be the role of hybrid trucks, including the largest Class 8 vehicles, for meeting future emission regulations. Cummins [B. Sutton] believes that hybrid trucks are likely to play some role in meeting the EPA Phase 3 requirements. While hybrids seem to attract more attention than they did a few years ago, some vehicle makers questioned the value of heavy-duty hybrids for the customer.
Due to its superior energy density, diesel fuel and diesel engines will remain essential for bigger applications [M. Dane, Cummins]. Diesel engines will also remain the key powerplant for military vehicles [P. Schihl, US Army Combat Capabilities Development Command (CCDC)]. For logistical reasons, the US Army operates land based vehicles on the same jet fuel (JP-8) used by the aircraft. While electric vehicles are potentially attractive for the military—EVs are compatible with certain modern weapon systems—charging considerations currently prevent the use of EVs in combat operations. The use of high sulfur jet fuel is also among the reasons why military vehicles are not equipped with emission control catalysts.
Hydrogen Engines. Even though hydrogen fueling infrastructure is in its infancy, effectively disqualifying hydrogen engines as a practical solution in the short term, several engine makers and engine research labs have advanced the development of hydrogen-based powertrains, with most developers focused on the H2 internal combustion engine. Important advantages of the H2 ICE over the H2 fuel cell engine include higher efficiency at high load and the tolerance of low purity H2 fuel.
The Southwest Research Institute (SwRI) displayed their hydrogen truck prototype. The Class 8 truck is powered by a Cummins X15N natural gas engine converted to run on port-injected hydrogen. The H2 engine delivers 370 hp and 2,025 Nm of torque, and has a peak efficiency of 43%. Using SCR aftertreatment, the engine achieves NOx emissions of 0.008 g/bhp-hr, well below the EPA 2027 limit of 0.035 g/hp-hr.
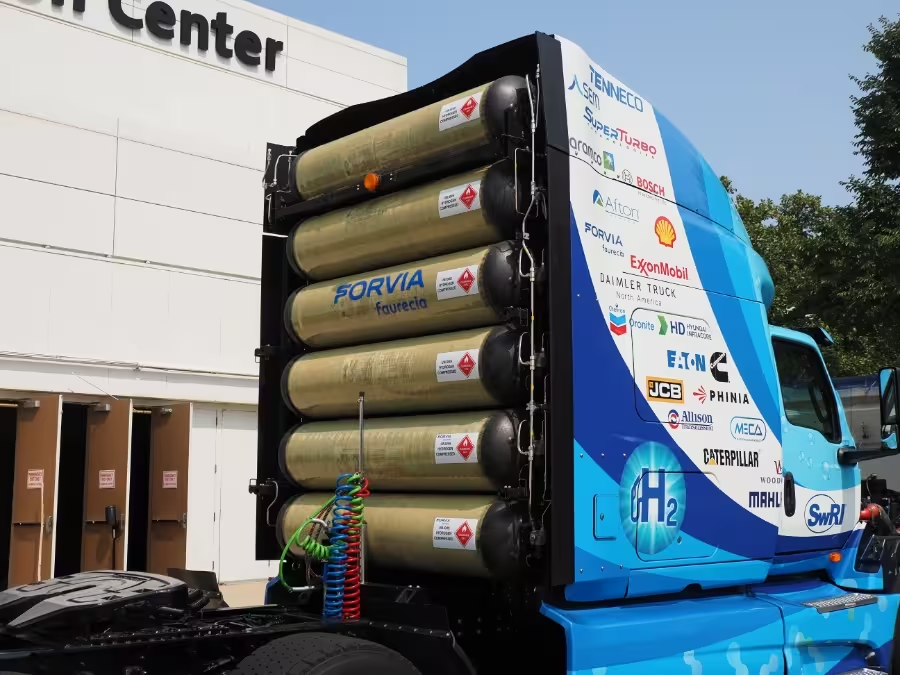
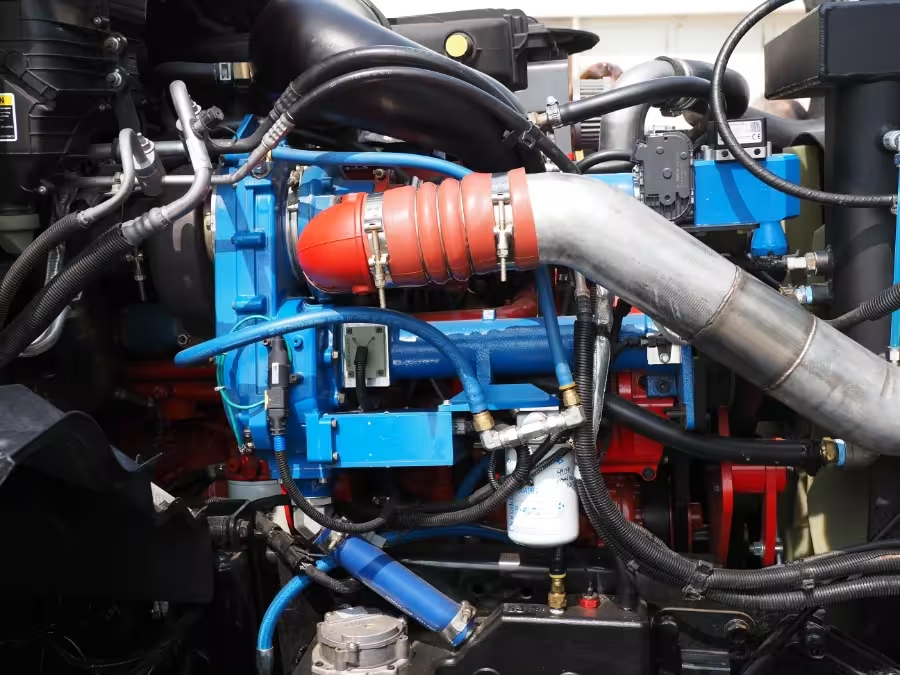
Argonne National Lab [R. Scarcelli] has been developing a hydrogen combustion engine as part of their ICE research funded through the DOE DORMA (decarbonization of off-road, rail, marine, aviation) program. Some of the key challenges with hydrogen combustion that Argonne researchers are working to overcome include flame instabilities, pre-ignition, back-fire, and power output.
TUPY [B. Ryan]—a Brazil based producer of cast iron components for engines—reported on their H2 combustion engine program conducted in cooperation with AVL and Westport. The developers reported high, ~50% engine efficiency demonstrated and/or modeled in various configurations, with a potential for 52% BTE.
MAN [A. Broda] discussed the development of their hydrogen combustion engine, MAN H4576. The 6 cylinder engine has a displacement of 16.8 L (increased from the 15.3 L of the diesel base engine due to the lower power density of H2 ICE) and delivers 383 kW and 2,500 Nm of torque with a CR of 1:12 and Pmax of 170 bar. The hydrogen ICE powers the MAN hTGX truck, which has recently won the Truck Innovation Award at the IAA Transportation in Hannover. The truck has a 600 km range made possible by a 700 bar hydrogen pressure tank with a capacity of 56 kg. Interestingly, MAN engine developers are not able to refuel their prototype hTGX truck at public service stations during their road testing. Even though hydrogen fuel is available at some fuel stations in Bavaria, only H2 fuel cell vehicles—classified as electric vehicles in Germany—can be refueled. The service stations cannot sell the same hydrogen fuel for ICE vehicles due to the higher taxation of fuels for combustion engines.
MAN is also developing an H2 fuel cell heavy-duty truck. The vehicle is powered by a 350 kW electric motor and a 200 kW battery. The biggest challenge is presented by the integration of the fuel cell and heat management. Different cooling fluid circuits have been implemented for cooling of the fuel cell stack.
Bosch [M. Thorington] discussed their development program of PEM fuel cells for heavy-duty applications. The program targets include a peak efficiency of 55%, lifetime of 20,000 hours, and power of 224 kW.
* * *
Next year, COMVEC will be held again in Schaumburg, Illinois—the event is scheduled for September 16-18, 2025.