Conference report: SAE WCX 2021 Digital Summit
29 April 2021
The SAE WCX 2021 Digital Summit was held on April 12-15, 2021. The event followed the virtual, online-only format introduced last year. The virtual conference included 95 live sessions—including various discussion panels, High Efficiency IC Engine Symposium sessions, and live presentations by car makers and auto industry suppliers. In addition, hundreds of pre-recorded on-demand presentations have been made available that covered all areas of automotive technology. The on-demand content will remain available on the WCX 2021 website until July 15, 2021. The following summary details a number of WCX 2020 papers on engines, engine emissions, and related technologies.
Please log in to view the full version of this article (subscription required).
The world’s governments have been adopting policy targets to reduce GHG emissions from the transportation sector and from the economy in general. These pledges envision reducing emissions by some 50% by 2030-2035, and reaching “net-zero” emissions in the 2050 timeframe. Most of these targets are political postulates, which assume continuing economic growth while underappreciating the energy and natural resource limits, and the enormous scale of the energy transition project. Discussion panels by experts in energy, fuels, and powertrain technologies provided more insight into the challenges of transitioning to low-carbon mobility, based on life cycle analysis of the underlying energy and emission impacts.
Shell [R. Cracknell] analyzed three energy transformation scenarios following the Covid-19 crisis: (1) Wealth first, focused on economic growth, (2) Security first, focused on nationalistic autonomy and self-sufficiency, and (3) Health first, with focus on human well-being. The latter scenario, dubbed Sky 1.5, could meet the 1.5°C warming target by 2100 set by the Paris Agreement, while the two other scenarios produced warming levels in excess of 2°C. Even under the Sky 1.5 scenario—the most effective decarbonization pathway—oil remains the largest source of energy in transport beyond 2050, Figure 1. As apparent from the chart, Shell expects efficiency improvements to play an important role in the decarbonization of transport.
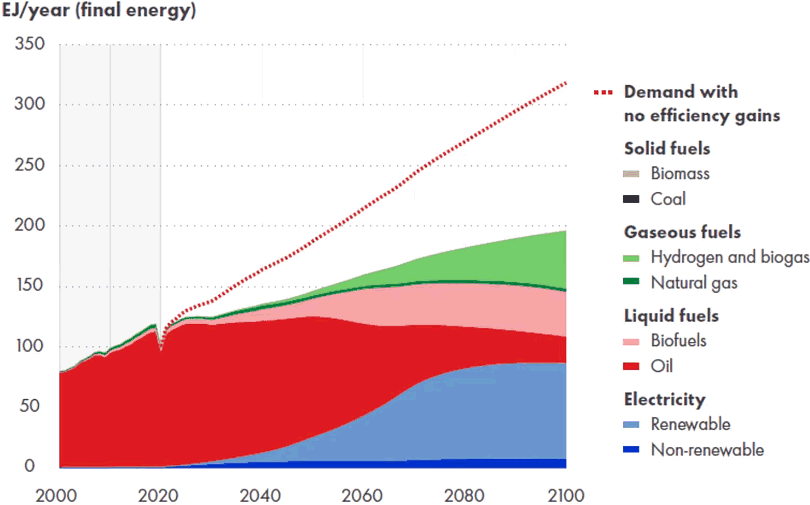
(Source: Shell Global Solutions)
A discussion panel on next generation powertrains identified a number of challenges along the way to low carbon mobility. The conception of “carbon neutral” road transport is based on the prerequisite of carbon neutral electricity generation, and includes various mixes of battery electric, hydrogen fuel cell, liquid e-fuels, and biofuel powertrains [Zissis Samaras, Aristotle University]. The liquid fuels would be used mostly in ultra low emission hybrid vehicles. There are, however, large efficiency differences between these options. Battery electric vehicles (BEV) have by far the best efficiency—their combined well-to-tank (WTT) and tank-to-wheels (TTW) efficiency is 64%, i.e., 1.57 MJ of renewable electricity is required at the point of generation to supply 1 MJ of energy to the vehicle wheels. In contrast, the efficiency of the least efficient fuel option, e-fuels manufactured via direct air capture (DAC) of CO2, is only 16%, i.e., 6.25 MJ of electricity would be needed to supply 1 MJ of energy to the wheels. Of course, e-fuels are compatible with existing engines and fuel distribution infrastructure, and could be used in heavy-duty vehicles that are hard to electrify, but in energy terms e-fuels would come with a heavy price tag. A number of further challenges were discussed in the panel presentations and in the following Q&A session:
- Electricity generation and upgrades to electrical grid—Scenarios that involve high levels of electrification of both light- and heavy-duty vehicles suggest that the European electricity generation would have to increase by some 35-50% (similar estimates exist for the United States). In scenarios with high e-fuel use, EU electricity generation would have to increase 1.4 times. While this is not realistic, e-fuel proponents suggest e-fuels could be produced in areas with more abundant renewable electricity (and water) resources, and imported into Europe.
- Battery production and resource limits—Electrification would require a rapid increase of battery production. Each 2% annual increase in electrification of US light-duty vehicle sales requires a 30 GWh/yr battery production plant. To achieve 40% of LD sales by 2035 would require 20 battery gigafactories; there are currently four in the United States [Chris Atkinson, Ohio State University]. In addition, the production of batteries and other electrification components depends on critical materials and minerals, including Li, Co, and 35 others.
- Emission effects—As the GHG effect of EVs is front-loaded, because of the large emission contribution of battery manufacturing, their overall emission effect depends on the vehicle miles traveled and on the electricity mix in the grid. A life cycle analysis (LCA) by Convergent Science [Kelly Senecal] showed that in the United States, hybrid-electric vehicles provide higher CO2 emission reductions than BEVs in 25 states under “most favorable assumptions for BEVs”, and in 44 states under “least favorable assumptions for BEVs”. Therefore, many EV policies that rely on tailpipe emissions rather than on the LCA approach will result in increased GHG emissions.
- Environmental and social justice—Realistically, low income families cannot afford electric vehicles, while most EV subsidies benefit the affluent, higher income customers who buy them. As a result, the most polluting vehicles continue to be used in poor and disadvantaged communities. There are many other ‘clean’ and ‘green’ initiatives that run contrary to the principles of social justice.
Regulatory developments and new technologies in the area of engine efficiency and emissions were discussed in the Emission Controls panel by Ameya Joshi of Corning. Among new emission regulations, the upcoming Euro 7/VII will focus on achieving ultra low emission levels under a wide range of operating conditions. This means that tighter RDE testing rules may be an important part of the regulation. In addition, the emission limits are to be tightened, and a number of new species are expected to be regulated (potentially, NH3, CH4, N2O, HCHO). Depending on the political choices by the EU regulators, the final Euro 7 regulation may be challenging for ICE powered vehicles.
In the United States, the California Air Resources Board (CARB) has adopted the Low NOx regulation for heavy-duty engines, with very challenging NOx emission limits (0.02 g/bhp-hr over the FTP), additional emission limits over the low load cycle (LLC), and significantly extended useful life periods (up to 800,000 miles). Meeting the low NOx targets will require new thermal management methods (cylinder deactivation, heated catalysts), very high SCR conversions, and dual dosing SCR configurations with very low N2O formation. A heavy-duty low NOx regulation, possibly harmonized with the CARB requirements, is also expected to be adopted at the federal level by the US EPA. For light-duty vehicles, CARB started the development of LEV IV emission standards (Advanced Clean Cars II regulation), which could potentially include a SULEV20 (NOx+NMOG = 20 mg/mi) fleet average requirement and a PM emission limit of 1 mg/mi.
GCI Engines
Gasoline compression ignition (GCI) continues to be an active area of research and is driven by considerations that include the potential for lower engine-out NOx and soot emissions and improved efficiency over diesel combustion. However, realizing these benefits is not always straightforward. Injection strategies that take advantage of gasoline’s higher volatility and potential for low-temperature combustion (LTC) seem to be effective for realizing efficiency benefits through lower heat losses, faster combustion and a higher specific heat ratio (γ). This can also avoid the need for EGR to limit NOx at some operating conditions along with the associated efficiency penalties - especially if high pressure EGR is used. The cost of these LTC approaches, however, is an increase in the complexity of controlling the combustion process and a potential for elevated HC and CO emissions. On the other hand, injection strategies that are more diesel-like may simplify the control problem and keep HC and CO low but also reduce potential benefits from GCI. A number of papers were presented that illustrate these approaches and challenges.
SwRI compared diesel and GCI operation in a single cylinder version of Volvo’s MY 2017 D13 engine as part of their internal CHEDE program [5087][5088]. Diesel operation was on ULSD and GCI on 87.8 AKI (91.5 RON) E10 gasoline with a lubricity additive. Two piston designs were evaluated; a stepped-lip piston as well as Volvo’s WAVE piston with 12 and 6 hole injector nozzles respectively. Testing and simulation work was carried out at a compression ratio of 22:1 for all cases. While both combustion systems could be operated successfully in GCI mode, they required different strategies for optimization. For example, at the A75 operating point (1200 rpm and 19 bar IMEP), the stepped lip piston required a post injection to keep unburned HC and CO emissions in check. Efficiency was comparable to conventional diesel combustion. i.e., a significant benefit in efficiency from GCI was not observed. However, further optimization could improve GCI performance. The stepped-lip piston design showed better indicated thermal efficiency (ITE) than the WAVE piston primarily due to lower heat transfer losses resulting from a lower piston surface area.
Based on previous work, Aramco Research identified that early/late IVC (EIVC/LIVC) combined with optimization of the air handling system could provide significant improvements in efficiency in a heavy-duty diesel engine operated with GCI. This approach was evaluated using simulation for a 2013 Cummins ISX15 operating with GCI [5091]. It was found that LIVC had lower boost pressure demands and lower pumping losses than EIVC. Additionally, when combined with a prototype 1-stage turbocharger with improved efficiency over the stock turbocharger, considerable improvements in BTE should result. Compared to the stock turbocharger, combining LIVC with the optimized turbocharger would increase BTE from 40.9% to 42.3% at B50 and from 41.5% to 44.3% at B75. The higher BTE resulted from reduced heat losses, reduced exhaust losses and reduced pumping losses. At the B75 operating point, the reduced pumping losses were especially dominant. Comparison to diesel operation was not presented.
Sandia National Laboratories presented work on optimizing the fuel injection strategy for their Additive Mixing Fuel Injection (AMFI) low temperature gasoline combustion (LTGC) concept for medium- and heavy-duty applications [5089]. At a part load condition of about 3-6 bar IMEP, it was demonstrated that a double injection strategy could control fuel stratification and thus combustion phasing. The timing of the first injection (70-90% of the fuel) was fixed at about 60° (early in the intake stroke) while the timing of the second injection (10-30% of the fuel) varied from 200° to 315° (early to late in the compression stroke). To maximize the range of combustion phasing control, some adjustment of EHN dosing would also be required. Earlier work with AMFI at similar loads used a single direct injection late in the compression stroke. Other work with AMFI showed that Octane Index [=RON-K(RON-MON)], a metric used to characterize autoignition as a function of engine operating conditions, had a very poor correlation with autoignition reactivity for the highly diluted and often lean conditions found with LTGC and HCCI combustion [5090].
Work on light-duty GCI at Aramco Research has focused on combustion strategy development and EGR system optimization. At least some of this work is being carried out on a 2.2 L engine similar to that previously used at Delphi. At part load conditions, the combination of a 16.3 compression ratio, new piston bowl design that reduced fuel-rich pockets near the cylinder periphery and facilitated enhanced fuel stratification distribution as well as a double injection strategy that provided PPCI diffusion combustion (double injection near the end of the compression stroke using 400 bar GDI fuel injection equipment) lead to the lowest HC, CO and soot emissions, lower boost requirements and improved efficiency. A comparison to two light-duty commercial diesel engines (BMW N57 3.0 L and Hyundai 1.6 L) at 1500 rpm/6 bar BMEP showed 86-94% lower soot emissions and 3-8% lower BSFC [5094]. Another project examined alternatives to the low-pressure EGR system used on the 2.2 L engine to reduce pumping losses and improve the transient response of boost and EGR. A hybrid HP/LP EGR system was identified as the best alternative [5093].
Other work at Aramco Research using a 2.6 L engine equipped with a 2000 bar diesel fuel injection system evaluated injection spray pattern, swirl ratio and fuel injection strategy on GCI combustion at full load (2000 rpm/23.5 bar IMEP). A zero swirl ratio combined with an 8 hole injector with total nozzle area 1.5 times that of the baseline injector and an optimized double injection strategy was found to reduce ISFC by 5.1% and soot by 50% over the baseline. Compared to the BMW N57 at the same operating condition, NOx and soot were reduced by 80% and 67% respectively. A comparison to the efficiency of the diesel engine at full load was not provided. Future work will extend the investigation to part load conditions [5092].
Hyundai-Kia America Technical Center evaluated GCI in a 2.2 L diesel engine using load sweeps at 1500 and 2000 rpm [5095]. Injection pressures during CGI up to 700 bar were used. It was found that CGI required no EGR to meet an engine-out NOx target of 5 g/kWh while with diesel, up to 10% high-pressure EGR was used. The BTE with CGI was observed to be 2.2% to 6.5% higher.
Alternative Engines
Achates updated progress on their CARB funded demonstration project [5105]. The 10.6 L engine in this project will meet the 2027 low NOx FTP emission limit and will be installed in a Peterbilt 579 tractor. Recent changes to the engine include replacing the VGT and supercharger with a SuperTurbo and Eaton EGR pump. The originally proposed aftertreatment system with a dual dosing close-coupled and underfloor SCR catalysts will be replaced with an underfloor system comprising a DOC, SCRF, SCR and ASC. Work has shown that the opposed piston engine can meet the 2027 NOx limit without a dual dosing SCR system. One benefit of the opposed piston engine is that peak exhaust temperatures can be as much as 100°C lower than with conventional four-stroke engines and can be exploited to store more ammonia on the SCR catalyst to improve NOx conversion.
Engine Systems Innovations is developing a variable displacement engine based on a nutating mechanism [5107][5108]. Simulation work on an earlier version of the design suggested improvements in part load efficiency of about 70% that translate into a fuel economy benefit of about 30%. With the nutating mechanism, use of rolling element bearings is critical to keep friction low.
Boosting
Mitsubishi Heavy Industries next generation variable geometry turbocharger will incorporate 3D vanes in the exhaust turbine [5118]. These are shaped in a way to guide the main flow towards the mid-span section of the vane, Figure 2. At small vane openings, this significantly reduces interference effects caused by leakage flow past the end of the vane and can increase turbine efficiency at low mass flows by about 5.7%.
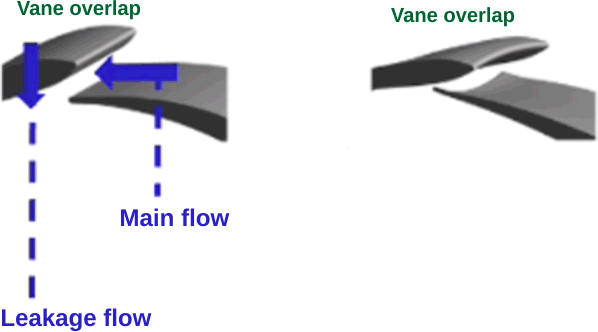
Cylinder Deactivation
Tula Technologies mDSF combines Dynamic Skip Fire with Miller cycle operation that uses an asymmetric intake valve design rather than a 2-step valve lift system commonly used for Miller cycle implementation. In each cylinder, one intake valve (Miller Intake) has a Miller cycle lift profile while the other (Power Intake) has a more conventional profile to ensure the required engine power targets can be met, Figure 3. When Miller cycle operation is required, the Power Intake valve is deactivated (Low Fire)—otherwise both valves operate (High Fire). With their 2018 VW Passat demonstration vehicle, a fuel consumption decrease of 7.8% was measured over the US city-hwy cycles and 6.0% on the WLTC representing 8.5% and 6.4% fuel economy increases. Cost for CO2 reduction is estimated at $30/%. Reductions in CO emissions were also noted due to less need for catalyst enrichment due to use of deceleration cylinder cut-out (DCCO) instead of deceleration fuel cut-out (DFCO) [5109].
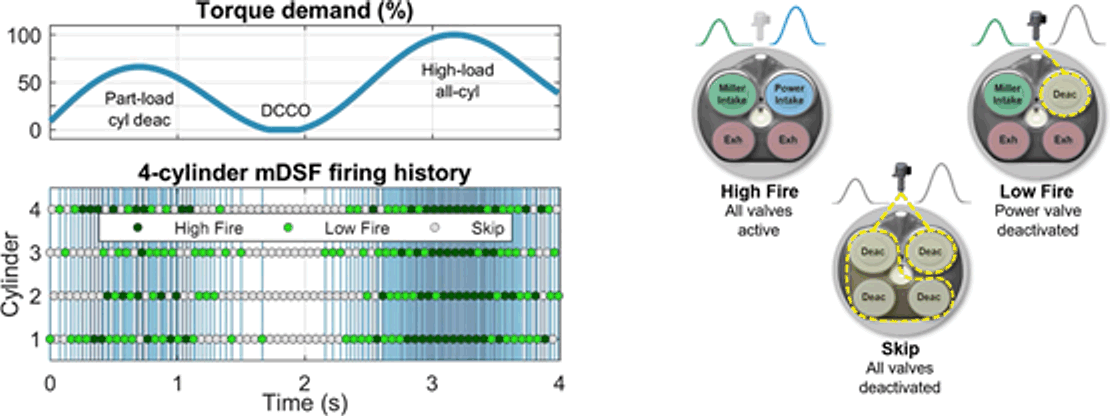
For heavy-duty diesel engines, Tula and Cummins provided vehicle simulation results for a Freightliner Cascadia with a Cummins X15 engine using dDSF. Combining dDSF with the conventional thermal management measures in the baseline engine was estimated to provide a 23% NOx and 0.8% CO2 reduction over the heavy-duty FTP and 74% NOx and 5% CO2 reduction over the LLC. If dDSF is combined with a more aggressive engine-based thermal management strategy so that CO2 emissions remain similar to the baseline engine, NOx reductions are even higher at 48% and 79% over the FTP and LLC respectively. In-use duty cycle evaluations [idle/creep, urban/transient (low), urban/transient (high) and highway] showed dDSF with the baseline thermal management strategy provided NOx reductions ranging from 34% to 96% and CO2 reductions from 0.7% to 9.4%. With regard to NVH characterization, driver’s seat vibration remained within ±0.01g for most firing densities when compared to all-cylinder operation; torsional vibration at the flywheel, transmission input and transmission output increased moderately at lower firing densities; and cabin sound pressure level remaining with ±1 dB [5110].
AVL evaluated a naturally aspirated engine concept that combined DSF with increased engine displacement, LIVC for a heavy Atkinson cycle and cooled external EGR (2.5 L, 14.0 CR PFI). Fuel consumption over the WLTC for the baseline engine (2.0 L, 11.5 CR, PFI) was 929 g, for the baseline engine with DSF was 882 g, for the upsized Atkinson cycle engine with cEGR was 921 g and for the upsized engine with cEGR and DSF was 860 g. This concept also compared favorably to some downsized and boosted engines: Honda L15B7 (895 g fuel), Ford 1.6 L Ecoboost (994 g fuel) and PSA EP6CDTX (890 g fuel) [5111].
Emission Aftertreatment
SwRI discussed the CARB Stage 3 Low NOx demonstration program that achieved NOx emission levels near the 90% reduction target (FTP/RMC NOx = 0.02 g/bhp-hr) with no adverse GHG impacts, using aftertreatment system aged to 435,000 miles [5122]. A 2017 Cummins X15 engine was used for the demonstration. Unlike the engine used in earlier stages of the program, the X15 engine did not use turbocompounding, but was fitted with additional cylinder deactivation hardware (Eaton). Figure 4 shows the dual SCR aftertreatment system developed in the project.
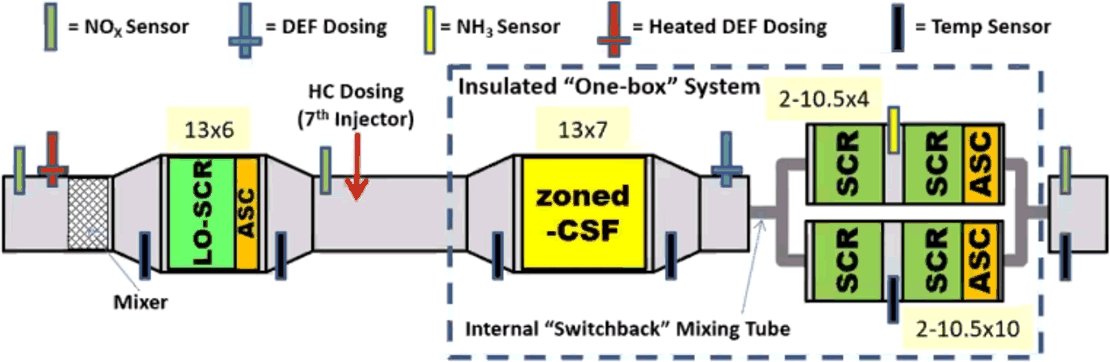
Electrically heated catalyst (EHC)—a technology that was developed in the 1990s, but has found only limited commercial use—is being reconsidered to control cold start emissions in a range of future applications, from Euro 7 to California heavy-duty low NOx. Vitesco evaluated the effectiveness of preheating a PHEV’s aftertreatment system using an EHC to reduce high-power cold-start (HPCS) emissions [5127].
A study by Umicore suggested a new catalyst approach to meet SULEV20 emission standards in gasoline vehicles [5128]. A zeolite-based HC trap was used in the close-coupled location, followed by an underfloor three-way catalyst. The aged experimental system resulted in NMHC and NOx emissions of 5 and 10 mg/mi, respectively, with CO emissions well below the 1.0 g/mi LEV III SULEV20 limit. The PGM amount in the tested system was lower than the OEM design.
While most future emission regulations increasingly focus on emission durability and in-use compliance, aftertreatment system failures may occur for reasons beyond the control of the vehicle or catalyst maker. FCA investigated a real-world aged diesel vehicle that exhibited a deterioration in tailpipe emissions [5129]. It was found that the vehicle catalysts were irreversibly damaged due to exposure to high levels of sodium and potassium. The level of Na and K contamination on the catalyst was found to be far greater than what would be expected from use of market grade diesel or biodiesel blends that adhere to ASTM specifications. It was concluded that the vehicle must have been operated using fuels that did not meet the applicable industry standards.
New developments in particulate filter technology focus on gasoline particulate filters (GPF). Current Euro 6 PN requirements are met using GPF materials with fresh filter efficiency on the order of 80%. In the expectation that future emission standards may tighten the PN requirements, new, higher efficiency GPF formulations are being developed. One example is a new Corning filter with a high PN filtration efficiency, in most cases above 90%, even in the totally fresh state and over aggressive drive cycles [5124]. This new small pore size formulation is intended for uncatalyzed GPF applications.
Other noteworthy GPF papers discussed the optimization of GPF catalyst coating intended for China 6b applications [5126], and the development of a model based engine calibration generation for GPF regeneration [5125].
It is anticipated that Euro 7 and post China 6 emission regulations will increasingly focus on the control of secondary emissions such as ammonia and nitrous oxide. Umicore investigated N2O and NH3 emissions from a variety of China 6 production gasoline vehicles over the WLTC and RTS 95 test cycles [5123]. It was found that N2O emissions were below 5 mg/km on all vehicles, well below the China 6 limit of 20 mg/km. However, NH3 emissions varied from 2 to 48 mg/km. Methods to reduce N2O and NH3 emissions were discussed from the perspective of catalyst system design.
Horiba reported on the development of an onboard emission analyzer for the measurement of NH3 and N2O emissions [5121]. The analyzer employs a newly developed absorption spectroscopy named infrared laser absorption modulation (IRLAM). A detection limit of ≤ 0.1 ppm was achieved in both NH3 and N2O measurements. A correlation test was conducted between the new, portable analyzer and a stationary quantum cascade laser-based emission analyzer on an engine test bench.