SuperTruck II 2020 program update
11 July 2020
The US Department of Energy (DOE) Vehicle Technologies Office (VTO) 2020 Annual Merit Review (AMR) was held virtually on June 1-4, 2020. At the AMR meeting(s), advanced technology development projects funded by the DOE are presented and reviewed for their merit. This year—among other technology areas, ranging from fuels and combustion to batteries and electrification—the presentations included updates on the SuperTruck II program, providing an insight on the technology choices by Daimler, Volvo, Cummins/Peterbilt, Navistar and PACCAR to demonstrate a 55% engine brake thermal efficiency (BTE) and to achieve other SuperTruck II targets. All presentations are available for download from the AMR website.
Please log in to view the full version of this article (subscription required).
SuperTruck II kicked off in 2016 with 4 participants (Daimler, Volvo, Cummins/Peterbilt, Navistar); in 2017, the program was joined by PACCAR. Work on the initial four projects was scheduled to be completed in the second half of 2021 and in autumn of 2022 for PACCAR. Delays due to the coronavirus could push completion dates for some of the projects back by up to 1 year.
SuperTruck II has three targets: a greater than 100% improvement in vehicle freight efficiency (on a ton-mile-per-gallon basis) relative to a 2009 baseline for a long-haul freight application, demonstration of a minimum 55% engine BTE at 65 mph (104 km/h) on a dynamometer and the development of cost effective efficiency technologies. All teams have proposed freight efficiency targets ranging from 120% to 140% improvement. SuperTruck II also allows teams to consider truck applications beyond Class 8 long-haul trucks. Demonstration of the overall freight efficiency improvement goal is over a “customer-tailored” Class 8 long-haul drive cycle that meets the needs of the particular customer application. Freight efficiency over the EPA Phase 2 GHG/fuel efficiency regulatory cycles should be similar. Initial approaches to the engine efficiency targets were presented at the 2017 Annual Merit Review.
Current commercial vehicles already achieve significantly better freight efficiency than the 2009 baseline vehicle. For example, Daimler’s 2017 Cascadia offers a 61% improvement in freight efficiency over their 2009 baseline, Figure 1 [4792]. Figure 1 also illustrates the relative importance of engine and powertrain efficiency improvements to freight efficiency; combined they are expected to contribute about ¼ of the improvement.
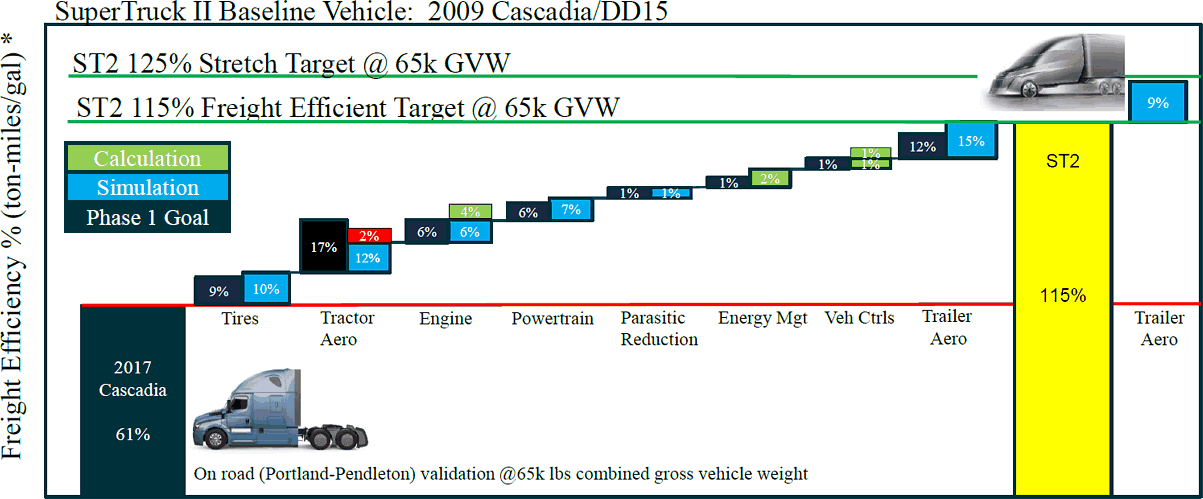
While there are unique features with each project’s approach to achieving the 55% BTE engine efficiency target, there are also common elements including: fast combustion, high efficiency turbocharging, minimization of friction losses, waste heat recovery (WHR) and reducing losses to the coolant and oil using thermal barrier coatings or low conductivity materials. By reducing the amount of heat lost to the coolant, the amount of exhaust heat available to the WHR and turbocharger (to improve open cycle efficiency) can be increased. Most teams are also using a higher expansion ratio through some combination of increased compression ratio, Miller valve timing and long stroke.
All teams have also adopted hybridization, mostly using a 48 V mild hybrid system with the electrical machine located somewhere between engine crankshaft and transmission output. Mild hybridization allows accessories such as HVAC, power-steering and fans to be electrified and operated with recovered kinetic energy even during highway operation. Efficiency gains of electrified versus belt driven accessories such as pumps can be as much as 0.5% to 0.7% BTE [4794].
Daimler
Daimler has demonstrated a BTE of 52.9% BTE for their 13 L engine [4792]. The most significant outstanding improvement required for achieving 55% BTE is to increase the performance of the WHR system by switching from a cyclopentane based system to a phase change engine cooling system with a piston expander, Figure 2. The phase change cooling system is still being evaluated and manufacturing issues around casting the cylinder head are being addressed. The phase change cooling system is expected to contribute 3.5% to BTE by operating at up to 50 bar and 305°C with a 60/40 water/ethanol mixture to delivery up to 159 kW “vapor” power. Additional gains in BTE are also expected from further refinement of combustion and air handling, friction and parasitic losses and aftertreatment system optimization.
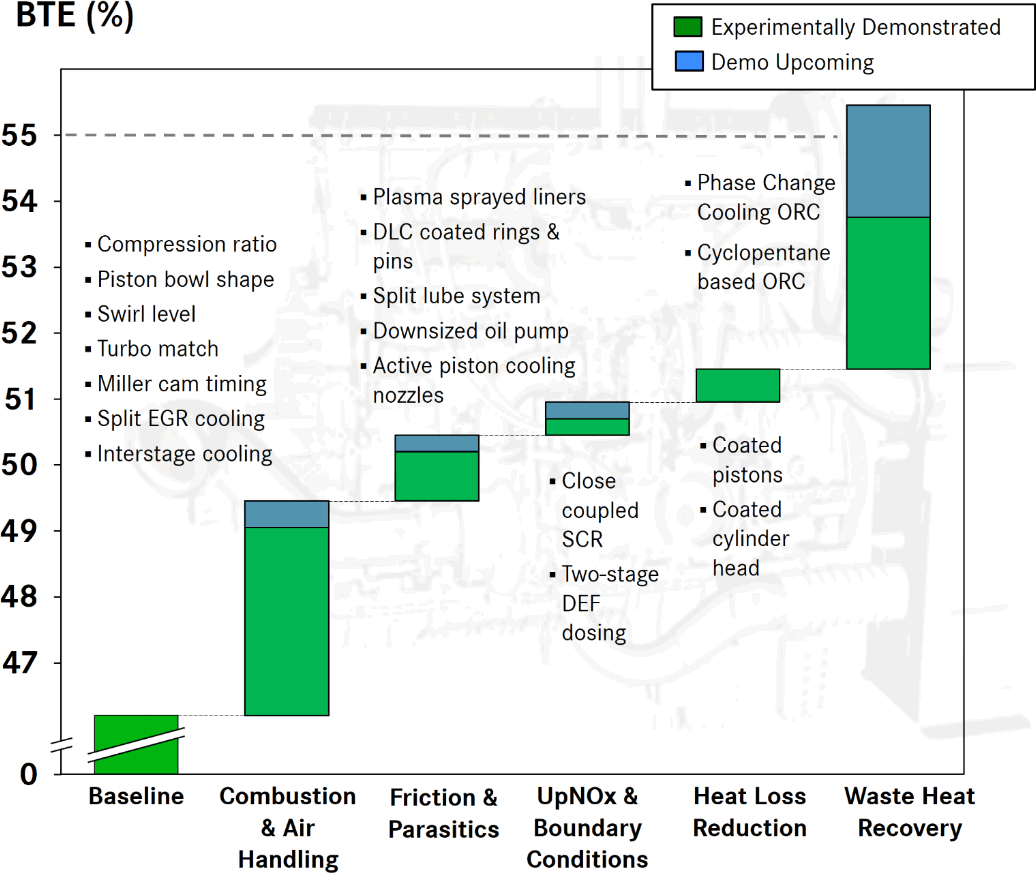
Another notable features of Daimler’s approach is a low temperature cooling circuit that provides some EGR cooling, charge air cooling, 48 V electric machine cooling and transmission thermal management. In the later case, transmission oil is either heated or cooled to maintain its temperature at 80°C to limit transmission friction.
Thermal barrier coatings for the piston and cylinder head are being evaluated. A 1% ISFC improvement has been estimated and 0.8% BSFC improvement demonstrated in a single cylinder test engine. 100 hour durability has been demonstrated.
The aftertreatment system incorporates 2-stage urea dosing and two SCR catalysts, one close coupled and the other located after the DPF.
The 48V mild hybrid system includes a 7 kWh LTO (lithium titanium oxide or lithium titanate) battery and by locating the electric machine at the transmission output, improved performance is possible compared to a belt driven starter/generator (BSG). 48 V accessories include starter, HVAC fan, HVAC compressor and power steering pump.
Volvo
Volvo has achieved a BTE of about 50% for the 11 L powertrain (ST2 Powertrain) optimized for demonstrating freight efficiency, Figure 3 [4794]. Incorporating WHR, reducing heat transfer to the engine coolant, further reductions in friction and parasitic losses with a 13 L engine platform are expected to yield 55% BTE. A 50% BTE engine in the freight efficiency demonstration vehicle suggests Volvo’s freight efficiency targets can be met without resorting to a 55% BTE engine.
The 11 L engine uses a 20:1 compression ratio, 250 bar peak cylinder pressure and a thermal barrier coating on the piston. A fixed geometry twin entry turbocharger combined with a 48 V EGR pump allows the turbocharger to be optimized for positive pumping work and a higher air-fuel ratio to achieve a higher combustion rate. A Miller intake camshaft combined with high efficiency turbocharger improves BSFC more than with conventional valve timing.
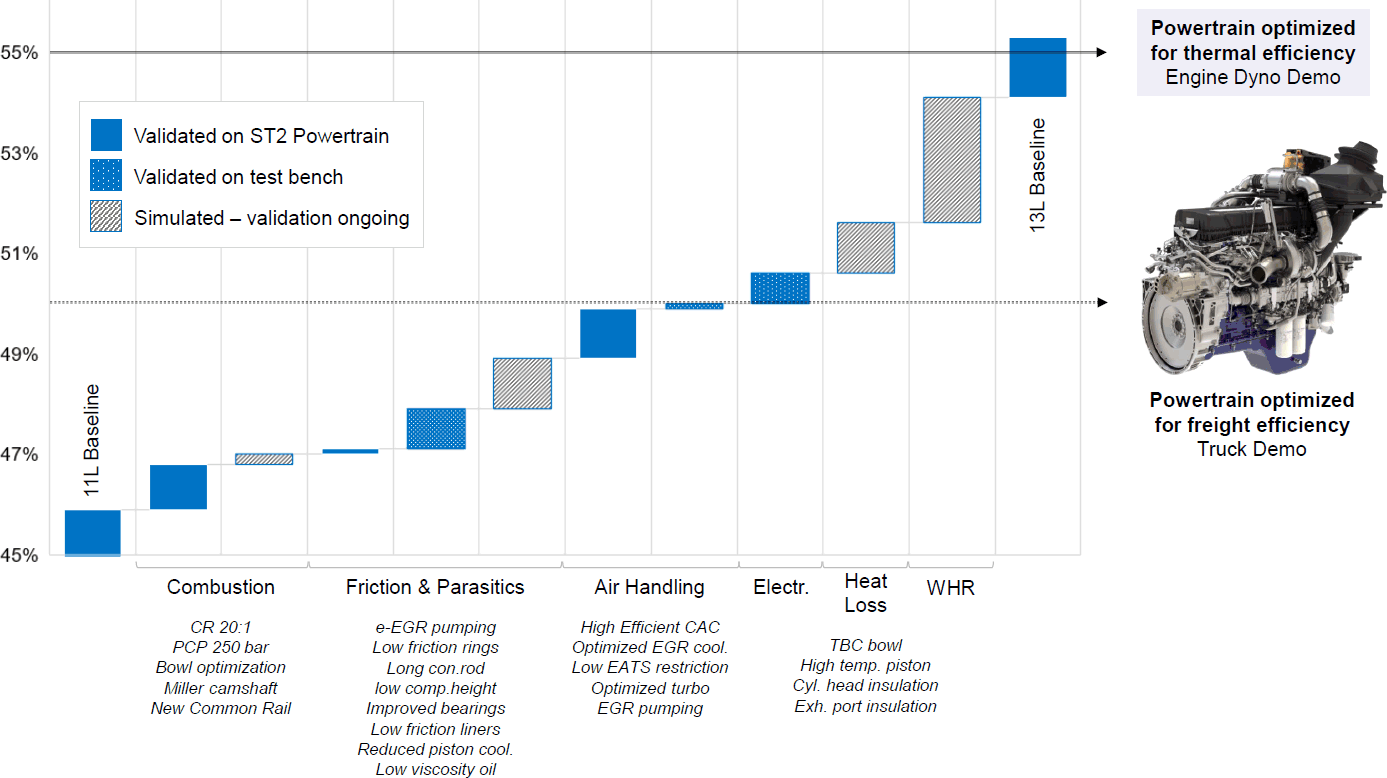
The aftertreatment system for the 11 L engine incorporates an electrically heated catalyst, while the DPF/SCR substrates are thin walled, have a high cell density and are short to achieve a low backpressure. For the 55% BTE demonstration engine, pre-turbine catalysts are being evaluated because of the lower expected exhaust temperatures. Pre-turbine catalysts show some improvement in NOx and NH3 conversion and lower NH3 slip with overdosing.
The WHR for the 55% BTE demonstration engine is a dual loop system collecting waste heat from the exhaust and engine coolant. It will be connected to the 48V mild hybrid system. The tailpipe WHR system is being rebuilt while the coolant WHR system is still being designed. Two different working fluids will be used: cyclopentane and an unspecified refrigerant.
The 48 V hybrid system for the freight efficiency demonstration vehicle uses an integrated starter/generator (ISG) mounted on the rear PTO and connected via a two speed gearbox. Energy storage is via a 14 kWh Li-ion battery. Electrified accessories include the radiator cooling fan, coolant pumps, EGR pump and HVAC system.
Cummins/Peterbilt
Cummins has demonstrated 53.5% BTE for their engine [4795]. An additional 0.8% BTE is expected from optimizing the combustion system with low heat transfer pistons and cylinder head, increased injector flow and improved injector targeting. An additional 0.5% BTE is expected from improving turbocharger efficiency through increased turbine efficiency and improved matching for the low heat transfer pistons and head. Reduced engine friction is expected to provide 0.3% BTE via lower oil pressure, lower engine oil viscosity improved bearing fit and a superfinish (polished) crankshaft. The final build-up and optimization of the WHR system is expected to provide an additional 0.1% BTE.
Cummins approach to reducing heat transfer to the coolant relies on several measures. Piston temperature is raised via material selection, component design and managing the piston oil cooling nozzle flows while heat transfer through the cylinder head is reduced through head material selection, limiting interactions with the coolant and insulating the bottom of head fire deck. Additionally, a dual wall exhaust manifold and turbine housing material selection and insulation are used to limit heat losses after the exhaust gases leave the cylinder. For the base engine, the split between coolant and exhaust losses is about 28% and 19% of fuel energy respectively while for the 55% BTE engine, the expected split is 11% to the coolant and 29% to the exhaust.
The WHR uses the dual entry turbine Cummins has been developing for several years. The turbine is expected to provide up to 10.5-11 kW at around 30k rpm and is mechanically connected to the engine output shaft via a transmission.
The 48V mild hybrid system uses an ISG integrated into the transmission. Electrified accessories include the HVAC system, power steering, cooling fans and WHR system lift pump.
PACCAR
PACCAR is targeting 51% BTE for their engine prior to accounting for WHR. WHR is expected to provide the remaining 4% BTE required to achieve 55% BTE [4793]. Implementation of a high-efficiency, two-stage fixed geometry turbocharger system with intercoolers after the low and high pressure stages is the most significant outstanding task to achieve 51% BTE. Baseline engine efficiency is 47% BTE [4799].