Conference report: 17th FAD Conference
27 November 2019
The 17th FAD Conference was held on 6-7 November 2019 in Dresden, Germany. The conference is organized by the Research Association for Emission Control Technologies from Combustion Engines (Förderkreis Abgasnachbehandlungstechnologien für Verbrennungskraftmaschinen, FAD)—an industry/academia group to promote science and research in the field of emission aftertreatment technologies. This year’s meeting was attended by over 150 participants.
The technical sessions were opened by Prof. G. Zikoridse, the Conference Chair, who discussed the role of combustion engines in future mobility. While the use of electric vehicles is likely to expand in urban zones—due to their local zero-emission capability—electric mobility cannot offer the functionality and flexibility to replace the internal combustion engine (ICE), which is far from being a stranded technology, and is expected to continue to exist for decades. Neither is electric mobility emission free—the main difference is that CO2 emissions are released remotely at the powerplant. Therefore, a lifecycle approach is needed to calculate CO2 emissions from electric vehicles and to compare them with ICE emissions. However, the public discourse of future mobility in general and the future role of ICEs in particular became very politically charged, to the point that automotive OEMs prefer to avoid the discussion altogether. As a result, many ICE-related technologies such as hybridization or CO2 neutral fuels may lack the resources and the talent to be developed to their full potential [H. Becker, Institut für Wirtschaftsanalyse und Kommunikation]. The political nature of the debate has been clearly visible in German media where the coverage is often biased, with electric vehicles portrayed, without any rational analysis, as a silver bullet solution to our sustainability problems [A. Dittler, KIT]. In many cases, press coverage has been incompetent, ill-informed and filled with errors—for instance, some German newspapers have called to establish air quality limits for nitrogen (sic!).
Diesel Aftertreatment. For EU Stage V nonroad mobile machinery (NRMM), Liebherr introduced an aftertreatment system based on the SCR-on-filter (SCRF) technology, brand named SCRFilter [F. Jaussi]. The SCRFilter system includes a diesel oxidation catalyst (DOC), followed by urea injection and mixing, a wall-flow diesel particulate filter (DPF) coated with a vanadium-based SCR catalyst, and a flow-through vanadia-based SCR catalyst with an ammonia slip catalyst (ASC) coated over the outlet zone. The system can provide a high NOx reduction efficiency of 96% (NRTC), which enables engine calibration for high engine-out NOx and low PM. This, in turn, allows for high NO2:PM ratios downstream of the DOC, facilitating passive DPF regeneration—further supported by the vanadia catalyst. If the exhaust temperature is sufficiently high, continuous passive regeneration keeps the soot load on the filter low (≤ 2g/L). In situations where normal passive regeneration is not sufficient, thermal management measures are applied, primarily through exhaust gas throttling (the thermal management system does not utilize exhaust fuel injection). Duty cycles with very light loads may require “manual” regeneration—the machine must be stationary for about 45 minutes to complete the process. Since vanadia is not sensitive to sulfur poisoning, the SCR catalyst does not require desulfation. The DPF’s ash cleaning interval is 4,500 working hours.
Another talk about a Stage V aftertreatment system was given by HJS [D. Lamotte]. The starting point of the development was a compressor with a Cummins Stage IIIA 224 kW engine, which was first upgraded to Stage IV and then optimized for Stage V. The emission system included a DOC, a sintered metal particulate filter (SMF), urea injection, and an SCR catalyst. A “swirl-cap” urea mixer was used that induces swirl motion of exhaust gas to provide the required NH3 uniformity within a very short mixing path.
TU Braunschweig [K. Friese] reported on an interesting study of aftertreatment system fouling, looking into the face plugging phenomena in diesel oxidation catalysts. An engine bench set-up and test cycle were developed that could produce accelerated formation of carbonaceous and organic deposits, within up to ~60 hours, over the catalyst face. DOC samples subjected to fouling were evaluated via light-off temperature testing, scanning electron microscopy (SEM), and temperature programmed oxidation (TPO). The study was supported by the FVV project AGN-Belagbildung (ATS fouling).
Marine Emissions. Marine engines and fuels are another area of technology that is facing a disruptive change driven by the fuel quality and emission requirements—adopted and anticipated—by the International Maritime Organization (IMO). Existing IMO regulations impose limits on NOx emissions and on sulfur content in marine fuels (≤ 0.5% S from 2020). No PM emission limits have been set—it was assumed that setting fuel sulfur limits automatically ensures PM reductions [T. Mundt, DNV GL]. However, under the IMO’s Black Carbon (BC) program focused on reductions of BC emissions in the Arctic, IMO members and the industry have developed a BC definition, measurement method, and a reporting protocol. A measurement campaign by the UBA was conducted on an MAN research engine using six reference fuels, from GTL (0% S, 0% aromatics), through DMA (S=0.1%), to HFO of 2.5% S. The results showed that FSN and PM emissions increased with increasing aromatics content, while the impact of sulfur content in the fuel on particulate emissions remains uncertain. Modern injection systems have a positive effect on BC emissions. Gas mode Otto cycle engines show a BC emission advantage compared to the diesel versions.
Ambitious targets are also being considered for the reduction of CO2 emissions from shipping—a 50% CO2 emission reduction by 2050. As shipping volumes are predicted to increase by 20% by 2050, meeting the 50% reduction target would require reducing ship emissions by as much as 70%. In the long term, meeting these GHG emission reduction targets appears to only be possible using CO2 neutral fuels—assuming that such fuels could be produced in a cost effective and energy efficient manner. One of the options are synthetic hydrocarbon fuels such as methane or GTL paraffinic fuels [B. Buchholz, Universität Rostock]. Synthetic paraffinic fuels would be easy to use in existing ship engines, which is important considering that the typical life cycle of a ship is 25-30 years. Other low-carbon marine fuel options under consideration, including alcohols or ammonia, would require engine modifications.
The HyMethShip Consortium—a EU Horizon 2020 project—is developing a marine propulsion system targeting a 97% GHG emission reduction as well as substantial reductions of pollutant emissions relative to conventional marine engines [N. Wermuth, LEC GmbH]. The ship concept is fueled by methanol—to be manufactured from recycled CO2 and H2, the latter obtained via water electrolysis using renewable electricity—and features a pre-combustion carbon capture system.
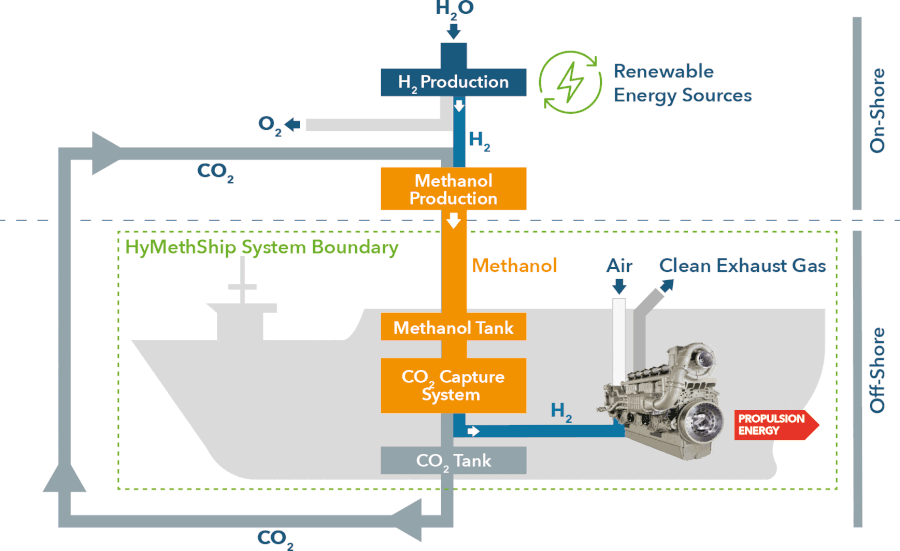
Onboard the ship, methanol is split back into CO2 and H2 via catalytic reforming. The hydrogen—separated in a membrane reactor—fuels the ship propulsion engine, while the CO2 is stored in an onboard tank for later recycling. The H2 engine could rely on a diesel pilot ignition (1-3%), and could be operated in the diesel mode up to 100% load for redundancy. First single cylinder engine results have been presented, and an onshore demonstration is planned for an application in the 1-2 MW range. One of the main challenges faced by the project is the overall energy efficiency—the process includes a number of energy conversion steps that incur thermodynamic losses.
Natural Gas Engines. Isuzu conducted a concept study on CNG propulsion for medium-duty vehicles up to 7.5 tonnes [C. Hörhammer]. A spark ignited, stoichiometric engine was selected, with a high-pressure EGR system (10% EGR over a wide area of the engine map and more at high load), and a three-way catalyst (TWC) for emission control. Exhaust temperatures of 500-550°C would be required to achieve high TWC conversion rates for methane; thermal management methods that have been considered include retarded ignition (at low loads) and an electrically heated catalyst. An important advantage of the concept is the possibility for high amount of carry-over of diesel engine parts. However, stoichiometric CNG engines may require particulate filters at the Euro VI-E stage (2023/2024 for PI engines), when PEMS testing for PN emissions will be required.
IAV reported on the development of a CNG range extender for a urban refuse collection vehicle [O. Dingel]. The electric refuse truck used in the project is powered by a 150 kWh battery, which is not sufficient for a full one day of operation. The truck was fitted with a CNG tank module—which can store 22 kg of gas, which is sufficient to provide about 100 kWh of electrical energy to the battery—and a CNG range extender module. The latter utilized a 1.4 L VW EA211 TDI CNG engine producing 81 kW of power and an 80 kW generator module. The engine had to be Euro VI certified as a truck engine. Laboratory PN emission results were well below the standard and no particulate filter was necessary. PEMS testing requirements (or methods) for this kind of range extender application remain uncertain. The refuse truck with the range extender is now tested in regular duty operation in Munich. The development was funded in part through the EU project ASSURED, focused on electrification technologies for urban commercial vehicles.
Emission Measurement. The recent changes in EU emission regulations and testing protocols also presented new challenges—as well as new business opportunities—for suppliers of automotive testing systems and equipment. Horiba [L. Hill] summarized the recent and future developments in the measurement of PN emissions for type approval, in service conformity (ISC) and RDE. PN emission limits were first introduced at the Euro 5 stage (2009/2011) to force the use of particulate filters on diesel cars, and then expanded on Euro VI heavy-duty engines and Stage V nonroad engines. Following the EU, PN limits have been adopted by a number of other countries such as China and India—with the notable exception of the United States. The Condensation Particle Counter (CPC) has been selected for the measurement due to its sensitivity and because it was an open technology, with no patent restrictions. The PN measurement procedures are being modified to count particles from 10 nm (d50), down from the current cut-off point of 23 nm. This change—anticipated in the second half of 2020—is not expected to bring any changes to diesel aftertreatment, but it may be important for gasoline and alternative fueled engines. The JRC has prepared a draft document with the proposed specifications for PN 10 nm systems for laboratory type approval testing, and is also considering their extension for on-road use, based on the current text of the GTR 15. Some key elements include a CPC counting efficiency of 50–80% at 10±1 nm and > 90% at 15±1 nm. The use of catalytic stripper is accepted in addition to the existing evaporation tube. A decision was made to define the performance specifications for the laboratory PN 10 nm systems such that the existing PN 23 nm systems could be modified rather than replaced, thereby significantly reducing the financial implications of legislation changing from PM 23 nm to 10 nm for the automotive industry. A draft GTR 15 document is expected to be delivered to GRPE in time for the June 2020 meeting in Geneva. For on-road (RDE) measurements, it is still an open question if PEMS-PN systems can be modified for the 10 nm requirement. Other related work by the GRPE Particle Measurement Program (PMP) will consider whether PN measurement can be conducted directly from heavy-duty engine exhaust on the engine test bed, without dilution (CVS or partial), as well as test and measurement methods for particles generated by non-exhaust sources such as brakes and tires.
Particle counting instruments will also be used in periodic technical inspection (PTI) programs for in-use vehicles. In Germany, PTI PN measurements are scheduled to start from the beginning of 2021, with a regulatory limit of 250,000 particles/cm3. TSI has developed a new PN instrument, called the APET, optimized for PTI/workshop use [J. Spielvogel]. Like its Model 3795 predecessor, the APET utilizes an isopropanol-based CPC. In the APET, the isopropanol fluid is replenished automatically from a docking station, where it must be added only once a year. The presentation also covered the Engine Exhaust Particle Sizer (EEPS) Model 3090, which measures the particle size distribution from 5.6 to 560 nm with a fast time resolution (10 Hz). In order to minimize sample losses, a new dilution and sample conditioning system, the Porous Tube Thermodiluter (PTT) Model 3098 has been developed.
Two real driving emissions (RDE) studies were presented that applied PEMS instruments for the measurement of emissions from alternatively fueled vehicles. One study [K. Thuneke, TFZ] used the Semtech Ecostar Plus instrument to measure emissions from a gasoline/CNG Audi 3 g-tron, and from a flexible fuel Audi A4 (gasoline/E85). The other study [M. Kortschack, TAC] used gaseous emissions and PN PEMS systems to measure emissions from diesel vehicles fueled by a number of biodiesel (FAME) and renewable diesel (HVO) blends, and from gasoline vehicles powered by E10, E20 and E85. While a number of emission effects were detected, in both studies the main factor affecting emissions was the engine and aftertreatment technology rather than the alternative fuel.
Non-Exhaust Emissions. Vehicle emissions from sources other than exhaust gases—notably particle emissions from brakes and from tire wear—attract increasingly more attention, and may become regulated at the Euro 7 stage [K. Augsburg, TU Ilmenau]. The adaptation of exhaust particle sampling and measurement technology to non-exhaust emissions is challenging, especially in the case of tire wear particles, because the contact area between the tire and the dyno roller is different from that on the road. Among the two types of non-exhaust particles, brake emissions have been relatively well researched. Brake particles are formed via tribological friction processes. Typical WLTC emission factors for European brake pads are about 2×1010 km-1 for PN emissions and 0.004 mg/km for PM. These emission factors are comparable to Euro 6 exhaust emission standards (PM = 0.005 g/km), suggesting that non-exhaust emissions are a major source of particle emissions from modern vehicles. Electrified vehicles might have even higher brake emission rates due to their heavier mass. However, brake emissions can be significantly reduced through regenerative braking due to reduced friction temperatures. This emission reduction potential is estimated at up to 98% for battery electric vehicles, and up to 50% for hybrids. Brake pad/disk materials can have a significant impact on the quality and quantity of brake particle emissions. Emission control systems for brake emissions have been proposed; these include the “Feinstaubfresser” (Fine Dust Eater) by Mann+Hummel and a French “Dust Sucker” system.
* * *
The 18th FAD Conference will be held in Dresden on 4-5 November 2020.Website: 17th FAD Conference