Conference report: ASME Internal Combustion Engine Fall Conference (ICEF 2020)
21 November 2020
The 2020 ASME Internal Combustion Engine Fall Technical Conference (ICEF)—originally scheduled to take place in Denver, CO—was held on November 4-6, 2020 as a virtual event. The technical program included several keynote and invited talks, and 75 technical papers grouped in seven tracks covering (1) Large Bore Engines, (2) Fuels, (3) Advanced Combustion, (4) Powertrain and Emissions Systems, (5) Fuel Injection and Sprays, (6) Numerical Simulation, and (7) Engine Design and Mechanical Development.
The conference opened with a keynote speech by Dr. John Farrell of the US DOE National Renewable Energy Laboratory (NREL) who discussed the challenges of decarbonizing the transportation system. Most of the perceived paths to decarbonization of transport, including the one envisioned by NREL, rely on a mix of biofuels and renewable electricity, mostly wind and solar PV. The potential of biofuels remains limited—they currently account for only 9% of US transportation fuels (mostly ethanol blended into gasoline), which is well below the official targets. The other low-carbon source of energy, “renewable electrons”, can be most efficiently used to power battery electric vehicles (BEV). The real challenge is presented by the “hard to electrify” segments, including heavy trucks, marine propulsion, and aviation. Biofuels are envisioned to play a role in aviation and, together with NH3, in marine engines. Many other applications are expected to be powered by synthetic liquid fuels (possibly compatible with existing engines) manufactured using renewable electricity—known as electro-fuels or e-fuels. E-fuels, however, are just an energy carrier, not an energy source, and their production is energy-intensive. According to some estimates, the cost of e-fuels would be 3-5 times higher than petroleum fuels. The transition to e-fuel based transport would be also a project of a massive scale. For instance, under German conditions, a full conversion of light- and heavy-duty transportation to e-fuels would require the installation of an additional ~40,000 5 MW wind turbines, and tripling today's electrical grid capacity. Overall, the task of decarbonization of the transport sector and the economy in general is highly challenging, and the projected future CO2 emission trajectory—assuming continuing economic growth—is not overly optimistic, Figure 1.
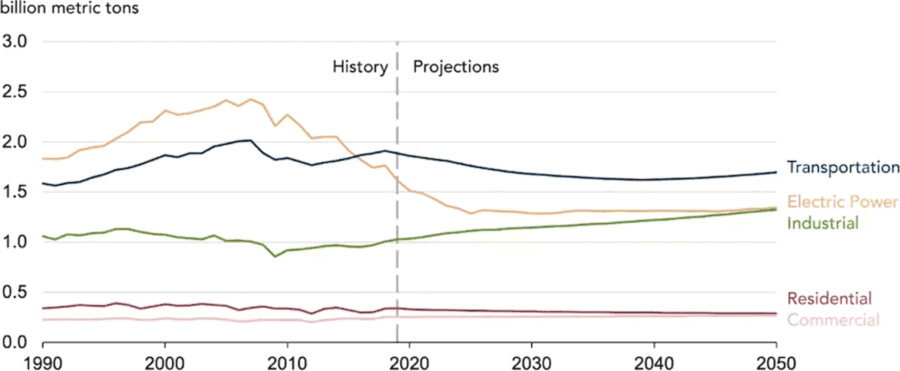
Another keynote, delivered by Dr. Prith Banerjee of ANSYS, discussed the growing role of artificial intelligence (AI) and machine learning (ML) in engineering simulation and design software. A future engineering design vision was presented, where the AI/ML techniques are used not only to learn and parametrize the prior designs, but also to learn the performance and use surrogate models for rapid evaluation of design variants.
Combustion
Papers on combustion covered a range of concepts including controlled end gas auto-ignition, gasoline compression ignition and different approaches to igniting premixed dilute mixtures.
Controlled End-gas Autoignition. Woodward provided an update on their flame triggered auto-ignition work for heavy-duty natural gas engines [4963]. In this approach, combustion is initiated via a spark and proceeds as a flame front until more than 50% of the charge has been consumed. The remaining charge then auto-ignites and is consumed very rapidly in a volumetric auto-ignition process. In this way, combustion durations of 12-17 CAD are possible—significantly shorter than the 20-30 CAD typical for conventional flame front combustion. The short combustion duration improves the degree of constant volume combustion and contributes to improved thermodynamic efficiency. A 44% BTE at 20 bar BMEP is reported for their Gen III version, Figure 2. While higher BMEPs were reported last year, the maximum 42% BTE was lower. The Gen. III engine uses a 15:1 compression ratio, 21% EGR and a stoichiometric mixture. This efficiency level is on par with many heavy-duty diesel engines and brings the potential GHG reduction benefit of stoichiometric natural gas engines to about 25% relative to diesel assuming minimum methane emissions. This is similar to HPDI engines. For current commercial stoichiometric engines, the GHG benefit is ~11% or less depending on methane emissions. Technologies used on the Gen. III engine include a passive pre-chamber spark plug that provides fast and stable combustion at the high EGR rate and a custom piston shape that enables more complete combustion and reduced heat transfer losses. Active combustion control uses a cylinder pressure sensor, Woodward RT-CDC (Real-Time Combustion Diagnostics and Control) technology and a combustion control algorithm that enables FT-AI (Flame Triggered Auto Ignition). Also, Woodward’s Gen III-EGR module provides the required levels of cooled EGR with near zero pumping work. The AFR control system coupled to a TWC enables “near zero” methane emissions and the capability to reach future California NOx emissions.
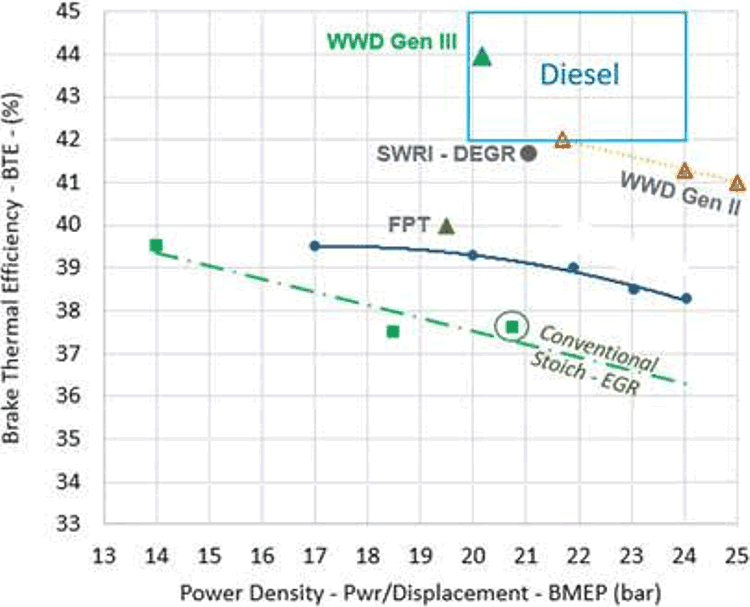
A key requirement to control end gas auto ignition is to be able to accurately control the amount of unburned mixture that auto-ignites while avoiding significant knocking combustion. Colorado State and Woodward reported on one approach that could be used [4964]. The approach adjusts spark timing to control a parameter referred to as the Combustion Intensity Metric (CIM). CIM is a weighted average of peak cylinder pressure, burn duration, peak rate of pressure rise, heat release rate rise slope and knock intensity. Cycle resolved control is used to move cycles with high CIM closer to the average cycle to shrink the knock margin and allow sufficiently advanced spark timing to enable end gas auto-ignition without experiencing heavy knock. It was found that CIM correlated very well with the fractional heat release due to auto-ignition (f-EGAI), i.e., the percent of energy available in the cylinder after auto ignition begins. Thus, controlling CIM to a predetermined level will hold f-EGAI constant and keep the engine in a steady state beyond the traditional knock limit to improve combustion efficiency, reduce combustion duration, improve power output, and increase total system efficiency. For the CFR engine used in this study, the maximum efficiency occurred at 34.1% f-EGAI and higher values created unstable combustion events that negatively impacted efficiency. At the 34.1% level of f-EGAI, the knock intensity determined via the knock ripple sum method was 38.3% based on a 0% to 100% scale that signifies a light to medium knock intensity. Work on testing this approach on a Cummins X15 engine platform is in progress.
Another aspect of controlled end gas auto-ignition is the need to accommodate varying natural gas quality. To address this issue, CFD work is being carried out by Colorado State University in conjunction with Cummins to study the fuel-engine interactions that lead to end-gas autoignition [4973]. It was demonstrated that models can predict the knock onset crank angle and pressure rise rate for light, medium, and heavy EGAI under a variety of fuel reactivities and engine operating conditions. These models can potentially be used to develop EGAI control strategies that account for varying fuel reactivity, engine operating parameters and EGR.
GCI. Gasoline compression ignition received significant attention with a relatively large number of papers. Aramco and Cummins explored the relationship between geometric compression ratio, variable valve actuation (VVA) and emissions when using GCI combustion strategies on an ethanol-free gasoline (RON of 91.4-93.2) fueled Cummins ISX15 heavy-duty diesel engine with unmodified production air handling and fuel systems [4965]. Testing was carried out a load and speed representative of a highway cruise condition. A split injection strategy was used to yield a two-stage combustion process consisting of a mild partially-premixed combustion phase followed by a dominant mixing-controlled phase. Varying compression ratio from 15.7 to 18.9 showed only a minor impact on BTE due to higher friction and pumping losses but increased smoke considerably—lower compression ratio promoted partially-premixed combustion which reduced smoke. While increased EGR rate at constant compression ratio decreased NOx emissions, a significant fuel consumption penalty and increase in smoke emissions suggested that further air-handling system development would be beneficial. The effect of EIVC was investigated via simulation and is an effective means to lengthen ignition delay and promote partially-premixed combustion—a 2.3% ISFC improvement was estimated when combined with a suitable fuel injection strategy.
A significant challenge with GCI operation is maintaining control over the combustion process through the fuel injection strategy, such that the engine can be controlled on a cycle-by-cycle basis. At loads relevant to light-duty engines, partial fuel stratification (PFS) provides very little controllability over the timing of combustion while heavy fuel stratification (HFS) provides very linear control over combustion timing. However, achieving LTC operation with HFS is challenging due to the air handling burdens associated with the high EGR rates required for NOx control. Marquette University, Oak Ridge National Lab and Chevron investigated a variety of gasoline fuel reactivities (octane numbers ranging from <40 to 87) using a HFS strategy in an attempt to understand how fuel effects influence GCI operation [4968]. At a light load (4 bar BMEP), LTC was achieved at EGR rates of 45-50% using a gasoline with <70 RON and with high injection pressure (1000 bar). At medium load (10 bar BMEP), fuel reactivity differences are diminished, and all the fuels require very similar injection timings for mixing controlled combustion operation. However, the magnitude of premixed heat release is significantly affected by fuel reactivity and gasoline fuels yielded soot emissions reductions relative to diesel at equal NOx levels.
Argonne and Aramco investigated the use of spray guided glow plugs to aid GCI combustion under low temperature conditions using CFD [4966]. The glow plug enhanced GCI combustion under cold idle conditions—by improving fuel vaporization which led to a rich mixture near the glow plug and enhanced combustion efficiency. The glow plug can also improve cold start performance at an ambient temperature of 0°C and a 200 rpm cold start condition.
Argonne and Aramco used findings from a previous parametric study in an attempt to improve injector design to suppress cavitation inside the orifices of a heavy-duty diesel injector while operating with a high-volatility gasoline fuel [4967]. The improved designs were able to prevent fuel vapor formation at 1000 and 1500 bar injection pressure and avoid super-cavitation at 2500 bar. The orifice shape can have strong influence on the pressure and fuel vapor volume fraction distributions within the orifices.
Dilute Mixture Ignition. Laser igniters have reached a point in their development where their size, power requirements and resistance to vibration and temperature could allow their practical use for engine applications. However, fouling of the final optical element that introduces the laser into the combustion chamber is still a challenge that leads to a relatively short service life. To address this concern, Argonne National Lab devised a fouling reduction strategy that included shielding to reduce the impact frequency of contamination aerosols and improved heat transfer to reduce the temperature of the final optical surface to further discourage particle adhesion [4959]. However, on its own this strategy was not able to extend the service interval for laser igniters to be on par with that of standard spark plugs (1500 h). Analysis showed that compounds originating from the lubricating oil, Zn3(PO4)2 and Ca3(PO4)2, were still contributing to fouling. When a low ash engine oil was used, 98% lens transmissivity was still maintained after 1500 h and the associated transmissivity trend suggested the service life of laser igniters could be extended to 6000 h.
While pre-chamber spark plugs create long-reach ignition jets (turbulent jet ignition or TJI) that have the potential to mitigate knock due to their rapid consumption of end-gas, detecting knock is more challenging because main chamber combustion pressure oscillations occur during normal as well as knocking combustion—conventional knock detection methods based on pressure oscillation may not be reliable. Aramco studied this problem in more detail using a passive pre-chamber spark plug and found that for knocking cycles, the amplitude of the main chamber pressure oscillations increased rapidly as combustion proceeded [4960]. This two-stage pressure oscillation behavior is unique to TJI combustion and can form the basis for knock control methods. Other work related to passive pre-chamber spark plugs carried out by Aramco used simulations to investigate flow and combustion characteristics as well as pre-chamber design variants in a stoichiometric gasoline engine that used aggressive valve overlap to increase internal EGR [4961].
Three low-temperature plasma (LTP) ignition systems were compared to a more conventional inductive spark ignition system at Sandia National Lab with an emphasis on their ability to extend the lean limit for gasoline combustion [4962]. The systems evaluated were an Advanced Corona Ignition System (ACIS) from Tenneco, a Barrier Discharge Igniter (BDI) also from Tenneco and a Nanosecond Repetitive Pulse Discharge (NRPD) from Transient Plasma Systems. The lean stability limit was extended for both the ACIS (φ = 0.68) and NRPD (φ = 0.65) ignition systems compared to the inductive spark (φ = 0.73). For the ACIS system, less spark retard was required compared to spark ignition due to larger initial kernel volumes while for the NRPD system, additional pulses were thought to add expansion energy to the initial kernel. These factors led to accelerated initial flame propagation for these two systems that extended the lean limit and increased ITE from 32.5% for the spark igniter to 33.8% and 34.5% for ACIS and NRPD, respectively. However, the lean stability limit was not reached during the limited test window for NRPD, which suggests further improvement is possible. The performance of the BDI system was very close to that of the inductive spark system.
Turbocharging
In 2018, Wabtec launched an initiative to investigate and demonstrate how additive manufacturing (AM) technologies could benefit turbochargers [4969]. One goal was to identify and demonstrate design improvements enabled by additive manufacturing which could provide performance, development time and cost benefits. Rather than iterate based on a prior design, a turbocharger was designed from a clean sheet based on what would be possible using additive manufacturing.
Laser Powder Bed Fusion (L-PBF) additive manufacturing technology with Nickel Alloy 718 (NA718) was used to manufacture a single piece integrated turbine-bearing housing that eliminated the need to bolt separate turbine and bearing housings together. This housing features an internal lattice structure to realize a 22% reduction in material while continuing to meet stiffness requirements. A dual wall construction around the turbine wheel for burst containment eliminates the need for a large number of additional parts that would otherwise be bolted to the turbine housing.
For the turbine wheel, L-PBF using NA718 also offers a cost competitive, short lead time option to milled-from-solid manufacturing using a 5-axis CNC machine without the same geometric limitations. To minimize build height and component cost, a process was developed to friction weld a 4140 steel shaft to the NA718 wheel.
A compressor wheel was made from titanium (Ti-6Al–4V) using Electron Beam additive manufacturing technology. Electron beam AM technology is able to effectively print unsupported surfaces at more extreme angles than L-PBF and also has the potential to be cost and lead time competitive with low volume conventional manufacturing methods.
A single piece tilting pad bearing in bronze alloy using L-PBF was also manufactured. Traditionally tilting pad thrust bearings are multi-piece. The design also incorporates a feature which supplies oil to the leading edge of the bearing pad face that encourages hydrodynamic oil film development and that could not be executed with conventional manufacturing methods.
Additive manufacturing also enabled a fluidic variable turbine (FVT) shroud that offers an alternative to a mechanically variable geometry turbine. With the FVT, the turbine inlet flow characteristics are changed by using a jet of air to partially block inlet flow rather than pivoting the vanes. Equivalent performance to a mechanical pivoting vane turbine is believed to be possible using a single piece design with no moving parts. As shown in Figure 3, slots are located on the vanes that would be very difficult to manufacture using conventional methods.
The Additive Content Turbocharger was tested for over 50 hours and was able to meet the functional and performance design targets and no component failures were encountered during the test. The overall efficiency was within 2% of the baseline conventionally manufactured turbocharger and it is expected that an additional 3-5% improvement in efficiency could be achieved with optimization.
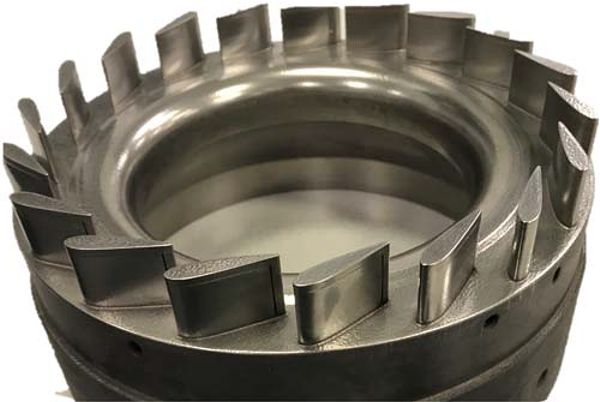
The University of Oxford investigated the effect of an inner insulated turbine housing on exhaust temperature during engine warm-up, a step load transient and the WLTC cycle using simulation and experiments with a 2.2 L prototype diesel engine [4970]. At a steady state condition, the insulated turbocharger can achieve 5 to 14 K higher turbine outlet temperature depending on the engine speed and load conditions. During the engine warm up test, the temperature drop between the turbine inlet and outlet was reduced by 4K with the insulated turbine housing. With the step load transient test, the insulated turbine housing also provided a 4 K temperature increase but also 2000 rpm higher turbocharger speed under the same turbocharger inlet and outlet boundary conditions. Over the WLTC cycle, the average turbocharger speed was increased by 800 rpm while average turbine outlet temperature was 1.7 K higher.
Engine Efficiency
KTH Royal Institute of Technology and Wärtsilä carried out an exergy analysis to identify losses and improvement potential of a large bore Wärtsilä 31DF four-stroke marine engine system with two-stage turbocharging [4957]. Engine irreversibilities were characterized as: combustion losses, heat dissipation losses, and gas exchange losses. Combustion irreversibility dominated and accounted for up to 2/3 of the total exergy destruction. The proportion of total fuel exergy lost due to combustion irreversibility ranged from 27.5% at 25% load to 25.3% at 100% load in dual fuel mode and 29.8% at 25% load to 26.7% at 100% load in diesel mode. The lower combustion irreversibilities in dual fuel mode resulted from faster and more homogeneous combustion which produced less entropy and led to higher fuel conversion efficiency in dual fuel mode. Instantaneous in-cylinder exergy balances showed that in the latter portion of the combustion phase, fuel exergy is destroyed instead of being converted into piston work. Gas exchange irreversibility accounted for about 15-25% of the exergy destruction for the system with losses through the turbochargers dominating. Losses through the high pressure turbocharger account for a relatively constant 40% of the gas exchange losses across the load range while the losses through the low pressure turbocharger increased from about 25% to 45% as load increased from 25% to 100% load respectively. Exergy destruction through the compressor is higher than through the turbine for both stages. Heat dissipation exergy losses account for about 10% of the total exergy losses. The charge coolers present an opportunity to recover about 9% (or 492 kW) of the brake power at full load.
Multiple injector concepts reduce the heat losses for compression ignition engines by lower near-wall temperature gradients, a smaller wall area exposed to hot gases, and reduced near-wall velocity and turbulence. Heat loss reductions of up to 25% are claimed to be possible under some low swirl conditions by replacing a central injector with two injectors at the rim of the piston bowl. However, under conditions where swirl flow is present, the effect of multiple injectors is less clear. To answer this question, researchers at King Abdullah University of Science and Technology’s Clean Combustion Research Center carried out numerical CFD studies at different swirl ratios for a heavy-duty diesel engine [4958]. They found that while swirl increased heat losses and reduced indicated efficiency, the use of multiple injectors diminished the efficiency reduction. At a given swirl ratio two injectors with spray targeted into the swirling charge had the lowest heat losses. However, at the same swirl ratio, three injectors with spray targeted the same way had the highest indicated efficiency due to faster combustion.
Emissions
Researchers from the University of Oxford and Cambustion conducted crank-angle resolved NO, NO2, and HC measurements from a single cylinder high-speed light duty diesel engine at a variety of engine speed and load conditions with and without EGR [4972]. Fast response analyzers were used, including a fast response CLD for NO, a new laser-induced fluorescence (LIF) fast response instrument for NO2 (τ10-90 = 2 ms), and a fast FID for unburned HCs. The NOx emitted per cycle was found to be highly correlated with the peak cylinder pressure of that cycle. A variation of the NO:NO2 ratio through the engine’s exhaust stroke was also observed, indicative of in-cylinder stratification of NO and NO2. A new link between the NO:NO2 ratio and the HC emissions from an individual engine cycle was also reported—the results showed that where there are higher levels of unburned HC emissions in the first part of the exhaust stroke (blowdown), perhaps caused by injector dribble or release from crevices, the proportion of NO2 emitted from that cycle was increased. This effect was observed and analyzed across all test points and with and without EGR.
Increased stringency of NOx emission limits for small power class CHP plants (<50 kWe) in Germany have raised the possibility that the lean burn strategy may not provide sufficiently low NOx emissions. While a stoichiometric combustion process with a three-way catalyst is one option, UAS Karlsruhe, TU Braunschweig demonstrated that lean burn combined with direct water injection into the combustion chamber is alternative [4971]. The main drawbacks of water injection are a longer combustion duration and higher CO and HC emissions. In addition, the lower exhaust gas temperature causes a deterioration of the conversion of the HC molecules in the oxidation catalyst and reduces the heat recovery efficiency of the CHP-system.
* * *
The 2021 Internal Combustion Engine Fall Conference (ICEF 2021) is planned as a virtual event for October 13 – 15, 2021.
Conference website: event.asme.org/ICEF