Conference report: SAE HDD Emissions Control Symposium
26 October 2018
The 2018 SAE Heavy-Duty Diesel Emissions Control Symposium was held October 16-17, 2018 in Gothenburg, Sweden. There were about 20 presentations in a single track and the conference was attended by about 125 participants. Presentations covered regulatory developments related to Euro VI in service conformity (ISC) requirements, GHG emissions and the CARB ultra low NOx regulations currently under development. Technical solutions focused primarily on achieving CARB ultra low NOx levels. There were also sessions covering future powertrain strategies.
Please log in to view the full version of this article (subscription required).
Regulatory Developments
Euro VI ISC. The in service conformity (ISC) testing requirements for current Euro VI heavy-duty vehicles, up to Euro VI-D, only cover gaseous emissions (NOx, HCs and CO) and do not include cold start emissions (i.e., during the first 15 minutes when engine coolant temperature < 70°C). Work is proceeding under the Technical Committee Motor Vehicles (TCMV) to develop a Euro VI-E stage that would include both cold start and PN emissions in the ISC PEMS testing requirements. Regulatory details are expected to be published in the spring with implementation possibly as early as 2022.
Based on an evaluation of a number of procedures for accounting for cold start emissions carried out by the European Commission’s Joint Research Centre (JRC), the Commission is recommending an approach that would maintain the current work-based moving average windows and apply a 0.14/0.86 weighting to the cold/warm conformity factors (CF) when determining the overall ISC CF. The cold CF would be the 100th percentile (i.e., the maximum) CF for the entire ISC trip when coolant temperature is ≥ 30°C while the warm CF would be the 90th percentile CF for the entire ISC trip when coolant temperature is ≥ 70°C [Thedinga, European Commission]. A 10% power threshold would apply to the WBWs. NOx emissions during the cold start can represent as much as 70% of the total emitted by some vehicles during ISC driving, Figure 1.
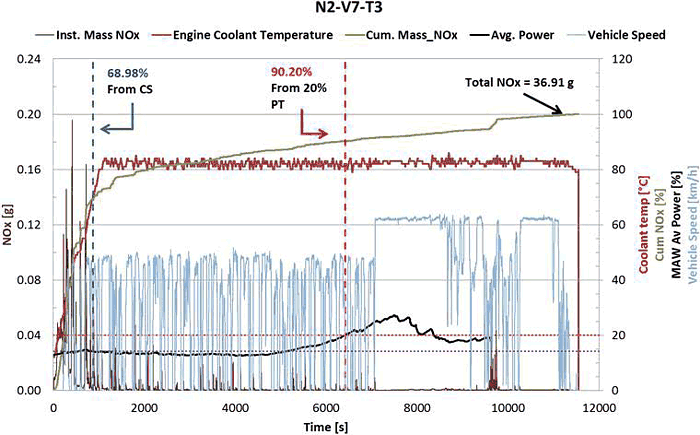
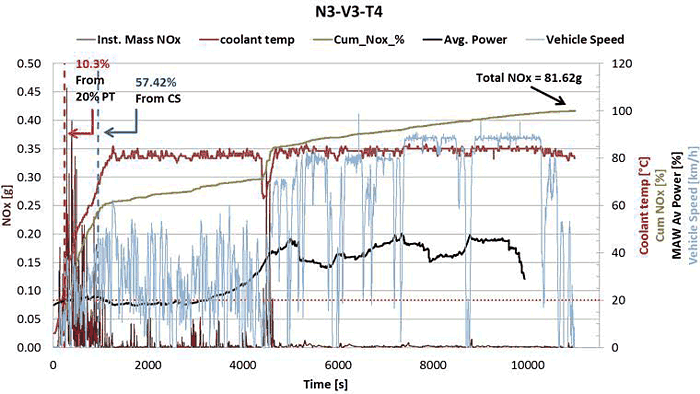
Regarding the PN requirements, the PEMS procedure will largely follow the light-duty procedure and cover particles larger than 23 nm. The conformity factor is still undecided but is expected to be higher than the current 1.5 value required for gaseous emissions.
CARB Ultra Low NOx. Development continues of the regulatory instruments associated with California’s proposed tightening of the emissions certification requirements for heavy-duty vehicles, including a NOx limit that could be as low as 0.02 g/bhp-hr. Proposals being considered include revised test procedures that would add a low-load cycle and account for idle emissions and replacing NTE in-use testing with a work-based window approach similar to Euro VI PEMS testing. The CARB work-based window would attempt to capture operation over the full duty cycle and could have a 5% power threshold (compared to the Euro VI-D threshold of 10%), include cold starts and ambient temperatures down to -7°C. Test results from over 200 trucks showed that while 90% would pass the current NTE requirements, only about 12% would pass under the new work-based window approach [Johnson, Corning].
Technology for CARB UL NOx
The primary emphasis for achieving the expected CARB UL NOx standard will be ensuring NOx aftertreatment is active during low exhaust temperature conditions such as during the cold start phase of the FTP cycle and during idle and low load operation. Another issue is operating conditions at high exhaust temperatures (above ~450°C) where SCR conversion efficiency starts to decrease; current conversion efficiencies of 95-96% in this region may not be adequate [Strots, IAV].
A common approach for addressing the issue of SCR performance at low temperature is dual dosing SCR systems consisting of a close-coupled SCR (ccSCR) catalyst, a post DPF SCR catalyst and dual urea injection points, Figure 2 [Strots, IAV][de Monte, AVL][Newman, Johnson Matthey][Geisselmann, Umicore][Wille, BASF]. However, the close-coupled SCR catalyst on its own would be insufficient to ensure NOx levels of 0.02 g/bhp-hr. The system also needs to be combined with a thermal management strategy that not only increases turbine-out exhaust temperature at cold start (e.g., with early post and/or retarded main injection) but also minimizes the catalyst cooling during idle and low load operation (e.g., with intake and/or exhaust throttles) to achieve NOx conversion efficiencies over the composite heavy-duty FTP of greater than 99.5%; the challenge is even greater if dual turbocharger systems are employed [Strots, IAV]. In order to avoid the use of external heaters, the combination of these two thermal management approaches is especially important for the heavy-duty FTP cycle that has two significant periods of idle/low load operation and limited opportunities for raising exhaust temperature through engine measures during the first 370s.

With NOx conversion efficiencies greater than 99.5%, engine-out NOx levels ranging from 2-4 g/bhp-hr would be required; suggesting EGR levels could be a little lower than those used on EPA 2004 engines.
Thermal management strategies such as those mentioned above come with a fuel consumption penalty of about 3% compared to a state-of-the-art Euro VI engine [Strots, IAV]. Another thermal management strategy that could be used is early exhaust valve opening (EEVO) and an engine calibration providing 1.5 g/kWh (1.1 g/bhp-hr) engine-out NOx during the cold start. After the ccSCR becomes fully active, the engine calibration can be switched to provide 5 g/kWh (3.8 g/bhp-hr) engine-out NOx for improved efficiency. Figure 3 reflects the thermal management demands based on the cold start engine-out NOx calibration during the first 370s of the heavy-duty FTP cycle [de Monte, AVL].
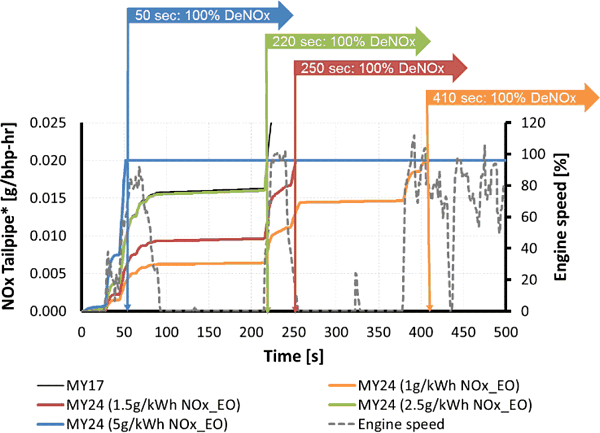
Control of the dual SCR/dual dosing system requires some added complexity but can be done in a way that still provides similar opportunities for passive regeneration of the DPF as current systems that place the SCR catalyst after the DPF. After a cold start, urea is dosed only to the ccSCR once its temperature reaches about 200-250°C. Once the second SCR catalyst reaches operating temperature, the dosing to the ccSCR is reduced while that to the second catalyst is maximized to ensure overall high NOx conversion. During operation, the urea supply to the two SCR catalysts can be further varied depending on their respective temperatures and the estimated soot loading on the DPF [de Monte, AVL]. In one example, an ammonia/NOx ratio (ANR) of 0.5 on the ccSCR and 0.6 on the rear SCR was sufficient to maintain a constant average back-pressure over 150 repetitions of the FTP [Newman, Johnson Matthey].
Having an SCR catalyst as the first aftertreatment brick is challenging for numerous reasons including the dynamic temperature conditions, exposure to sulfur and hydrocarbons and lack of NO2. Catalyst formulations could be either Cu/zeolite or vanadium [Newman, Johnson Matthey][Geisselmann, Umicore][Willie, BASF]. Vanadium benefits include its sulfur tolerance and activity for hydrocarbon oxidation. However, hydrocarbons can accumulate on the vanadium catalyst if light-off is not fully achieved and lead to uncontrolled temperature increases higher than 600°C. Cu/zeolite has the benefit of better low temperature and NO-only performance but its performance deteriorates with exposure to sulfur and hydrocarbons. Periodic exposure to 400-550°C temperatures is required to desulfate Cu/zeolite. This could be achieved with engine measures, a DOC placed upstream of the ccSCR or hydrocarbon dosing over the Cu/zeolite catalyst itself. A DOC would also provide NO2 generation but adds cost, takes up space and adds a thermal lag that could delay the start of urea dosing. Cu/zeolite has some hydrocarbon oxidation activity that could be utilized to generate the temperatures required for desulfation but fuel dosing can significantly reduce its low temperature deNOx activity. Some catalysts, such as small/medium pore zeolites are more hydrocarbon tolerant than others.
An important requirement for a ccSCR is an ammonia slip catalyst between it and the DOC. Any ammonia slip that is not cleaned up can lead to the formation of N2O and suppress NO oxidation to NO2. Hybrid catalysts combining ammonia slip and DOC functions in different layers or through zone coating are under development. The focus of these developments is to improve NO2 generation while reducing the inhibiting effect of NH3 and keeping N2O generation at a minimum [Geisselmann, Umicore][Newman, Johnson Matthey].
Instead of a ccSCR, a DPF with SCR functionality (SCRF) could be used as the first SCR catalyst in a dual dosing system. However, a DOC would be required as the first catalyst; delaying the temperature rise and possible requiring more aggressive thermal management measures than a system with a ccSCR [Wille, BASF][Newman, Johnson Matthey].
Passive NOx adsorber (PNA) technology looked promising for the CARB UL NOx application at one time. However, its commercial introduction to heavy-duty applications in the very near future is unlikely. The durability for heavy-duty diesel lifetime requirements is unproven [Newman, Johnson Matthey]. Also, given the focus on thermal management strategies discussed above that raise exhaust temperature quickly, the duration of the window during which a PNA would be needed could be short. However, interest in it remains as a means to reduce the potential CO2 penalty of some thermal management strategies [Strots, IAV].
Conference website: hddec18.org