Engine efficiency developments at Engine + Powertrain symposium
11 February 2021
The “Sustainable Internal Combustion Engine Symposium” organized by the Engine + Powertrain Technology magazine was held as a virtual event on February 3-4, 2021. Among many presentations on various IC engine related topics, several interesting talks focused on engine efficiency technologies, ranging from engine efficiency improvements, GHG emission reductions, and thermal management, to new engine concepts.
Cummins summarized their views on future heavy-duty powertrains that will require meeting lower GHG emission standards, ultra-low NOx compliance and demands of new certification requirements such as the LLC [D. Gosala]. While current diesel powertrains can be expected to meet the 2027 EPA Phase 2 GHG standards at 0.2 g/bhp-hr NOx with further optimization, Figure 1, further reductions in GHG and NOx will require some different approaches. To achieve NOx reductions such as those required by CARB and, potentially, by the US EPA for 2027 without penalizing GHG emissions, diesel powertrains will likely require technologies such as cylinder deactivation and advanced aftertreatment systems (presumably dual dosing urea SCR systems). Further reductions in GHG emissions from diesel engines beyond the 2027 requirements will require hybridization (P1 or P2 parallel hybrid). Alternatively, high efficiency stoichiometric natural gas engines with a TWC offer the potential for both low GHG and NOx without the need to adopt a hybrid powertrain. However, current challenges with the high cost of on-board fuel storage and limited refueling opportunities limit the potential of natural gas. Other options include adopting a well-to-wheels approach for GHG emissions that would allow GHG reductions possible from renewable fuels to be accounted for and the use of plug-in series hybrids that could be recharged with renewable electricity.
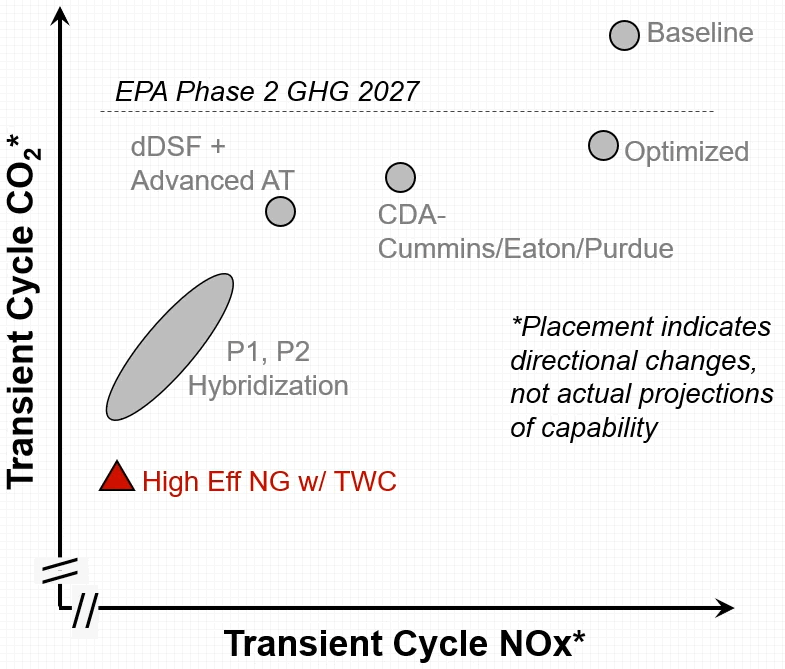
For light-duty diesel engines, Tula Technologies’ cylinder deactivation (dDSF) offers a lower cost alternative solution to thermally manage the aftertreatment system for Euro 7 vehicles during urban driving [H.-J. Schiffgens]. Compared to some other options, active thermal management with dDSF is required primarily during engine warm-up, Figure 2. Tula’s dDSF provided CO2 reductions of 7.8% and 2.4% for the urban portion of the RDE cycle and the WLTP respectively a cost of €200. While a 48V P0 hybrid with electrically heated catalyst (EHC) provided slightly higher CO2 reduction of 10% and ~3% over the same respective drive cycles, the cost was considerably higher at €700.
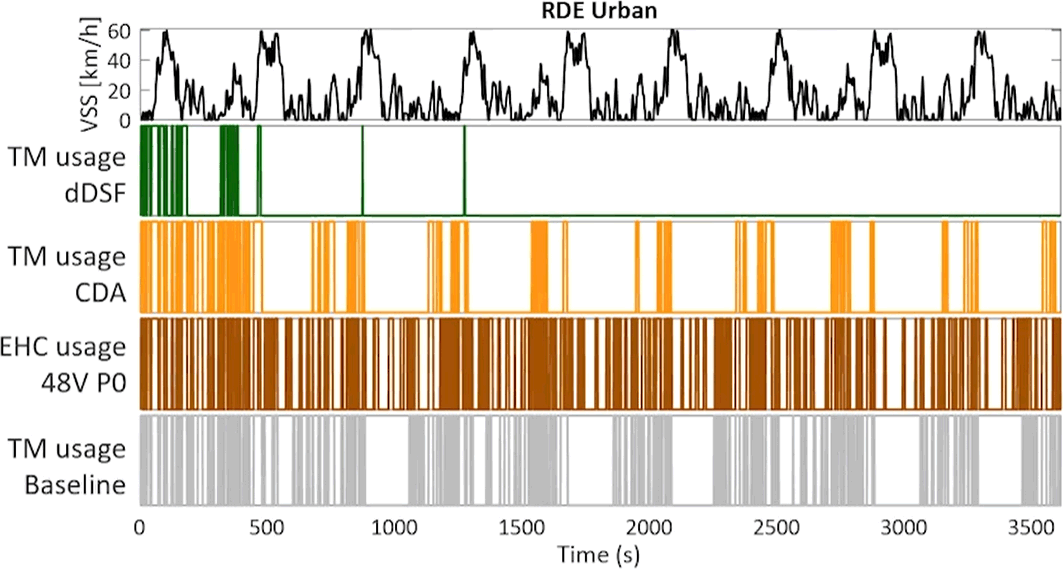
2000 kg curb weight LCV with 2.3L, 4-cylinder diesel and a “Euro 7 oriented” aftertreatment system targeting 22 mg/km NOx over the WLTP and 90 mg/km NOx over the urban portion of the RDE cycle
Ricardo presented a number of engine thermal management solutions that could be used in vehicles with a range of powertrains [C. Rouaud]. A Multi Temperature Cooling (MTC) circuit with a heat pump could allow heat to be transferred between different coolant circuits which operate at different temperatures and which would normally be separated. Heat is directed to other circuits where it can provide benefits rather than rejecting it to the environment. For example, in a standard PHEV, it is only possible to cool the battery with a chiller but by using a MTC, the battery can be both heated and cooled with a refrigerant loop heat pump. Another example is for charge air cooling—adding a second CAC that is coupled to the air conditioning chiller can enable intake air temperature to be cooled below ambient temperatures and enable increased compression ratio and a modified engine calibration that can provide fuel consumption benefits of 1-2% over the WLTP. Advanced split cooling systems that separate the block and cylinder head cooling circuits using separate coolant pumps and integrated heat storage and/or exhaust waste recovery are estimated to provide fuel consumption benefits of 0.5-1.5% over the WLTP. Lubricating oil circuits with reduced heat transfer from the oil galleries to the engine block through the use of low thermal inertia design, insulated oil galleries and hot oil storage or a dry sump can provide more rapid warm-up and reduced parasitic losses to enable a 1-2% WLTP fuel consumption benefit. Maximizing the heat transfer from the exhaust/EGR to the engine oil by placing a heat exchanger in the lubricating oil circuit after the oil pick-up or after the oil pump can provide up to 2% fuel consumption benefit on the WLTP. Engine encapsulation that aims to keep the engine hot after a long shut-down and has seen limited commercial application could provide a 1.8% WLTP benefit at an ambient temperature of 14°C. Integrating the coolant control circuit to information from the navigation system can provide predictive control functions that for heavy-duty applications that can provide fuel consumption benefits of 3-4%.
Ricardo updated progress on their Magma xEV spark ignited dedicated hybrid engine concept [R. Osborne]. Previously reported work with Geely had demonstrated a 45% BTE using a corona discharge ignition system. More recently, active and passive prechamber igniters have been shown to achieve 47% BTE at λ~2.2 and 45% BTE at λ=1.6 respectively, Figure 3. The passive prechamber spark plug was also capable of 41% BTE at λ=1.
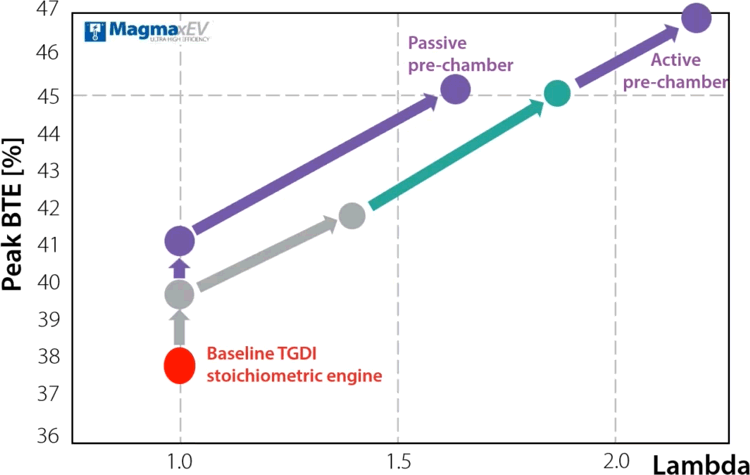
The Institute for Combustion Engines of RWTH Aachen University [C. Kayacan] reported on work carried out with FEV and others on the potential of advanced manufacturing methods and composite materials to reduce weight and provide functional improvements to a light-duty diesel engine with an aluminum block and cylinder head. In the LeiMot (Leichtbau Motor) research project, an engine block and head based on a VW EA288 diesel engine were manufactured using a laser powder bed fusion (LPBF) additive manufacturing process. Weight reduction was achieved by minimizing the material in the cylinder head and block through the use of an I-beam/shear box cylinder head design, lattice structures, stiffening ribs and lightweight grids, using an integrated liner, replacing steel caps in the block with an aluminum bedplate and replacing aluminum side covers with functional plastic covers that incorporate the water pump and coolant gallery. The LPBF process allowed optimization of the oil passengers to achieve a 20% lower pressure drop, the volume of the water jacket to be reduced for faster heat-up and a 40% lower coolant flow rate (Figure 4). The coolant flow rate reduction was enabled by reducing hot spots with artery cooling and a more even cylinder-to-cylinder temperature distribution using cross flow cooling made possible with interbore cooling passages.
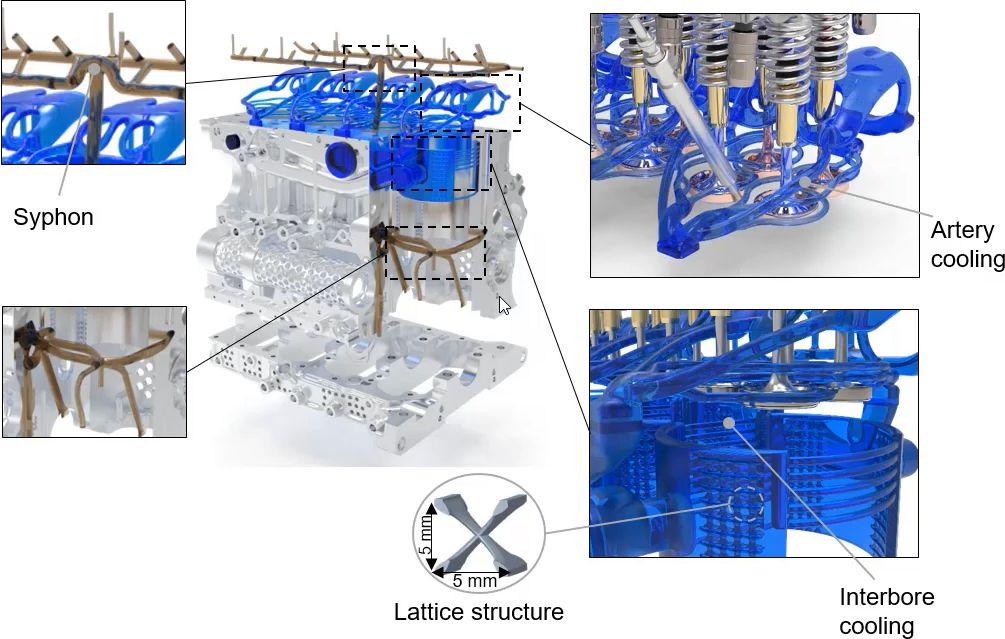
To improve cylinder liner stiffness, a lattice structure was incorporated into the water jacket that also improved coolant flow guidance, allowed a reduced wall thickness between the coolant passage and the cylinder liner surface and reduced bore distortion. Lattice elements were also used around the exhaust ports to provide thermal isolation and reduce the heat flux to the coolant by ~3%. Compared to the baseline EA 288 engine, the weight reduction for the head and block was over 20% and the coolant volume in the cylinder head was reduced by 0.5 L, Figure 5. However, additive manufacturing techniques require substantial increases in through-put to enable their application to large volume production of complex structures such as engine blocks and cylinder heads.
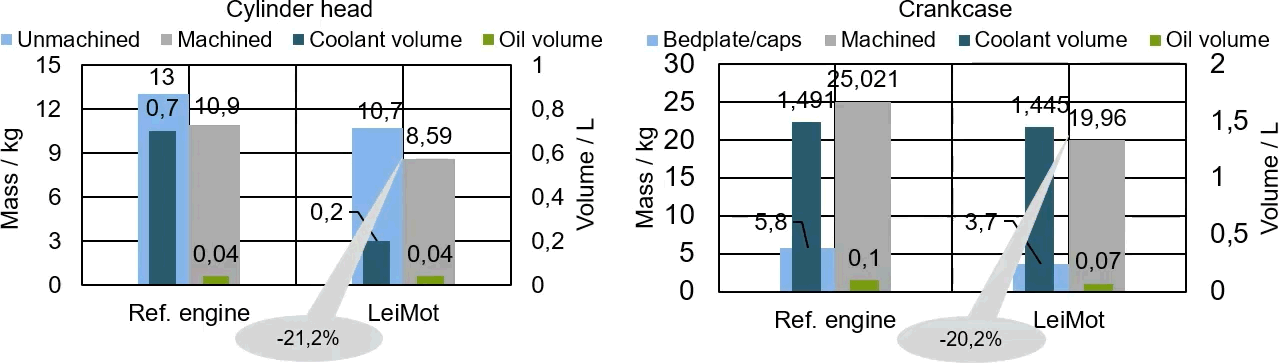
A number of alternative engine concepts were presented by Achates, Econamiq, Patentec, GlideValve and Dolphin N2. Patentec has developed an engine design that incorporates variable compression ratio (VCR) and double expansion that they refer to as the Hilberg engine. GlideValve proposes replacing poppet valves with hollow linear sliding valves with a side port that can be operated independently of the engine rotary motion and that can be actuated with a variety of means including electric, fluid or pneumatic actuators. Dolphin N2 was spun off from Ricardo in 2017 and was acquired by FPT Industrial in 2019. Their recuperated split-cycle engine for heavy-duty applications is claimed to achieve 50% BTE. If water is injected into the cold cylinder (33% water/fuel) BTE can be increased to ~55%. If liquid nitrogen is injected instead (3× liquid N2/fuel) BTE can be increased to ~60%. Single cylinder engine data suggests 27 mg/kWh NOx is possible using an SCR system with 96-98% conversion. Further improvements in engine-out NOx coupled with a >99% SCR system could lower NOx by a factor of 10. The engine can operate on a variety of fuels including diesel fuels, hydrogen and methane. Very recently, a multi-cylinder version of the engine has been started-up. Production is targeted for 2025.
Source: Sustainable IC Engine Symposium