Conference report: 41st International Vienna Motor Symposium
29 April 2020
The 41st International Vienna Motor Symposium that was scheduled to take place on 22-24 April 2020 in Vienna, Austria, was canceled due to the Covid-19 restrictions. Instead, the organizers have offered “virtual participation” through online access to conference materials. Virtual participants receive access to conference papers and presentation slides, with some presentations also available in video format. The main focus of the event was on light-duty applications with talks on gasoline and diesel engines as well as electric and electrified powertrains. Papers were presented on new engine design, engine components, exhaust aftertreatment, powertrain electrification, and other current issues.
Please log in to view the full version of this article (subscription required).
Diesel Engines
All new light-duty vehicles for Europe must now meet the final stage of Euro 6, the so-called Euro 6d stage, that includes an RDE compliance factor of 1.43 for NOx. To meet the RDE NOx requirements, the focus for diesel engines has been on reducing engine out NOx and improving aftertreatment system NOx reduction efficiency at the high load conditions encountered during the motorway portion of the RDE cycle. For the engines discussed at this year’s symposium, use of EGR at these conditions appears to be the primary solution to reducing engine-out NOx while the aftertreatment solutions presented all used two SCR catalysts, one of which was an SCRF.
BMW discussed the 6 cylinder diesel engine for their 30d and 40d vehicles that concluded the revamp of its modular engine lineup [4705]. The integration of a 48V system as a P0 mild hybrid allows: start/stop, engine load reduction, engine load increase, engine off-coasting, electric drive boost and kinetic energy recuperation. Fuel injection is via Bosch’s CRI3-27 injection system with 2700 bar maximum pressure, piezo injectors with needle closing sensor and the capability for up to 10 injections per engine cycle. Up to 3 late post injections are used to increase exhaust temperature when required. The needle closing sensor allows closed loop control of fuel injection over a wide range of operating conditions.
To reduce engine out NOx emissions, lower power versions of the engine will rely on a cascaded 2-stage high-pressure EGR system that has 2 cooling stages, 2 electrically actuated bypass valves and a water cooled EGR valve. The cooling stages consist of a moderate performance tube-type cooler that is soot-resistant and a high performance wavy fin type cooler. In the warm-up phase and in the heating mode of the engine, mainly uncooled exhaust gas is introduced into the intake system by bypassing both cooling stages. At low partial engine loads, the low-performance cooler is preferred while the high-performance cooler is used at high loads when there is a high cooling requirement. A second bypass valve allows either the low performance cooler or both cooling stages to be used. The highest rated engines also have a low pressure EGR circuit with both HP/LP systems used in parallel over the main operating range. EGR is used over the entire operating range of the engine with rates varying from a high of about 40% at low load/low speed to a low of about 10% at high load and also high speed conditions.
The aftertreatment system uses two SCR catalysts, a close coupled SCRF and an underfloor SCR, Figure 1. While 2-stage NOx exhaust aftertreatment has been in series production at BMW since 2012, for Euro 6d, the close-coupled component (NSC + DPF) has been replaced by a DOC + SCRF. The underfloor SCR catalyst incorporates an ammonia slip catalytic coating.
In most vehicles, a single urea doser at the SCRF inlet is used, however, in heavier vehicle variants, a second doser and mixer are used before the underfloor SCR catalyst. Control of urea dosing and SCRF monitoring are achieved via NOx sensors upstream of the DOC and downstream of the SCRF. The control of the SCRF system is based on a newly developed reaction kinetic approach.
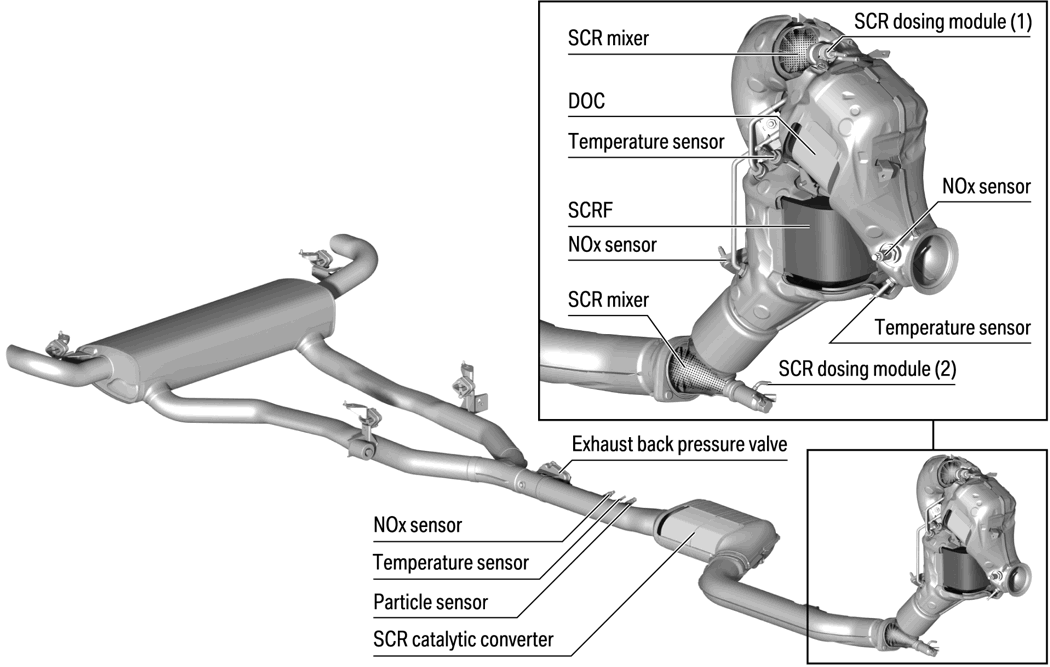
For Opel’s 1.5 L 4 cylinder diesel engine for the Opel Corsa, a new combustion system reduced fuel consumption by about 3% without adversely affecting NOx [4706]. A single can aftertreatment system is used with an SCRF replacing the underfloor SCR found in the previous version, Figure 2.
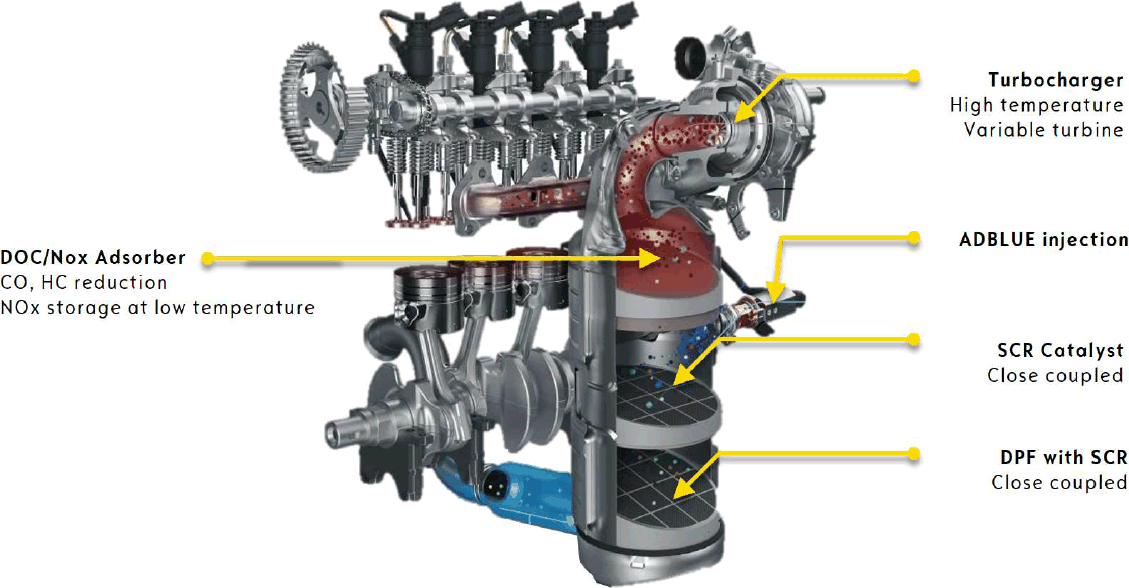
Diesel powertrains continue to be an important part of the Volkswagen AG powertrain portfolio when it comes to meeting customer needs and achieving the company's CO2 targets [4711]. The EA288 evo engine generation introduced in 2018 has been upgraded to meet Euro 6d standards. In terms of NOx emissions, engine out NOx emission reductions at high load were achieved by increasing the capacity of the low pressure EGR cooler to 12.5 kW from the previous 10 kW. The aftertreatment system is the twin dosing system announced in 2019 and further detailed in Figure 3. Compared to a single dosing system, the twin dosing system reduces NOx emissions by an additional 50% with high-load driving profiles such as the RDE cycle and up to 70% during DPF regeneration.
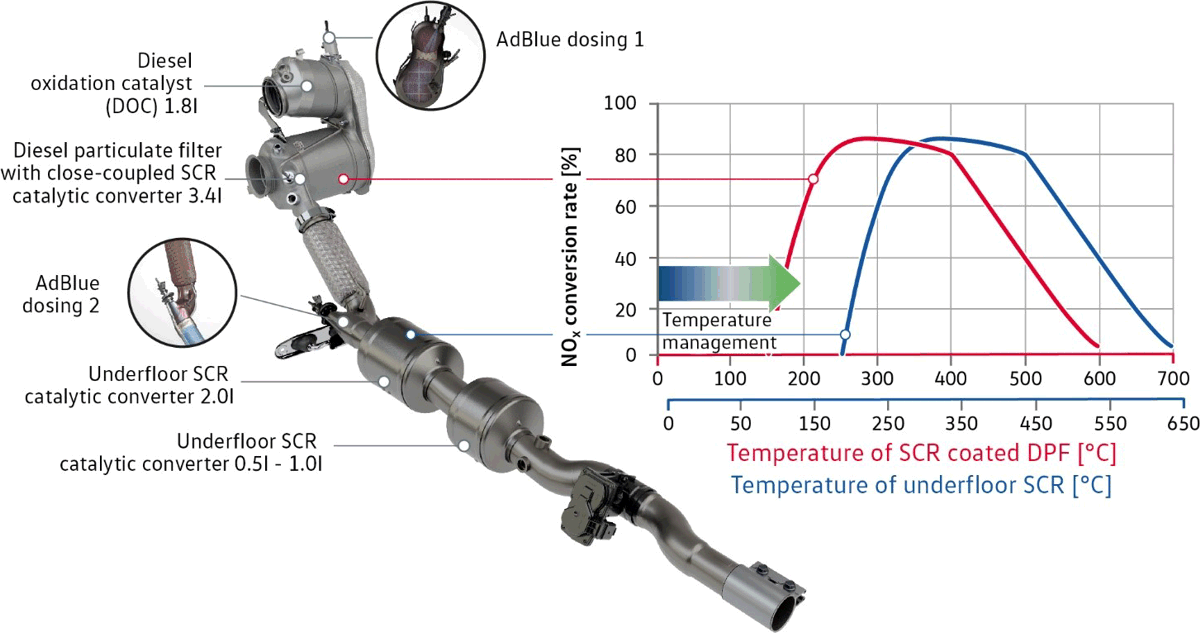
Fuel injection is via Bosch’s CRI 2-22 2200-bar system also equipped with a needle-closing sensor. Closed loop control of the fuel injection system is being used for the first time at Volkswagen and enables the use of up to 3 pilot injections. Also, during DPF regeneration, up to nine injections are used and their quantity can be stabilized. In order to further limit engine-out emissions, engine control functions during transient conditions have also been improved: combustion phasing control has been expanded from quasi-steady state conditions in the previous version of the engine to transient conditions and EGR rate and injection parameter corrections are applied during quick engine load changes as a function of charge deviation.
Thermal management during low load has a number of settings. In active heating mode, the exhaust temperature is managed by combusting post-injection of fuel. In the temperature holding mode, temperature is maintained by throttling airflow and optimizing the HP/LP EGR-split. Another option for maintaining exhaust temperature is to retard combustion phasing and combusting post-injected fuel.
SI Engines
For SI engines, the focus of many developments has been improved efficiency. A number of trends including full load stoichiometric operation and increased use of variable geometry turbochargers was apparent.
Ford’s 2nd generation of the 1.0 Liter I3 engine EcoBoost technology is based on the series production 1.5 L Ecoboost engine and is intended as a “stand-alone”-system or as an element of a hybrid powertrain while accommodating renewable fuels [4713]. The structure of the base engine was updated to be stiffer and capable of higher peak pressures while an optimized cooling concept reduces knock sensitivity. A long expansion stroke coupled with an integrated exhaust manifold enables the application of a variable geometry turbocharger. The combination of high compression ratio, priority cooling, valve train variability and variable geometry turbine enables stoichiometric operation over the entire map.
For the renewal of the Toyota Yaris, a new in-line 3-cylinder 1.5 L gasoline naturally aspirated engine has been developed as part of Toyota’s TNGA engine family [4714]. The engine has 2 variations, a GDI version for conventional vehicles (M15A-FKS, 92 kw/153 Nm) and a port injected version (M15A-FXE, 68 kW/120 Nm) for hybrid electric vehicles. The engine for conventional vehicles achieves a peak thermal efficiency of 40% while that for hybrid vehicles achieves 41%. Compared to the current Yaris, a prototype vehicle equipped with the new engine coupled to a CVT transmission achieves 5% better acceleration performance for 0-100 kph and a 6.3% fuel consumption improvement over the WLTP while with a new generation hybrid powertrain, acceleration improves 15% and fuel consumption 20%. A GPF is used in the port injected engine for hybrid applications to meet Euro 6d emission standards [4715].
Mercedes-AMG described what they refer to as the world’s most powerful four-cylinder engine in series production—the M139 [4716]. A unique feature of this engine is a three circuit cooling system. The cylinder head and crankcase have separate circuits, each with its own pump, thermostat and radiator. The cylinder head circuit is set to 85°C to minimize knock while the liner circuit is set to 115°C to minimize ring friction. A third independent circuit is used for charge air cooling.
Great Wall Motor has developed a new generation 1.5 L 4-cylinder EB modular gasoline engine platform to meet the needs of different powertrains with different levels of electrification [4717]. The engine for conventional drivetrains with no electrification adopts a second generation CVVL (Continuous Variable Valve Lift) technology with less friction, achieves a maximum thermal efficiency of 38% with Miller valve timing, incorporates a variable geometry turbocharger capable of 980°C turbine inlet temperature and is able to operate at a stoichiometric air fuel ratio over almost the entire engine map—the exception being near rated power. The engine for hybrid powertrains used LP EGR and a higher compression ratio to achieve a maximum thermal efficiency of 42%. The engine platform is intended for small and medium-sized SUVs.
Other SI engines that were discussed included Opel’s 1.2 L 3-cylinder EB [4706] and Hyundai-Kia’s 1.0 L 3-cylinder Smartstream [4727].
Future Powertrains
A number of papers examined future technology requirements related to CO2 emissions from long haul transport, emission reduction towards expected Euro 7 levels and fuel cells.
Long Haul Transport
A study by RWTH Aachen and FEV was intended to offer insight into the technology packages capable of achieving the 2025 and 2030 CO2 legislation in Europe for heavy duty long haul commercial vehicles [4718]. For 2025, currently available vehicle and powertrain improvement technologies such as waste heat recovery and 48V mild hybridization, combined with extended predictive powertrain controls should be sufficient, Figure 4. While extended predictive powertrain controls and hybridization are not yet accounted for in the VECTO tool used to determine compliance, this may change after a VECTO review expected in 2022. Based on the cost assessments made by FEV, the engine related measures are the most cost effective followed by mild hybridization. For 2030, more radical measures are required to achieve the additional CO2 reductions. The authors suggest full hybridization combined with a H2-ICE could be one option while fuel cells could become viable sometime after 2030.
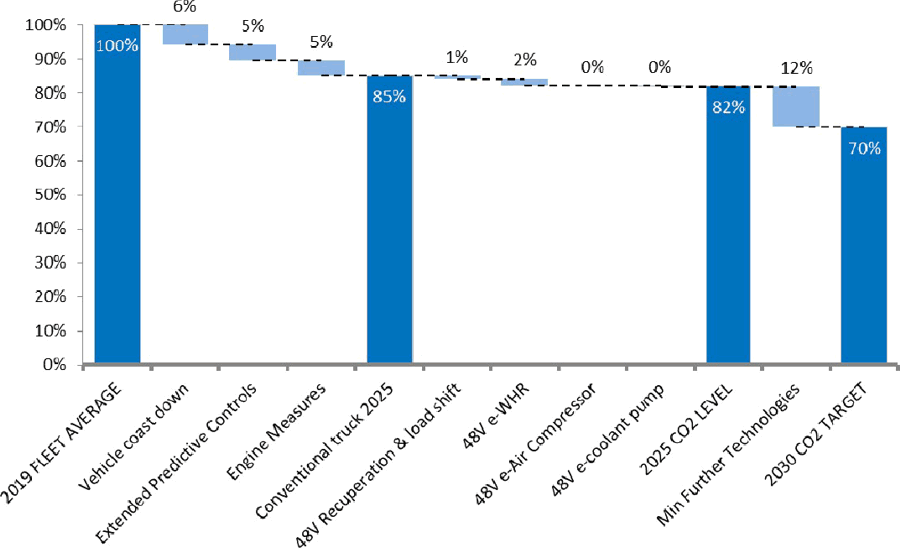
The Universität Stuttgart and IAV examined the life cycle GHG emissions of 5 commercial vehicle powertrains that could be suitable for long haul applications in the 2050 timeframe [4719]. They considered two plug-in hybrid vehicles (PHEV) fueled by different e-fuels (Fischer-Tropsch Diesel - FTD and Synthetic Natural Gas - SNG) and three electric vehicles; a battery electric vehicle (BEV), a catenary (overhead line) electric vehicle (CEV) and a fuel cell electric vehicle (FCEV). Using GHG emission estimates for current renewable electricity generation of 21.8 g CO2 eq./kWh (EU28; storage included) and 27.4 g CO2 eq./kWh (Middle East/North Africa), the CEV has the lowest life cycle GHG emissions followed by the BEV. The FCEV is in the middle, while the PHEVs have the highest life cycle GHG emissions. At 7 g CO2 eq./kWh electricity, the BEV is about the same as the FTD-PHEV.
The issue of well-to-wheel CO2 emissions from electric vehicle charging was examined by Prof. Hatamura from Hiroshima University [4720]. In the case of a large scale adoption of electric vehicles, use of the average grid power CO2 emission factors do not capture the true impact of large increases in electricity consumption from vehicle charging. In these cases, it is important to consider CO2 emissions from the marginal power source used to offset the added demand from vehicle charging. In Japan and Europe, coal-fired power generation would become the marginal power source and a large scale electric vehicle adoption could result in more electricity generation from coal. In such a scenario, CO2 emissions calculated using the emission factor of coal-fired power generation would provide a more realistic estimate for electric vehicle emissions. As a result, the widespread adoption of hybrid electric vehicles instead of EVs could reduce CO2 emissions by about 1/3. In order to achieve the same reduction in CO2 emissions through the spread of EVs, it will be necessary to limit the number of EVs, so that over 1/3 of the total EV charging demand can be supplied using surplus power from renewable energy.
Euro 7/Euro VII
According to AVL, in order to ensure hybrid vehicles with an SI engine have similar motorway fuel consumption as current diesel engines in a conventional drivetrain, SI engine brake thermal efficiencies of over 45% are required [4721]. Current SI production engines for hybrids can achieve about 41%. With increased compression ratio and boosting, 45% BTE has been demonstrated by AVL with a 2.5L engine in lean burn mode. It is expected that 45% in stoichiometric mode will be possible with further refinement. For hybrid applications, compromises can be made in terms of low speed torque and torque response to improve efficiency because of the assistance provided by the electric drive components. Also, auxiliaries can be electrified. NOx emissions can be reduced by 92% from Euro 6d levels using a close coupled electrically heated TWC followed by an underfloor passive SCR catalyst and NOx adsorber. Air injection would be required before the passive SCR catalyst.
Bosch presented a concept for gasoline engine based powertrains with ~80% lower emissions compared to Euro 6 vehicles [4722]. The concepts were implemented on a 48V mild hybrid demonstrator vehicle. Fuel injection improvements were focused on lowering cylinder liner and injector tip wetting for lower PN emissions. PN emissions were also controlled with a GPF having > 90% filtration efficiency. Closed loop control of oxygen storage on the TWC via a model-based approach was used to limit breakthrough of pollutants; Bosch refers to it as Balance Based Catalyst Control (BBCC). Current TWC control approaches react to oxygen breakthrough as detected by the downstream O2 sensor. Stoichiometric operation over the entire engine map can be achieved through reduced power density, cooled low pressure EGR or Miller cycle with modified turbocharging. For high power density, water injection can also be used. To ensure low emissions at high load stoichiometric operation, increased TWC volume can be required. Reduced cold start emissions were achieved with a lambda sensor with rapid heat-up, rapid TWC warm-up (Bosch is suggesting a burner) and an emissions based hybrid strategy that uses the electric drive components to ensure that the engine is not operated during warm-up in regions where emissions are excessive.
For diesel engines, a major challenge to further reducing NOx emissions is the relatively low exhaust temperature due to very lean operation. This can result in long warm-up times for aftertreatment systems and difficulty maintaining catalyst activity at low loads unless fuel consuming thermal management measures are taken. For heavy-duty applications, the potential of cylinder deactivation to not only increase exhaust temperature but to also reduce CO2 emissions has already been considered for some time and was further discussed in a paper by Cummins and Tula Technology [4704]. For light-duty applications, Eaton has developed an electro-mechanical variable valvetrain actuation system capable of cam profile switching down to engine temperatures well below the given minimum Euro 6 test temperature that allows cylinder deactivation as soon as possible after engine start. Work in conjunction with FEV showed cylinder deactivation as a potential technology to help achieve expected Euro 7 NOx emissions for a light-duty diesel engine mounted in a conventional drivetrain [4723].
Another option that has similar benefits to cylinder deactivation that was investigated by Schaeffler, IAV and JLR is intake valve lift variation coupled with a secondary lift of the exhaust valve during the intake stroke to provide internal EGR. The reduced intake valve lift variability also results in early IVC (EIVC) and is thus a Miller Cycle technology [4724]. In terms of keeping the turbine outlet exhaust temperature high at low loads in a warmed up engine, the combination of EIVC, secondary exhaust valve lift and post-injection showed an 8% BSFC benefit compared to a conventional heating strategy with intake air throttling and post-injection. For cold starts from 20°C, the combination of secondary exhaust valve lift and post-injection was most promising with a BSFC benefit of up to 11% compared to the conventional heating strategy. For cold start from -7°C, secondary exhaust valve lift on its own achieved a BSFC benefit of up to 9% compared to the conventional heating strategy.
Conference website: wiener-motorensymposium.at