Conference report: SAE HDD Sustainable Transport Symposium
20 May 2023
The 2023 SAE Heavy-Duty Diesel Sustainable Transport Symposium was held on May 3-4, 2023 at the Chalmers Conference Centre in Gothenburg, Sweden. The HDD Symposium—then called Heavy-Duty Diesel Emissions Control Symposium—had been a biennial event last held in 2018. The events planned for 2020 and 2021 were canceled due to Covid-19-related restrictions. DieselNet reported on the HDD Symposium held in 2018 and in 2016.
Please log in to view the full version of this article (subscription required).
This year, the HDD Symposium included 23 technical presentations and a panel discussion on sustainable transportation. Presentations covered regulatory developments and emission technology challenges related to Euro VII and US EPA 2027 emission regulations. Under the sustainability label, the second day of the Symposium was devoted to low-carbon powertrain strategies for future heavy-duty vehicles. The event was attended by 156 registrants from 19 countries.
The Symposium opened with a keynote by Lars Stenqvist, Chief Technology Officer, Volvo Group, who emphasized the company’s commitment to reduce GHG emissions from their trucks—Volvo has a goal to produce only fossil-free vehicles from 2040. However, there is no single powertrain technology, or a ‘silver bullet’ solution, that could provide an adequate replacement for the petroleum-fueled internal combustion engine. Volvo expects their future trucks will utilize a mix of powertrains, including battery electric vehicles (BEV), fuel-cell electric vehicles (FCEV) and internal combustion engines (ICE)—to be fueled by fossil-free renewable fuels and green hydrogen.
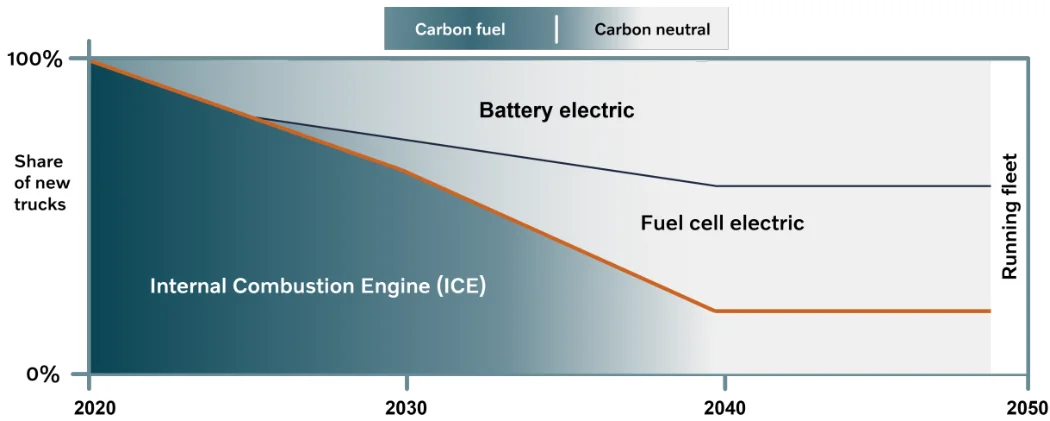
Volvo already offers battery electric trucks, but considers fuel cell and ICE powertrains for many applications. The development of fuel cell powertrains is challenging, due to the complexity of the system and heat generation, which requires sophisticated thermal management methods. Therefore, Volvo continues to invest in internal combustion engines, including hydrogen combustion engines.
Regulations & Technology
The first technical session covered the challenges posed by new emission standards, GHG regulations, and zero-emission vehicle mandates. Ricardo Suarez Bertoa of the European Commission’s Joint Research Council (JRC) discussed the proposed Euro 7/VII emission standards, which would require a 56% NOx emission reduction from heavy-duty vehicles, compared to Euro VI. Other important changes include more stringent PN limits, new regulated species (including N2O), changes to RDE testing conditions for heavy-duty vehicles, and first ever rules for tire and brake wear particle emissions. The ongoing Euro VII work includes durability multiplier for additional lifetime, battery durability requirements, onboard monitoring (OBM) system, and tests for brake particle emissions and tire abrasion.
The California Air Resources Board [S. Vergis] provided a summary of California zero emission vehicle (ZEV) requirements for heavy-duty trucks. The Advanced Clean Truck (ACT) regulation imposes ZEV mandates on vehicle manufacturers, as a minimum percentage of annual sales, starting from 2024. From 2035, ZEVs must represent 55% of Class 2b-3, 75% of Class 4-8, and 40% of Class 7-8 trucks. A recently adopted companion rule, the Advanced Clean Fleets (ACF) regulation, imposes ZEV requirements on California vehicle fleets to ensure sufficient demand for ZEV trucks. The ACF rule also includes a requirement that, starting from 2036, all Class 2b-8 vehicles sold in California must be ZEVs.
Ameya Joshi of Corning talked about the emission technologies for meeting the upcoming regulations, including Euro VII and US 2027 emission standards, as well as future decarbonization targets for heavy-duty vehicle fleets such as the recently proposed EPA Phase 3 GHG standards for heavy-duty vehicles. Meeting the Euro VII / US 2027 NOx standards will likely require the addition of a close-coupled SCR catalyst and advanced thermal management technologies—cylinder deactivation, electrically heated catalysts, or heated urea dosing. Another challenge is presented by the proposed Euro VII PN limits, which will require particulate filters of improved filtration efficiency or else the use of a secondary filter to control urea particles emitted from the SCR system.
Four types of propulsion technology are being considered to reduce carbon emissions from commercial vehicles [A. Walker, Johnson Matthey]. Each technology option comes with certain advantages and drawbacks.
Technology | Advantages | Drawbacks |
---|---|---|
Battery Electric | Very efficient use of renewable energy Zero emission at tailpipe TCO competitive with diesel for some MDVs |
Limited range and slowest refueling Heavy batteries may limit payload Critical raw material concerns (Li, Cu) Lack of charging infrastructure |
H2 Fuel Cell | Efficient/very efficient use of renewable energy Zero emission at tailpipe Relatively long range and rapid refueling |
Some components currently expensive Packaging H2 on vehicle Requires very high purity hydrogen Lack of refueling infrastructure |
H2 ICE | Builds on existing ICE supply chains Can use less pure H2 than FCEV Intermediate range and rapid refueling |
Packaging H2 on vehicle Less efficient use of renewable energy Not zero emission at tailpipe Lack of refueling infrastructure |
E-fuel ICE | Uses existing ICE supply chains Uses current refueling infrastructure Long range and rapid refueling |
Least efficient use of renewable energy Relies on DAC CO2 as feedstock Not zero emission at tailpipe High cost of fuel/high TCO Fuel competition from other sectors (e.g., SAF) |
A key barrier for electric technologies is the availability of critical metals and minerals, such as lithium, copper, nickel, and cobalt. Critical material considerations are already impacting battery prices and are expected to increase significantly in the future. Another set of challenges is presented by infrastructure considerations, from EV charging and electric grid upgrades to the production and distribution of green hydrogen.
Emission Control
Meeting Euro VII emission requirements will require significant changes to the aftertreatment system compared to Euro VI. Key emission challenges include the Euro VII cold NOx limit and PN emissions [J. Jansson, Volvo]. The proposed Euro VII PN limit has been tightened from Euro VI, while the particle size cut-off point has been lowered from 23 nm to 10 nm. As a result, PN emission sources that were not important at the Euro VI stage—such as particles produced during passive DPF regeneration and urea particles from SCR systems—make it challenging to meet the Euro VII PN standard. PN10 particles from urea injection alone can contribute as much as 50% of the Euro VII limit.
To meet the Euro VII cold NOx emission requirements, Volvo evaluated a number of aftertreatment modifications, including SCR-coated DPF to expose the SCR catalyst to higher temperatures, passive NOx adsorbers (PNA), and adding a close-coupled SCR (ccSCR) catalyst. The quality of fuels will be important to ensure catalyst durability. For instance, current FAME specifications for such catalyst poisons as phosphorus and potassium are not sufficiently protective for catalyst systems. Much less catalyst poisoning occurs with renewable diesel (HVO) due to a lack of catalyst poisons.
Particulate filter manufacturers are working on improved DPF formulations with a higher filtration efficiency for Euro VII applications. NGK [A. Wolz] presented a new cordierite filter material with smaller mean pore size, narrower pore size distribution, and a 9 mil wall thickness, which has shown high potential of meeting the Euro VII PN limit. However, the company is also considering the use of a secondary, uncoated Euro VI (12 mil) filter downstream of the SCR reactor to control urea particles.
Presentations by Johnson Matthey (JM) [M. Wallin] and by Umicore [A. Geisselmann] discussed SCR catalyst technologies for meeting Euro VII / US 2027 requirements—with a focus on low temperature activity for NOx reduction and low N2O emissions. Both catalyst makers consider vanadia-based formulations for the ccSCR catalyst, due to the low N2O formation of vanadia, its resistance to sulfur poisoning, and no desulfation requirements. JM has also suggested that the vanadia ccSCR catalyst, due to its oxidation activity, could be used as a warm-up catalyst with HC injection. However, potential issues are presented by the limited high-temperature durability of V-SCR catalysts and the adsorption of HCs by vanadia. A number of formulations, including V (limited to the EU market), Cu, Fe/Cu, and various two-stage configurations are possible for the rear SCR catalyst. Umicore claimed an improved Cu-SCR formulation with enhanced low- and high-temperature activity and suppressed N2O formation that could replace Fe/Cu-based SCR catalysts.
AECC [J. Demuynck] presented an update on their heavy-duty demonstrator concept targeting Euro VII emissions. The vehicle is based on a Mercedes-Benz Actros 1845 LS 4×2 truck powered by a Euro VI, 12.8 L, 6 cylinder OM 471 engine. The AECC emission control system includes a close coupled DOC, ccSCR/ASC, and an underfloor DOC + cDPF + SCR/ASC, with a twin urea dosing system and an HC doser. In phase 2 of the project, an electrically heated catalyst (EHC) has been added as part of the ccDOC. The catalysts have been hydrothermally aged targeting 500,000 km. Near-zero gaseous emissions have been demonstrated under warm operation. In phase 2 of the project, NOx emissions were reduced by 60-77% with the EHC. However, the depletion of ammonia storage over the SCR catalyst shows that robust control is needed for AdBlue dosing, ammonia storage, and thermal management.
Hydrogen ICEs, a potential future powertrain option that attracts considerable attention, would still require complex emission aftertreatment [P. Gwyther, Cummins]. The wide flammability range of H2—4-75% in air, compared to 0.7-5% for diesel—allows for both rich and lean combustion. Lean burn operation (λ>2) allows for very low engine-out NOx and high, diesel-like BMEP levels. However, transient NOx emissions would require SCR aftertreatment, while the high water concentration in hydrogen exhaust and lower exhaust temperatures in lean burn conditions create a condensation risk—with a potential impact on washcoat technology and catalyst packaging mats. Even though H2 combustion is soot-free, a Euro VII H2 ICE would still require a particulate filter (PF) to control PN emissions from oil bypass and urea by-products, Figure 2.
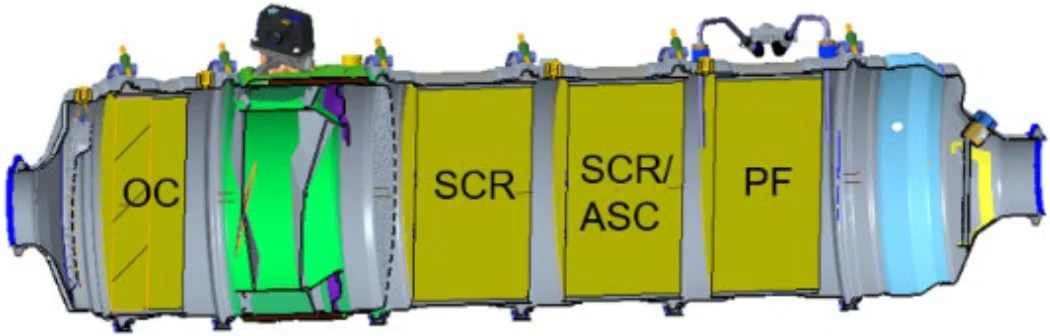
* * *
The next SAE Heavy-Duty Diesel Sustainable Transport Symposium is planned for May 7-8, 2025 in Gothenburg, Sweden.
Conference website: sae.org/attend/heavy-duty-diesel-sustainable-transport-symposium