Conference report: SAE WCX 2024 Congress
27 April 2024
The SAE WCX Congress was held on April 16-18, 2024, in Detroit, Michigan. The three-day schedule included about twenty panel discussions, 588 published technical papers, and several oral-only presentations covering all areas of automotive technology. In addition to the technical sessions, the Congress included an exhibition, keynotes by industry speakers, EV Ride & Drive, and other special events. The following summary covers two topical areas of the WCX Congress: Sustainability & Emissions and Advanced Powertrain.
Please log in to view the full version of this article (subscription required).
The sessions on engine and emission technologies opened with a panel discussion Year in Review: Emissions, Fuels & Propulsion, which built on the tradition of the Year in Review presentations given in the past years by Ameya Joshi and Tim Johnson of Corning. The topics covered by the panel included recent developments in global emission regulations and emission trends [Ameya Joshi, ClearFlame], low carbon fuels [Jim Szybist & Josh Phil, ORNL], global energy transition and the status of hybrid and electric vehicles [Addy Majewski, DieselNet], heavy-duty engines fueled by diesel, alcohols, natural gas, hydrogen, and ammonia [Paul Miles, Sandia], and heavy-duty engine emission control [Chris Sharp, SwRI]. Slides from the panel can be downloaded from qrco.de and from USCAR (courtesy of Andrea Strzelec).
Another panel discussion, Low Carbon Liquid Fuels and Decarbonizing Transportation, emphasized that low carbon fuels are the only alternative to reduce the carbon intensity of the existing fleets of internal combustion engine vehicles [Robert Wimmer, Toyota]. Energy companies evaluate a number of renewable fuel options, from renewable diesel and renewable natural gas to fuels produced using carbon capture technologies [Bob Anderson, Chevron][Tahmid Mizan, ExxonMobil]. Last year, Chevron partnered with Toyota to conduct a demonstration drive using a renewable gasoline blend in Toyota vehicles. However, due to the chemical composition of vegetable oils, the production of renewable gasoline is technically more challenging compared to renewable diesel. A key challenge faced by energy companies with regards to all low carbon fuels is the high cost. Ramping up production would require policy and regulatory incentives for lower carbon intensity fuels.
The US Environmental Protection Agency (EPA) provided an overview of the recent regulatory activity [W. Charmley - oral only]. The agency has finalized three new engine and vehicle emission rules within a period of just over one year—including the Light- & Medium-Duty Multipollutant Rule (GHG + Tier 4 criteria pollutants, MY 2027–2032+), the Heavy-Duty Low NOx Rule (MY 2027+), and the Heavy-Duty Phase 3 GHG Rule (MY 2027–2032+). While the EPA expects these regulations to result in significantly cleaner vehicles over the next decade, the new standards also represent an unprecedented challenge for engine and vehicles manufacturers. Both of the GHG regulations will require a significant degree of electrification of new vehicle fleets. For new light-duty vehicles, the EPA “Central Case” scenario predicts a 2032 mix of 56% BEVs, 13% PHEVs, 3% HEVs, and 29% ICE vehicles. For new heavy-duty vehicles, in one example technology pathway, the 2032 share of zero CO2 emission vehicles (EV & H2-ICE) would increase with vehicle weight, from 60% ZEVs in light heavy vocational vehicles to 25% in the sleeper tractor cab category.
Emission Control
The Southwest Research Institute (SwRI) provided an update on the CARB/EPA low NOx engine demonstration [paper #2024-01-2129]. Results were presented with the EPA Stage 3 (2020-2023) configuration, referred to as “System A”, aged to 800,000 miles using the SwRI Diesel Aftertreatment Accelerated Aging Cycles (DAAAC) protocol. The System A configuration includes a light-off SCR (LO-SCR) followed by a DOC/DPF unit and the main SCR catalysts. A cylinder deactivation system from Eaton was used. The key change from earlier configurations is a replacement of the Cu-based main SCR catalyst with a hybrid, Fe-Cu SCR system, in order to help reduce N2O formation over the SCR catalyst.
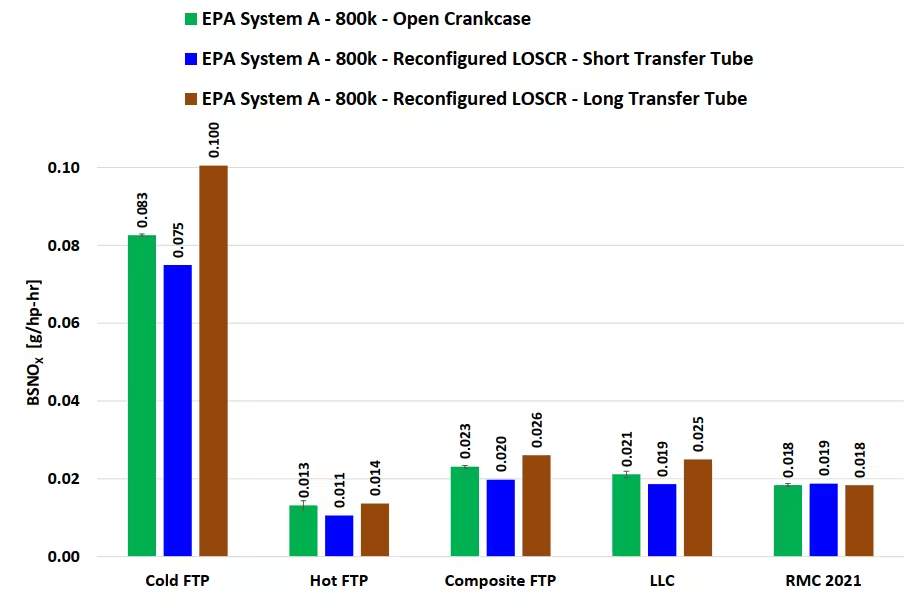
Results with open crankcase (CCV would be 6-8 mg/hp-hr lower)
Figure 1 presents NOx emission results with the laboratory System A set-up and with two packaged versions of the system. In the short configuration, the LO-SCR catalyst is placed underhood, with a short transfer tube to the underfloor catalyst (day cab vehicle). In the long configuration, all catalysts are placed underfloor, with a long transfer tube to the aftertreatment system. As apparent from Figure 1, the long transfer tube had some negative impact on NOx emissions, but the system could still meet the 2027 NOx standards, which shows that the LO-SCR catalyst does not have to be placed in the close-coupled location.
With these results, the regulatory work on the low NOx demonstration has been completed. Future work planned by the SwRI includes various optional configurations such as with an exhaust gas heater or using a vanadia-based formulation for the LO-SCR catalyst.
Another SwRI presentation discussed the CARB low NOx demonstration program for off-road engines [2024-01-2130]. The program, which builds on the low NOx demonstration for on-road engines, aims to demonstrate technologies to reduce NOx and PM emissions by 90 and 75%, respectively, from the current Tier 4 standards—i.e., to levels considered by CARB for the Tier 5 emission standards—while reducing CO2 emissions by 5-8.6%. The base engine, a 2018 John Deere 6.8 L Tier 4 final with 187 kW rating, was modified in several respects, including a modified engine calibration, new aftertreatment system with a light-off SCR catalyst, Figure 2, a new aftertreatment controller, and the addition of a closed crankcase ventilation (CCV) system. Two hardware options were evaluated, with and without cylinder deactivation. The system met the low NOx program target of 0.040 g/kWh as well as the SwRI internal development target of 0.020 g/kWh (NRTC, LLAC, and RMC test cycles).

MFC – Multi-function Catalyst (LO-SCR); zCSF = zone-coated Catalyzed Soot Filter; ASC = ammonia slip catalyst
Using the low NOx demonstrator engine (on-road version), the SwRI has also tested the impact of high biodiesel content fuels on low NOx aftertreatment [B. Zavala - oral only]. The tested fuels included biodiesel blends from 20 to 100% (B20, B50, B100) and a 50:50 blend of biodiesel and renewable diesel. While the steady-state RMC cycle results were not affected by biodiesel fuels, B50 and B100 would not meet the 2027 compliance requirements for NOx emissions. Engine calibration changes could mitigate these impacts if the engine can sense the change of fuel.
Exhaust gas thermal management, through both engine and exhaust system based measures, will play an important role in meeting future emission standards. However, there is still no indication what is the preferred approach for meeting the US EPA 2027 standards for heavy-duty engines. While the SwRI low NOx research has demonstrated that the standards can be met using dual-SCR aftertreatment combined with cylinder deactivation, engine manufacturers continue to evaluate exhaust heaters, which may be used in various alternative configurations.
Isuzu evaluated an electrically heated urea mixer (EHM™) developed by Emissol [2024-01-2377]. It was claimed that the heated mixer enabled rapid heat-up, resulting in several-fold lower tailpipe NOx and meeting ultra-stringent NOx regulations.
An aftertreatment system for the CARB Tier 5 application was also presented by FEV [2024-01-2628]. Two aftertreatment configuration were proposed—one similar to the SwRI configuration in Figure 2, including a close-coupled DOC+SCR catalyst, and another without a close-coupled SCR but with an exhaust gas heater located upstream of the main SCR catalyst.
Work was also presented on thermal management systems for light-duty gasoline engines. Bosch and Boysen have developed a Rapid Catalyst Heating System (RCH) for gasoline-fueled LEV IV/Tier 4 applications [2024-01-2378]. The RCH system utilizes a conventional port fuel injector and a fuel burner to provide upwards of 25 kW of thermal power upstream of the catalyst. A dedicated air pump is used to provide combustion air to the fuel burner.
Politecnico di Milano proposed a thermal management method utilizing post-oxidation phenomena [2024-01-2629]. The concept involves rich combustion in the cylinder (λ = 0.95) and a secondary air injection in the exhaust line. A CFD analysis was performed of the chemical reactions that are initiated in the exhaust manifold and occur all over the exhaust line. The simulation was validated through experiments on a four-cylinder, turbocharged GDI engine.
Diesel Engines
Chalmers University of Technology and Volvo Group Trucks Technology numerically investigated operating a four-stroke heavy-duty diesel engine in two-stroke mode with the help of a fully flexible variable valve actuation (VVA) system to achieve higher torque and power output. To avoid short-circuiting during the gas exchange process, deflectors were placed near the intake valve seats. A semi-circular deflector showed promise to achieve a 45% higher torque improvement compared to the baseline design without a deflector [2024-01-2686].
Work at Clemson University, Ground Vehicle Systems Center numerically investigated the use of diesel fuel injection parameters to manage piston thermal loads and maximize thermal efficiency at high load conditions. They found that later injection timings result in lower piston surface temperatures, but also lower efficiencies while reduced injection pressure at the earliest combustion phasing reduced the piston surface temperature with a slight drop in thermal efficiency [2024-01-2688].
Work on diesel engines was also covered in other papers. Isuzu Advanced Engineering Center showed that friction in the piston skirt to cylinder interface can be reduced by 30% by optimizing the cylinder bore profile [2024-01-2832]. Caterpillar confirmed that soot increases with Ducted Fuel Injection (DFI) in previous work was a result of re-entrainment of the DFI flame and the subsequent reduction of air entrainment into the on-going fuel injection around the lift-off length (LOL) [2024-01-2885].
Achates updated progress on real-world testing of their 10.6 L opposed piston (OP) engine. Compliance with EPA/CARB’s 2027 ultra low NOx requirement to 600k miles has been demonstrated and testing continues to demonstrate compliance to a full useful life of 800k miles. Ultra-low NOx is achieved with a conventional, single box aftertreatment system. Compared to a Freightliner Cascadia with a Detroit Diesel 15 (Daimler) engine, the Peterbilt 579 truck with the 10.6 L Achates engines is claimed to achieve 4% to 22% better fuel economy depending on the driving conditions. The 4% improvement is over highway driving route and the 22% improvement is over a route driven at a steady vehicle speed on secondary roads. A 16% improvement is claimed over a route consisting of a mix of downtown city and freeway driving. Initial results with hydrogen were also presented. Compression ignition of hydrogen was achieved, without the use of a spark plug, even under low speed and load conditions. Efficiency with hydrogen was “diesel-like” but NOx emissions were higher and further optimization is required so that available aftertreatment options can be used to meet regulatory limits [L. Fromm – oral only].
Clemson University and Achates Power investigated the application of an electrically assisted turbocharger (EAT), an electrified EGR pump, and a back-pressure valve (BPv) located downstream of the turbocharger to the Achates OP2S engine architecture. They found that a higher scavenging efficiency was achievable at low engine speeds as less of the fresh intake charge is short-circuited to the exhaust during the blow down process but any increase in the brake thermal efficiency is negated by the electrical energy consumed from pumping more air through the compressor. There was also an inherent challenge of decoupling airflow control from intake port pressure and optimizing scavenging at a given port pressure was difficult [2024-01-2386].
Natural Gas Engines
While it is known that natural gas engines used in medium- and heavy-truck applications would benefit from a high-tumble pent-roof combustion chamber, these engines are typically derived from higher-volume diesel counterparts, and the production volumes are insufficient to justify the amount of modification required to incorporate a pent-roof system. Southwest Research Institute investigated if it is possible to instead, maintain the flat firedeck and vertical valve orientation of the diesel engine while achieving the objectives of a pent-roof design. Numerical simulation suggested that not only is this possible, but that performance can exceed that of a pent-roof design. The new design, SwRI diamond tumble system, achieved increased burn rate and improved auto-ignition margin that allowed a compression ratio increase from the baseline 13:1 to either 14 or 14.5:1 depending on full-load timing retard decisions. A full-load thermal efficiency improvement of 0.7 to 0.8 points and part-load improvements of 1.5 to 2 points were estimated [2024-01-2115].
The effect of downsizing a heavy-duty HPDI natural gas engine for use in a hybrid powertrain was numerically investigated by Simon Fraser University, Westport Fuel Systems and the University of Alberta. They found that downsizing from a baseline 328 kW 6-cylinder engine to either a 230 kW 4- or 6-cylinder engine had a small potential benefit for engine BSFC. While engine efficiency gains at high load were offset by either higher heat losses for the downsized 6-cylinder variant or higher exhaust losses for the downsized 4-cylinder variant, a cycle-composite fuel consumption reduction of 3.5% was estimated over the WHTC for the downsized engines mainly due to fuel consumption reductions from 900 to 1000 rpm [2024-01-2114].
Alternative Fueled Engines
Methanol engines were covered in a number of papers that covered topics including improving its ignitability in CI engines through the use of ignition improvers [2024-01-2122][2024-01-2701] and pilot injections [2024-01-2119], emissions from dual fueled engines [2024-01-2364] and auto ignition characteristics in a direct-injection SI engine operated at both stoichiometric and lean (λ = 2.0) conditions [2024-01-2819].
While cetane improvers can improve the low load ignitability of methanol [2024-01-2122], Lund University and Ghent University showed that pilot injections can also be used and thus reduce the reliance on high cost cetane improver additives [2024-01-2199]. They found that a dwell time ranging from 15 to 20 CAD, combined with a pilot injection of 250 to 375 μs, at low load (5 bar IMEP/950 rpm) can lead to highly stable combustion at an intake air temperature of 61°C, about 30°C lower than the 97°C required for pure methanol when not using a pilot injection. They also noted a five-percentage point increase in low load thermal efficiency, comparable CO and HC emissions, and significantly reduced NOx emissions with pilot injections.
The Southwest Research Institute evaluated a dual fuel single cylinder research engine configured to match a 2017 Volvo D13 engine port fueled with methanol and ignited by a diesel pilot. At a low load condition, methanol substitution rates up to about 90% were possible but combustion efficiency was poor as indicated by higher CO and HC emissions. At high load, methanol substitution ratio was limited to about 47% due to increasing peak pressure rise rates. Methanol also increased formaldehyde and methane emissions, but these could possibly be mitigated with advanced injection timing or higher intake temperature [2024-01-2364].
Work covering ammonia fueled engines included retrofitting existing diesel engines with port injectors for ammonia/diesel dual fuel operation [2024-01-2368] or to operate with spark ignition using methane ammonia blends [2024-01-2371], ammonia/hydrogen blends [2024-01-2365][2024-01-2099][2024-01-2109][2024-01-2104] and ammonia/methanol blends [2024-01-2820]. Mahle Powertrain found that 60% of the speed-load map in a high tumble spark ignition engine could be covered by pure ammonia operation but other areas of the map require aid from a secondary fuel [2024-01-2815]. Hyundai Motor Company summarized the development of a direct injection ammonia fueled 4-cylinder SI engine based on a 2.5L LPG T-DI engine. Hydrogen addition, up to 25%, was used at engine speeds above about 1000 to 1500 rpm (depending on the load) to overcome the low flame propagation speed of ammonia. Engine-out ammonia emissions ranged from 3,000 to 12,000 ppm. Several aftertreatment system configurations were evaluated based on combinations of a TWC, active SCR, passive SCR and close coupled SCR. Tailpipe NOx and NH3 emissions remained above the Euro 7 engineering targets and further development work is required [2024-01-2818].
Mahle Powertrain and Liebherr detailed the development of a prototype high power, ultra-low NOx heavy-duty port-injected hydrogen engine that achieves power and torque levels consistent with the 9-liter Liebherr D964 base diesel engine it is derived from. An active pre-chamber ignition system was used to promote stable dilution limit extension, which lowers combustion temperatures and in-cylinder surface temperatures to reduce abnormal combustion. The ignition system also reduces the risk of instability-induced abnormal combustion. The additional lean stability, especially during transient operation, leads to ultra-low cycle-average NOx emissions, achieving engine-out NOx of 0.24 g/kWh on a non-road transient cycle (NRTC) with a preliminary transient calibration [2024-01-2610]. In the past, Liebherr has discussed two hydrogen engine prototypes, a PFI 6 cylinder 13.5 L engine and a 4-cylinder 9.0 L engine. The presented material appears to reflect work early in the development process as the 9.0 L engine now claims to incorporate direct injection [5605]. Other hydrogen SI engine developments included those by Ricardo [2024-01-2609] and Karlsruhe Institute of Technology [2024-01-2113].
Brunel University and Mahle Powertrain demonstrated that a DI hydrogen fuel system can have a 2% higher indicated thermal efficiency (ITE) and higher power output than a PFI fuel system because of the DI fuel system’s higher injection pressure and late injection timing during the intake stroke allows stoichiometric operation. Not only is backfire mitigated but combustion efficiency is enhanced because hydrogen is prevented from bypassing through the exhaust.
Other papers on hydrogen included the demonstration of a Superturbo on a 13 L heavy-duty hydrogen engine [2024-01-2087], the demonstration of a passive pre-chamber spark plug on a heavy-duty hydrogen engine [2024-01-2112], the effect of in-cylinder flow on fuel-air mixture formation in a medium-duty DI-SI hydrogen engine [2024-01-2117], the impact of different piston geometries on a light-duty SI hydrogen engine [2024-01-2613], hydrogen/diesel dual fuel combustion [2024-01-2363][2024-01-2367], hydrogen injection [2024-01-2616][2024-01-2617][2024-01-2615][2024-01-2623][2024-01-2693][2024-01-2687], and hydrogen-air mixing in a large-bore locomotive dual fuel engine [2024-01-2694].
Emission Control Catalysts
A study by the Aristotle University of Thessaloniki and EMISIA SA investigated conversion of methane over the three-way catalyst (TWC) [6145]. Through experiments and computer modeling, it was shown that the CH4 conversion is more complex than HC conversion in gasoline applications and cannot be explained by gasoline TWC models. At rich lambda, the main reaction pathway involves H2O via a reversible steam reforming reaction, which is favored at a reduced Pd catalyst state. Lean/rich cycling around stoichiometry was found to enable a higher CH4 oxidation, as the oxygen storage seemed to balance the individual effects of Pd oxidation and rich deactivation.
CH4 conversion in natural gas engines was also studied by Cummins, with a focus on sulfur impacts on the methane steam reforming reaction [6146]. It was found that exposure to sulfur at high temperatures under rich conditions inhibited the steam reforming reaction to a greater degree than the NOx reduction activity of the TWC. After undergoing a deSOx treatment at 600°C, NOx conversion was fully restored, while CH4 conversion did not fully recover. It was suggested that the sulfur-induced deterioration of active sites and oxygen storage capacity was linked to the formation of carbonaceous species on the catalyst surface.
The Oak Ridge National Laboratory (ORNL) investigated the effect of phosphorus derived from biofuels on emission control catalysts [T. Toops - oral only]. Phosphorus (P), derived from lubricating oil additives such as ZDDP, is a known catalyst poison. However, phosphorus in plants—and presumably in fuels such as biodiesel—exists in the form of phospholipids such as lecithin, which may affect its activity as catalyst poison. In the study, aged catalysts were tested using ultra-low sulfur diesel fuel mixed with lecithin. It was found that P significantly affected HC conversion over a DOC. Interesting results were observed with SCR catalysts (Cu/SSZ-13). Several SCR configurations were tested, including a light-duty (LD) configuration which included an upstream DOC catalyst, and a light-off SCR catalyst in heavy-duty (HD) engine system without an upstream catalyst. Adding P to fuel in the LD configuration resulted in a drastic decrease in SCR reactivity, Figure 3. Surprisingly, the LO-SCR catalyst in the HD configuration was not nearly as deactivated as the LD SCR. This suggests that lecithin-based P is likely oxidized over the DOC to a form that is more harmful for the downstream SCR.
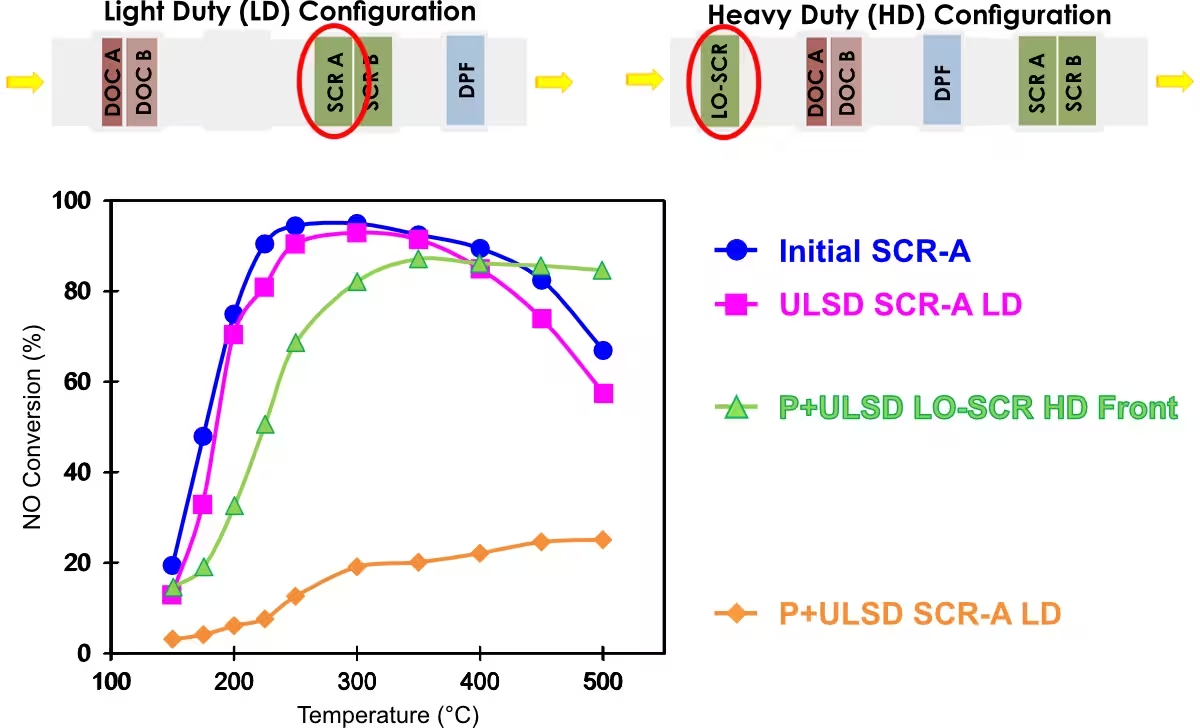
Two studies, by Cummins [6147] and by the SwRI [6148], examined the light-off behavior of biodiesel over a DOC. The results show that biodiesel is harder to light-off than diesel—a fact that may have emission compliance implications. The SwRI study found that in the transient light-off test, light-off temperature for ULSD was typically less than 225°C, while for B100 it ranged from 290°C to 330°C. Both studies concluded that biodiesel fuels have a higher light-off temperature primarily because of their higher boiling points. The lower energy content of biodiesel may present a minor secondary impact.
The Karlsruhe Institute of Technology (KIT) evaluated catalysts for the reduction of NOx emissions from lean-burn H2 engines [6149]. A catalyst system was proposed including an oxidation catalyst (OC) for tuning the NO:NO2 ratio and for H2 oxidation, followed by a vanadia based NH3-SCR catalyst. One of the key challenges was the formation of N2O over the OC at low temperatures (< 250°C)—N2O concentrations up to 50 ppm were formed in some of the experiments. While the H2-SCR process would offer a more elegant solution than NH3-SCR, it has poor selectivity and a narrow temperature range.
Fuels and Lubes
Shell looked at the effect of deposit control additives (DCA) on particulate emissions to determine if there is any merit to the argument that high doses of DCA could have detrimental effects on emissions due a direct contribution to particulates. A fleet of 7 GDI Euro 5 and Euro 6 vehicles fueled with EN228 compliant gasoline treated with a high dose of DCA were used. In the first phase of testing, the vehicles were fueled with the gasoline treated with a high dose of DCA and driven a minimum of 4750km with periodic WLTC emissions measurements to determine the potential for particulate emissions, fuel consumption and CO2 emissions reduction attributable to injector clean-up. In the second phase, a series of WLTC tests were conducted while the fuel was alternated between the high-DCA fuel and the same fuel excluding the DCA to determine the instantaneous effect of the DCA on particulate emissions. A fleet-average reduction in particulate emissions, fuel consumption and tailpipe CO2 emissions were observed with the continuous use of high-DCA fuel whereas no statistically significant differences were observed from the tests alternating between the high-DCA and unadditized fuels. They concluded that the injector cleanliness benefits of high-DCA fuel far exceeded any detriments due to the instantaneous impact of the DCA [2024-01-2127].
bp Castrol evaluated the fuel economy benefits of low viscosity engine lubricants in hybrid electric vehicles. In a conventional ICE vehicle, a lower viscosity 0W-16 lubricant provided about a 0.55% fuel economy benefit compared to a higher viscosity 0W-20 lubricant. However, when tested in two different hybrid electric vehicles, the lower viscosity oil either provided no benefit (HEV B) or increased fuel consumption by about 0.52% (HEV C). Hybrid vehicles have a wide range of engine operating strategies that may explain this variation. Less engine on time, lower oil temperatures and different engine loads may explain the lack of fuel economy differentiation. An increased number of stops and starts, increased time at engine speeds less than 650 rpm, increased fuel and water dilution and the effect of lubricant type on the dynamic behavior of the engine control system may explain the decreased fuel economy for HEV C [2024-01-2824].