Conference report: ASME Internal Combustion Engine Fall Conference (ICEF 2021)
29 October 2021
The 2021 ASME Internal Combustion Engine Fall Technical Conference (ICEF) was held on October 13-15, 2021 as a virtual event. The technical program included four keynote speeches and two panel discussions, as well as 72 technical papers grouped in seven tracks covering (1) Advanced Combustion, (2) Engine Design and Mechanical Development, (3) Fuel Injection and Sprays, (4) Fuels, (5) Large Bore Engines, (6) Numerical Simulation, and (7) Powertrain and Emissions Systems.
Decarbonization of Transport
US president Biden has issued an Executive Order that sets a policy goal to “put the United States on a path to achieve net-zero emissions, economy-wide, by no later than 2050”. This goal poses a number of challenges, which are particularly severe in case of ‘hard-to-electrify’ heavy-duty powertrains. A panel discussion titled “Towards Decarbonizing Heavy-Duty Freight Transportation” looked into future powertrain and fuel options that are envisioned for heavy-duty trucks.
Decarbonizing the transportation sector, which contributes 33% of US GHG emissions, would require dramatic changes in vehicles and the transportation infrastructure system. These changes should have an impact already by 2035, to allow for fleet turnover [M. Weismiller, US DOE]. The envisioned powertrain technology depends on the market segment: battery electric vehicles with clean grid are envisioned for passenger cars and light commercial vehicles; flight and large ocean-going vessels would require liquid fuels; long-haul freight, rail, construction, and agriculture would likely require a mix of ‘net-zero’ CO2 gaseous and liquid fuels and fuel cells or ICEs as conversion devices. Some of the future fuels would be derived from biomass, however, the biofuel potential is way too small to replace the current US fossil fuel consumption. Therefore, most of the future fuels are envisioned to be electro-fuels—H2 and/or liquid—produced using low carbon electricity. The latter prerequisite hinges on another policy goal of the current US administration—that of achieving 100% non-fossil electricity grid by 2035.
The US DOE battery and electrification program has a goal to reduce the cost of electric vehicle batteries to less than $100/kWh, decrease charge time to 15 minutes, and to enable a high power density 100 kW peak electric traction drive at a cost of $6/kW.
Considering the US policy goals, as well as climate policies in the EU and some other countries, engine and vehicle manufacturers expect future regulatory proposals to be technology forcing toward zero tailpipe emission powertrains such as electric and fuel cell vehicles, following the trend set by some clean vehicle rules already adopted in California. Most truck manufacturers, including Volvo [J. Li] and Navistar [J. Cigler], already offer battery electric versions of their city delivery vehicles and school buses, and expect electric and fuel cell regional haul tractors to be available within a few years. However, the current EV technology is not yet ready for the mass migration towards electrification, and numerous challenges remain—such as those related to vehicle range and charging time, charging infrastructure, system costs, and customer acceptance. Hydrogen fuel trucks face an even longer path toward commercialization, with a long list of outstanding technical and infrastructure concerns.
The current US decarbonization policies (as well as those in the EU) rest on the assumption that sufficient amounts of non-fossil fuel electricity will be available to power battery electric vehicles and to manufacture low-carbon electro-fuels—notwithstanding their inferior energy efficiency—and that the necessary electro-fuels manufacturing capacity will be indeed developed within the desired time frame. As already mentioned, the current US administration has goals of 100% clean electricity by 2035 and net-zero carbon emissions by 2050. However, recent US EIA projections for 2050 show that the United States is not on track to meet these goals. Based on the EIA projection, transportation alone will add more than 50 Gt of CO2 to the atmosphere unless significant interventions are taken. In a keynote talk, Dr. James P. Szybist, Head of the Propulsion Science Section at Oak Ridge National Laboratory, examined some of the options that could be used to help meet these goals.
Electrification combined with clean electricity is assumed as the most likely option to decarbonize light-duty and some medium and heavy-duty vehicles. On the other hand, there remain many applications, especially those for which the vehicles are heavy and the distances traveled large, that will not be easy to electrify. Examples include long-haul transport, rail, marine, and aviation. While some of these could use fuel cells, many will still require the use of an internal combustion engine burning a low-carbon liquid fuel. While rail electrification is technically feasible, the current railroad usage and ownership models in the US make electrification challenging. These hard to electrify applications is where future engine research should be focused.
Many renewable fuels are available or are being developed that could be used in these ICE applications, however, it is not practical to have a wide range of fuel types. While a single fuel that could be used in all the applications is most desirable, limiting the offerings to only a few may be required.
Desirable characteristics of Low Lifecycle Carbon Fuels include high production efficiency, scalability and sustainability. Energy will continue to be a valuable resource and maximizing production efficiency and thus the energy content of the feedstocks in the final product is essential. Oxygen removal from feedstock is not always desirable since this step can be very energy intensive. Production efficiency considerations may also affect the viability of some options that appear to be a good fit for today’s engines and infrastructure. Since the energy demand of transportation is enormous, fuels need to be ubiquitous and fungible – not necessarily fungible with the current technology but fungible with whatever is coming. To be sustainable, they need to be so from the community, energy source and land and water use perspectives.
Some options that are currently thought to meet these requirements include ethanol, methanol, hydrogen and ammonia. Ethanol is currently a commercial fuel that is claimed to have less than 40% of the lifecycle carbon emissions of gasoline. Further decarbonization could be possible through carbon capture and sequestration. Methanol, hydrogen and ammonia all have potential production routes that could avoid carbon emissions. While ethanol and methanol are resistant to autoignition, this could be addressed with additives, dual fuel pilot ignition or pre-chamber ignition. Other challenges that would need to be addressed include aldehyde emissions, engine durability related to oil dilution and fuel quality challenges arising from impurities and water. Challenges with hydrogen include knock, surface ignition, hardware durability, lean NOx aftertreatment and power density. With ammonia, toxicity, NOx emissions and corrosion are challenges.
While electrification of the light-duty fleet, urban buses and some medium-duty applications is progressing, several factors must “go right” in order to realize significant carbon emission reductions. Currently, EVs only represent a small portion of new car sales and few customers have experienced them. The proportion needs to increase significantly and customer experience must remain positive. While electricity production is decarbonizing, it is unclear whether full decarbonization will happen by 2035. Battery material sources, recycling and manufacturing must combine to ensure sufficient supply of key materials. Finally, the charging infrastructure must continue to grow at a suitable rate.
Prof. Federico Millo, Politecnico di Torino, made the case for hydrogen as an engine fuel in his keynote talk. Key technologies that require development to make this a reality include high density on-board storage, several key engine technologies and suitable aftertreatment systems.
High density hydrogen storage remains a significant challenge. Gaseous storage is still the primary option that is commercially available but in the longer term, cryogenic or chemical storage would offer higher storage density and lower storage costs.
Key engine technologies that require development include boosting systems, fuel injection, avoiding pre-ignition and suitable materials. Two-stage boosting systems that efficiently provide the high air flow and EGR requirements are essential to ensuring competitive BMEPs and low engine-out NOx emissions. Direct injection of hydrogen after IVC would help limit boost requirements while providing high power density and avoiding the risk of backfire. Pre-ignition of hydrogen is a significant challenge due to its low ignition energy, wide flammability limits and rapid combustion rate. Hot surfaces and uncontrolled lubrication oil consumption must be avoided. Hydrogen embrittlement of typical ICE materials requires new design approaches and alternative materials.
Emissions of NOx are the primary emissions of concern related to hydrogen engines and suitable aftertreatment systems will be required. H2-SCR is one option that could avoid the need for urea but requires further development. Other emissions that would need to be considered and that arise from the combustion of lubricating oil include HC, CO and PN. Of these, PN may be of most concern and could require exhaust filtration. Ammonia emissions could also be possible under conditions that generate rich combustion.
In a keynote focusing on light-duty vehicles, Dr. Elana Chapman, Senior Fuels/Biofuels Engineer at GM made the case that while light-duty vehicles are transitioning to electric, this transition will take decades and managing carbon emissions during the transition is important. Since current transportation energy use is dominated by light-duty vehicles burning gasoline, a suitable low-carbon fuel is required to accelerate GHG reductions during the transition. Key enablers include a national low carbon fuel standard and net-zero-carbon fuels.
A national low carbon fuel standard would provide pathways to low carbon fuels including “drop in” fuels for the legacy fleet. Drop-in fuels would be compatible with existing vehicles and retail stations and would meet specifications for current market fuels. The drop-in fuels would not only have low lifecycle carbon emissions, they should also enable further improvements in engine efficiency.
The current trend is to use downsized boosted gasoline engines and these engines greatly benefit from high RON, high sensitivity gasoline fuel. There are also significant opportunities to further improve these engines with lower fuel sulfur and lower regional variations in fuel properties. Also, the role of lube oil, additives and/or combustion chamber deposits in causing LSPI needs to be resolved. Desirable fuel properties for these engines include: minimum RON of 100, a sensitivity (i.e., RON-MON) greater than 12, maximum sulfur of 10 ppm, reduced variation in the drivability index (DI), a particulate matter index (PMI) below 1.5 and, heat of vaporization (HoV) no less than current levels.
Ammonia is currently being widely promoted as an alternative fuel, especially for marine applications. However, very little useful information on the detailed emission characteristics is available. This is especially the case for unburned ammonia which is toxic and N2O which is a powerful greenhouse gas. Combustion characteristics of ammonia such as a high ignition temperature (924 K vs 520-560 K for diesel) and low flame speed (0.15 m/s vs 43-45 m/s for diesel) could lead to significant quantities of unburned ammonia in the exhaust. Researchers at Japan’s National Maritime Research Institute have been investigating this issue for some time. Using a small single cylinder diesel engine operated at a BMEP of about 600 kPa using port injected ammonia ignited by a diesel pilot, they investigated the effect of several combustion strategies on emissions. With a conventional diesel pilot near TDC, about 15% of the ammonia escaped unburned while CO2-equivalent GHG emissions where reduced 20% (623 g/kWh) relative to diesel-only (~780 g/kWh) for an ammonia ratio of 46% For an early diesel pilot strategy using an ammonia ratio of 56%, unburned ammonia decreased to about 2-4% while CO2-equivalent GHG emissions were about 416g/kWh (46% lower than for diesel). The full CO2 reduction potential of ammonia was not realized primarily due to N2O emission [5230].
FEV evaluated hybrid, electric and fuel cell powertrain options for Class 6-7 urban truck application. After examining a range of hybrid powertrain options, they selected a 48V P3 configuration as offering the most favorable total cost of ownership over 8 years/192,000 miles among the different hybrid options. This hybrid configuration was then compared to battery electric, fuel cell and a range extended EV configuration operated with several different fuel options. Compared to the baseline diesel truck, all of the configurations provided sufficient fuel consumption reductions to meet upcoming GHG requirements but at widely varying total ownership costs. The range extended EV with a natural gas engine provided the lowest cost of ownership at $165,000 followed closely by the 48 V P3 hybrid at $167,000. The ownership cost of the baseline diesel truck was $180,000. While the battery electric options provided very high fuel consumption reductions, the cost of ownership was highest at $207,000 to $325,000 depending upon the driving range [5231].
SuperTruck Program
During the decarbonization discussion panel, Volvo [J. Li], Cummins [D. Mohr], Paccar [M. Meijer], and Navistar [J. Cigler] also provided a brief update on their SuperTruck 2 projects (see our AMR summary of July 2021 for more SuperTruck coverage).
All engine manufacturers have reached a ~51% brake thermal efficiency (BTE) using essentially similar mix of engine technologies. These include friction reduction, optimized combustion with high compression ratios and high peak cylinder pressures, 48 V hybrid systems, electric pumps and fans, optimized pumping system (EGR, turbo), and optimized aftertreatment, in some cases (Volvo) with an electrically heated catalyst. The combination of technologies used by Volvo and their contribution to BTE improvement is shown in Figure 1.
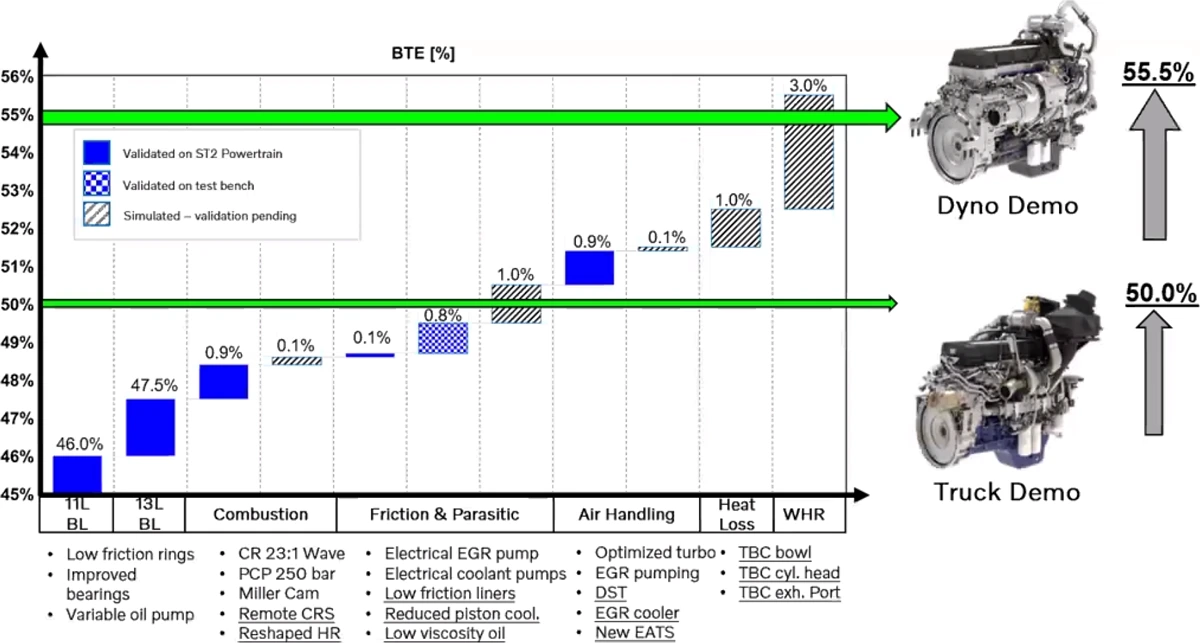
Waste heat recovery (WHR)—typically a dual-loop organic Rankine cycle (ORC) system—is necessary to reach the SuperTruck 2 target of 55% BTE. The WHR provides a BTE benefit of around 3-4 percentage points. In the case of Cummins, who already demonstrated a 55% BTE engine (some of the other manufacturers’ results are still based on simulation), the WHR system provided a 4.4% BTE benefit. The Cummins WHR system includes a high and low pressure loop, and extracts heat from the coolant, EGR, and from the exhaust. Cummins projects a 170% freight efficiency improvement (ton-miles per gallon vs a 2009 baseline) in their SuperTruck 2 prototype.
Low NOx Heavy-Duty Diesel Engines
In the second panel discussion, titled “Pathways to Achieve Ultra-Low NOx Emissions”, Chris Sharp of the SwRI presented an update on the demonstration efforts towards the California 2027 low NOx targets for heavy-duty engines. As reported at the recent CLEERS Workshop, the engine with a dual-stage SCR emission system aged over an accelerated aging cycle to 435,000 miles achieved 0.02 g/bhp-hr NOx over the FTP test cycle—a numerical equivalent of the applicable NOx emission standard, but without any engineering margin. Now, new results were presented with the aftertreatment system aged to 600,000 miles. NOx emissions of 0.027 g/bhp-hr were achieved over the FTP cycle. While this is below the 600 k miles NOx standard of 0.035 g/bhp-hr, an ongoing analysis will determine if the engineering margin is sufficient. NOx results over the LLC test cycle were well below the applicable limits at both durability points (435 and 600 k miles). In-use emissions, evaluated using the moving average window (MAW) method, met CARB 2027 requirements, but fell short of meeting the 2030 standards.
Future plans include continued aging to 800,000 miles and testing over regulatory and field cycles, testing at low ambient temperatures and with wind, and further technology refinement to simplify the system and reduce the catalyst volumes and space requirements. The researchers hope to further improve NOx performance through continuing refinement of the control algorithm, and an updated desulfation strategy of the close-coupled SCR catalyst. In the area of emission measurement, the project will look into PEMS variability at low NOx levels, and will examine sensor-based measurements for potential future on-board monitoring (OBM).
Among the key changes to be brought by the CARB 2024/2027 low NOx emission standards is an extension of the emission durability requirements. For the heavy heavy-duty engine category, the full useful life period has been nearly doubled, from 435,000 miles to 800,000 miles. To assess the long term durability of low NOx aftertreatment systems, accelerated aging protocols are urgently needed that would capture the same type and frequency of failures that are observed in real world operation of heavy-duty engines [H. Chen, ORNL]. Field aging over 800,000 miles can be extremely time consuming and costly—it would not be practical for emission certification or for development purposes. Validation of diesel aftertreatment accelerated aging protocols is being conducted at the SwRI, as an effort related to the low NOx engine demonstration.
Challenges that CARB’s low NOx regulation and the anticipated EPA’s Clean Truck Initiative (CTI) raise for manufacturers were summarized in a keynote by Cynthia Webb, Director of Regulatory Technology at the PACCAR Technical Center.
For regulatory compliance on the test cycles, the low load cycle that these legislative packages introduce is characterized by low exhaust temperature that will require measures to keep the aftertreatment system warm and low temperature urea dosing. The lower NOx limit over the FTP will require rapid warm-up after a cold start, introduces control precision and catalyst space velocity challenges as well as introducing the need for catalysts that have a low response to aging. The low temperature challenges may see increased use of fuel burners or electric heaters as well as close-coupled SCR catalysts and substrates with low “thermal mass”.
With respect to GHGs, the aftertreatment systems will create back pressure challenges and require higher power input for thermal management that will create an energy integration challenge. To offset the increased energy demand of the aftertreatment system, options such as electrified accessories, cylinder deactivation, regenerative technologies and larger batteries could be used.
Once the engines are in the field, extended warranty/FUL challenges will arise that will require increased durability, the possibility of additional aftertreatment system maintenance intervals and require accelerated aging protocols. The warranty costs are a significant unknown. If there were no new technologies added to the vehicle, the cost of additional warranty coverage could be reasonably predicted. However, as new hardware and strategies are added to comply with lower emission standards, risks from longer warranties are relatively unknown and can only be determined through application. Any errors in estimating durability of new technologies could lead to costly hardware corrections in the field.
The compliance (or engineering) margin allows factors that can have some variability to be accommodated while still ensuring emissions compliance at FUL. Figure 2(a) shows the compliance margin at FUL of the current technology. As FUL is extended and if aging continues at the same rate and no additional measures to reduce emissions are taken, the compliance margin decreases at the extended FUL, Figure 2(b). A smaller compliance margin increases the risk of emission exceedances and the need for recalls and field hardware replacements. If the emission limit is also decreased, the compliance margin can decrease to very small values that further increase the warranty risk even if very low emissions prior to aging are demonstrated, Figure 2(c).
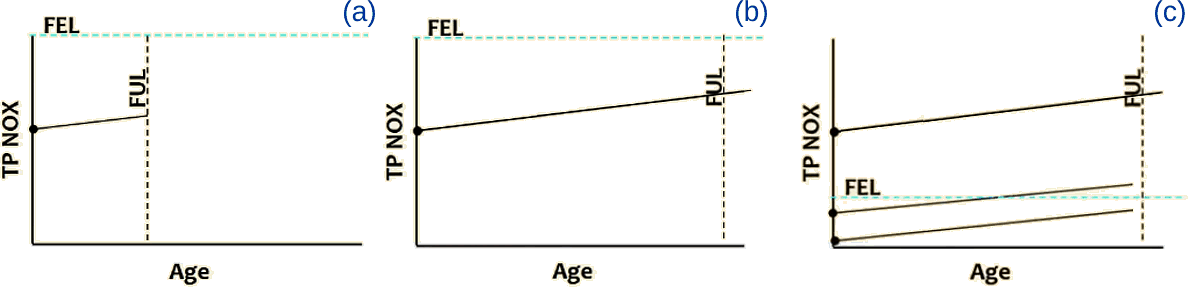
In-use compliance challenges will arise from the need to comply over an expanded compliance boundary (beyond the current NTE limits) and over non-specific drive cycles, the new 3-bin moving average window (3-BMAW) method of in-use PEMS testing, PEMS measurement accuracy and OBD detection gaps.
With regards to PEMS measurement accuracy, the 3-BMAW approach uses a multiplicative conformity factor of 2.0 while the current PEMS measurement allowance is additive. As the emission limit becomes lower, a multiplicative factor implies the PEMS system becomes more accurate which is clearly not the case.
An OBD detection gap arises from the capability of current NOx sensors and the lower OBD threshold. Meeting the lower NOx limits will require average exhaust NOx concentrations below about 5 ppm. To reliably measure these requires a NOx sensor with accuracies of +/- 1 ppm in the 0 to 10 ppm range. Such sensors are not currently available. Current sensors are about 35% accurate in the low ppm range. Thus, there can be a significant shift in the sensor output that might still be within the accuracy of the sensor and will not be detectable. Attempting to detect sensor errors that are below the sensor accuracy would result in a high level of false failures. Thus, current NOx sensor technology leaves a large gap between the OBD detection limit (10 x in-use) and the in-use OBD threshold (2 × FEL) that would allow emissions to exceed the in-use standard while the MIL remains off and could result in recalls for vehicles that have no detectable faults.
Achates provided an update on their CARB funded demonstration project developing a 10.6 L opposed piston diesel engine meeting CARB 2027 emission limits for a Class 8 tractor. Since the last update, The aftertreatment system has been modified and now incorporates a DPF followed by two SCR bricks rather than the SCRF followed by a single SCR brick used previously. A DOC and ASC are still used. Emission results with the earlier system using an SCRF showed combined cycle tailpipe NOx of 0.016 g/bhp-hr (0.067 g/bhp-hr cold/0.008 g/bhp-hr hot). While FTP results with the updated aftertreatment system have yet to be confirmed, they are estimated to be 0.007 g/bhp-hr NOx and 465 g/bhp-hr CO2 [5232].
Engine Combustion and Emission Research
West Virginia University investigated the potential of combined heat and power options to reduce the energy consumption of shale gas drilling operations. On average, diesel engines consume 6 million MJ/well, while natural gas engines consume 11 million MJ/well with the difference attributable primarily to engine efficiency differences. In cold weather, boilers are used to prevent freezing and can consume about 60,000 MJ/24h of operation. By utilizing waste exhaust heat from the engines, the boiler could potentially be eliminated and by additionally including a hybrid module with sufficiently large battery pack (584 kWh for this study), it may be possible to operate fewer engines at higher efficiency. With the diesel engine, exhaust heat alone was insufficient to meet the heat demand under all the test conditions and additional coolant heat recovery was required. The natural gas engines provide sufficient exhaust heat. With the diesel engines, the payback period for the CHP configuration without the hybrid module was estimated to be 220 days of boiler operation while adding the hybrid module increased it to 257 days of boiler operation. The corresponding values with the natural gas engines were 419 and 592 days of boiler activity respectively [5233].
Aramco provided an update on their heavy-duty GCI work based on a Cummins 15 L engine. As noted last year, further air-handling system development would be beneficial. To this end, the effect of Millerization combined with an e-compressor at mid-to-high loads was investigated numerically for its ability to lower effective compression ratio at these loads and enhance the benefits of GCI. With Miller timing, the stock turbo is unable to meet the AFR target and additionally incurs a high PMEP penalty. Combining the stock turbo with an e-compressor extends the AFR limit and improves PMEP but potential BSFC benefits are negated by the power requirements of the e-compressor. While a prototype high efficiency turbo can provide sufficient performance up to about 4 bar IMEP, PMEP increases rapidly at higher loads. However, when the high efficiency turbo is combined with an e-compressor, the PMEP above 4 bar IMEP can be reduced significantly to realize a BSFC benefit of about 2% [5235].
Woodward presented work on using RCCI combustion to achieve low methane slip with low pressure dual fuel combustion. Methane slip from conventional low pressure dual fuel combustion can be a significant challenge. By applying RCCI combustion using port injected natural gas, an early diesel pilot (just after IVC) and active combustion control with a pressure sensor, methane emissions of 1.0 g/kWh or less and NOx emissions of 1.8 g/kWh or less were shown to be possible up to 14 bar IMEP. RCCI combustion also improved indicated efficiency up to 8% relative to diesel. The improvements in efficiency and low methane emissions translate into a 20-28% GHG benefit for the RCCI engine in the load range of 8-14 bar IMEP. The proportion of diesel fuel required for RCCI combustion was unclear. The engine is currently load limited to 14 bar IMEP due to peak cylinder pressure [5236].
The US EPA presented work that characterized benefits and challenges of applying a European series production (MY 2019) catalyzed gasoline particulate filter (GPF) to a US Tier 2 turbocharged light duty truck (MY 2011 3.5 L Ecoboost Ford F150) in the underfloor location. The lightly loaded (0.1 to 0.4 g/L of soot) underfloor GPF achieved 85-99% reduction in PM mass, 98.5-100.0% reduction in EC, and 65-91% reduction in filter-collected OC, depending on test cycle. Cycle average pressure drop across the GPF ranged from 1.25 kPa in the 4-phase FTP to 4.64 kPa in the US06 but did not affect BTE or CO2 emissions in a measurable way in any test cycle [5234].
Current NOx sensors have the drawback of being cross sensitive to ammonia that makes accurate measurements of tailpipe NOx for control and OBD purposes subject to potential error. While numerous correction approaches have been developed, there is a need for further improvements. Universitat Politècnica de València presented an approach that uses a control-oriented ammonia slip catalyst (ASC) model to predict NH3 and NOx exhaust tailpipe emissions using NOx and NH3 emissions downstream the SCR catalyst as inputs. The approach also estimates the tailpipe NOx sensor cell temperature in order to determine a cross-sensitivity factor. The approach was validated with a Euro 6c diesel passenger car over the WLTC using several different urea dosing strategies and showed the ability to estimate tailpipe NOx and NH3 emissions with reasonable accuracy without the need for a physical NH3 sensor [5229].
* * *
The 2022 Internal Combustion Engine Fall Conference (ICEF 2022) is planned as an in-person event, to take place on October 23-26, 2022 in Indianapolis, Indiana.
Conference website: event.asme.org/ICEF